From polishing optics to cutting sheet metal, abrasive materials play vital roles across an array of industrial applications. Industrial abrasives are usually comprised of grains of a hard manufactured material, for example, brown fused alumina.
This material can either be “bonded” – dispersed throughout a matrix made from a material such as rubber, glass or ceramic – or “coated” – adhered to a backing material, such as paper or cloth.
Coated abrasives are often used for power tools such as belt sanders or orbital, while bonded abrasives can be shaped for applications, including rotary tool heads and cutting/grinding wheels.
Abrasives can also be suspended in wax, paste or liquid, such as in polishing agents for lenses; or used in combination with compressed air for sandblasting.
Whether abrasives are used for cutting, drilling, grinding, buffing or honing, the mechanism of action is similar. On the microscale, abrasives are comprised of small, sharp tips. These tips make minute cuts in the workpiece, which steadily results in the removal of material.
However, the forces exerted between the workpiece and the cutting tips go both ways: over continual use, pieces of the abrasive material are ground away by friction. In commodity abrasives, the wearing of pieces is particularly quick. Whilst higher performance abrasive grains can maintain sharpness throughout wearing.
What Makes a Good Abrasive?
High hardness is one quality shared across all abrasive materials. To effectively wear away other materials by friction, a material must be hard – in the same way that a diamond, a common abrasive, can score glass.
As a rule of thumb, the larger the difference in hardness, i.e., between the workpiece and the abrasive, the quicker the abrasive action.
Moderately hard materials, such as garnet, are used as some of the most common abrasives: whilst these are not particularly efficient, these materials are inexpensive and occur naturally. Therefore, they lend themselves to general-purpose coated applications.
Fused aluminum oxide, also known as fused alumina, is seen as the next step up in materials. Most commonly, alumina abrasives take the form of Brown Fused Alumina (BFA).
BFA is made by the fusion of naturally occurring bauxites in electric arc furnaces. BFA offers durability and high hardness, making it well suited for use with metals such as steel, bronze and iron. BFA is a popular commodity abrasive because of its high performance and versatility at a relatively low price point.
The hardness of abrasive material is not the only determining factor in its performance. Even the hardest of materials will ultimately be “smoothed” by the abrasive process as abrasives are worn over time.
Consequently, abrasives are commonly prepared as grains for bonded applications: over sustained use, smoothed, old grains are worn away, whilst new, sharper grains are revealed.
However, whilst this extends the usable life of bonded abrasives, they are still subject to inevitable wear over time. As a result, their abrasive performance will never be as good as new.
Developing Sustainable High-Performance Abrasives
The vast array of applications and the consumable nature of abrasives means that, on an industrial scale, the sustainability of abrasive materials can have a large impact.
The requirement for a sustainable high-performance abrasive grain inspired the development of Targa ceramic alumina grains from Saint-Gobain Abrasive Materials.
Targa grains are made from pure alumina, offering a vastly improved performance compared to commodity-fused alumina grains, such as BFA. Made from the seeded gel process, Targa ceramic alumina grains, otherwise known as Cerpass TGE®, were first developed in 1984 by Saint-Gobain Abrasive Materials.1
By using the seeded gel process, highly uniform alumina particles are produced with special abrasive properties.2 The process starts with a colloidal dispersion of sub-micron (<100 nm) particles of Al2O3 or other “seeding agent” compounds (such as titanates or αα-ferric oxides) in a semi-solid gel.
The addition of seeding agents to the gel produces a vast quantity of available nucleation sites to form Al2O3 crystals.3 This results in the eventual formation of small (<400 nm) Al2O3 crystals exhibiting very narrow size distribution and high uniformity.
By producing Targa grains using this method, the grains exhibit a unique abrasive characteristic thanks to their engineered friability and nanoscale structure.
Targa grains will fracture when exposed to shear stresses, thus exposing new, sharp cutting edges as required. This “micro-fracturing,” which persists at a rate that maintains productivity, means that Targa grains are in essence self-sharpening – their quality remains good-as-new even as they continue to wear away.
This mechanism of micro-fracturing is qualitatively different from that of traditionally fused-alumina ceramics, which become dull by the formation of worn flat surfaces over sustained use and also wear via larger scale macro-fracturing.
The renewal of the cutting surface of Targa alumina grains under stress is a quality known as engineered friability. This quality does not reduce the life of these abrasives; it instead surprisingly increases their life whilst offering greater material removal rates.
It has been demonstrated that seeded gel alumina oxide abrasives exhibit a greater grinding ratio compared to conventional abrasives.4 In addition to the seeded gel material itself, Targa grains feature a high aspect ratio elongated shape that serves to cut much more aggressively than does standard crushed grain. As a result, Targa grains offer a three to five times improvement in grinding speed compared to commodity grains.
In addition, for a given grinding operation, the energy required for Targa grains can be four times to five times smaller than for brown fused alumina.
Targa ceramic grains can offer dramatically reduced carbon emissions compared to commodity-fused alumina grains due to its longer life and much lower required energy to grind.
Frequently, choosing the “sustainable” option requires a trade-off in performance. Conversely, this is not the case with Targa abrasive grains. Targa grains offer a significantly longer lifetime, are considerably faster and grind with much less power compared to BFA.
By choosing a high-performance ceramic grain, manufacturers can lower their carbon footprint and waste whilst saving equipment, energy and space — the result is a more sustainable operation that requires fewer resources and generates less waste.
Saint-Gobain Abrasive Materials can support your company’s transition to more sustainable abrasive solutions.
To find out more about Targa grains and other sustainable high-performance abrasive solutions available, get in touch with a member of the Saint-Gobain team.
References
- Ceramic Grains | Abrasive Ceramics | Ceramic Abrasive. https://www.abrasivematerials.saint-gobain.com/products/cerpass-ceramic-grain
- Lindsay, R.P. (1989) The Performance of Seeded Gel Abrasives in the Laboratory and at Customer Test Sites. Aircraft Eng & Aerospace Tech. 61, 20-26
- Jackson, M.J. (2020) Recent advancements in ultraprecision abrasive machining processes. SN Appl. Sci. 2, 1172
- Eranki, J., Xiao, G., Malkin, S. (1992) Evaluating the performance of “seeded gel” grinding wheels. Journal of Materials Processing Technology. 32, 609-625.
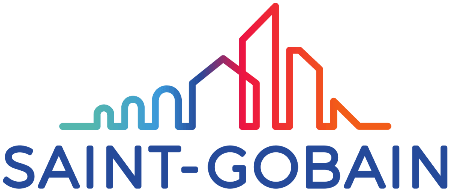
This information has been sourced, reviewed and adapted from materials provided by Saint-Gobain Specialty Grains and Powders.
For more information on this source, please visit Saint-Gobain Specialty Grains and Powders.