What types of adhesives can be used to bond titanium to carbon-carbon composites when faced with extreme temperatures?
High temperature resistant epoxies, certain grades of silicones, bismaleimides, polyimides and (inorganic) ceramic adhesives are known to resist high temperatures.
Are there any real life case studies demonstrating the use of such adhesives?
While there are numerous case studies, one example was where the researchers1 from the QSS Group, Inc., the Ohio Aerospace Institute and the NASA Glenn Research Center tested multiple adhesive formulations to see how they performed under such conditions.
The study’s aim was to ascertain the feasibility of adhesive bonding in conjunction with brazing in the assembly of heat rejection systems for the Jupiter Icy Moons Orbiter (JIMO). Another aim of the study was to ensure that the use of bonding agents could improve and simplify manufacturing.
In the case study mentioned above, how were the adhesives evaluated?
In this particular case study, maintaining robust thermal conductivity was an important goal for these adhesives and they were evaluated for voids, porosity and cracks between the bonded joints. Bonded surfaces were also subjected to extreme high and low temperatures to determine their long-term durability.
Butt-strap tensile (BST) lap shear strength was measured after exposure to 530-600 K (494-620 °F/257-327 °C) for 24 hours on the high end and to liquid nitrogen 77 K (-321 °F/-196 °C) for 15 minutes on the low end of the spectrum. Testing was adjusted to 530 K after it was determined that subjecting bonded specimens to 600 K was too severe.
What performance properties were sought from the testing?
Mechanical performance, maintaining thermal conductivity, proper adherence of the substrates and adequate overall strength of the adhesive were all necessary to achieve success for this application.
What kind of results were seen during the testing?
Eighteen adhesives were tested using microscopic analysis. Of the eighteen, twelve adhesives were disqualified due to voids, porosity and cracks that were observed between the bonded joints.
The rationale for eliminating these adhesives was because this would not only adversely affect the strength of properties but also the thermal conductivity of the mated structure.
It is important to note that the initial results showed that some adhesive systems did not adhere well to titanium. To overcome this deficiency and improve adhesion, Ti coupons were grit blasted to roughen surfaces.
What were the conclusions reached by the researchers?
The final results of this study indicated that aluminum nitride filled Master Bond EP45HTAN shared the best mechanical properties and exhibited a shear strength of 8-9 MPa under the conditions tested.
The study revealed that after bonding with EP45HTAN, the tensile failure took place in the outer ply of the carbon-carbon composite, demonstrating that the adhesive was stronger than the composite substrate being joined together.
What are some of the other product advantages of EP45HTAN and in what types of applications can this adhesive be used?
- Easily applied, paste-like viscosity
- Exceptionally long pot life at room temperature
- Exceptionally wide service temperature range
- Cryogenically serviceable
- Thermally conductive and electrically insulative
- Superior dimensional stability
EP45HTAN can be used in aerospace, electronic, specialty OEM, automotive, oil and gas processing, among other industries where extreme low and high temperature resistance and thermal conductivity are important requirements.
About Venkat Nandivada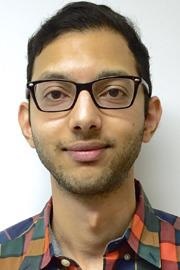
Venkat Nandivada - Manager of Technical Support at Master Bond Inc since 2010. He has a Masters in Chemical Engineering from Carnegie Mellon University. He analyzes application-oriented issues and provides product solutions for companies in the aerospace, electronics, medical, optical, OEM and oil/chemical industries.
Reference
- Cerny, Jennifer, Gregory Morscher. Adhesive Bonding of Titanium to Carbon-Carbon Composites for Heat Rejection Systems. http://ntrs.nasa.gov/archive/nasa/casi.ntrs.nasa.gov/20060051753.pdf
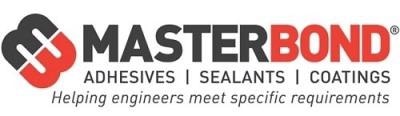
This information has been sourced, reviewed and adapted from materials provided by Master Bond Inc.
For more information on this source, please visit Master Bond Inc.
Disclaimer: The views expressed here are those of the interviewee and do not necessarily represent the views of AZoM.com Limited (T/A) AZoNetwork, the owner and operator of this website. This disclaimer forms part of the Terms and Conditions of use of this website.