Owners and specifiers often need to create durable structures within a tight budget. This article describes some options for protecting steel structures from corrosion for several years whilst avoiding costly stripping and repainting schedules.
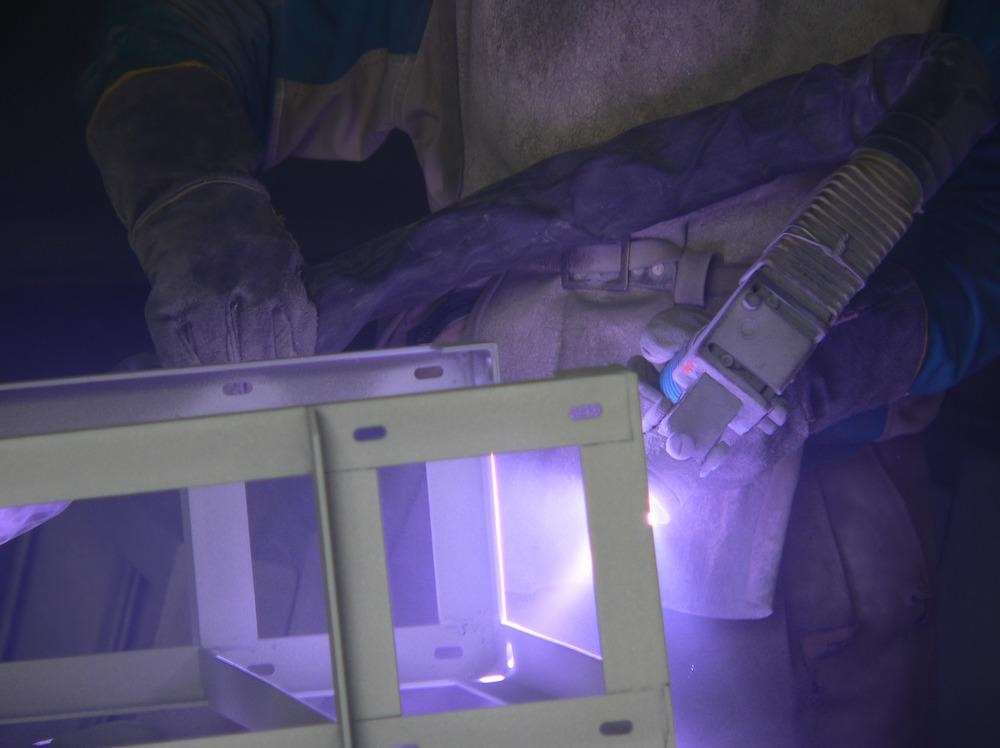
Zinc Spray Coating. Image Credit: Dainis Derics/Shutterstock.com
The Principle of Galvanic Protection of Steel
Various methods are available to protect steel from corrosion. One of the most elegant of these is the use of zinc. Zinc lies below steel in the galvanic series and therefore will corrode preferentially to steel, offering “galvanic protection”.
When galvanic protection is in operation, gaps in the zinc layer do not result in loss of steel but instead accelerate the corrosion rate of zinc. The conditions that need to be met to achieve galvanic protection are:
- the steel has to be electrically connected to the zinc
- the materials are close enough for a protective electrical circuit to be made through the corrosive environment
The second of these conditions is by far the harder to judge since service conditions vary greatly. So, in atmospheric corrosion, the metals must be immediately adjacent to each other, but in seawater immersion much greater separation of steel and zinc may be tolerated.
Options for Zinc Protection
There are three main options for the protection of large structures by zinc. Each has key advantages so it is important to assess each application’s particular circumstances.
Galvanized Steel
Galvanizing is extremely reliable but needs to be built into a project in the design stage to ensure that the components can be prepared and coated prior to manufacture.
Galvanized steel can come as hot-dipped or electrogalvanized. Hot dipped galvanized steel is generally exceptionally reliable and predictable, and can be supplied at a number of different thicknesses.
The lifetime of the material is extended by the intermetallic layers (iron-zinc) that forms as the steel is dipped into molten zinc.
This layer ensures that the coating cannot fail by delamination and actually corrodes slower than the outer zinc layer, so visible rusting of a hot-dipped galvanized structure does not automatically mean that the structure itself is suffering physical damage.
Electrogalvanized steel is extremely useful, predictable and flexible but does not possess a protective intermetallic layer.
The material is produced using an electroplating operation and is most commonly used on strip steel products. A range of finishing treatments can be applied to optimize the performance of the product.
Both hot-dipped and electrogalvanized zinc coatings protect steel galvanically.
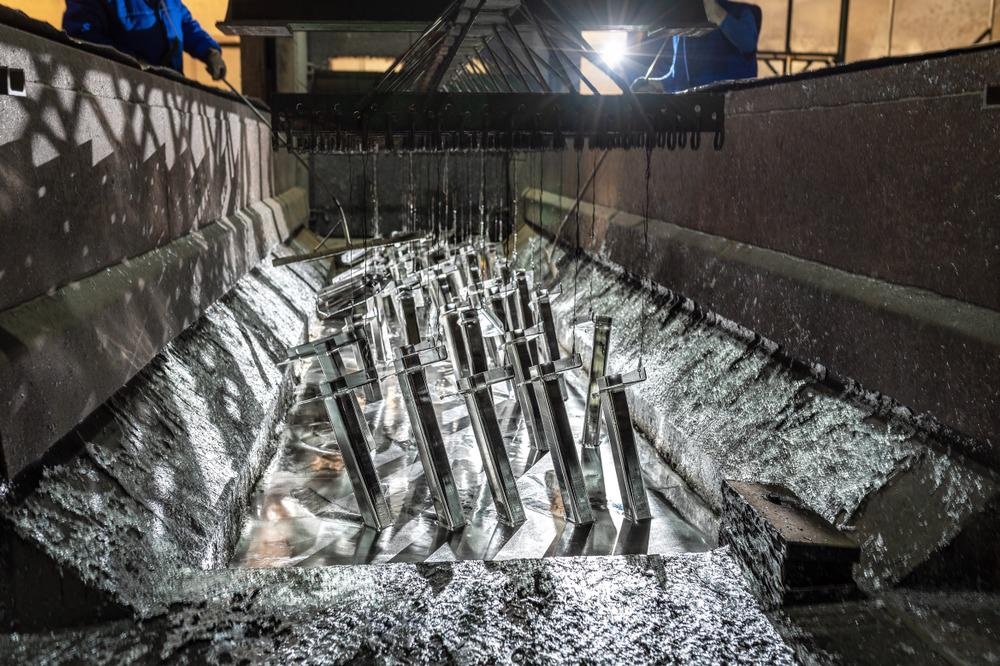
Galvanizing Steel in a Hot Zinc Bath. Image Credit: Bogdan Vija/Shutterstock.com
This is crucially important because corrosion does not spread underneath the coating meaning any damage is initially limited and therefore easier to repair.
Thermally Sprayed Zinc
Thermally sprayed zinc coatings can be applied to large structures post-manufacture.
Close relatives of thermally sprayed zinc coatings are aluminum-zinc and pure aluminum.
Zinc is more active than aluminum so it is generally more suitable for lower-corrosivity inland applications whereas aluminum-bearing alloys find use preferentially in marine applications.
Very large structures such as wind towers can be coated as long as the necessary pre-coating conditions can be met.
Correct surface preparation ensures intimate contact of the steel and coating to activate the corrosion-limiting galvanic protection.
Multiple applications can be used to build up the thickness of the coating. The lifetime of the coating is predictable and improves with increasing coating thickness as long as the bond between the coating and the structure is sound.
Thermally spraying structures is a skilled job and accredited contractors should be used whenever possible, since a poor steel-zinc bond results in premature failure.
Zinc-Containing Coatings
Zinc-containing coatings may seem to be the ideal solution where galvanizing and thermally sprayed zinc are impractical.
However, there are many different types and grades of these coatings and consideration should be given to consulting professional help before using one of these coatings for a critical application.
The use of these coatings is often referred to as “cold galvanizing”.
A great advantage of these coatings is their simplicity for use on-site, however adherence to specification on-site can be problematic, with both the preparation of the surface prior to painting and actual choice of zinc coating (the specified coating might not be immediately available) being possible areas of deviation.
Poor mixing of the paint is another potential problem as the zinc pigment can settle and may be difficult to disperse.
The zinc used in these coatings varies in particle size and oxide content – both of these factors can affect the paint performance as to obtain galvanic protection the particles need to align and conduct through the body of the finished product.
Zinc coatings are the most accessible solution for many applications and can offer sound protection.
For previously galvanized or thermally sprayed structures these coatings can effectively extend lifetime, protect welds, cut edges, and other defects. There are also many examples of these coatings being used as the primary anti-corrosion tool with great success, even in challenging environments.
References and Further Reading
The Galvanisers Association. (n/a). Atmospheric Corrosion Resistance. [Online]. https://www.galvanizing.org.uk/atmospheric-corrosion/
ISO. (2017). Zinc coatings — Guidelines and recommendations for the protection against corrosion of iron and steel in structures — Part 1: General principles of design and corrosion resistance. [Online]. https://www.iso.org/standard/71135.html
Disclaimer: The views expressed here are those of the author expressed in their private capacity and do not necessarily represent the views of AZoM.com Limited T/A AZoNetwork the owner and operator of this website. This disclaimer forms part of the Terms and conditions of use of this website.