Like all ceramics, piezo ceramics are brittle materials that are well suited to handling compressive loads but are highly sensitive to bending, shear and tensile loads. A number of mechanical solutions have been developed to help protect piezo material from these undesirable forces.

Image Credit: PI (Physik Instrumente) LP
Piezoelectric transducers have become mainstream, everyone has "made contact" with or at least seen ultrasound piezo transducers in medical applications. Outside of medical engineering and therapy, there are many industrial uses for these versatile devices. One novel type of transducer, and new approach to protect it from unwanted forces, is found in the patented laminate structure of the DuraAct patch transducers. These composites of one or more thin piezoceramic plates are fitted with electrodes, mechanically pre-stressed via a polymer outer skin and are electrically insulated.
Strands can be glued, soldered or clamped at two contact points, depending on the application in question. The patch transducer is also able to offer separate sensor and actuator functionality when several layers are contacted separately.
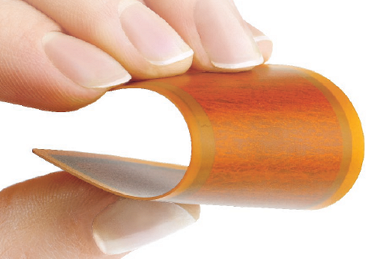
Piezoelectric patch transducers can be very flexible the minimum bending radius for the DuraAct type is as low as 12mm. Image Credit: PI (Physik Instrumente) LP
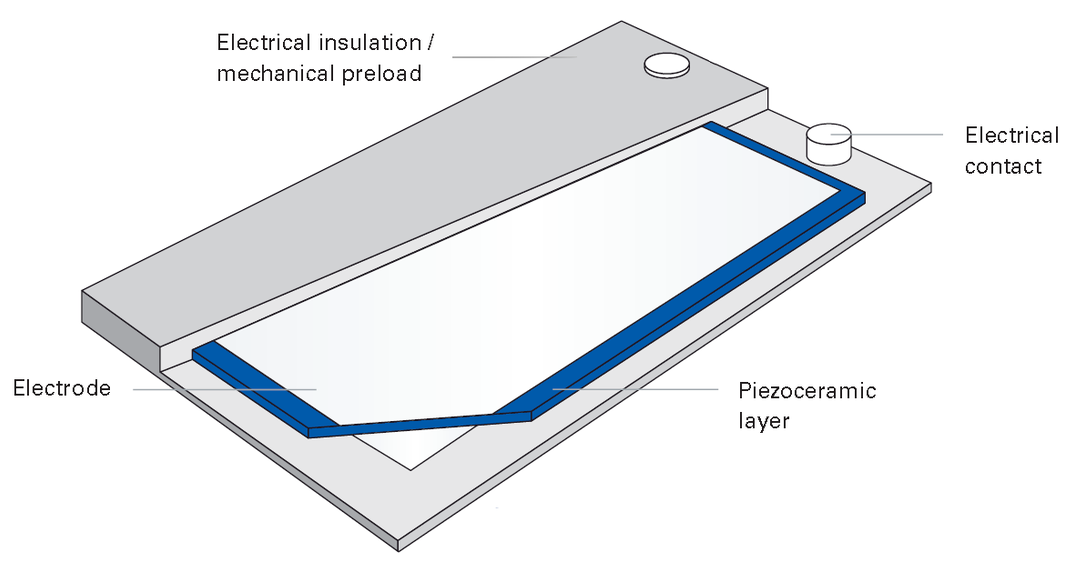
Basic design of the laminated piezo patch transducer. Image Credit: PI (Physik Instrumente) LP
Structural Health Monitoring
Piezoelectric transducers can be employed in the measurement of deformations on components or structures that are traditionally difficult to access, for example, weld seams and bridges.
Whole areas can be actively monitored by utilizing transducers as wave-generating actuators, while other modules function as sensors to detect these waves. Disturbances within a component (for example, microcracks) are detected by comparing the signal to reference signals from unharmed systems.
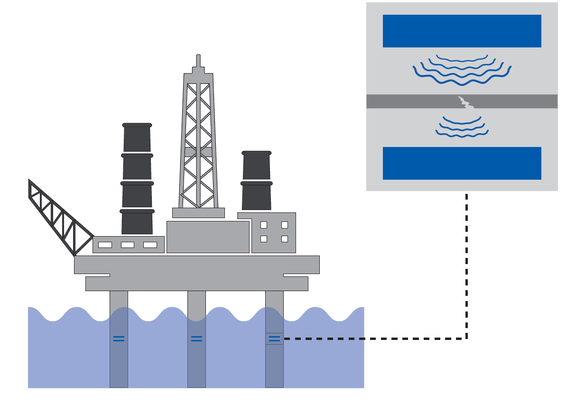
Image Credit: PI (Physik Instrumente) LP
Active Vibration and Sound Insulation
It is possible to operate DuraAct Patch Transducers in sensor and actuator mode. In actuator mode, they are able to dampen or even cancel unwanted vibrations. The phase-shifted sensor signal can also provide a voltage supply for the same piezo element.
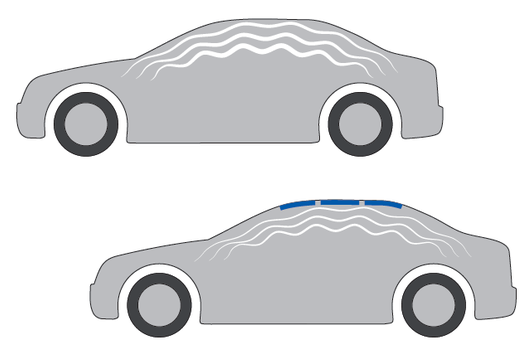
Image Credit: PI (Physik Instrumente) LP
Contouring
DuraAct Patch Transducers can detect deformations due to their function as sensors. These deformations may be offset by driving an appropriate signal into the actuator, enabling both contouring and deformation with precision in the sub-micrometer range.
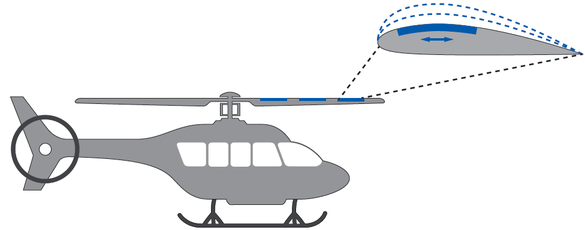
Image Credit: PI (Physik Instrumente) LP
Different Designs: Shear Mode, Contraction Mode, Bulk and Multilayer Variants
A number of variations are available. Each of these variants behave differently when utilized as actuators, as well as offering different directional sensitivities when employed in sensor mode.
For example, standard variations such as the P-876 type transducers are specifically polarized to facilitate longitudinal and transversal contraction or expansion upon application of an electric field.
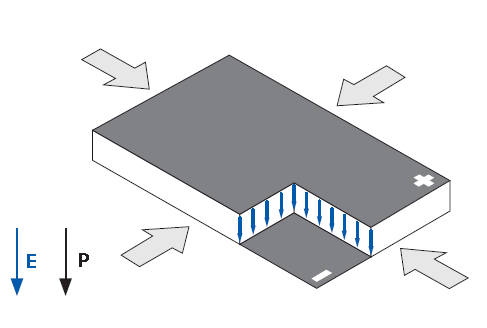
Image Credit: PI (Physik Instrumente) LP
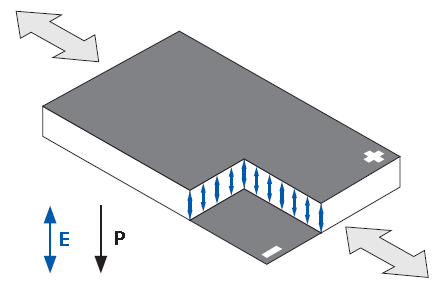
Image Credit: PI (Physik Instrumente) LP
This occurs with a maximum displacement of 800 µm/m and a maximum operating voltage of 1000 v. A minimum bending radius to 12 mm is made possible due to these versions’ high level of flexibility.
Shear piezo transducers allow a degree of shear motion between the top and bottom surfaces. These transducers can be employed in the generation of surface acoustic waves and offer a maximum drive voltage of 500 v.
Multilayer piezoelectric patch transducers, such as the P-878 flexible power patch transducer family, offer longitudinal expansion with transverse contraction, alongside comparatively high axial displacement up to 1200 µm/m. The multilayer design of these devices improves their efficiency, reducing their maximum operating voltage to 120 v.
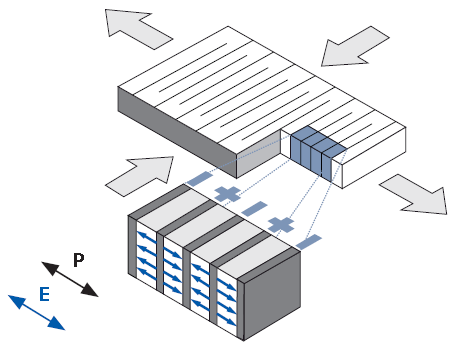
Image Credit: PI (Physik Instrumente) LP
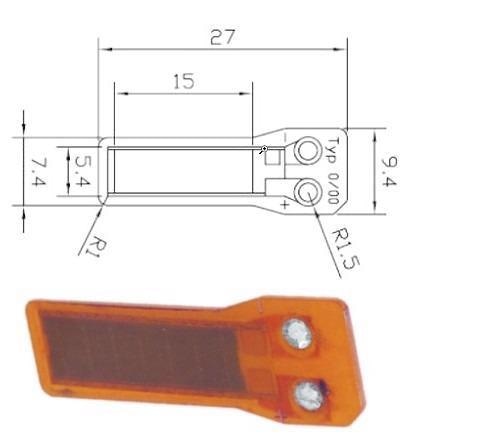
Image Credit: PI (Physik Instrumente) LP
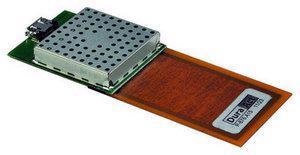
Patch transducer with integrated piezo amplifier / driver. Image Credit: PI (Physik Instrumente) LP
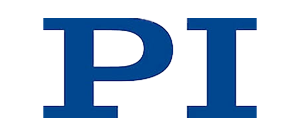
This information has been sourced, reviewed and adapted from materials provided by PI (Physik Instrumente) LP.
For more information on this source, please visit PI (Physik Instrumente) LP.