All of the components in a stripper chemical and stripped PR must be monitored precisely throughout the PR stripping process to minimize the likelihood of panel damage and enhance process yield through enhanced process control.
This article seeks to underline the importance of process control using efficient and precise analysis tools.
An outline of pre-existing technologies demonstrates the importance of the real-time, high-precision analysis of this process. It also highlights the relevance and advantages of ABB’s Wet Process Analyzer (WPA) as a real-time multi-stream analytical technique for optimizing the FPD PR stripping process.
A liquid crystal display panel is made of two sheets of glass that are isolated by a gap of 5 μm filled with liquid crystals. The display creates the image when an electric current is applied to the liquid crystals to manipulate the passage of light.
The technology leverages the characteristics of liquid crystals to not just maintain the same orientation in relation to each other but also change orientation upon applying a voltage value.
Developing a liquid crystal display (LCD), the most common type of flat panel display (FPD), involves a process similar to the process of manufacturing semiconductors, except that the transistors are built on a glass substrate rather than a silicon wafer.
Fabricating circuits that form the needed array on the glass substrate is one of the key steps in making a liquid crystal display panel.
This is achieved by applying a photoresist coating on the array. The assembly is first exposed and then etched. Fundamentally, it is a process of lithography. Then, it is essential to strip the photoresist (PR) film from the panel.
The PR stripping process ensures that any unwanted photoresist material layer is eliminated from the panel as fast as possible. Process control procedures should make sure that no surface material beneath the photoresist material is affected by the used stripping chemicals.
Thus, rigorous and continuous process control is crucial (see Figure 1), and the technologies should provide accurate and reliable results in real-time, without any impact on the process.
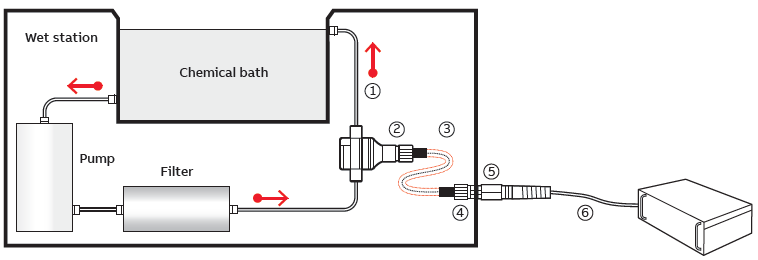
Figure 1. Bath monitoring process. Image Credit: ABB Measurement & Analytics
Bath monitoring process components in figure 1:
- The ClippIR+ is designed to be directly clipped around the recirculating line and is self-supporting. However, an optional bracket can be provided.
- 15.2 cm (5.98 in) minimum clearance around the ClippIR+
- Teflon tubing is used to protect the fiber optics: 1.5 m (4.92 ft) long
- 2.5 cm (0.98 in) access hole is necessary
- Standard bulkhead fitting
- Standard 10 to 100 m (32.80 to 328.08 ft) optical cables housed in PVC tubing
Fast and precise measurement of the concentrations of the PR stripping chemical is vital to ensure an improved process control that results in an increase in process yield by minimizing the probability of panel damage.
Moreover, the measurement results can be used to identify the endpoint of stripper bath life and allow chemical auto-spiking to increase the service life of the bath.
Background Technological Horizon
In the past, various technologies have been invented to measure the concentrations of stripping chemicals. Moreover, the composition of the stripping chemical formulations has changed substantially, thus minimizing toxicity while maintaining stripping efficiency.
Conventional analytical methods are usually invasive, generate chemical waste and necessitate process circulation tubing modifications. This can result in the contamination of the stripping solution and impact the process integrity.
Another issue here is that most technologies do not support the real-time analysis of the stripping chemical.
Four main technologies are used for this purpose: filter photometry, titration, UV-based solutions and Fourier transform near-infrared (FT-NIR) spectrometry.
The first three technologies exhibit less versatility in determining a broad range of chemical components and usually need direct interaction with the process circulation tubing and chemicals.
The fourth technology works based on the FT-NIR spectrometer and is a robust analytical tool for accurate quantitative analysis of various components. It is the best-in-class wet process analyzer (WPA) created by ABB.
The WPA avoids the need for chemical reagents, is non-destructive and renders highly repeatable analysis quicker and more reliable.
ABB’s Wet Process Analyzer (WPA): A Complete Multi-Stream Online Monitoring Solution
The WPA from ABB (see Figure 2) is a non-contact chemical measurement technology that enables real-time analysis of PR, solvent and amine concentrations from the PR stripping process. It uses the most innovative and patented ClippIR+ and near-infrared spectrometry to eliminate the risk of chemical bath contamination.
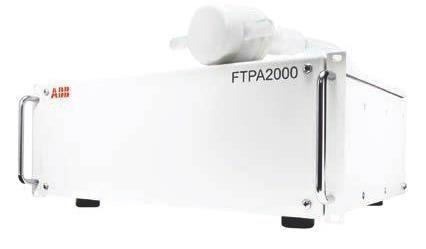
Figure 2. WPA with patented ClippIR+. Image Credit: ABB Measurement & Analytics
The patented sampling system has been engineered such that it is directly clipped onto the existing circulation tubing, which enables quick and simple installation without any process interruptions (tube modification/cutting) and avoids the need for sample extraction/conditioning.
The ClippIR+ (see Figure 3) is fully made of Teflon™, providing maximum chemical resistance. Thanks to the Teflon™ design, the ClippIR+ is safeguarded from the chemical vapors discharged from the tool.
Moreover, the WPA avoids the need for unworkable bypass lines: through the optical fiber, the infrared light is brought to the measurement point, which enables direct measurement with the help of the PFA process tubing.
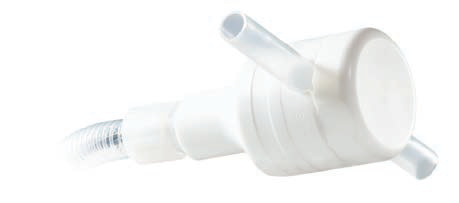
Figure 3. The patented ClippIR. Image Credit: ABB Measurement & Analytics
The absence of chemical contact (see Figure 4) or interference with the stripping system enables the measurement to be made at operational bath temperatures, which facilitates real-time process control from the sample conditioning process without any delay. Reagents or cooling units are not needed.
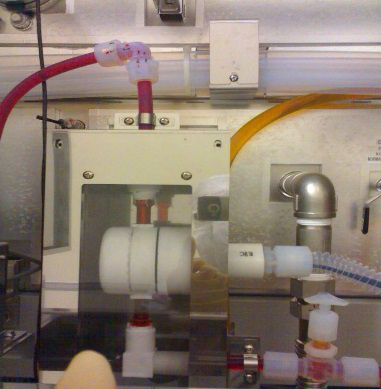
Figure 4. ABB’s ClippIR+ non-contact sampling accessory. Image Credit: ABB Measurement & Analytics
In addition, the WPA supports several FPD stripper chemical calibrations, thus offering the end user the versatility of altering calibrations to suit evolving process changes. A single WPA can be used on multiple tools to measure different applications or chemistry.
The WPA has tried and tested abilities to measure all key stripper chemicals used in the FPD industry, such as DPS-3300-XC: PR, amine, NMF, H2O; ETS-100: PR, DMAC, AEE, MMF, NMP, H2O; LGS-200-DIZ: PR, amine, H2O; N-300: PR, MEA, H2O; TOK-106: PR, MEA, DMSO, H2O.
Thanks to such a universality, the WPA can be easily adapted to virtually any FPD PR stripping process monitoring.
The trend chart shown in Figure 5 illustrates changes in the concentration of PR and amine for the PR stripping process, where continuous fresh stripper chemical dosing has been controlled by the PR concentration level.
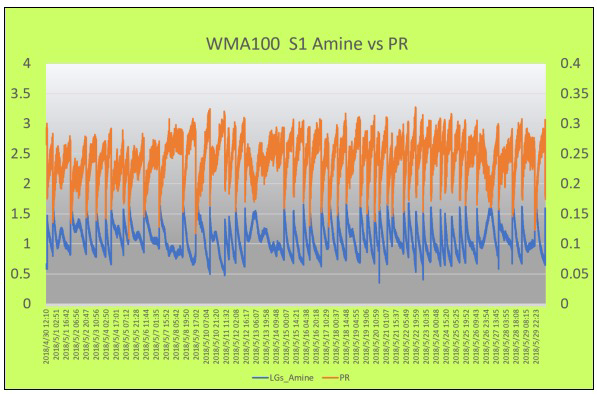
Figure 5. Table showing amine vs PR trends. The figure shows the PR stripping process trend chart. Image Credit: ABB Measurement & Analytics
Legend: Red: amine; Blue: PR; x-scale: in days; y-scales: Left (wt% for amine), Right (abs for PR).
The multi-stream analysis function of the WPA enables a single analyzer to monitor up to eight different chemical baths (see Figure 6). This is a highly economical solution than configurations with multiple analyzers in a single tool.
Users can achieve accurate end-of-bath alert and bath life extension, via chemical auto spiking, through the real-time monitoring feature with a less than 30 seconds measurement time.
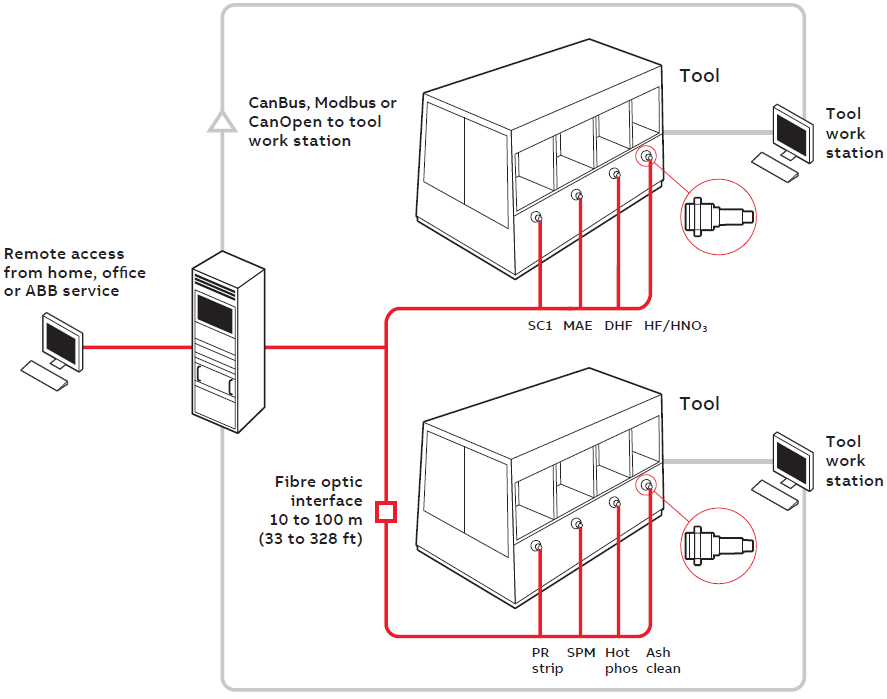
Figure 6. Only one wet process analyzer (WPA) for multiple tools and 8 baths per WPA. Image Credit: ABB Measurement & Analytics
In short, the WPA ensures savings by boosting higher bath lifetimes and minimizing chemical consumption, while ensuring accurate multi-stream chemical analysis. In addition, the installation (with the patented non-contact sampling accessory ClippIR+) does not necessitate any downtime and off-line laboratory analysis, which makes the WPA a comprehensive process control tool.
Conclusion
With flat panel displays (FPD) becoming more advanced and costly to manufacture, economical production solutions must be implemented with the most efficient and reliable technologies.
Optimal real-time process control has a key role in achieving performance landmarks and each process optimization adds to higher profit.
To achieve this, engineers depend on the most advanced analytical tools to ensure ideal quality control, which results in an optimized process yield. The PR stripping process is a crucial step in ensuring high-quality production standards in FPD manufacturing.
The implementation of the established ABB Wet Process Analyzer (WPA) system to the current stripping process tool considerably minimizes panel damage risk by ensuring an improved process control through quick and accurate monitoring of stripping chemical concentrations.
Thanks to its online multi-stream analysis capability, ABB’s WPA is the market leader for monitoring the PR stripping process in the FPD industry, with huge install bases in China, Taiwan and Korea.
The analyzer provides a quick, reliable and efficient real-time analysis solution for FPD makers. The non-invasive method enables accurate data-driven process control without the need to interact with the process itself.
ABB has a large install base in Northern Asia, where most of the FPDs are produced, and since 2003, it has been recognized as the pioneer for PR removers in display manufacturing in Asia. In simple terms, the ABB WPA is an indispensable analytical tool for any FDP manufacturer.
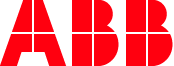
This information has been sourced, reviewed and adapted from materials provided by ABB Measurement & Analytics.
For more information on this source, please visit ABB Measurement & Analytics.