The conventional process of hand cutting prep-stock samples with shears or scissors is laborious and time consuming, so much so that some laboratory staff have reported attempting to use handheld coffee grinders for this task.
Many users prefer to obtain a sample of material from a production environment, but these are frequently contaminated with other materials being processed.
Dynisco’s MiniGran has been developed to offer a robust addition to any quality control laboratory. It has been specifically designed to provide appropriately sized prep-stock material to run in the Dynisco Melt Flow Indexer, Laboratory Capillary Rheometer or other lab equipment that necessitates a reduction in material size prior to analysis.
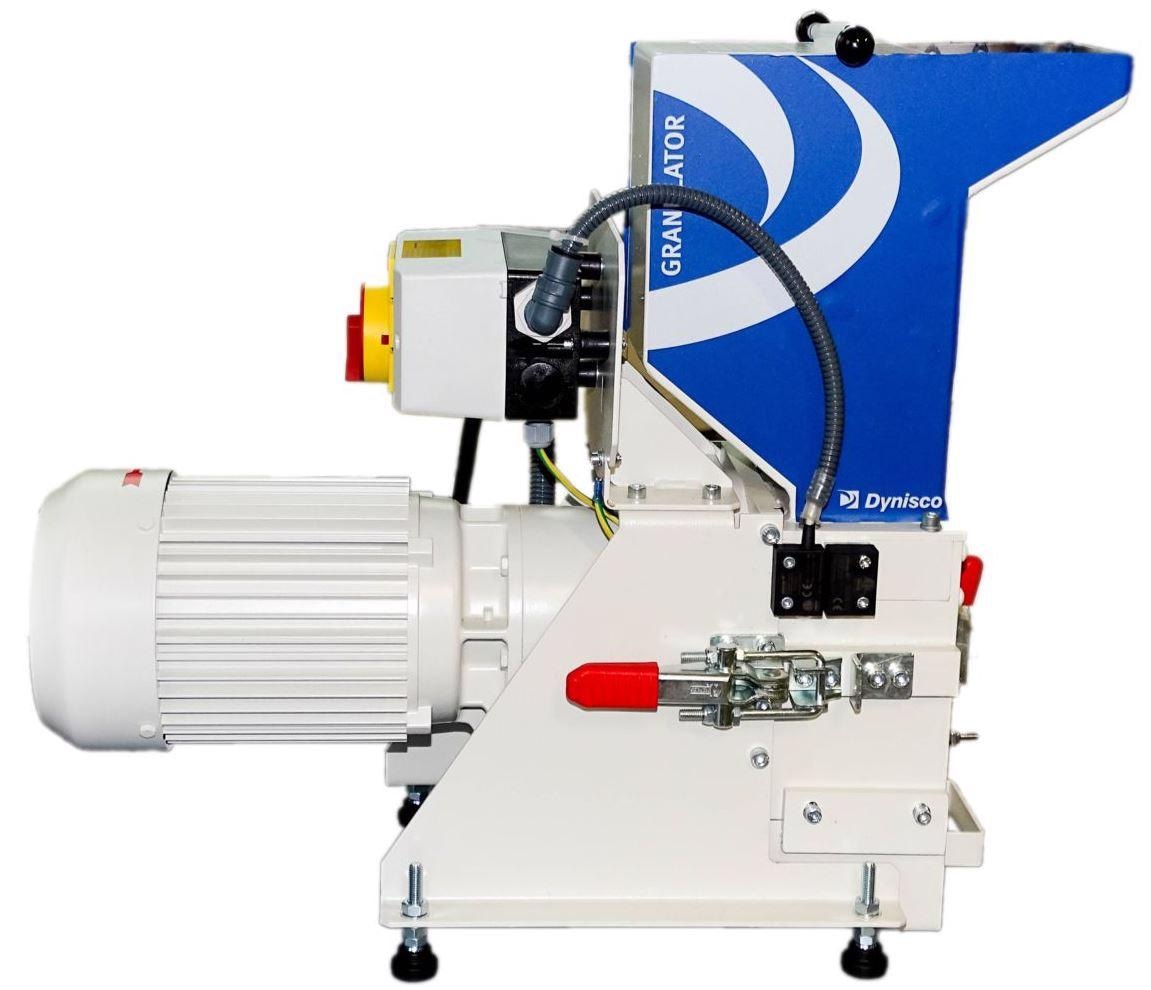
Image Credit: Dynisco
Dynisco’s Minigran is a true benchtop granulator. It has a small footprint and is far more compact than traditional beside-the-press granulators or granulators designed to be used on the manufacturing floor.
The instrument weighs approximately 90 lbs and will comfortably sit on top of any standard tabletop or bench. It features a nominal 3 ” x 4 ” hopper opening ideal for reducing the size of small parts and materials.
Every MiniGran includes a 4 mm round holed screen, with other sizes of screen available if required. This screen is designed to ensure that material processed via the instrument is small enough to be used as appropriate prep-stock for Melt Flow Indexers and Rheometers with barrels 3 / 8 ” internal diameter or larger.

Image Credit: Dynisco
Routine cleanout of the Dynisco Minigran is quick and straightforward. It is a fully toolless entry piece of equipment that does not require the use of wrenches or additional tools to open, clean out, operate or maintain the granulator - a vacuum, hand brush and blast of shop air is sufficient.
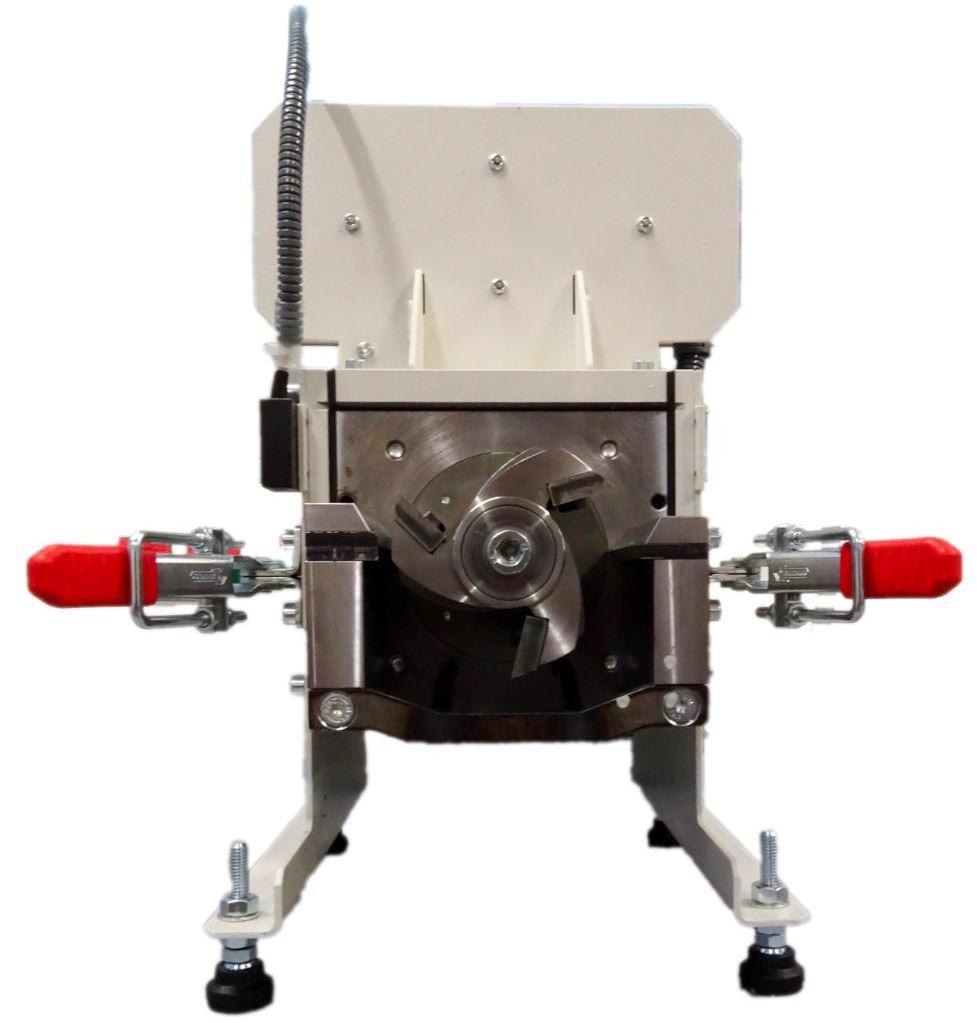
Image Credit: Dynisco
The granulator features a 1HP (230/460 V/3 Ph) Direct Drive motor. The motor will automatically switch off and stop turning if the electrical safety circuit is broken by releasing the clamps and either removing the screen, hopper, material collection bin or upper cutting chamber.
When complete, the Dynisco Minigran rotor comes to an abrupt stop, allowing users to quickly and easily access the screen, the cutting chamber and the material collection bin for cleanout.
This differs significantly from beside-the-press and central granulators which typically utilize a motor and a flywheel, requiring users to wait for the inertia of the rotor to stop turning before being able to safely open the granulator.
This feature is critical for users running a large number of small samples, particularly users who must ensure that there is no contamination between samples.
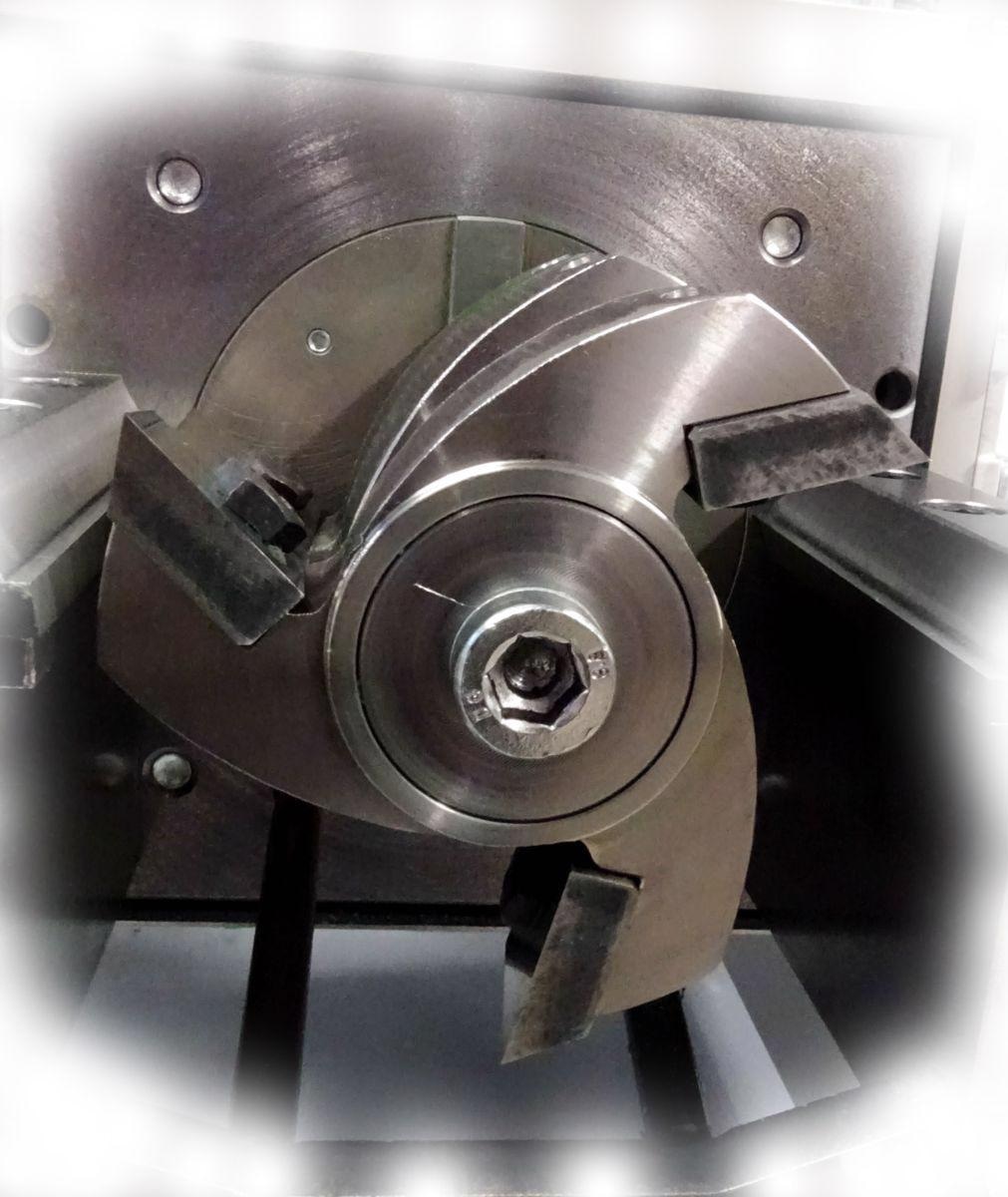
Image Credit: Dynisco
The MiniGran is preconfigured with a Constant Cutting Circle comprised of 4-sided stationary bed knives (stator blades), and 3 rows x 2 cassette knives per row of rotor knives.
Installation or replacement of the granulator does not require gapping, and because the bed knives (stator knives) are 4 sided it is possible to utilize each side of each knife before this requires replacement.
The rotor knives have been specifically manufactured to ensure the gap is set upon the installation of a new set of knives. No adjustment is necessary – they simply need to be torqued down before the grinder is closed and returned to operation.
Replacement screens and knives are affordable and do not require any specific maintenance other than simply removing and replacing these when all sides have become worn from grinding.
Acknowledgments
Produced from materials originally authored by Jason Bradley from Dynisco.
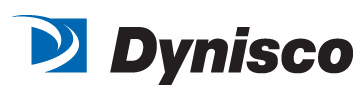
This information has been sourced, reviewed and adapted from materials provided by Dynisco.
For more information on this source, please visit Dynisco.