Carbon dioxide (CO2) is one of the most frequently employed gases in the beverage industry, while ‘carbonic acid’ is central to soft drinks’ and beers’ sparkling and refreshing qualities. Carbonic acid also improves the shelf life of still beverages.
CO2 is produced via fermentation in drinks such as beer or sparkling wine, though it may also be added artificially to drinks such as lemonade or soda water.
Artificially added carbon dioxide is pumped into the beverage under high pressure during the production process, with approximately 0.2% of the added CO2 reacting with water to form carbonic acid.
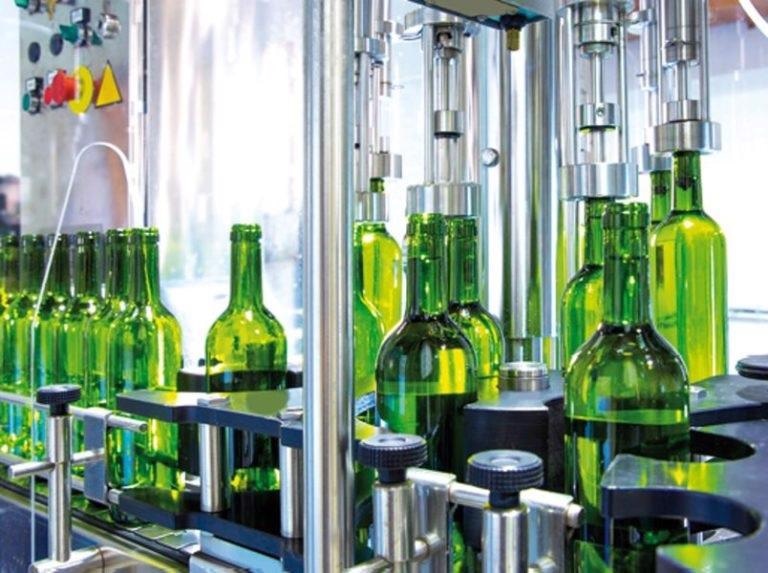
Image Credit: © stock.adobe.com
Gas Detection of CO2 and H2S
The efficient, accurate and continuous detection of a range of gases is an important safety consideration in beverage production and beverage bottling.
MSR-Electronic offers an array of reliable gas sensors, controllers and warning devices that are ideal for protecting employees, customers and equipment from combustible and toxic gases.
CO2 is also a key gas in winemaking, used in blanketing or to help keep oxygen away from wine to preserve its taste and color. Winemakers will typically utilize either N2 or a mixture of CO2 and N2. Under these circumstances, gas sensors will be used to measure oxygen content to ensure reliable gas detection.
The presence of H2S may lead to odor problems in the food and beverage industry, with the majority of food industry applications generating wastewater that is contaminated with high levels of biodegradable organic substances.
The odors caused by wastewater are but one of many ongoing environmental issues linked to the food and beverage industry - a nuisance that is often related to the release of hydrogen sulfide (H2S).
MSR-Electronic offers a comprehensive range of gas monitoring solutions specifically designed for the beverage industry. This range includes individual gas sensors and gas warning systems that are able to detect combustible or toxic gas concentrations.
CO2 Gas Sensors from MSR-Electronic
A standard gas sensor will contain three key components:
- A sensor element
- A measuring amplifier
- A μcontroller designed to process measured values
These components allow data to be processed and evaluated, for example, the temperature required to compensate the measured value.
It is also necessary to monitor calibration interval and errors, transmitting these to the evaluation device as required.
X-Change technology enables calibration to be performed with ease, by simply exchanging the sensor head or via the use of the system’s convenient, integrated direct calibration routine.
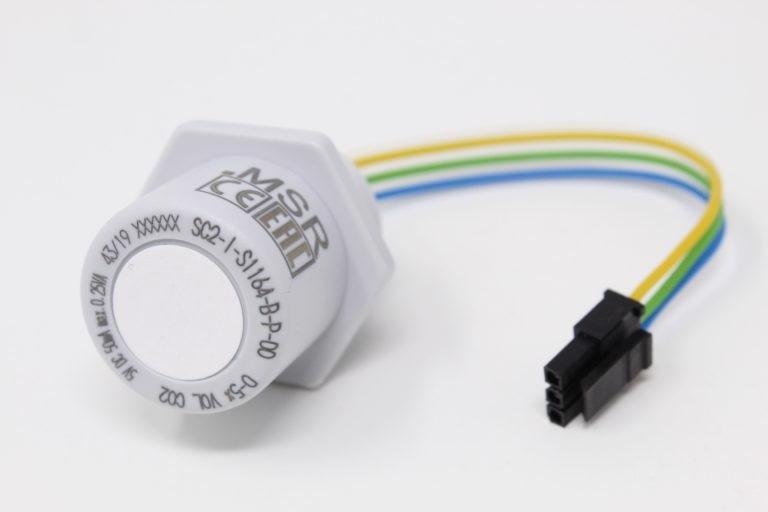
Image Credit: © MSR-Electronic GmbH, CO2 Gas sensor
Gas sensors from MSR-Electronic can also be connected to a range of MSR controllers and boards, allowing these to be interlinked, for example:
- The DGC-06 Gas-Controller is an ideal solution for large systems, able to manage up to 128 gas sensors.
- The Compactcontroller is able to manage up to 10 gas sensors.
- The MSC2 Controller is able to manage up to 3 gas sensors.
The Control Center: The DGC-06 Gas Controller
The DGC-06 Gas-Controller from MSR-Electronic offers an ideal solution for reliable gas detection. It is able to monitor and warn of the presence of toxic and combustible gases and able to accommodate a wide range of gas measurement techniques.
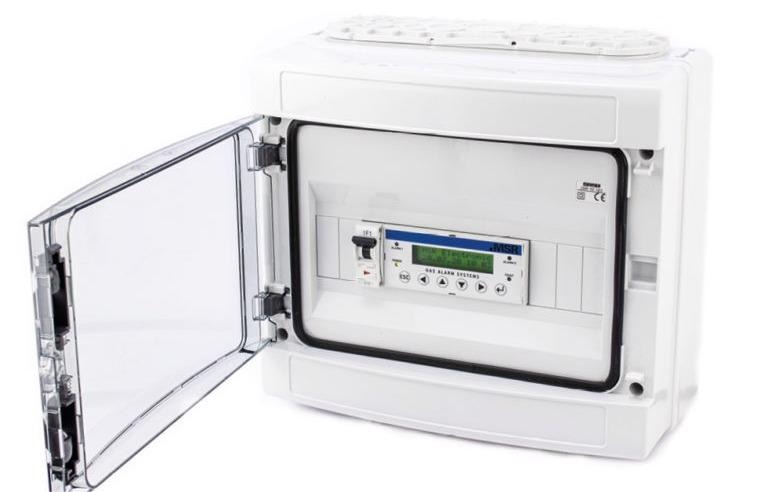
Image Credit: © MSR-Electronic Gas measurement device DGC-06
The instrument’s array of adjustable parameters and customizable set-points allow the DGC-06 Gas-Controller to be adapted to specific applications with ease.
As well as a number of roles in food and beverage applications themselves, the DGC-06 Gas-Controller can also be employed to monitor CO in garages, tunnels and even go-kart tracks in adherence with the current EN 50545-1 regulation.
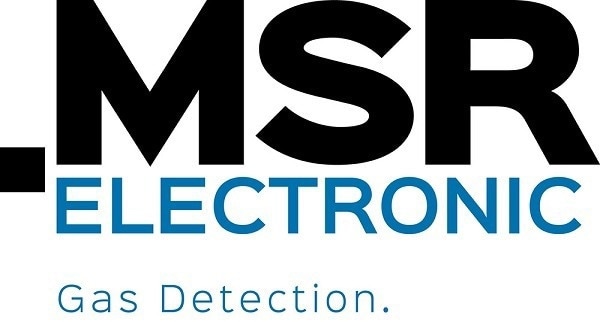
This information has been sourced, reviewed and adapted from materials provided by MSR-Electronic GmbH.
For more information on this source, please visit MSR-Electronic GmbH.