Polycarbonates are a group of polymers that can be formed by heat (thermoplastic), but still contain carbonate groups in their chemical makeup. Polycarbonates are strong and tough, and some grades are completely transparent. They are easy to work, mold, and form, and so find many applications in a wide range of industries.
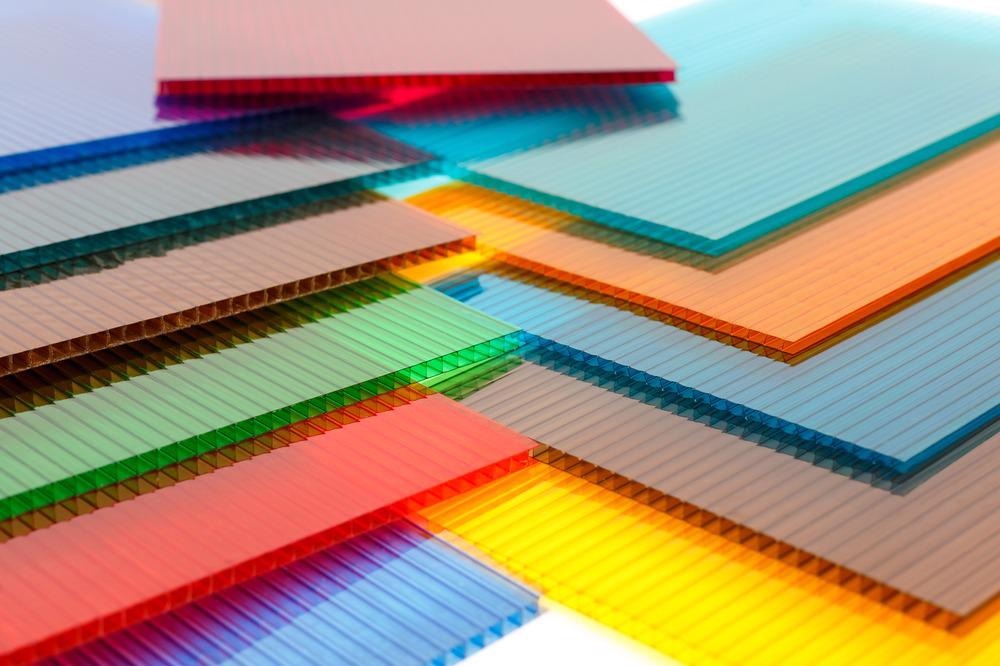
Image Credit: Usacheva Ekaterina/Shutterstock.com
Properties of Polycarbonate Materials
Polycarbonate is known for being exceptionally durable, especially when considering its lightness as well. It has high impact resistance but has low scratch-resistance unless a hard coating is applied. It is also known for being highly weather resistant. Both the impact and weather resistance found in polycarbonates are superior to comparable qualities in other kinds of polymer.
Polycarbonate is comparable to polymethyl methacrylate (PMMA, otherwise known as acrylic) in terms of material characteristics. However, it is stronger than PMMA and holds up in extreme temperatures for longer.
When thermally processed, polycarbonates are typically completely amorphous. This is what makes them exceptionally transparent to visible light, having better light transmission even than many kinds of carbonate glass. Polycarbonate can provide up to 89% light transmission, whereas standard plastics can only achieve 80%.
The glass transition temperature for polycarbonate is around 147 °C. This means that above this temperature it gradually softens. When it reaches 155 °C, polycarbonate will flow as a viscous liquid. To make products without signs of strain or stress, manufacturers have to keep polycarbonates at relatively high temperatures (above 80 °C) during processing.
It is easier to mold low molecular mass grade polycarbonates than higher grades, but this results in a material with slightly less mechanical strength. The toughest polycarbonate grades have the highest molecular mass, but they are harder to process as a result.
Once processed, polycarbonates can resist temperatures up to 120 °C. This is superior to common plastics, which can typically only withstand temperatures up to water’s boiling point (100 °C).
One novel characteristic of polycarbonate is that it is self-extinguishing. It is impossible to burn a fire based on polycarbonate fuel. Plastic, on the other hand, is flammable.
Polycarbonate Panels
After electronics, the second-largest consumer of polycarbonate materials is the construction industry. Building developers value the material for its durability and lightness, as well as for aesthetic features like its transparency or the unique look of plastic-like materials in buildings.
In construction, polycarbonate panels are used for dome lights, glazing including curved glazing, roofing sheets, and soundproofing layers.
There are three main types of polycarbonate panels (or sheets) that are used in the construction industry today. These are solid or textured polycarbonate sheets, multiwall polycarbonate sheets, and corrugated polycarbonate sheets.
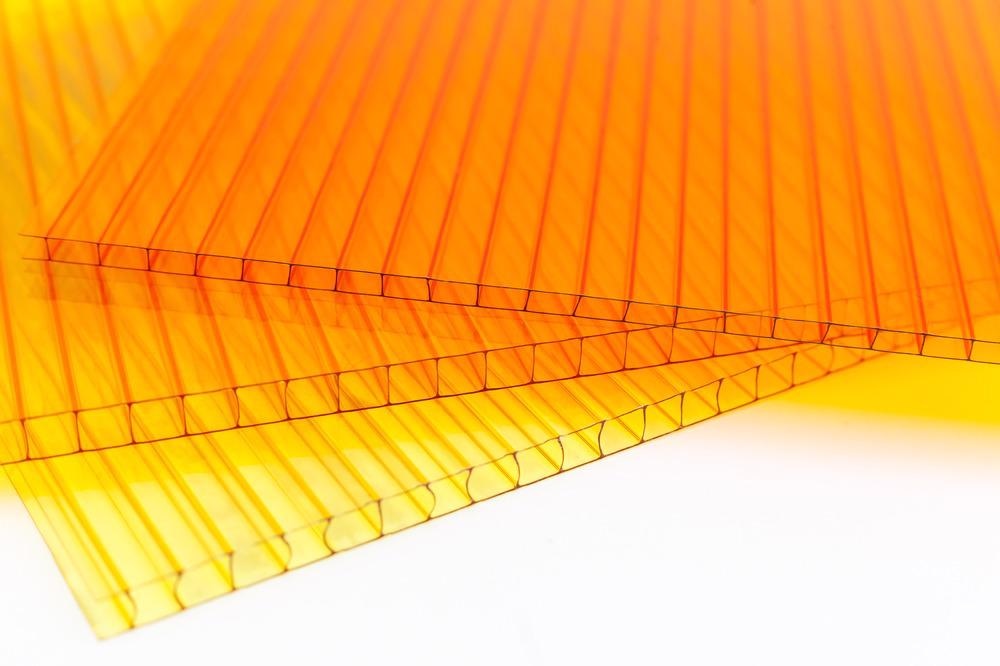
Image Credit: Usacheva Ekaterina/Shutterstock.com
Solid and textured polycarbonate sheets are designed to withstand extreme weather, be it heavy rain, strong UV radiation, or low temperatures. These panels have high impact strength and durability but are also flexible. They transmit light and have some thermal and chemical resistance.
Solid and textured sheets can be cut and drilled easily and are simple to store, handle, and install. This makes them popular with construction firms and architects alike.
Multiwall sheets are prized for their flexibility, heat reflection, and light transmission. While they can also withstand extreme weather, multiwall sheets are often used for interiors. They are also flame resistant, making them a good safety precaution for building designers.
Corrugated sheets perform better than other kinds of polycarbonate panels in terms of impact resistance. They are used for commercial, industrial, and residential settings. Corrugated sheets can be produced to precise specifications and are especially well suited for daylight harvesting in large industrial buildings and offices. They are made from a two-wall structure.
More Applications for Polycarbonate Materials
Although polycarbonates were first discovered in 1898 by German scientist Alfred Einhorn, no commercial applications for the materials were developed until 1953. Since then, manufacturing giants Bayer and General Electric have spearheaded efforts to develop the material and expand its list of applications.
Now, polycarbonates are used in a wide variety of sectors.
In the automotive industry, polycarbonate material is injection molded to create smooth surfaces for sputter deposition or evaporation deposition, important steps in the processing of aluminum.
Polycarbonate is the material used for bullet-proof “glass,” both in security vehicles and the windows and barriers for tellers in banks and other security-focused commercial settings. To make polycarbonate bullet proof, it is laminated over a number of layers.
Theft-proof packaging for small items – the plastic boxes that some electronics are sold in, for example – is typically made from polycarbonate. The material is also used for most eye protection, either safety goggles in laboratories or visors for construction and machinery workers.
The main use of polycarbonates, however, is still in manufacturing electronic components. It is a good electrical insulator and resists heat and flames. This makes the material well suited for use in electrical and telecommunications hardware.
References and Further Reading
Abts, G., T. Eckel, and R. Wehrmann (2014). Polycarbonates. Ullmann's Encyclopedia of Industrial Chemistry. Available at: https://doi.org/10.1002/14356007.a21_207.pub2.
Polycarbonate Sheets Vs. Plastic. Tuflite.
Disclaimer: The views expressed here are those of the author expressed in their private capacity and do not necessarily represent the views of AZoM.com Limited T/A AZoNetwork the owner and operator of this website. This disclaimer forms part of the Terms and conditions of use of this website.