The term ‘hydrogen induced cracking’ (HIC) refers to internal lesions resulting from material becoming trapped in budding hydrogen atoms. This can result in a loss of important mechanical properties as atomic hydrogen diffuses into a metallic structure and becomes saturated.
Should a build-up of molecular hydrogen be repressed, atomic hydrogen may enter the metal instead, rather than forming a gaseous reaction, forming a crack in the metal and negatively impacting its strength.
Steel can be designed to specifically resist hydrogen induced cracking, helping to mitigate this risk.
Where an application presents a significant risk of hydrogen induced cracking, for example, in boilers, it is advisable to utilize hydrogen induced cracking-resistant steel plates. This is a common occurrence in the gas and oil industry, which routinely employs steel pressure vessels.
Hydrogen induced cracking is regarded as a significant risk in wet H2S environments. These environments - referred to as ‘sour service’ – risk inducing cracking over an extended period, ultimately resulting in the entire pressure vessel failing.
Where the partial pressure of hydrogen sulfide is greater than 3.5 mbar, it is generally recommended to measure these risks and ensure these are properly managed.
Manufacturing Hydrogen Induced Cracking-Resistant Steel
The manufacture of HIC-resistant steel is typically accomplished in one of two ways.
The first method involves optimizing the steel manufacturing process to accommodate the need to be HIC-resistant from the outset; for example, forming steel that is corrosion-resistant and extremely high quality.
This approach ensures that the hydrogen induced cracking-resistant plate will be produced consistently and reliably enough to pass any necessary retests.
The second method involves producing a standard boilerplate, then testing this and determining whether this standard boilerplate is sufficiently HIC-resistant.
This method requires a lower initial investment and is more cost-effective, but because testing is only carried out on samples of steel plates, the risk of the plates not meeting regulations is far higher.
The manufacture of consistently high quality and reliable HIC-resistant steel involves a number of considerations.
The metallurgy of the steel should be carefully monitored, ideally by performing primary metallurgy testing and measuring ladle composition. The results of this testing should then inform the finetuning and optimization of further iterations of the steelmaking process.
Key Differences Between HIC and SOHIC
Stress-oriented hydrogen induced cracking (SOHIC) is a particularly serious issue that arises from steel’s exposure to hydrogen sulfide in wet and sour service environments.
SOHIC typically occurs where there is elevated hydrogen activity, resulting in a different cracking pattern to HIC and adversely affecting the heat-affected zone of welds.
Mitigating the Risk of Hydrogen Induced Cracking
Hydrogen induced cracking-resistant steel plates must be tested to determine their susceptibility to hydrogen induced cracking.
MASTERHIC from Masteel offers an ideal solution for fine-grain pressure vessels, allowing steel to be manufactured with the precise properties required for use in sour gas applications.
Masteel is a leader in this field, and the company’s experts can offer detailed insight into the optimal type of hydrogen induced cracking-resistant steel and testing methods for each application.
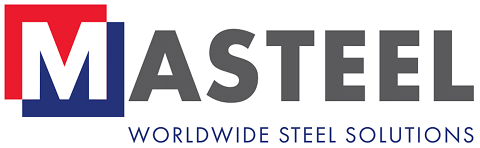
This information has been sourced, reviewed and adapted from materials provided by Masteel UK Ltd.
For more information on this source, please visit Masteel UK Ltd