Melt flow index is a central component of any plastics sustainability initiative and key to increasing the amount of recycled material that can be utilized before material quality is adversely affected.
A melt flow indexer is an innovative laboratory instrument able to provide a plastics recycler or processor with valuable information. In new materials manufacturing, this information can be used to confirm a polymer’s specification from a data sheet, while in the recycled material process, it can notify operators of the current Intrinsic Viscosity (IV) or Melt Flow Index (MFI) of the recycled plastic.
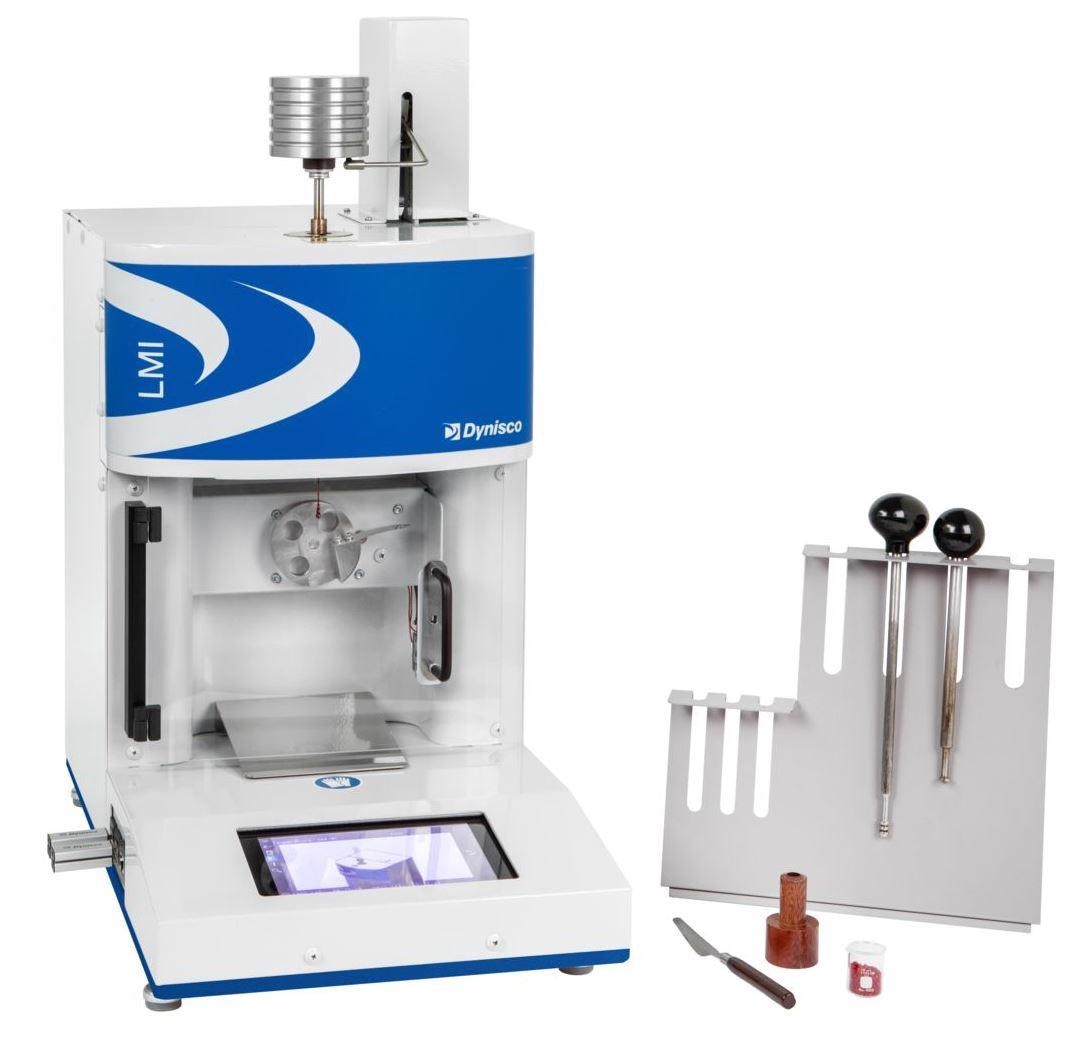
Image Credit: Dynisco
The most commonly asked question about the melt flow indexer is in regard to the most appropriate way to use the information provided by the instrument in daily plant operation.
A list of potential uses is provided below.
Step 1: Review Polymer Target Specification
It is important to have useful data from the offset when looking to insert recycled material into a process. A melt flow indexer can provide this information, allowing users to verify a polymer on the specification sheet to confirm it exhibits the expected properties.
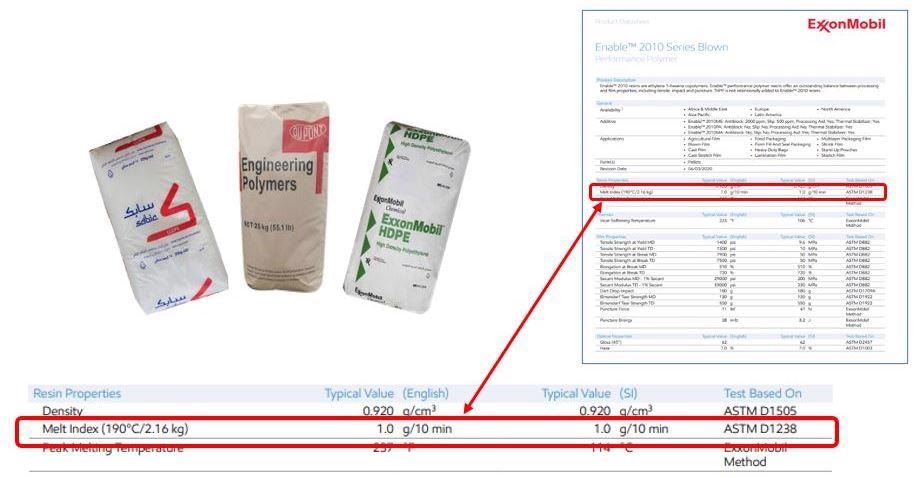
Image Credit: Dynisco
Step 2: Take a Sample (or Samples) of Granulated Material Out of the Gaylord
Information on samples’ melt flow index can be used to confirm the quality of each gaylord of material. Samples can be rapidly tested to determine their melt flow index in terms of g/10 min.
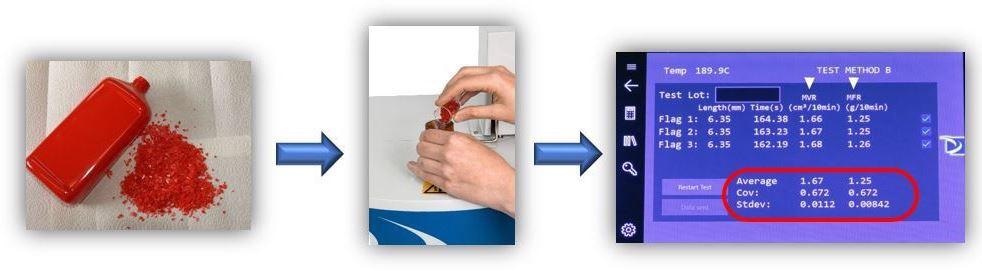
Image Credit: Dynisco
Step 3: Mark or Record the Melt Flow Index
Once a lot of recycled material’s average melt flow index or intrinsic velocity has been determined, this can be recorded in a material database by gaylord, or the melt flow index can be written on the gaylord for quick identification.
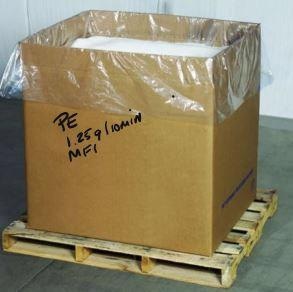
Image Credit: Dynisco
Step 4: Adjust a Blender or Feeding System
With the melt flow index of the recycled material known and recorded, processes can be adjusted to ensure quality; for example, adjusting virgin/regrind ratios or introducing an additive to the process to bring regrind back into specification.
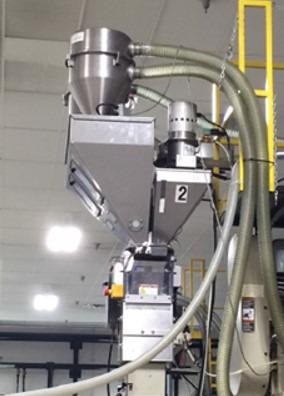
Image Credit: Dynisco
Processes involving extruders may benefit from the addition of a Dynisco Online ViscoIndicator to the standard extruder. This robust instrument enables comprehensive lot-to-lot measurement of production run while allowing an automatic signal to be sent to a blender or feeder for real-time adjustment if required.
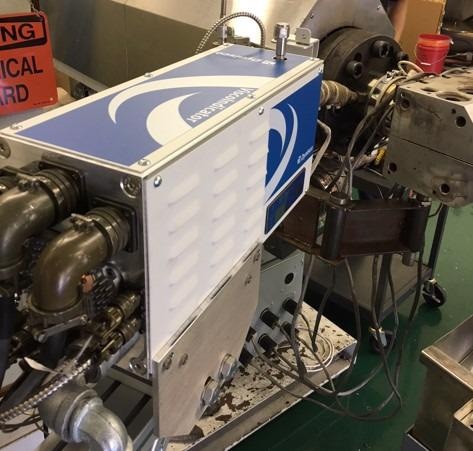
Image Credit: Dynisco
Data from the ViscoIndicator can be correlated with data from a melt flow indexer, confirming that the polymers in use meet specific process standards.
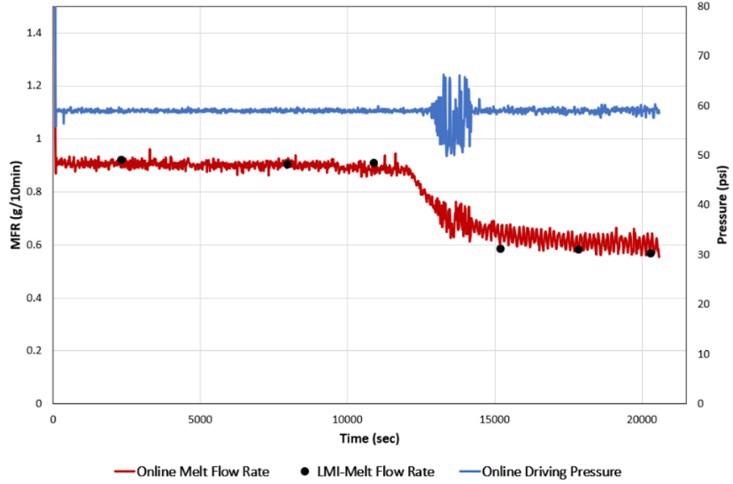
Image Credit: Dynisco
These test samples and this polymer data can be uploaded to the Dynisco IoT Cloud Connect system for storage and comparison by production run, device, operators or global locations. The Dynisco IoT Cloud Connect system is accessible by smartphone, tablet or PC.
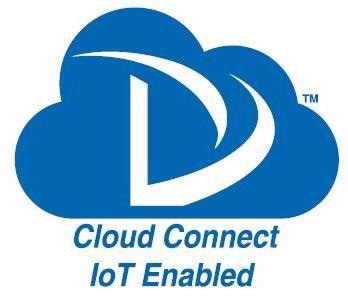
Image Credit: Dynisco

Image Credit: Dynisco
Acknowledgments
Produced from materials originally authored by Bill Desrosiers from Dynisco.
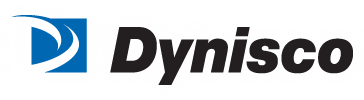
This information has been sourced, reviewed and adapted from materials provided by Dynisco.
For more information on this source, please visit Dynisco.