Piezoelectric ceramics (electroceramics) can directly convert electrical energy into mechanical motion and mechanical motion into electrical energy, based on a series of crystalline solid-state effects. Piezoelectric transducers and actuators are uniquely able to combine speed, force and precise motion into a compact package.

Image Credit: PI (Physik Instrumente) LP
To increase the accessibility of piezoelectric transducers and actuators for OEM designers, manufacturers may package these devices inside a protective arrangement of flexures. This approach offers a straightforward mounting interface alongside amplified motion and precision guidance.
Flexures are typically manufactured from steel, aluminum or titanium. Without wear and friction, flexures can provide tens of hundreds of billions of cycles of maintenance-free service.
Difference between Transducer and Actuator
When it comes to piezoelectric devices, the terms transducer and actuator are often used synonymously. However, when motion or force is the main objective, one usually speaks of piezoelectric actuators, and when sensing or high frequency applications such as ultrasound, flow or distance measurement are targeted, transducer is the more common word. Acuators usually are not operated at resonance, transducers often are. Basically both respond to external pressure with building an electric charge, and vice versa when an electric field is applied they will change their shape.
Piezoelectric Actuators for Motion
Piezo motion devices confidently facilitate position changes in milliseconds or even microseconds, with precision down to sub-nanometers. Motion amplified piezoelectric actuators provide motion output that is proportional to drive voltage – typically up to one millimeter - alongside high dynamics - with frequencies in the hundreds to thousands of hertz.
Piezo Motion: Nanopositioners, Piezo Flexure Actuators & Motors for Precision Autiomation
Video 1. Animation – operating principle of several types of piezoelectric actuators. Video Credit: PI (Physik Instrumente) LP
Piezoelectric devices are not subject to mechanical wear, and their lack of frictional parts ensures limitless resolution.
These factors make them ideal solutions for a wide range of precision motion and positioning applications in life sciences, medical engineering, industry, microscopy and space settings.
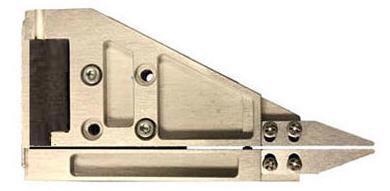
Piezo actuated micro grippers provide fast response, high force and nanometer precision. Models with force feedback are available for handling delicate optical devices. Image Credit: PI (Physik Instrumente) LP
Actuator Reliability
Prior to the arrival of cofired, monolithic and ceramic encapsulated piezo actuators, piezo ceramics’ reliability was highly dependent on the application site’s specific environmental conditions.
Humidity, temperature and operating voltage have a considerable impact on actuators with conformal coatings because no polymer insulation is completely impermeable. The life expectancy of these devices decreases dramatically in highly humid conditions.
Moisture ingress coupled with the application of the electric field applied can trigger chemical reactions in the component. These reactions are accelerated by higher temperatures, initially causing increased current leakage and leading to a complete dielectric breakdown - a short-circuit between electrodes.
During dynamic operation, piezo ceramics’ service life may be impacted by alternating mechanical stress conditions and other dynamic forces. Inadequately designed ceramic actuators may experience microcracks that result in rapid failure.
The Solution
The solution to many of these issues can be found in appropriate optimized materials and manufacturing processes, effective design and the right choice of insulation.
PICMA® cofired piezoelectric stacks (Figure 1) from PI are an ideal example of a robust solution to these issues. These stacks are comprised of layers of specialized ceramic that are a few dozen microns thick, interleaved with electrodes and sintered to create a solid structure.
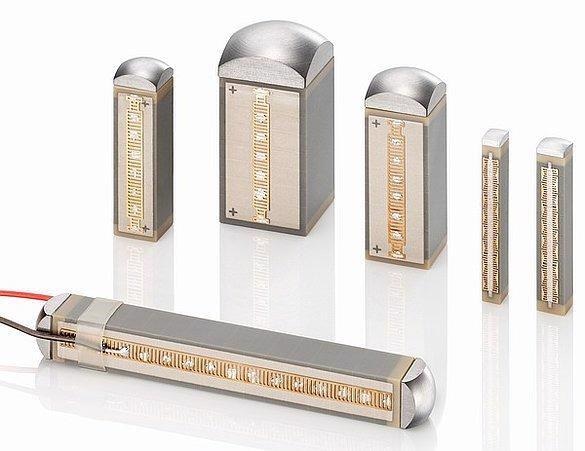
Figure 1. Ceramic-insulated, cofired high-performance piezo stacks outlast polymer-insulated types. Image Credit: PI Ceramic
A ceramic material based on a special modified PZT (a ferroelectric ceramic) is ground to create a slurry. Thin ceramic foils are then cast from this (Figure 2).
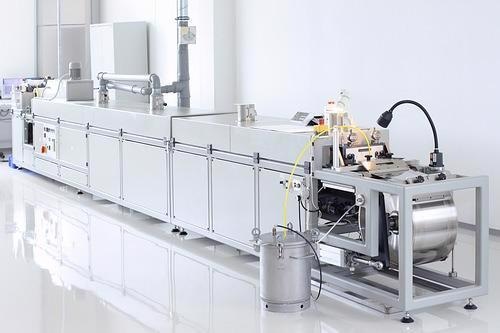
Figure 2. The multilayer cofiring technology is a particularly innovative manufacturing process. Image Credit: PI (Physik Instrumente) LP
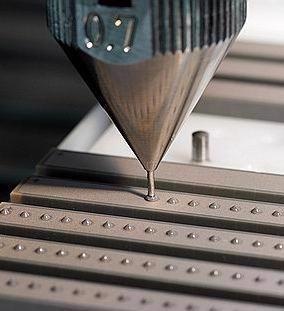
Figure 3. Automated contacting process of a piezo stack actuator. Image Credit: PI (Physik Instrumente) LP
The ceramic material is ideally suited to motion positioning applications due to PZT ceramic’s capacity for small, almost linear dimensional change when a drive voltage is applied across the electrodes.
Electrodes will then be screen printed prior to the layers being laminated to stacks. Compacting the ceramic removes any air trapped between its individual layers, and this is then sintered together with the electrodes (cofiring technology) to produce a monolithic block.
A ceramic insulation layer protects this block against humidity and failures, while its monolithic design improves material stiffness and provides a higher mechanical resonant frequency. These features are key to ensuring rapid mechanical response to electric input – essential prerequisites for highly dynamic applications.
It should be noted that the ceramic is not flexible - motion is entirely based on solid-state effects.
Solely employing inorganic materials in the insulation and electrical contacts (Figure 3) means there is no outgassing and these devices are suitable for use in ultra-high vacuums.
Figure 4 displays a range of accelerated lifetime testing results obtained under high humidity conditions. These results compare piezo ceramic actuators with traditional conformal coatings and ceramic insulated PICMA® actuators.
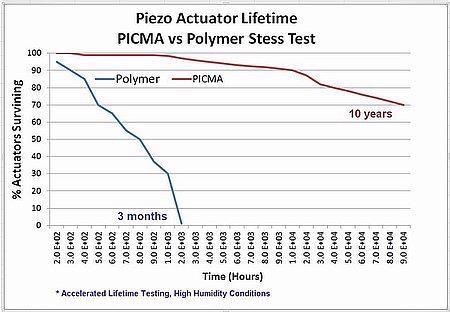
Figure 4. Accelerated lifetime testing of ceramic insulated actuators compared to actuators insulated with conformal coating materials, under high humidity conditions. Image Credit: PI (Physik Instrumente) LP
Resistance to humidity is an important consideration for positioning applications within the semiconductor industry.
These applications typically employ high and constant offset-drive voltages to maintain a stable wafer position throughout lithography and inspection. Clean rooms are artificially humidified to avoid electrostatic flashovers as part of this process.
Piezo actuators are used in machining applications in active vibration cancellation, fast tool servos and precision alignment. These applications frequently utilize cooling liquids, which may cause a substantial increase in ambient humidity, adversely affecting the actuator.
Independent Testing for Space Applications
Piezo actuators are frequently found in applications working under space conditions, including high vacuum and ultra-low temperatures.
Numerous actuator types were considered and tested by NASA during work on the Mars Mission. The sample analyzer system at the CheMin laboratory unit of the Curiosity Mars rover (Figure 5) opted to use PICMA® piezo actuators after these actuators demonstrated 100 billion cycles with no failure or performance loss.
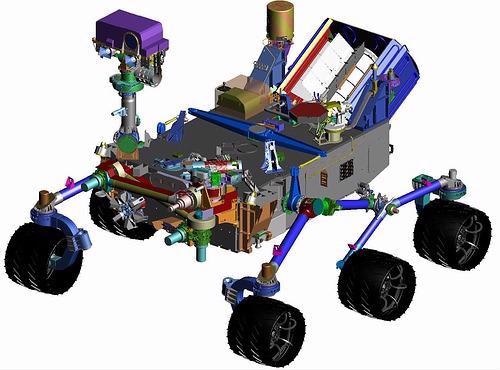
Figure 5. The CheMin spectrometer for chemical and mineralogical analyses in the Mars rover: equipped with piezo actuators from PI Ceramic. Image Credit: NASA.
Piezoelectric Transducers on Mars Rover | Ultra-High Performance + Reliability | #Life_on_Mars | PI
Video 2. PI’s ultra-reliable multi-layer piezo stack actuators were employed in the shaking mechanism and in addition a PI precision motion stage was used as a focusing motor for the laser. Video Credit: PI (Physik Instrumente) LP
The CheMin instrument is responsible for performing mineralogical and chemical analyses on Mars rocks.
In order to supply the instrument with appropriate rock samples, rock powder must be sorted. This is done by shaking the powder at a range of amplitudes and frequencies in the 0.9 to 2.2 kHz range to achieve separation according to density or homogeneous particle sizes.
PICMA® multilayer piezoelectric actuators are utilized in this vital task, performing the required oscillations at defined amplitudes and frequencies to ensure proper material selection and supply.
It is imperative to ensure success in such a multi-billion dollar project. Prior to being permitted on board, the piezo actuators were required to pass extensive qualification and testing.
PICMA® actuators were able to achieve impressive results in this application, with comprehensive NASA/JPL performance and service life tests demonstrating zero failures after 100 billion (10 exp 11) cycles.
Additional independent tests were conducted by the European Community Research Infrastructure to evaluate the behavior of piezoelectric actuators in conditions that were equivalent to 10 years of operation in an active frequency tuner for ILC superconducting cavities (SC).
Stress Loading and Managing Humidity
It is vital that the risk of cracks be managed if the lifetime is to be maximized and stress is to be minimized in dynamic applications. PICMA® actuators’ patented slot design helps minimize the tensile load, with its lateral slots limiting mechanical tensile stress in the stack, effectively preventing the formation of uncontrolled cracks (Figure 6).

Figure 6. Patented piezo stack design with lateral slots to avoid uncontrolled expansion of micro cracks during dynamic operation. Image Credit: PI Ceramic
Stress on the electrodes must also be considered since repeating an identical motion 100 billion times can wear these out.
A patented meander-shaped design (Figure 7) ensures internal electrodes maintain stable electrical contact even at extreme dynamic loads, avoiding fractures of the termination electrodes. These factors combine to ensure that the PICMA® design offers excellent performance and lifetimes, even where other designs do not.
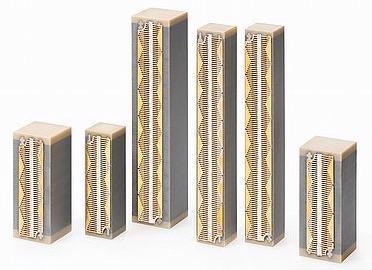
Figure 7a. Patented, meander-shaped external electrodes: stable electric contact even under extreme dynamic stresses. Image Credit: PI Ceramic.
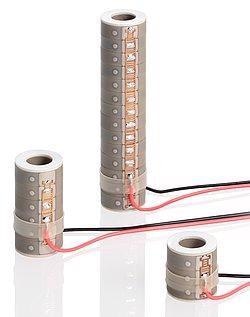
Figure 7b. Ceramic-insulated piezo actuators are also available as tubular stacks. Image Credit: PI (Physik Instrumente) LP
Low Operating Voltage
Unlike most conventional actuators, PICMA® actuators have been developed using particularly thin ceramic layers, allowing them to run at minimized operating voltages. They can achieve their nominal motion output at operating voltages well below 150 v - as low as +/-30 v in the case of bender-type actuators.
Contemporary production technologies allow multilayer actuators to be manufactured in almost any shape whilst still ensuring that every surface remains encapsulated within the ceramic insulation (Figure 8).
A range of basic shapes with round or triangular cross-sections can be provided, featuring insulated center holes on benders, chips and stack actuators.
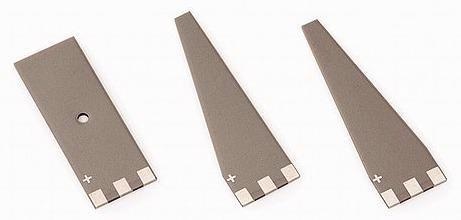
Figure 8. Piezo bender actuators with variable contours: flexibility geometries maintaining the full ceramic encapsulation while requiring very low operating voltages of only +/-30V. Image Credit: PI Ceramic
Flexure Designs for Long Travel and Easy Integration
Piezo ceramic actuator operation is characterized by four factors:
- Precision
- Speed
- High force
- Relatively short displacement
Since the actuator’s positioning precision is a result of molecular effects, it is free of stiction, free of friction and can be controlled down into the sub-nanometer range. High force motion can also be exerted in microseconds.
Piezoelectric mechanisms are a cornerstone of the latest generation of fuel injection valves, super-resolution microscopes, semiconductor lithography tools and an array of nanoscale-precision metrology and positioning systems.
A piezo stack’s motion is limited to around 0.1% of its physical length. In applications requiring longer motion ranges, ease of installation and integration, it is advisable to utilize a flexure actuator with an integrated motion amplifier. These flexure actuators rely on a piezo stack for their core operation (Figure 9).
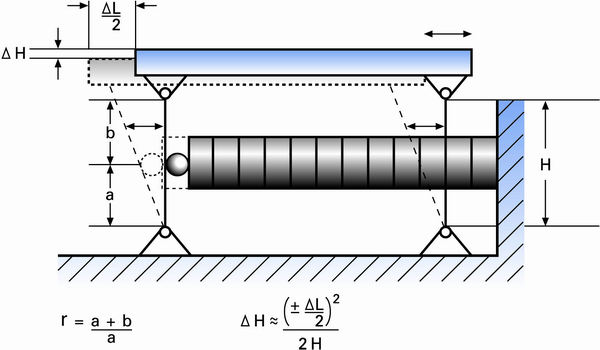
Figure 9. A very basic piezo motion amplifier based on a simple parallelogram flexure lever and guiding system. The amplification r (transmission ratio) is given by (a+b)/a. Typical flexure actuators are significantly more complex and are manufactured based on the wire-EDM (electrical discharge machining) process. Image Credit: PI (Physik Instrumente) LP
Depending on its specific design, the motion range can be amplified up to 20X while maintaining protection from lateral and tensile forces, ensuring effective precision guidance is added.
This increase in motion range does reduce stiffness, however, meaning that a careful balance must be managed between maximum displacement, stiffness and force.
Piezoelectric flexure actuators are available in a range of configurations and carefully designed mounting provisions. These are easy mechanisms to integrate into a design (Figure 10, Figure 11) – a factor that is central to their utility and popularity.
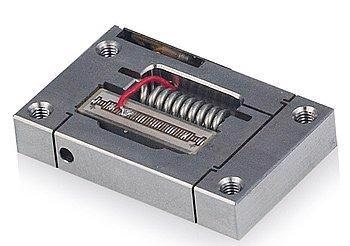
Figure 10a. Low-cost motion amplified piezo actuators for OEM application. The image shows the integrated piezo stack actuator and the preload. A position feedback sensor is optional. Image Credit: PI (Physik Instrumente) LP
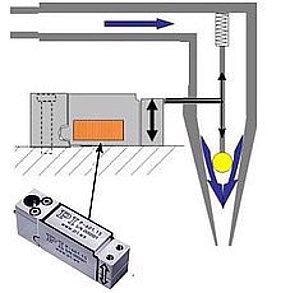
Figure 10b. Precision dispensing, metering. Flexure amplified piezo actuators provide benefits in high–speed, high-precision valves, compared to conventional solenoid or voice coil actuation. Image Credit: PI (Physik Instrumente) LP
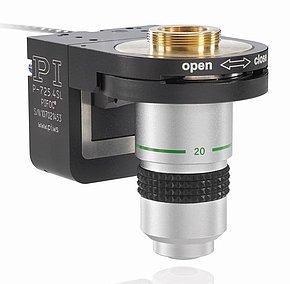
Figure 11. Highly integrated piezo flexure positioning device for high-precision nano-focus applications in microscopy and surface metrology. Image Credit: PI (Physik Instrumente) LP
Every aspect of their use has been considered and optimized.
Piezoelectric flexure actuators’ integrated preload mechanisms can accommodate even high-dynamic actuation, and their optional position feedback sensors are mounted in the best location to ensure reproducible hysteresis-free information. Their robust flexure guidance is suitable for a wide range of common applications.
Ease of Control
Motion system designers benefit from an array of piezo motion controller options encompassing a diverse range of capabilities and price ranges.
Even the most compact, cost-effective and OEM-friendly units boast excellent features such as up-to-date high speed digital and analog communications interfaces, advanced all-digital servo-algorithms with auto-calibration, internal waveform-generation capability, data-recorders designed to enable evaluation of transients and system optimization (Figure 12, Figure 13).
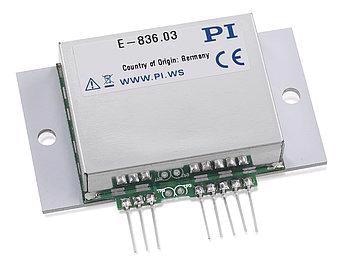
Figure 12. OEM board-level piezo driver. Image Credit: PI (Physik Instrumente) LP
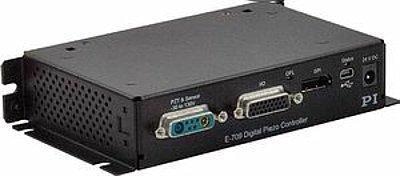
Figure 13. Compact, digital servo piezo motion controller for closed-loop piezo mechanisms. Image Credit: PI (Physik Instrumente) LP
What is the Difference between a Piezo Transducer and Piezo Actuator
When it comes to piezoelectric devices, the terms transducer and actuator are often used synonymously. However, when motion or force is the main objective, one usually speaks of piezoelectric actuators, and when sensing, structural health monitoring, or high frequency applications such as ultrasound, flow or distance measurement are targeted, piezoelectric transducer is the more common word. Acuators usually are not operated at resonance, transducers often are. Basically both respond to external pressure with building an electric charge, and vice versa when an electric field is applied they will change
The Future of Piezoelectric Motion and Positioning Devices
Piezoelectric devices are seeing increased and more varied use in product designs and applications where precision motion control is essential.
Piezoelectric stack actuators and the latest generation of flexure actuators offer wide ranging product development options for OEM designers, and piezo ceramics continue to provide the basis for numerous motion control solutions.
For example, piezo motors are a separate class of piezo motion devices designed for long travel applications as they provide precise, rapid motion at distances far beyond one millimeter.
Piezoelectric motors can be divided into several subcategories, including inertial motors, resonant motors and inchworm-type motors. Linear and rotary motor configurations are also available, each offering specific performance characteristics.
What is a Piezo Motor? How does it work? Piezo Motor Designs for Automation & Motion Control | PI
Video 3. Piezo motors combine long travel ranges with high precision motion. This animation explains several types of piezo motors for different applications. Video Credit: PI (Physik Instrumente) LP
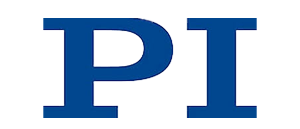
This information has been sourced, reviewed and adapted from materials provided by PI (Physik Instrumente) LP.
For more information on this source, please visit PI (Physik Instrumente) LP.