Plasma cutting – occasionally referred to as ‘plasma arc cutting’ – is a melting process that sees a high-temperature ionized gas jet used to melt the material and expel it from a cut. This ionized gas can reach temperatures of more than 20000 °C.
The plasma cutting process prompts an electric arc to strike between an electrode and the workpiece (or a cathode and anode, respectively) before being recessed in a cooled gas nozzle. This limits the arc, prompting the creation of a narrow, high velocity, high-temperature plasma jet.
How Does Plasma Cutting Work?
Recombination occurs as the formed plasma jet hits the workpiece, prompting the gas to revert to its original state. This process emits intense heat, melting the metal and ejecting this from the cut along with the gas flow itself.
Plasma cutting is suitable for cutting a diverse array of electrically conductive alloys, including plain carbon and stainless steel, titanium and nickel alloys, aluminum and aluminum alloys.
The plasma cutting technique was initially developed to cut materials which the oxyfuel process was unable to cut effectively.
Key Advantages of Plasma Cutting
Plasma cutting offers a number of distinct advantages.
It is relatively cost-effective for medium-thickness cuts and can offer high-quality cutting for thicknesses of up to 50 mm while being able to accommodate a maximum thickness of 150 mm.
Plasma cutting can also be used to cut complex shapes due to its high accuracy. It also results in minimal dross and finishing requirements because the process removes excess material from the workpiece. Its rapid speed also minimizes heat transfer, reducing the risk of warping.
Plasma cutting can be performed on any conductive material – a notable advantage over flame cutting which is only suitable for use with ferrous metals. Plasma cutting offers a significantly smaller cutting kerf compared to flame cutting.
Plasma cutting offers an optimal approach to cutting medium thickness stainless steel and aluminum, offering more rapid cutting speeds than oxyfuel. CNC plasma cutting machines also offer exceptional precision and repeatability.
It is possible to ensure smaller heat-affected zones and reduced noise levels by performing plasma cutting in water.
Key Disadvantages of Plasma Cutting
Plasma cutting does result in a far larger heat-affected zone than conventional laser cutting. Yet, this can be mitigated by conducting plasma cutting in water.
Laser cutting tends to be more precise, particularly when working with thinner sheets and plates. Plasma cutting is also unable to cut the high thicknesses achievable using waterjet or flame cutting. It also causes a wider kerf than laser cutting.
Summary
While other forms of cutting may be a better, more accurate choice for some applications, plasma cutting offers a number of significant advantages when used with appropriate applications and materials due to its powerful, robust capabilities and cost-effective nature.
Masteel is able to offer extremely precise plasma cutting, which involves minimal heat transfer to the profiled steel, reducing the heat-affected zone and ensuring optimum quality.
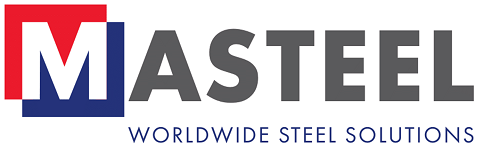
This information has been sourced, reviewed and adapted from materials provided by Masteel UK Ltd.
For more information on this source, please visit Masteel UK Ltd