The aim of this paper is to review the current understanding of the adhesion when at least one of the two materials adhering is a polymer. The second material may also be polymeric, but also it may be an inorganic material such as a glass or metal. However the specific area of biological adhesion will not be considered, although it can reasonably be considered as polymer-polymer adhesion. Much of the field of adhesion is covered here, as adhesives are most commonly polymeric in nature. The reason for restricting the review to polymer adhesion is that polymers typically have rather different deformation processes than other materials and obtain their toughness from their long chain nature. They also typically have a lower modulus and deformation resistance than other materials. Hence deformation at a polymer-inorganic interface normally occurs within the polymer and failure often occurs within the polymer or at the interface. Hence it is the polymer, together with the interface chemistry, that often controls the adhesion. Failure within the polymer or at the interface is however not always the case. There is a range of situations where adhesion failure occurs within the inorganic material, particularly within a weak oxide or hydroxide film on a metal. Much of the technology of adhesion pre-treatments for metal surfaces is concerned with mitigating this failure in a weak oxide film. Factors to Consider When Looking At Polymer Adhesion When considering polymer adhesion it is important to recognise that the bulk mechanical properties of the polymer control the type of interfacial forces required for good adhesion. High adhesion can only be obtained if the interface can sustain sufficient stress to induce dissipative forms of deformation, such as flow, yield or crazing, in the polymer. Under most circumstances such deformation modes can only be obtained when the interface is coupled with a sufficient density of covalent bonds, together with perhaps some toughening effects due to surface roughness. However the rubbery but viscous polymer mixtures that make up pressure sensitive adhesives deform and dissipate energy at low stresses and so are capable of giving strong adhesion at an interface coupled just by Van der Waals forces. We shall hence consider the two situations separately. Adhesion of Glassy and Semi-Crystalline Polymers In this section we shall consider the adhesion of glassy and semi-crystalline polymers to other similar polymers and then to inorganic substrates. The approach is to first consider the forms of molecular coupling that can occur at the interface and then examine the way that this coupling can initiate deformation and energy dissipation in the polymer. Sources of Strength Most uncross-linked polymeric materials gain their strength from entanglement between the chains. The polymer chains form an entangled network that cannot pull apart when the material is in the glassy or semi-crystalline state. Instead, under stress the whole network deforms and then strain hardens as the chains become stretched. Fracture requires scission of these covalently bonded chains. To form strong polymer-polymer adhesion it is necessary for the network to be continuous across the interface. This continuity can be formed by (i) chain interdiffusion, if the materials are sufficiently miscible, by (ii) the use of coupling chains placed at the interface or (iii) by chemical reaction to form coupling chains at the interface. Coupling Chains Placed at Polymer-Polymer Interfaces Much of our understanding of polymer adhesion at a molecular level has come from the use of specific coupling chains, typically diblock copolymers. Such materials are also used commercially for the coupling between phases within polymer blends. A diblock copolymer consists of linear chains each of which contains two chemically distinct blocks of repeat units made of materials which shall be designated A and B. Diblock copolymers can be very effective coupling agents between bulk polymers designated C and D, if the pairs A and C, and also B and D, are miscible or close to miscible. Of course the pairs A and C, and B and D, can be the same material. Examining Failure Mechanisms The most effective way to examine the mechanism of failure at a polymer-polymer interface has been to use coupling chains that contain some form of label and then look for the labelled section on the two fracture surfaces after interface failure, as shown schematically in Figure 1. Typically the label has been deuterium with the location of the deuterium found using ion scattering or secondary ion mass spectrometry (SIMS). Most information can be obtained if two sets of A-B diblock copolymer coupling chains are used, those with A deuterated, and those with B deuterated, though that is not a requirement. 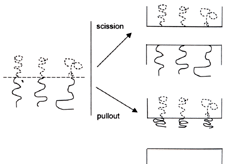 | Figure 1. Block copolymers tend to organise with the two blocks, shown as continuous and dashed lines, on either side of the interface. Chain pullout can be distinguished from scission by positions of the blocks on the fracture surfaces. | The Mechanism of Interface Failure The form of coupling, that is to say the mechanism of interface failure, has been found to depend on the molecular weight of the coupling chains. Short chains can pull out of the bulk material at a force that increases with the length of the pulled-out section. As the length of the chains increases to somewhere between one and four times the length required to from an entanglement in the melt, the force required for pullout becomes greater than the force to break chains, so they fail by scission. The scission force is typical of that required to break carbon-carbon bonds, about 2 nN, consistent with both calculations and estimates from flow experiments. The extent of adhesion is strongly affected by the molecular failure mechanism as tough interfaces are normally only obtained when the failure is by scission. However scission failure does not guarantee a tough interface. Coupling by Polymer-Polymer Interfaces by Chemical Reaction A common technique to couple two bulk polymers is to introduce into one or both of the materials a small percentage of chemically modified chains that can react with the other polymer to form coupling chains at the interface. A classic example of this technique is the introduction into polypropylene of some maleic anhydride grafted polypropylene chains to induce coupling with a polyamide such as Nylon 6. The maleic anhydride functionality can react with hydroxyl end groups on the polyamide chain to form a graft or block copolymer at the interface. The molecular mechanism of interfacial failure can again be either pullout or scission of these coupling chains. Pullout at low force can occur if either one of the blocks in the copolymer formed at the interface is rather short or if there are too many coupling chains at the interface. In the polyamide-polypropylene example, where typically there are very few grafts per polypropylene chain, pullout is only expected if the grafted polypropylene chain is rather short which can easily happen as the grafting process tends to cause scission. The polyamide chain is typical of bulk material and so has a molecular weight well above the entanglement molecular weight to give the material a useful cohesive toughness. In other systems, when multiple grafts are possible on a single chain, then the coupling chains can become so densely packed at the interface that they exclude other chains and so cannot entangle well with the bulk material, causing pullout failure. This situation has been observed when the chains themselves were long enough to entangle. Coupling Polymers by Interdiffusion Coupling by chain interdiffusion can occur if the two polymeric materials are miscible in each other, or at least sufficiently miscible to form a broad interface. Welding is the most common form of interdiffusional coupling but chain interdiffusion is also important in solvent bonding. Polymer diffusion normally occurs by the process of reptation, a form of curvilinear diffusion in which the chain moves a long a ‘tube’ formed by its entanglements with all the other chains. Hence interface coupling is formed by a chain end initially crossing the interface and then slowly more of the chain following it across. Failure after short joining times is thus expected to be by chain pullout; with chain scission failure occurring as the diffusion distance increases. There has been a considerable amount of work on the kinetics of chain coupling in welding but the problem is not solved, as the initial location of chain end groups with respect to the interface is not well known. The Effect of Miscibility If the two materials are not fully miscible then a broad interface will remain at equilibrium and the extent of adhesion will depend on the width of the interface. For long chains failure is expected to occur by a combination of pullout of loops and chain scission but there is little evidence in the literature that this is the case. Coupling by Reaction and by Adhesion It is not possible in all cases to distinguish clearly between coupling by reaction and by adhesion. Sometimes diffusion of chains across the interface is required to permit significant chemical reaction between chains in cross-linking systems. A slightly more complex situation occurs in the technically important polyimide PMDA-ODA that is often deposited from solution as a polyamic acid and then cured to from a thin layer of the polyimide. If a second layer is deposited on a fully cured first layer very little adhesion is obtained. If the first layer is only part cured, or if a thin film at the surface of a cured first layer is chemical reverted to polyamic acid, then interdiffusion and good adhesion can be obtained. Clearly coupling here requires diffusion but chemical reaction as well cannot be ruled out. Solvent Boding or Welding Solvent bonding or welding is an interesting case of coupling by interdiffusion that is little understood. Interdiffusion presumably occurs in the presence of the solvent, even if the polymers are immiscible in the melt. However there is little information on what happens to the structure of the interface as the solvent slowly diffuses into the bulk material and the joint ages. Coupling of Polymers to Inorganic Substrates Much of the chemical approach to adhesion studies is concerned with the molecular level mechanisms of coupling polymers to inorganic materials. No attempt will be made here to summarise the existing theories of adhesion as they are well covered in a number of reviews and books. Instead the aim is to review some well-defined situations where there is good evidence of the existence of a specific coupling mechanism. Bonding Mechanisms at Polymer-Polymer Interfaces As emphasised in the introduction, it will be assumed here that simple dispersion Van der Waals forces are not sufficient to cause significant adhesion between a flat, smooth inorganic substrate and a glassy or semi-crystalline polymer. This assumption is based on the knowledge that such forces are not sufficient to cause a strong interface between a pair of polymers. If they were, welding between polymers could give a strong interface just by making good contact without interdiffusion. Also welding would be effective between cross-linked polymers. In fact chain interdiffusion or chemical reaction is a clear requirement for a strong polymer-polymer interface. As interdiffusion is impossible at a polymer-inorganic interface, it seems reasonable that strong adhesion requires interface bonds of higher energy (really higher strength) than obtainable with just dispersion forces. Hydrogen bonds, acid-base interactions or covalent bonds are required. Adhesion Between Polymers and Inorganic Substrates Much of the work on the adhesion between polymers and inorganic substrates is based on correlations between an estimated thermodynamic work of adhesion, often based on contact angle measurements, and a macroscopic measure of adhesion. The correlations can be good but, in the opinion of this author, they do not demonstrate that dispersion forces can provide sufficient coupling to cause good adhesion on smooth substrates. The inclusion of estimates of hydrogen bonding and acid base interactions into the work of adhesion is probably important, as is the relation between work of adhesion and wetting, particularly of rough surfaces. The Mechanics of Adhesion Testing One issue that has often adds difficulty to the understanding of adhesion is that the mechanics of adhesion testing can be complicated, particularly when the two materials, such as a polymer adhesive and a metal substrate, have such different elastic moduli. The elastic stress pattern at the crack tip cannot formally be described by the fracture mechanics relationships that apply to cohesive failure. However the standard fracture mechanics approach is a good approximation in most practical situations. At a more practical level it is necessary to recognise that simple specimen design can often result in considerable shear stress components on the interface which cause crack tip yield and make a poorly coupled interface appear tough. However a different specimen design that causes mainly opening mode at the interface, will demonstrate the low interface toughness. This review is written using the assumption that an interface can only be considered tough if it has a high failure energy in opening mode. Adhesion Between Polyimide and Metals The adhesion between the polyimide, PMDA-ODA and metals such as copper or chromium has received considerable attention due to its importance in the microelectronics industries. Typically copper lines are coated with chromium to improve their adhesion to polyimides. As mentioned, the PMDA-ODA is normally deposited from solution as the polyamic acid and cured in-situ to the imide form. Adhesion of the polyimide deposited on a metal is therefore a different problem than adhesion of a metal deposited on the cured polyimide. The former situation tends to give stronger adhesion than the latter but there can be problems of metal, particularly copper, dissolution. The interaction between the metals and the polyimide has been studied in great detail using x-ray photoelectron spectroscopy (XPS) and other surface analysis techniques but there is not complete agreement on the form of the interaction. However it is clear that strong interaction and electron transfer occurs when the metal is deposited from vapour onto the polyimide. When the polyamic acid is deposited on the metal and cured then reaction occurs between the acid and the metal. The strong interface formed between chromium and the polyimide is clearly a result of the strong chemical interaction but there is still considerable interest in making it more resistant to water and oxidation. Adhesion Between Epoxy Resins and Glass A second system that has been studied extensively because of its technical importance is the adhesion between epoxy resins and glass, particularly glass fibres. To improve the hydrolytic stability of the composite, the glass surfaces are normally modified by covering them with a thin layer of a silane adhesion promoter. These silanes are well known to self-assemble into mono-molecular and multi-molecular layers on surfaces such as glass or silicon dioxide. One end of the silane molecule typically has di or tri methoxy or ethoxy functionality whilst the other end normally has amine or epoxy functionality. The ethoxy functionality is believed to condense with the hydroxyl functionality on the surface of the glass whilst the amine functionality can react with the epoxy, as shown in Figure 2. Hence it is attractive to suggest a simple picture of a single molecular layer of silane adhesion promoter between the epoxy and the glass. However the real situation is much more complex. The amount of silane typically used is much too great to form a monolayer. Also as the silane has multi methoxy or ethoxy functionality it can self condense. The relatively thick layer of silane is believed to form a network and then the epoxy both mixes into and reacts with the network. Although it is clear that the silane causes covalent bonding between the glass and the epoxy, there is no way to estimate the actual density of coupling produced. It is interesting to note that fairly good adhesion can be obtained in dry conditions without the silane, however it has a profound effect on adhesion in the presence of water. 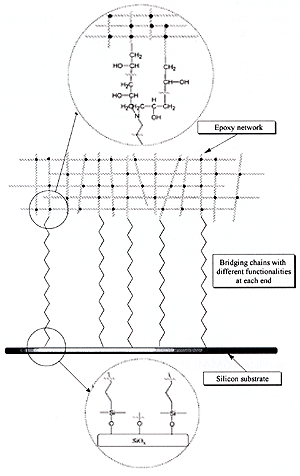 | Figure 2. Diagram illustrating the way bridging chains, with silane functionality at one end and amine functionality at the other, can form covalent links between an epoxy network and glass substrate. | Silanes as Adhesion Promoters Similar silanes are used as adhesion promoters between silicon dioxide and polyimides, such as PMDA-ODA However other techniques that form covalent coupling also work well. For example glycidyl methacrylate (GMA) chains, which contain epoxy functionality, can be grafted onto the surface of the silicon dioxide before deposition of the polyamic acid. On curing the GMA chains react with the polyimide. Grafted chains have also been shown to be very effective in coupling between a polyethylene and glass. The grafted polyethylene chains were obtained by reacting ethylene chains terminated by a monochlorosilane functionality with the glass. Adhesion Between Polymers and Substrates Adhesion between a polymer and a substrate often shows a maximum as a function of the number of grafted chains, or alternatively, the density of ‘stickers’ along a chain. This maximum is believed to have its origin in the requirement that the chains that are attached or tethered to the substrate must also entangle with the bulk material. The entanglement is restricted if the chains are densely end-tethered or, alternatively, have a high density of sticker groups along them. Failure Mechanisms and Interface Toughness As mentioned above, low molecular weight, uncross-linked glassy and semi-crystalline polymers tend to be very brittle. Cohesive failure normally occurs by chain pullout with very little deformation close to the crack tip. As the molecular weight of a glassy or semi-crystalline polymer is increased above the entanglement molecular weight, the toughness increases rapidly as crazes or yield zones begin to form and dissipate energy close to the crack tip. Eventually the toughness saturates at high molecular weight as chain pullout becomes insignificant. Very similar patterns of deformation and failure occur close to an interface in the adhesion situation. Consider first the extent of deformation when there is adhesion and the polymer (assumed to be high molecular weight) fails in the bulk by crazing. When the length or number of coupling molecules is low, failure occurs by simple chain scission or pullout with little bulk deformation. As the ability of the interface to withstand stress is increased by increasing either the length or number of coupling molecules, the failure mode changes and crazing starts to occur. This transition occurs when the product Σf becomes greater than the crazing stress σc, where Σ is the areal density of connectors, f is the force to break or pull out a connector. The toughness often shows a discontinuous jump at this transition. As Σf is further increased above σc, normally by increasing the areal density of connectors, the toughness continues to increase approximately as (Σf)2. This basic pattern has been seen at interfaces between two glassy polymers, at an interface between a glassy polymer and a cross-linked network and at interfaces between semicrystalline polymers. The failure energy is dissipated in growing a primary craze at the crack tip and final failure occurs within this primary craze, as shown in Figure 3. As the stress across a craze is approximately independent of its width, the toughness varies linearly with the maximum width of this primary craze. The dependence of the interface toughness on Σ2 has been explained by a model that relates the stress concentration on the craze fibrils at the crack tip to the width of the craze. Failure is assumed to occur when the stress on a craze fibril at the crack tip reaches a critical value required to break or pullout the molecules. This model essentially relates the molecular failure event, a chain pullout or scission, to the macroscopic toughness of the adhesive joint. 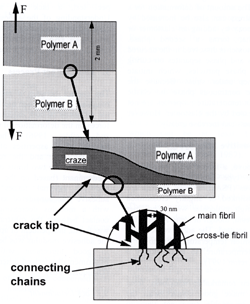 | Figure 3. Schematic representation of the structure at the crack tip in a crazing material are shown at three length scales. It is assumed that only material A crazes. The whole of the craze consists of lain and cross-tie fibrils. | Deformation in Epoxies The energy dissipation and failure processes are not as well understood in materials, such as cross-linked polymers, that deform at the crack tip by yield and shear banding, rather than crazing. This lack of understanding is highly relevant in adhesion as the classic structural adhesives, epoxies, are highly cross-linked and do not craze. Instead epoxies deform by the formation of diffuse yield zones. The size of the yield zones, and hence the energy dissipation on crack propagation, can be increased by decreasing the cross-link density of the material. However decreasing the cross-link density inevitably increases the viscosity and decreases the glass transition temperature of the epoxy, so limiting this approach to increasing the toughness of adhesive joints. The amount of deformation for a given interface stress can also be increased by modifying the epoxy by adding an elastomer or thermoplastic that forms a second phase. Typically an elastomer is dissolved in the uncured epoxy monomers and phase separates on curing to form second phase particles, which initiate deformation zones under stress. Because the epoxy forms the continuous phase the elastic modulus and high temperature properties are not profoundly depressed by the elastomer. However the epoxy toughness can increase greatly. Pressure Sensitive Adhesives As mentioned above, a second class of polymer adhesion is the type exhibited by pressure sensitive adhesives (PSA’s). These materials are typically uncross-linked or slightly cross-linked mixtures of a high molecular weight polymer with a tackifier resin, though in some systems the tackifier resin is omitted. The adhesive normally has a glass transition temperature 20°C to 50°C below the use temperature, so is essentially a rubbery liquid. How Pressure Sensitive adhesives Work PSA's obtain their remarkable 'stickiness' from their ability to make good contact with the substrate in a reasonable time but then to dissipate a large amount of energy on removal. To make good contact between the rough pressure sensitive adhesive surface and the rough substrate the pressure sensitive adhesive must be able to deform elastically and perhaps viscously under low external stresses. With intimate contact comes the formation of Van der Waals bonds between the adhesive and the substrate. pressure sensitive adhesives often contain a fraction of acid or ester units within the chains as these can both improve the interaction strength with a number of substrates and modify the viscous properties. Removal of a PSA at a reasonable speed causes a large amount of viscoelastic energy dissipation within the material, often with the formation of fibrils. As the energy loss is primarily viscous, it is inevitably rate dependent. The energy loss and hence joint toughness tend to be low at very low crack propagation rates and so pressure sensitive adhesives tend to have poor long-term holding power. Measuring Adhesion Strength of Pressure Sensitive Adhesives The measurement of pressure sensitive adhesives adhesion is normally done using one or more of three different tests, a peel test, a tack test and a shear test. Understanding of the adhesion process can be obtained by considering first the contact making process, then the detachment process in the tack test, and finally the peel process. The Contact Process The contact between a rough substrate and a rough adhesive has been modelled by considering the influence of both external load and surfaces forces on the deformation of the adhesive. The roughness was represented as asperities of varying height but fixed curvature and the real area of contact estimated in the two limits of (a) surfaces forces predominant (based on the classic JKR theory) and (b) external forces predominant. The adhesive was considered as an elastic medium with a modulus decreasing with time. Good contact between the substrate and the adhesive was found, independent of applied pressure, when the adhesive modulus was below a critical value, in good agreement with a well-known experimentally derived criterion for a good pressure sensitive adhesive. Tack Detachment In a tack test an adhesive covered substrate is pressed against a flat punch for a short time at a fixed pressure and then the joint is pulled apart The force and energy involved in the detachment process are measured, and shown schematically in Figure 4. As the two surfaces are moved apart the force increases rapidly to a maximum and then, for strong adhesion, tends to drop to a nearly constant value where it remains until final detachment. For weaker adhesion the force decreases rapidly to zero (detachment) after the maximum. The work of detachment can be very different between these two cases. In the strong adhesion case the adhesive forms voids and then fibrillates during the stress plateau with much energy dissipated in drawing out the fibrils. The adhesion energy, measured in either tack or peel tests, is known to be strongly influenced by the viscoelastic nature of the adhesive. It is greatest with high molecular weight, slightly cross-linked polymers with a large molecular weight between entanglements and a glass transition temperature about 50° below the use temperature. 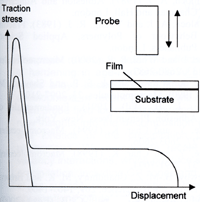 | Figure 4. Schematic representation of the probe tack test showing typical results for both strong and weak adhesion (see text). | The tack test has been the subject of two recent models, both of which are concerned with the growth at the interface of cavities that themselves initiate fibrils that grow within the adhesive. Both models are based on the assumption that the cavities grow from voids at the interface, caused by substrate and adhesive roughness. The models both assume that the adhesive is elastic but differ in the detailed mechanics. Peel Detachment In the peel test the backed adhesive is left in contact with the substrate for a long time and then peeled away at a fixed angle, often 90° The test measures the toughness of the interface. It is assumed that the adhesive has had time and pressure to make good contact with substrate so voids and roughness are no longer an issue. A polymer film or a cloth backs the adhesive so that it can be peeled away from the substrate without stretching in the pulling direction. The peel force, which relates directly to the interface toughness, normally is found to increase considerably with the rate of crack propagation. Sometimes as the crack propagation rate increases it shows a maximum and sharp drop as the mode of separation changes, perhaps from cohesive to interfacial, though not necessarily. This mode change is familiar to most people in the removal of adhesive bandages from skin. Increasing Peel Energy The monotonically increasing peel energy can often be described by a classic model that equates it to a product of the thermodynamic work of adhesion between the substrate and the adhesive and a viscoelastic dissipation function. The latter, which can be at least 100, is entirely phenomenological and depends on rate and temperature. The process of energy dissipation often, as in the tack test, involves fibrillation, though here it is likely that the fibrils form after a meniscus instability process at the crack tip. There is currently no model that predicts this viscoelastic dissipation in fibrillar peel. Weak Adhesion For weak adhesion situations it is clear that the thermodynamic work of adhesion is not the crucial parameter that controls the adhesion. Interfacial slip or its absence can have a profound effect. Increasing the ease of interfacial slip by increasing the molecular mobility of the substrate causes a strong decrease on the peel energy. The peel energy in this situation has been modelled as a viscous dewetting process with the dissipation controlled by the contact angle. It would seem likely that release films and release coatings operate, at least partly, by increasing the slip at the interface. Conclusions In attempting to understand adhesion it is valuable to distinguish between the molecular level coupling that occurs at the interface and the energy dissipation process that occur in the bulk materials adjacent to the interface. Although molecular level coupling is required for good adhesion, the type and strength of coupling required depends on the deformation processes of the bulk materials. Understanding of adhesion in particular cases then is likely to come from a knowledge of the interface chemistry, the deformation and failure properties of the relevant materials and the mechanics of the testing. Note: A complete list of references is available by referring to the original text. |