This article discusses the process and significance of laser surface functionalization and considers this alongside the use of coatings.
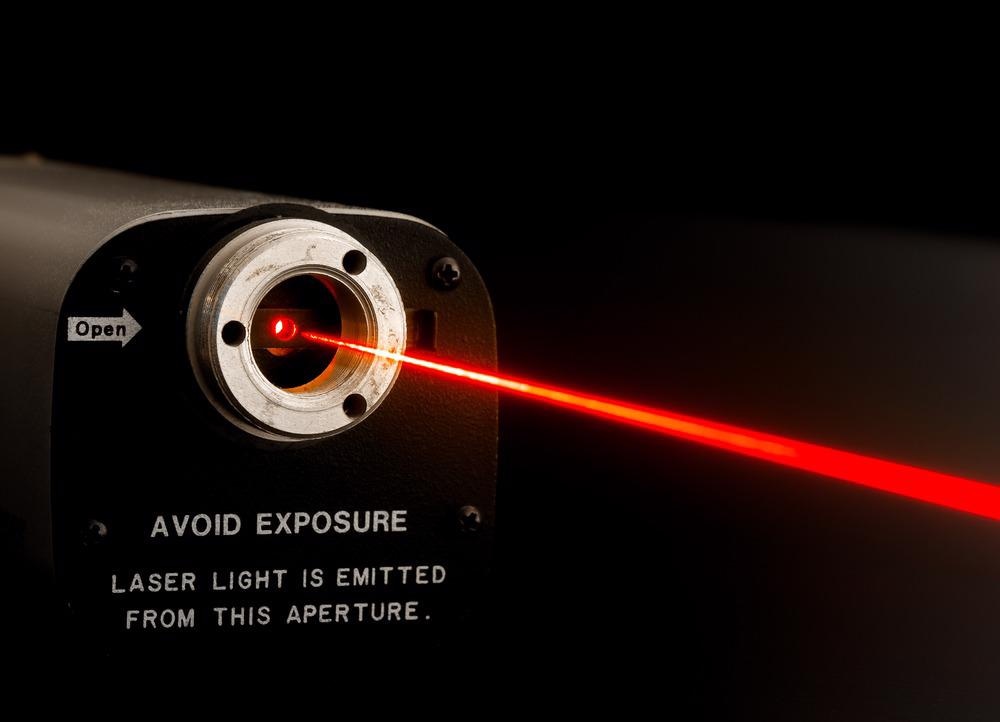
Image Credit: Doug McLean/Shutterstock.com
The surface of a material plays a pivotal role in determining its mechanical properties (e.g., friction and wear), the interaction with the environment (e.g., wettability), optical appearance, corrosion, adhesion etc. Additionally, chemical activity such as catalysis is also strongly dependent on the surface texture. The texture of surfaces can be changed when they are subjected to laser treatment. These changes enhance the utility of the material.
A surface engineer modifies solid surfaces to acquire novel, functional properties, and this newly developed material can be used in a wide range of applications. Many metals and their alloys, glass, polymers, etc., are subjected to laser treatment, which enhances their applicability, without applying any external coatings.
This technique involves the introduction of ultra-short pulse laser texturing, which is a popular one-step technique utilized to transform the surface properties of different materials to improve their functionalization required for various applications. Previous studies have revealed that laser treatments help gain several important characteristic features such as super-hydrophobicity and surface coloring.
Recently, scientists have conducted extensive research for a better understanding of the formation of laser-induced periodic surface structures (LIPSS). These structures possess improved mechanical and chemical properties. The nature of LIPSS strongly depends on the laser beam polarization. These structures are formed by irradiation with ultra-short linearly polarized laser pulses.
Factors on which Laser Surface Functionalized Structures Depend
Many scientists have explained the origin of structures differentially. One of the most accepted explanations is based on the interference of the incident laser radiation with electromagnetic surface waves, which are scattered or propagated at the surface of the material irradiated.
This process promotes intensity modulation that leads to selective ablation, producing various parallel structures with periods ranging between hundreds of nanometers and a few micrometers. Ablation is a process of removal or destruction of the molecules of the surface material by different processes, such as irradiation, vaporization, chipping, erosive processes, etc.
Surface patterns, on the sub- to several micrometer scales, result in the development of numerous surface functionalities. The formation of versatile and reproducible structures depends on various factors, such as wavelengths, customized micro-and nanometric spatial resolutions, varying laser pulse durations, and the rate of repetition of the laser sources.
Scientists have functionalized surfaces through LIPSS and included biomimetic functionalities on fluid transport, modified specific optical responses in technical materials, and customized the wetting properties (hydrophobicity, oleophobicity, hydrophilicity, oleophilicity, etc.).
Laser surface functionalization also enhances wear-resistance, catalysis, modified adhesion, improvement of tribological performance on metallic surfaces, and many more important characters. These surface features serve as templates for biological cell growth and develop antibacterial surfaces.
Importance of Laser Surface Functionalization
One of the important requirements of the nuclear industry is the availability of materials that can remain neutral and resist harmful radiation. These materials immensely help the working conditions of nuclear industry workers by prolonging its use while encountering radiation leakages. Typically, chromium is used as a corrosion-resisting and surface hardening agent; however, recent studies highlighted that it had adverse effects on human health and is carcinogenic.
Using Lasers to Create Super-hydrophobic Materials
Video Credit: University of Rochester/Youtube.com
Thereby, there is a need for alternate materials possessing similar properties without affecting human health. Scientists have developed materials using laser surface functionalization techniques that can withstand harmful radiations and, thereby, protect workers while working in a nuclear plant. Also, the efficiency of power plants (e.g., turbine blades that undergoes high stresses) could be improved by altering the surface properties of the material.
Biomimicry and Development of Unique Textured Surfaces
Many unique textured materials are present in nature that imparts exceptional properties, e.g., the surface of the lotus leaf remains dry in water. This is because of the presence of sharp spike-like structures on its surface to which water cannot adhere. Scientists have been inspired by this unique structure and developed a novel technology by biomimicking this concept.
Chunlei Guo, a professor at the University of Rochester’s Institute of Optics, used lasers with a high pulse rate (a quadrillion pulses per second) to transform a material without producing much heat. The pulsing motion of the laser helps develop unique structures by moving around the material’s surface in a precise manner.
Laser Surface Functionalization vs. Coating: Story of FLITE Material Science
Initially, Dan Cohen, CEO of FLITE Material Science, a startup company established in 2018, was looking for a coating that could keep snow, ice, and frost off of solar panels. He observed that, typically, coatings have many undesirable effects; for instance, they could change the color of the solar panel, contain toxic materials, and generate the need to be re-applied every year.
FLITE Material Sciences
Video Credit: Rice Alliance/Youtube.com
Chunlei Guo provided a solution to the existing problem. He came up with a technology that could protect solar panels from frost, rain, and snow, without the application of any coatings. This technology was based on laser surface functionalization which provided the panel materials with the ability to repel water and oil (hydrophobicity and oleophobicity) by itself. Additionally, this process helped prevent rusting of the solar panels.
Interestingly, this technology can be applied on a variety of surfaces including semiconductors and even human bone and teeth. Later, the University of Rochester agreed to license the technology and FLITE Materials Science to commercialize it.
FLITE Material Science spent its first year understanding this technology and exploring the product-market fit. They advanced the technique such that the material remains robust after altering the surface. At present, the company is aiming to apply the technology at a commercial scale targeting aerospace, life sciences, and other industries.
References and Further Reading
Korosec, K. (2021) Flite Material Sciences uses lasers, not chemical coatings, to keep ice and rust off surfaces. TechCrunch. [Online] Available at: https://techcrunch.com/2021/09/22/flite-material-sciences-uses-lasers-not-chemical-coatings-to-keep-ice-and-rust-off-surfaces/
Florian, C. et al. (2020) Surface functionalization by laser-induced periodic surface structures. Journal of Laser Applications. 32, 022063 https://doi.org/10.2351/7.0000103
Reif J. (2018) Surface Functionalization by Laser-Induced Structuring. In: Ossi P. (eds) Advances in the Application of Lasers in Materials Science. Springer Series in Materials Science. 274. https://doi.org/10.1007/978-3-319-96845-2_3
Gemini, L. et al. (2018) Surface functionalization of metal surfaces by large-area USP laser texturing. Proc. SPIE 10522, Frontiers in Ultrafast Optics: Biomedical, Scientific, and Industrial Applications XVIII. 105220F. https://doi.org/10.1117/12.229022
Disclaimer: The views expressed here are those of the author expressed in their private capacity and do not necessarily represent the views of AZoM.com Limited T/A AZoNetwork the owner and operator of this website. This disclaimer forms part of the Terms and conditions of use of this website.