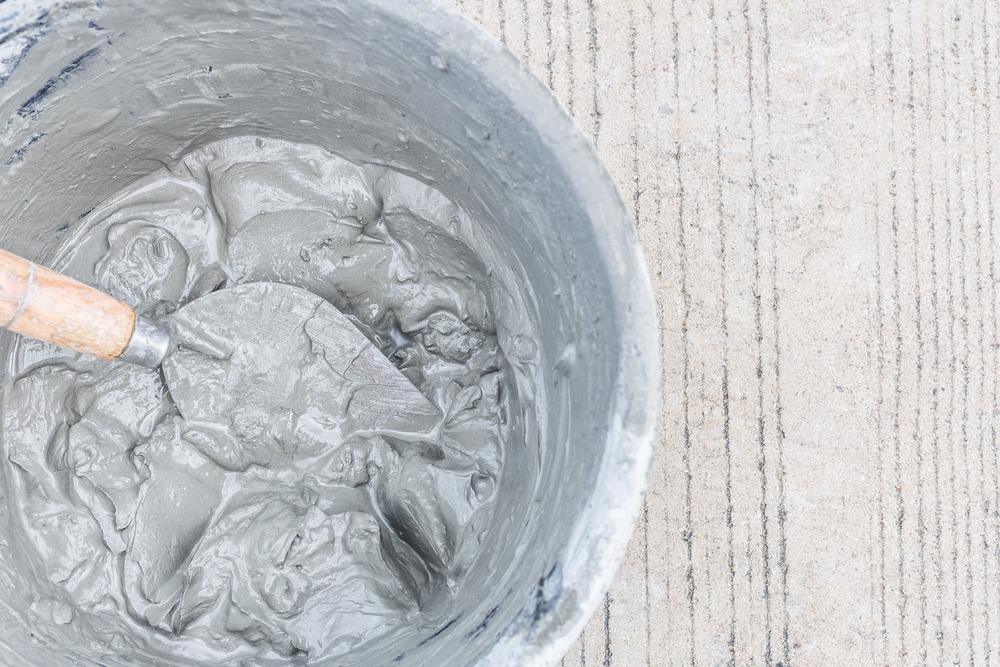
Image Credit: Avigator Fortuner/Shutterstock.com
While every concrete structure demands maintenance every so often, sometimes this go-to construction material abruptly cracks, chips off, becomes discolored, corrodes or even fails to support crucial structures.
When there is a serious and unexpected problem with concrete, forensic experts with backgrounds in engineering and construction materials can use microscopy, chemical analysis and other methods to describe the mechanisms behind the damage.
Their analyses may identify bad elements in the concrete mix, mistakes from contractors, contaminants or various other factors that have negatively impacted integrity and/or appearance. The findings of these investigations can be used to address the problem, prevent it later on, or identify a liable party.
How Concrete is Made
To understand the work of a concrete forensic investigator, it helps to know how concrete is made.
First, cement powder is mixed with small rocks and sand, which is known as aggregate. Next, the dry materials are mixed with water, which turns the cement powder into a glue-like substance that binds the aggregate. Eventually, the entire mix hardens into the familiar rocklike material we know as concrete.
Case Study: Too Much Water
One example of how this process can go wrong concerns a warehouse floor in Tiffin, Ohio that went through serious cracking only months after being installed.
According to an investigation from Bowser-Morner, an engineering consultation business in Dayton, Ohio, operator error was the cause of the cracking. Using microscopic and other analyses of big concrete cores extracted from the floor, investigators concluded that the contractor mixed an excessive amount of water into the mix as the slab was being installed.
The excess water was supposed to keep the mix smooth and easy to use. While this normally works, in this case, the contractor used too much water.
The concrete mix deliberately included very coarse aggregate, including large pebbles of limestone and dolomite, to decrease the amount of shrinkage that normally occurs as concrete sets as a result of lowering the ratio of cement in the mix.
Microscopic analysis revealed that the added water made the concrete too fluid, causing the coarse aggregate to sink to the bottom of the slab. The result was a layer at the surface mostly made up of cement paste.
Because of this, the shrinkage was restricted mainly to the slab surface, stressing the floor. When the warehouse opened and forklifts started driving over the new floor, cracks quickly formed.
Case Study: Too Little Air
Soon after a new farm maintenance building in Fulton County, Ohio became operational, the concrete floor began to delaminate, with millimeter-thin flakes stripping away.
The concrete floor was made in late autumn when colder temperatures will significantly slow concrete reaction dynamics. The licensed contractor for this particular job wanted to avoid any potential delays and therefore called for a lightly air-entrained mix of concrete.
Air-entrained concrete is made for use in cold temperatures and generally contains a foaming agent that creates a network of microscopic bubbles. This acts as a safeguard against crack-inducing pressure caused by residual water contracting and expanding during freeze-thaw cycles.
With air-entrained concrete, concrete workers must wait longer for the material to set so it can be finished. The concrete must support finishers’ weight but still be fluid enough to be workable.
The contractor, in this case, recognized that the cold temperatures meant his team would need to wait around several hours for the floor to be adequately set. To avoid paying for this wait time, concrete was made with a relatively low air concentration, determined by investigators to be around 3 percent. Air-entrained concrete usually has 4 to7 percent air by volume.
Thinking this air-entrained concrete mix would set in an affordable period of time, the contractor next added water to the concrete to maintain fluidity and ease of use. However, the surplus water mixed the foaming agent, making many tiny bubbles.
Due to its low density, the air-entrained component of the concrete rose to the top layer. When the finishers smoothed the concrete, they ended up breaking the bubbles, compressing this layer, and making it denser. With a dense layer on top and a foamy layer just beneath that, the result was poor adhesion between layers, causing the floor to delaminate and flake off.
Case Study: Mystery Powder
Sometimes, forensic researchers are called to investigate mysterious powders that suddenly appear on freshly set concrete.
In a Virginia office building, the surface of a new floor seemed to develop a white fluffy powder before construction even finished. Through the use of electron microscopy, X-ray methods and a bit of common sense, investigators quickly recognized that water-soluble salts within the concrete combined with water and seeped to the top layer. When the water evaporated, it left behind a layer of salt. This is a common phenomenon known as efflorescence.
This situation also involved cold weather. In this case, the contractor used an admixture to accelerate the process. Composed primarily of calcium nitrate, the admixture reacted with potassium compounds found in the concrete. When the concrete set, water high in potassium nitrate was released, and after evaporation, the crystallized salt was left behind.
Resources and Further Reading
Jacoby, M. The Case of the Flaking Floor and Other Tales of Concrete Forensics. Chemical & Engineering News. [Online] Available at: https://cen.acs.org/materials/inorganic-chemistry/case-flaking-floor-tales-concrete/99/i17
Jacoby, M. Alternative Materials Could Shrink Concrete’s Giant Carbon Footprint. Chemical & Engineering News. [Online] Available at: https://cen.acs.org/materials/inorganic-chemistry/Alternative-materials-shrink-concretes-giant/98/i4
Disclaimer: The views expressed here are those of the author expressed in their private capacity and do not necessarily represent the views of AZoM.com Limited T/A AZoNetwork the owner and operator of this website. This disclaimer forms part of the Terms and conditions of use of this website.