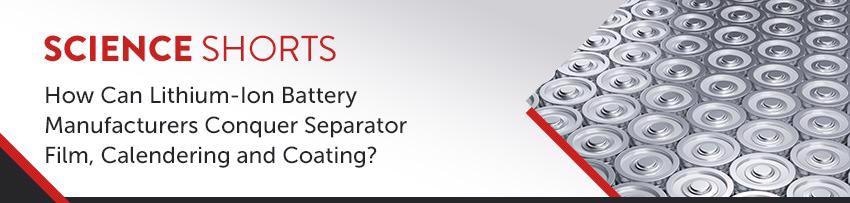
Research and Markets currently project that the global market for Lithium-ion (Li-ion) batteries will reach US$91.8 billion by 2025; this will be driven by the use of the batteries in a wide range of energy storage applications. The report goes on to say that electric vehicles (Evs) will be a major driver of growth.
On its website, the US. Office of Energy Efficiency & Renewable Energy explains how a Lithium-ion battery works:
“A battery is made up of an anode, cathode, separator, electrolyte, and two current collectors (positive and negative). The anode and cathode store the lithium. The electrolyte carries positively charged lithium ions from the anode to the cathode and vice versa through the separator. The movement of the lithium ions creates free electrons in the anode which creates a charge at the positive current collector. The electrical current then flows from the current collector through a device being powered (cell phone, computer, etc.) to the negative current collector. The separator blocks the flow of electrons inside the battery.”
The uniform coating of the anode and cathode materials, the use of high quality separator film and accurate thickness measurement of the calendered electrode are critical to the performance and safety of the battery.
Battery producers can improve these processes and in turn the quality, safety and efficiency of lithium-ion battery production by using online measurement and control technology. This will ultimately lead to reliable and high quality products.
Separator Film Lines
One of the key components of a lithium-ion battery is separator film. It can help to prevent short-circuiting and stop thermal runaways with its special thermal shutdown properties, all while still facilitating the flow of charged ions.
The safety and efficiency of separator film can be improved by coating it with materials such as ceramic.
Anode and Cathode Coating Lines
Applying a continuous pattern, patch or stripe coating on a copper (Anode) or aluminum (Cathode) substrate is challenging. However, it is critical to apply a uniform coating to avoid poor construction of the battery and to ensure the production of reliable and safe products.
Obtaining accurate control and measurement on both sides of the substrate ensures raw material savings, thereby improving both quality and yield.
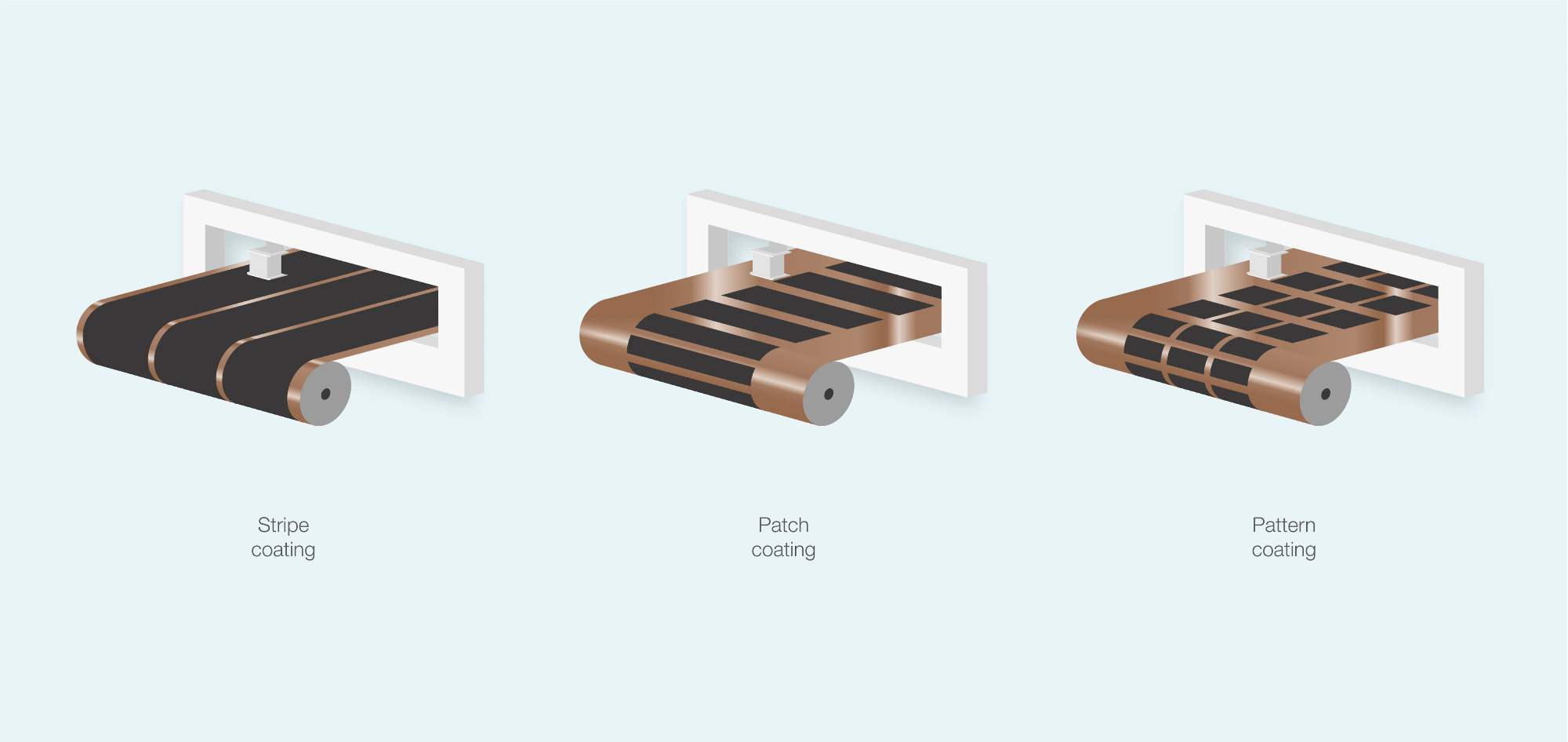
Image Credit: Thermo Fisher Scientific – Solutions for Industrial and Safety Applications
Calendering Lines
In the final process step, the coated electrode material is calendered for homogenous particle size and thickness. Pressing of the coating electrode assures the desired characteristics and improves adhesiveness and electrical contact. Coating thickness measurement and calender control are critical to ensure final dimensional accuracy and an overall high quality product.
To summarize, online control and measurement technologies for lithium-ion battery applications can provide results-oriented solutions to enhance profitability, improve quality and reduce costs by assisting battery manufacturers in meeting stringent customer specifications for the performance of materials while minimizing raw material waste.
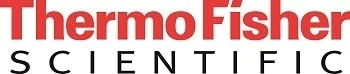
This information has been sourced, reviewed and adapted from materials provided by Thermo Fisher Scientific – Solutions for Industrial and Safety Applications.
For more information on this source, please visit Thermo Fisher Scientific – Solutions for Industrial and Safety Applications.