The life of the clutch, being an integral component of the transmission, directly impacts the gearbox's stability. A finite element model and a thermodynamic numerical method of a multi-disc clutch are developed in a study in the journal Materials to examine the effect of material characteristics on the contact pressure distribution.

3D diagram of a multi-disc wet clutch. Image Credit: Liu, Y., et al., Materials.
To begin, the pressure distribution index (PDI) was presented to measure the pressure differential between friction pairs. The clutch static pressure experiment confirmed the numerical model's correctness.
The wet multi-disc clutch, which determines the transmission's durability and safety, has long been critical in car gearboxes. Significant work has been spent on extending transmission life by overcoming wet clutch issues such as wear, buckling, breaks, and so on.
Fei et al. discovered that friction components with high porosity might reduce surface temperature, resulting in increased wear resistance. Because Fe might improve the material's strength and hardness, the wear rate dropped before rising as the Fe concentration rose.
Further research from China by Yu et al analyzed the wear processes of copper-based and paper-based friction materials, finding that the wear depth increased dramatically with rising air temperature.
Moreover, using connector tests, the significant effect of temperature on wear parameters was confirmed. Using slide tests and calculations, the researchers in the journal Materials investigated the thermal buckling phenomena of clutches.
They hypothesized that corrosion happened when temperature distribution was non-uniform in the radial direction. They studied the clutch crack phenomena and discovered that fractures typically developed around hotspots. As a result, the temperature of friction components significantly impacts clutch stability, and high temperature is the main cause of clutch failure.
In order to increase the clutch temperature distribution, several numerical models and practical demonstrations have been performed. Li et al. developed clutch heat transfer models and found the effects of carbon fiber density and specific heat capacity on the clutch temperature field.
Reduced carbon fiber content increased porosity, allowing lubricating oil to be discharged more efficiently, resulting in a clutch by putting forward a thermodynamic model. Another researcher discovered that the friction material containing granulated carbon black had a lower temperature than high-strength graphite. Others found that the transparency of the material might influence clutch temperature distribution.
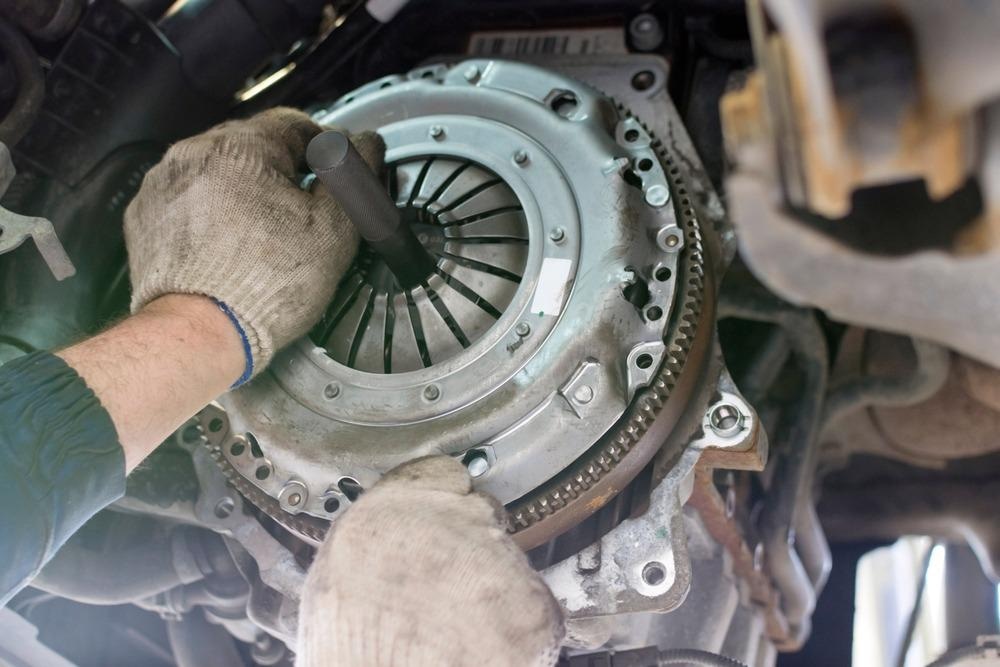
Image Credit: Ulianenko Dmitrii/Shutterstock.com
Further, many factors such as composition, temperature, and operating circumstances, might influence material transparency. Research by Ma et al. claimed that the metal matrix's heat capacity might also influence its temperature.
Previous research conducted by Xiao et al. evaluated the wear process of Cu-based brake pads. They discovered that certain debris might become stuck between friction surfaces, creating a further rise in temperature. As a result, almost every feature of the friction material has an impact on clutch temperature distribution.
Additionally, the working conditions in terms of temperature are important. It was found that raising the friction discs' system pressure, starting angular acceleration, and transparency might result in a high-temperature rise.
Clutch temperature fields were analyzed while considering friction disc grooves. The researchers simulated non-uniform clutch contact and found that the surface temperature slowly increased when the contact ratio lowered.
Many studies show that friction materials directly influence the temperature field. However, these studies mostly focused on failures and temperature transfer mechanisms using a simple single friction-pair model. The actual clutch structural characteristics significantly impact the contact pressure distribution difference, resulting in irregular temperature profiles on friction components.
A circlip restraint of this type causes a significant concentration of force in the clutch, resulting in an unequal distribution of contact pressure. Due to the limits of the transmission system's spatial design, such a structure is generally used in heavy-duty vehicles. Temperature and pressure fields are known to have a positive correlation.
The effect of clutch construction on contact pressure distribution has already been studied in depth. The impact of material parameters, on the other hand, is rarely studied, and these possibilities remain unexplored.
In order to explore the effect of material characteristics on the contact pressure condition distribution, a finite element model and a thermodynamic numerical model of a wet multi-disc clutch were created. The pressure differential between friction pairs was originally evaluated using PDI. Furthermore, clutch static pressure experiments were carried out to validate the abovementioned numerical models.
Finally, the optimal clutch material parameters were suggested by increasing the EM and PR of the backplate and decreasing the PR of the steel discs. The difference in clutch pressure distribution may be drastically reduced. The friction lining and circlip material parameters have little impact on clutch pressure and temperature distribution.
The optimum material condition differences were minimized by 74 kPa and 14.9 degrees Celsius, 27.2 percent, and 10.3 percent, respectively.
References
Liu, Y., et al. (2021). Influence of Material Parameters on the Contact Pressure Characteristics of a Multi-Disc Clutch. Materials and Modelling for Extreme Loading Conditions. Published: 25 October 2021. https://www.mdpi.com/1996-1944/14/21/6391/htm
Li, M., et al. (2017). Analysis of the thermal buckling of annular disks in clutches under the condition of radial temperature gradient. J. Therm. Stress. 2017, 40, 1275–1284. https://www.tandfonline.com/doi/abs/10.1080/01495739.2017.1334251
Fei, J., et al. (2015). Effect of carbon fiber content on the friction and wear performance of paper-based friction materials. Tribol. Int. 2015, 87, 91–97. https://www.sciencedirect.com/science/article/abs/pii/S0301679X1500064X
Yu, L., et al. (2020). Investigation on the thermodynamic characteristics of the deformed separate plate in a multi-disc clutch. Eng. Fail. Anal. 2020, 110, 104385 https://www.researchgate.net/publication/338561053_Investigation_on_the_thermodynamic_characteristics_of_the_deformed_separate_plate_in_a_multi-disc_clutch
Ma, X., et al. (2021) Comparison of braking behaviors between iron- and copper-based powder metallurgy brake pads that used for C/C–SiC disc. Tribol. Int. 2021, 154, 106686. https://doi.org/10.1016/j.triboint.2020.106686
Xiao, J.. et al. (2020). Wear mechanism of Cu-based brake pad for high-speed train braking at speed of 380 km/h. Tribol. Int. 2020, 150, 106357. https://en.x-mol.com/paper/article/1248718598367903744
Disclaimer: The views expressed here are those of the author expressed in their private capacity and do not necessarily represent the views of AZoM.com Limited T/A AZoNetwork the owner and operator of this website. This disclaimer forms part of the Terms and conditions of use of this website.