Lasers have been used to weld together plastic parts for decades, but until recently the technology had one major disadvantage: it could not be used to weld clear polymers. Recently, high-powered laser technology has allowed for the development of clear plastic welding techniques with the use of special steps or additives.
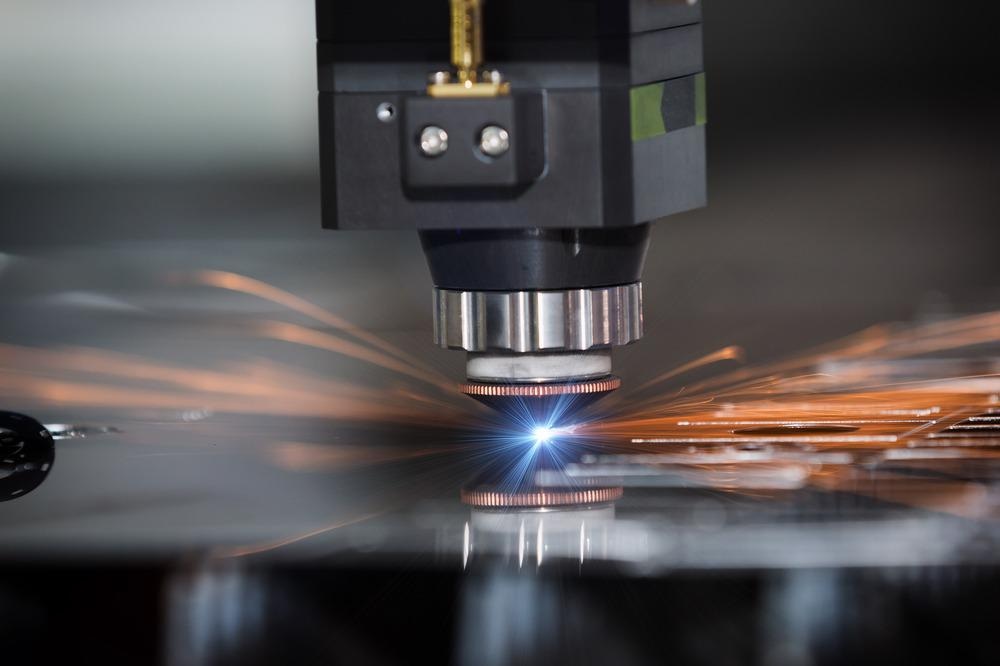
Image Credit: Aumm graphixphoto/Shutterstock.com
The creation of these techniques has resolved many problems and opened a wide range of new possibilities, particularly in the medical device and consumer goods industries. Numerous technologies and the medical device industry require transparent plastic assemblies. In the consumer goods industry, fierce competition is driving up expectations with respect to form and function, especially when it comes to consumer electronics.
If a material appears transparent to the human eye, it does not absorb much light energy in the visible part of the electromagnetic spectrum.
The light of many lasers is located in the visible part of the spectrum, rendering these lasers useless for welding clear materials, as these clear materials will not absorb the laser energy and convert it to heat.
Until very recently, the way to overcome this drawback was to use through-transmission laser welding (TTLW). This technique involves an optical laser that emits radiation in the 1μm part of the spectrum, at least 95 percent of which passes through clear polymers.
To increase the absorption of laser radiation, TTLW involves the addition of an absorbing base layer that could be placed alongside a single layer or between two layers. The technique involves using the 1μm laser to heat up the absorptive layer, causing the clear polymer layer to melt so that it could be fused with another piece of clear polymer. The additive layer could then be removed.
Further Reading: Increasing Wear Resistance with Laser Heat Treatments
The fiber lasers typically used for TTLW have a Gaussian beam, small weld spot size, and a high power density. This kind of laser beam is not ideal for the welding of polymers. Smoother power distribution is needed to be useful at the low melting temperatures of these materials.
There are a number of strategies that can overcome the limitations of a Gaussian beam. These strategies include the use of beam shaping elements or quickly scanning the laser back and forth to produce a broader weld.
While TTLW can be unwieldy, adding an extra step to the welding process, it is effective and quite popular.
Switching to a New Laser
While the energy from a 1μm laser mostly passes through visibly-clear materials, these materials will absorb a significantly larger amount of energy from lasers operating in higher wavelengths.
Thus, the development of 2μm laser technology has allowed for the welding of clear polymers without the use of an absorptive layer. At this higher wavelength, enough absorption occurs to melt a clear polymer. Approximately 70 to 85 percent of the energy from a 2μm laser will pass through a clear polymer, which means about 30 to 15 percent of the energy is absorbed without the use of an additive layer.
As any layer passes through a clear material, some energy is absorbed in each material surface. In the case of welding together two clear polymers, a 2μm laser passes through four surfaces where absorption can occur. The weld joint of two polymers has two absorptive surfaces, making a 2μm laser a useful solution for welding clear polymers.
Applications
The use of TTLW and other 1μm laser techniques is still common. However, 2μm laser welding has been a boon to certain applications and industries.
The medical device industry has been particularly receptive to the use of 2μm laser welding techniques.
These techniques can be used to weld parts for microfluidic devices, diagnostic cassettes, fluid bags, catheters, filtration devices, and medical tubing. In particular, diagnostic cassettes and microfluidics require components that are transmissive and either the visible or ultraviolet regions. Therefore, is difficult to use additional absorptive layers that are needed for 1μm laser welding.
Welding techniques that make use of 2μm lasers and also becoming popular in some areas of the consumer goods industry. Water bottles, smartphone parts, sensor enclosures, parts for wearables, hearing aids, kitchenware, and other items have been made using 2μm laser welding.
Unlike in the medical industry, 2μm laser welding in the consumer goods industry is more for aesthetic purposes and size requirements. Highly competitive markets are pushing companies that make consumer goods to raise their standards and product ranges. The ability to weld clear polymers allows companies to meet and raise standards for their customers.
Resources and Further Reading
Brown, J. 2µm Lasers: Revolutionizing Welding of Clear Plastics. Plastics Decorating. [Online] Available at: https://plasticsdecorating.com/articles/2020/2%C2%B5m-lasers-revolutionizing-welding-of-clear-plastics/
LPKF Lasers & Electronics. Transparent Laser Plastic Welding. [Online] Available at: https://www.lpkfusa.com/products/laser_plastic_welding/transparent_laser_plastic_welding/
Ruotsalainen, S. at al. Laser welding of transparent polymers by using quasi-simultaneous beam off-setting scanning technique. Physics Procedia. [Online] Available at: https://www.sciencedirect.com/science/article/pii/S187538921501528X
Disclaimer: The views expressed here are those of the author expressed in their private capacity and do not necessarily represent the views of AZoM.com Limited T/A AZoNetwork the owner and operator of this website. This disclaimer forms part of the Terms and conditions of use of this website.