The StereoLithography (STL) file format was initially developed for 3D systems in the late 1980s. Additive manufacturing was a relatively new technology at this time, having been developed shortly after the invention of the first Stereolithographic 3-Dimensional Printer.
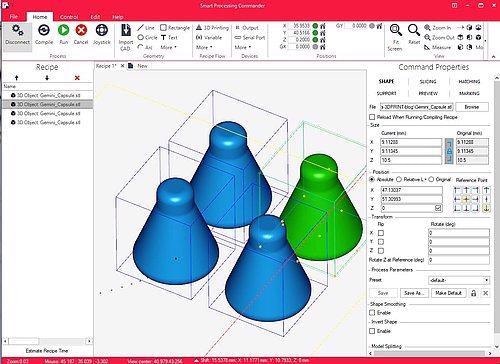
A Batch Recipe of 3D Printed Parts in Smart Processing Commander software with an imported STL file (converted from solid part). Image Credit: PI (Physik Instrumente) LP
It was necessary to encode and transfer 3D model information in a format which enabled the printer to read it as part of in a layer-by-layer fabrication process. This challenge was solved via the use of a 3D surface approximation using a closed polygon tessellated surface mesh formed by triangular facets.
STL has become the de facto standard for 3D printing since that time, seeing frequent use at leading research and commercial institutions and in a range of techniques, including both laser and/or direct material dispense.
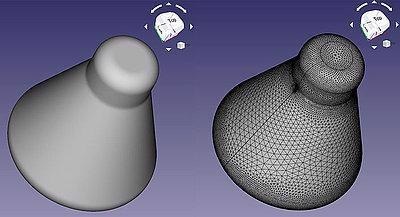
A Solid Part converted to a Fine Surface Mesh for STL export via FreeCAD (an open source CAD package) here using a fine mesh applied with thousands of facets. Image Credit: PI (Physik Instrumente) LP
State-of-the-Art Systems for Next-Gen Processes - Direct from STL
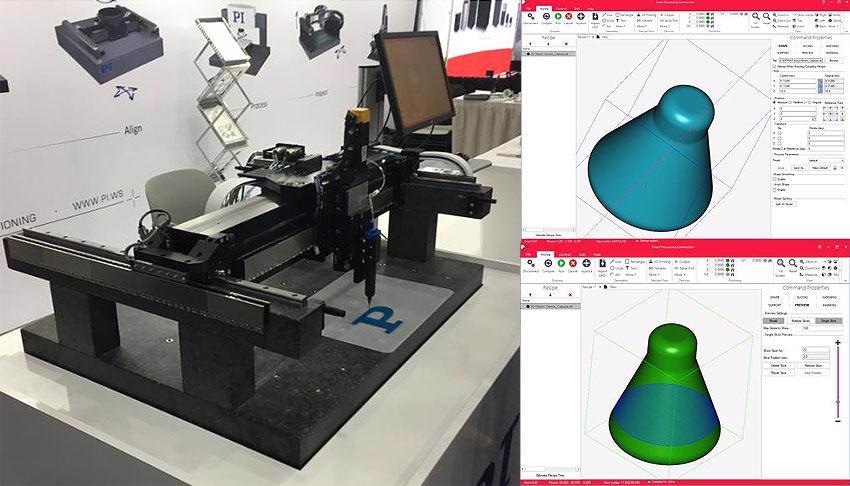
PI A-341 motorized high speed and high precision YYZ Gantry Stage based 3D Print Development Platform running ACS SPC for material dispense demonstration and development. Shown here as well are STL files imported to SPC direct from Meshed Solid Part-sliced with user-defined infill. Image Credit: PI (Physik Instrumente) LP
PI has successfully developed a robust 3D Print System Interface software that can operate directly from STL files. The interface employs the ACS motion controller’s Smart Processing Commander (SPC) software, affording users full system control and access to the ACS controller’s full range of capabilities via an intuitive interface. Its functionality includes:
- XSEG
- Advanced Gantry Control
- LCM (EtherCAT® Laser Control Module)
- ServoBoost
ACS SPC has been developed to support next-gen laser and direct material dispense 3D printing processes via a single interface. It is suitable for use with multi-purpose next gen additive manufacturing R&D platforms, and the interface can also be customized to pass through on commercial OEM 3D print systems.
Conversion, slicing options, process parameters, and job execution for STL files are accommodated in a single user interface with flexible process control. The system can be directly integrated with multiple dispense devices, lasers, galvos, autofocus, machine vision, and surface height sensors.
G-Code in Support of STL Files
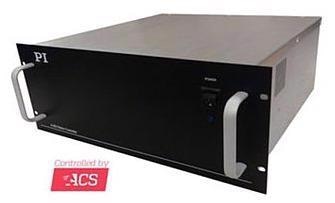
A-824, ACS-based motion controller by PI. Image Credit: PI (Physik Instrumente) LP
ACS motion controllers also feature G-Code compatibility, with systems suitable for integration in third party CAD/CAM packages. G-Code is converted directly from STL files via third party packages like Slic3r, while post-processors can be developed in some instances to support specific functions not typically available in a generic G-Code implementation.
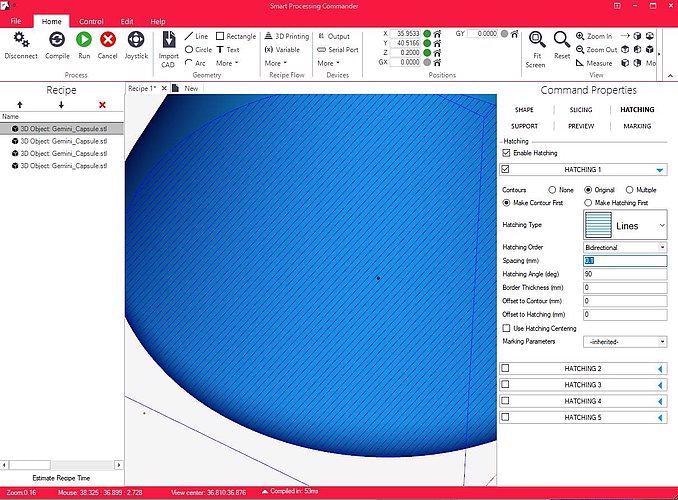
STL file infill options are shown above with a line hatch pattern using alternate 90® rotated lines from layer-to-layer in a log pile pattern. Image Credit: PI (Physik Instrumente) LP
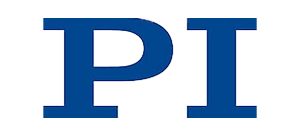
This information has been sourced, reviewed and adapted from materials provided by PI (Physik Instrumente) LP.
For more information on this source, please visit PI (Physik Instrumente) LP.