The Murano™ heating stage is a compact stage that has been designed to be employed alongside electron backscatter diffraction (EBSD). This instrument facilitates high-resolution, in-situ observation of dynamic changes within a sample.
This article outlines an experiment conducted using the Nordlys detector from Oxford Instruments.
Context
Automotive industries are continuing to develop materials that are lightweight while offering high strength and increased ductility.
Advanced high-strength steels (AHSS) represent a promising group of materials that offers low-cost, high-volume production of ultra-high-strength sheet steel. This sheet steel is unparalleled when compared with other engineering materials.
One notable developmental limitation of AHSS is its relatively high yield strength. This is the result of the precipitation of nano-sized carbides or carbon nitride (V, Nb and Ti), which occurs as part of the austenite to ferrite transformation – a phenomenon that causes the AHSS to offer only modest formability.
It is possible to refine these precipitates via the addition of Mo, although characterization of the resulting transformation kinetics is complete. In the experiment presented here, the Murano heating stage was utilized to support an improved understanding of Mo’s role throughout the steel forming process.
Materials and Methods
Two samples of low-carbon V-bearing steel were acquired from Tata Steel. One of these samples featured 0.2 wt.% Mo addition and one did not.
Both of the steel samples were heat-treated before being transferred to a Murano hot stage mounted inside a Zeiss Gemini FEG-SEM.
The heating rate was set to 100 °C per minute to reach a target temperature of 925 °C. Once the target temperature had been achieved, the austenitic grain growth was confirmed using the Oxford Instruments EBSD Nordlys system.
The Murano stage was able to maintain a stable target temperature of 925 °C, and a series of high-resolution EBSD maps were collected for the two samples following holding times of 600 seconds, 1800 seconds and 4200 seconds.
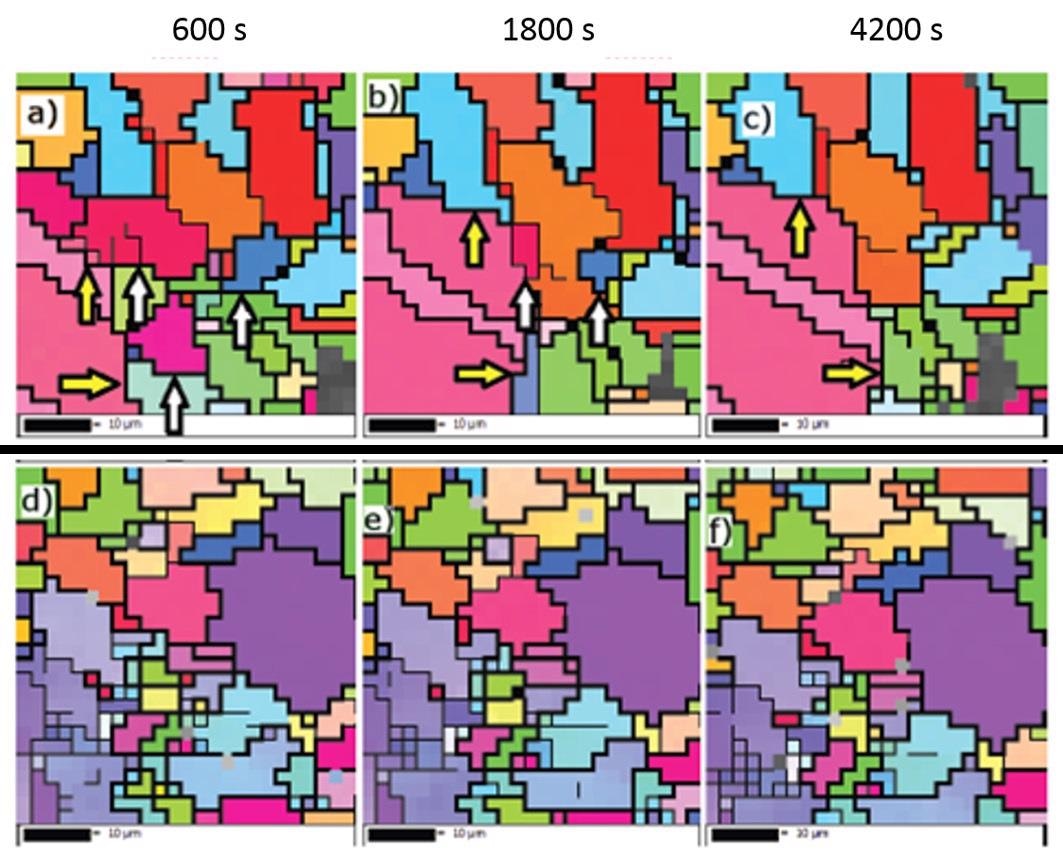
Figure 1. Maps a – c show the steel sample without Mo, maps d – f show steel with added Mo. White arrows in maps show grains that were at later stages of treatment consumed by a progressing high angle boundaries of large neighbouring grain that is growing selectively (yellow arrow). No such events were observed in the sample that included Mo. Image Credit: Gatan, Inc.
Summary
The experiment presented here demonstrated the benefits of in-situ characterization via hot-stage EBSD. Using this method, it was possible to directly evaluate the role of Mo in austenitic grain growth and its impact on the kinetics of austenite to ferrite transformation.
It was determined that the addition of 0.2 wt.% Mo to V-bearing low carbon steel could limit austenitic grain growth, affording additional insight into how the presence of Mo improves AHSS.
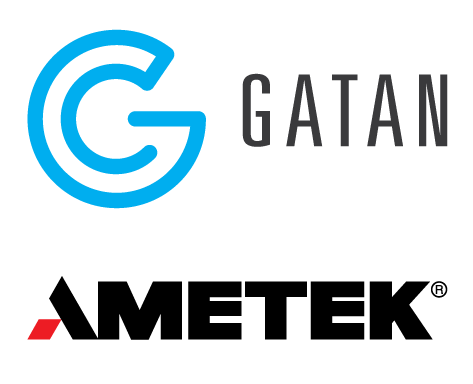
This information has been sourced, reviewed and adapted from materials provided by Gatan Inc.
For more information on this source, please visit Gatan Inc.