Perform mechanical durability tests of hybrid and electric vehicle batteries utilizing HBK electrical testing solutions and vibration testing equipment.
The existing competition and pace of development of hybrid drive technology in the automotive industry are encouraging manufacturers to invest in the research and development of batteries.
Although the time to market is crucial, comprehensive product testing of the batteries should not be compromised. Failing to test batteries may lead to the recall of vehicles, which incurs significant costs.
During their lifetime, batteries and their subsystems (for example, connections, cooling, etc.) are susceptible to failure. It could be a decline in the battery performance or a complete failure.
Different types of test methods are mandatory to verify the battery durability, considering the different sizes, shapes, weights and chemical compositions of batteries in electric and hybrid vehicles. The three main battery types are modules, battery cells and packs.
According to major standards and regulations for electric and hybrid vehicle batteries, such as MIL, ISO and USABC, mechanical, electrical, environmental and chemical testing must be done on the modules, battery cells, packs and subsystems.
HBK provides battery testing solutions for mechanical vibration testing, thermal testing and electrical testing. All these facilities are sold separately or in the package.
Electric Battery Testing Equipment
Apart from vibration test simulation, it is vital to perform physical vibration testing of a vehicle battery and its subsystem.
HBK LDS vibration test systems offer a turnkey solution for shock, altitude and mechanical vibration testing, including regulations UN 38.3 and ECE Reg 100, which stipulate that before any battery cell, module or pack is transported, it must be tested under the dangerous goods act.
However, several other regulations apply to different countries, and in turn concentrate on different technology/battery types (cells, modules, packs, etc.).
As different battery types and their subsystems feature varied sizes, weights and required vibration test profiles, a robust and versatile system is crucial. The system must be easily adaptable to various testing requirements capable of simulating the life of the vehicle.
The durability test must also be performed repeatedly, requiring the vibration test solution to be simple to configure, perform and sign off. This is to ensure that the test is precise and consistent throughout.
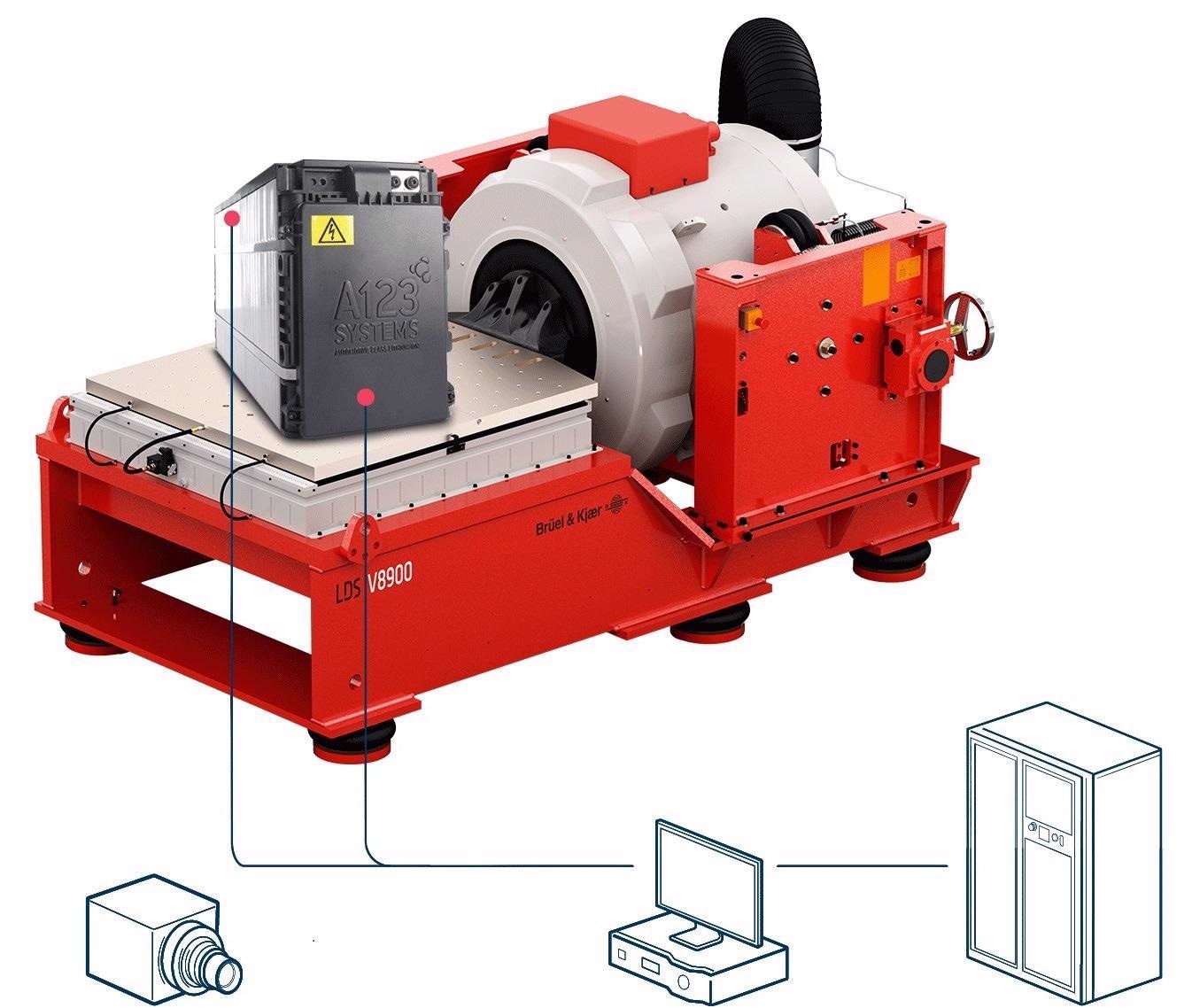
Figure 1. Image Credit: Brüel & Kjaer
A climatic chamber can be combined to strictly control the temperature and humidity during vibration testing. Furthermore, HBK turnkey solutions facilitate a simultaneous measurement of mechanical vibration and thermal/power cycling of a battery.
From the transducers and sensors, the data collation and integration to the analysis software, HBK vibration test solutions enable the user to test the durability of the batteries quickly and effectively.
Vibration Transducers
Vibration transducers are employed not just to monitor and control the vibration transferred to the test object based on specified profiles but also to obtain data for immediate or post-process analysis.
Brüel & Kjær vibration transducer features accelerometers, impedance heads, vibration calibrators, force transducers, impact hammers and accessories such as cables and other key equipment for performing an accurate measurement.
LDS Shakers and Testing Equipment
LDS shakers are employed to induce vibration into the test object. Apart from a broad range of electrodynamic shakers, HBK LDS shaker systems also offer thermal barriers, head expanders, slip tables and work closely together with manufacturers of climatic chambers and ancillary equipment.
LDS amplifiers provide the drive signal to the shaker. A wide array of HBK LDS linear and digital-switching amplifiers are developed to operate HBK LDS shakers, including third-party shakers.
LDS vibration controllers provide the testing profile for the LDS amplifier to generate a drive signal into the shaker. HBK presents LDS Vibration Controllers for easy configuration as well as for advanced testing technologies. HBK works closely with controller manufacturers for high channel counts.
Vibration Control Software
An immediate output and/or post-process analysis can be done using LDS vibration control software, which comes readily integrated into every LDS vibration controller.
nCode software can be used to produce a power spectral density loading spectrum that represents the fatigue damage in a very quick timeframe.
Datasets with generic PSD, sine sweep profiles from ISO, MIL, USABC standards are offered to provide baseline qualification. This PSD spectrum can be used for physical testing to drive an LDS Shaker System as well as to drive virtual shaker table analysis.
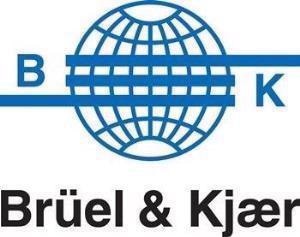
This information has been sourced, reviewed and adapted from materials provided by Brüel & Kjær.
For more information on this source, please visit Brüel & Kjær.