Article updated on 26 August 2021
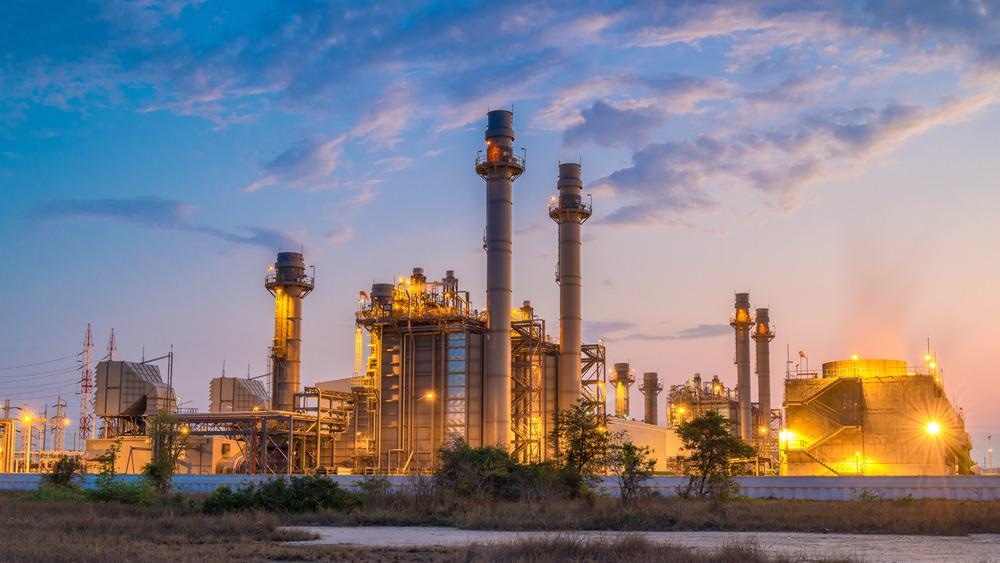
Image Credit: PLUkaAOM/Shutterstock.com
Non-Destructive Testing (NDT) is a diverse portfolio of measurement and inspection techniques deployed to investigate pipelines, tanks and other plant infrastructure in terms of their mechanical integrity, detecting material flaws/faults and possible safety issues without causing any damage.
The continuous health assessment of safety-critical components can eliminate compromise via timely troubleshooting often by pre-empting structural failure for example, in turn avoiding accidents and even death in the workplace.
Executed well, NDT can provide revealing data that saves time and money while ensuring efficient process management. In this piece, some of the traditional NDT methods used in the oil and gas industry are highlighted and some more recent developments are touched upon.
Keeping an Industry Safe and Profitable
Originally driven by an unfortunate reputation for fatal accidents, the oil and gas industry has been at the vanguard of NDT development, first and foremost, to ensure safety. These days, regulation compliance and risk mitigation are heavily underpinned by continuous assessment and preventative maintenance.
Regular testing of systems is necessary to address reliability, hazard prevention and alarming malfunctions. NDT can provide much-needed quality assurance, reducing the probability of failure and benchmarking assets, keeping them under control in terms of security, reach and scope while playing a part in environmental sustainability concerns.
With complex, state-of-the-art facilities and 24/7 operation as the norm, the industry is now highly dependent on NDT technologies to optimize and maintain apparatus and units with frequent health checks. It is important to monitor equipment and facility operating conditions under reliable and efficient regimes.
Peak functionality across the value chain and the often sprawling networks that are a feature of the industry is also essential in generating profitability and sustaining it. Minimizing equipment/plant downtime and maximizing production are the main drivers in this regard. Equally important is the need to obviate expensive component repairs or replacement of equipment. Prevention is better than cure and even in the oil and gas industry.
NDT Techniques
Underpinning most traditional NDT techniques is a device that uses either sound or electromagnetic radiation to produce a signal from a sensor that ultimately gets converted into meaningful data.
Perhaps the most cross-cutting NDT method is remote visual inspection which tends to use a range of probes (typically cameras and optical instruments) to internally examine the structure of an inaccessible object or sampling a component’s material located in a dangerous environment.
Among other diagnostic techniques to become standard are the use of liquid penetrants (such as fluorescent dye) and magnetic particles that reveal flaws and/or detect cracks. Techniques that utilize electromagnetism are favored when it comes to screening material degradation within metallic structures (often steel), core among these are eddy current testing and magnetic flux leakage.
Technological Advances
In terms of new developments, much of the current focus seems placed on the use of inspection robots to perform reliable testing tasks. Many robots can operate autonomously making them ideal for placement within the extreme environments often experienced in the industry.
They can be designed to offer a myriad of testing possibilities, not least in offshore production where drilling equipment is being subjected to increasingly more hostile conditions as deepwater wells continue to be drilled down to greater and greater depths resulting in higher downhole pressures and well temperatures.
As a consequence, this space is now populated by autonomous underwater and remotely operated vehicles (or in short AUVs and ROVs) while also in the mix are unmanned ground and aerial vehicles (or UGVs and UAVs). The sophistication in capability with these robots will only grow in time, more research realizing more features that will adapt to the specific rigors of the industry.
Significant growth is also anticipated in ultrasonic testing. This is where the transmission of low-frequency sound waves (typically 20kHz-100kHz) can detect and locate changes in material properties, often a flag that the mechanical integrity of a part is being undermined. Often this is the detection of corrosion in either submerged or buried pipelines.
Growth in this particular type of testing is expected, in part, due to the rise of manufacturing in developing nations but mainly its technological advances in the level of precision (that is deviation-free) in fault detection that will drive more extensive adoption enhanced by the ease of equipment handling in the next generation of ultrasonic test devices allowing greatly simplified procedures to become standard.
As working practices continue to transition and future-proofing business becomes ever more important, it is likely that the oil and gas industry will embrace the use of data analytics in the context of NDT to progress the sustainability integration agenda as well.
Striking that Important Balance
All the key players within the oil and gas industry, ranging from the exploration companies to the petrochemical refineries and many of those in between, find that NDT is essential.
It is needed to strike the balance between attaining the high productivity levels need for profitability while making no compromise in terms of protecting life with the implementation of the most robust safety measures and practices.
References and Further Reading
Leijian, Y., et al. (2019) Inspection Robots in Oil and Gas Industry: a Review of Current Solutions and Future Trends. 2019 25th International Conference on Automation and Computing (ICAC) pp. 1-6 https://doi.org/10.23919/IConAC.2019.8895089
Disclaimer: The views expressed here are those of the author expressed in their private capacity and do not necessarily represent the views of AZoM.com Limited T/A AZoNetwork the owner and operator of this website. This disclaimer forms part of the Terms and conditions of use of this website.