Could you tell our readers about RETSCH, Verder Scientific, and your role at the company?
RETSCH is a member company of Verder Scientific, which has over 1,000 employees in 22 locations around the globe.
Verder Scientific is setting new benchmarks in terms of high-tech R&D and quality control solutions tailored for analytical laboratories, cutting-edge manufacturing companies and research institutions
Its product offerings range from heat treatment, hardness testing and elemental analysis to sample preparation and particle characterization. Verder Scientific’s group of companies delivers major benefits to clients’ processes, sustainability, outcomes and ultimately profitability.
Could you give a brief overview of RETSCH’s range of jaw crushers and talk about how these tools support the production of cathode and anode materials?
RETSCH offers a broad selection of tools for different steps of anode and cathode production.
Jaw crushers are utilized for the initial size reduction of brittle materials. RETSCH supplies eight different types of jaw crushers, and each one accepts different feed sizes and delivers different results in terms of final fineness.
All models of jaw crushers have a superior throughput and give a superior degree of size reduction relative to their intent and size. Each model also provides good quality final fineness.
Two RETSCH models, the BB 50 and the BB 500, are capable of providing particles that are under one millimeter in diameter, which is excellent for any jaw crusher.
When considering the final sizes of crushed materials, we frequently mention the D90 value, which implies that 90% of the crushed particles will be smaller than the given value.
The RETSCH range of jaw crushers possesses a zero-point adjustment for wear compensation. Each has breaking jaws comprising different materials to guarantee a neutral analysis workaround, ensuring that the crushed particles are not contaminated with iron or heavy metals utilized in steel-breaking jaws.
An array of accessories are available, for example, the no-rebound feed hopper for safe operation. Every one of RETSCH's solutions is built for easy access and easy cleaning of the crushing chamber.
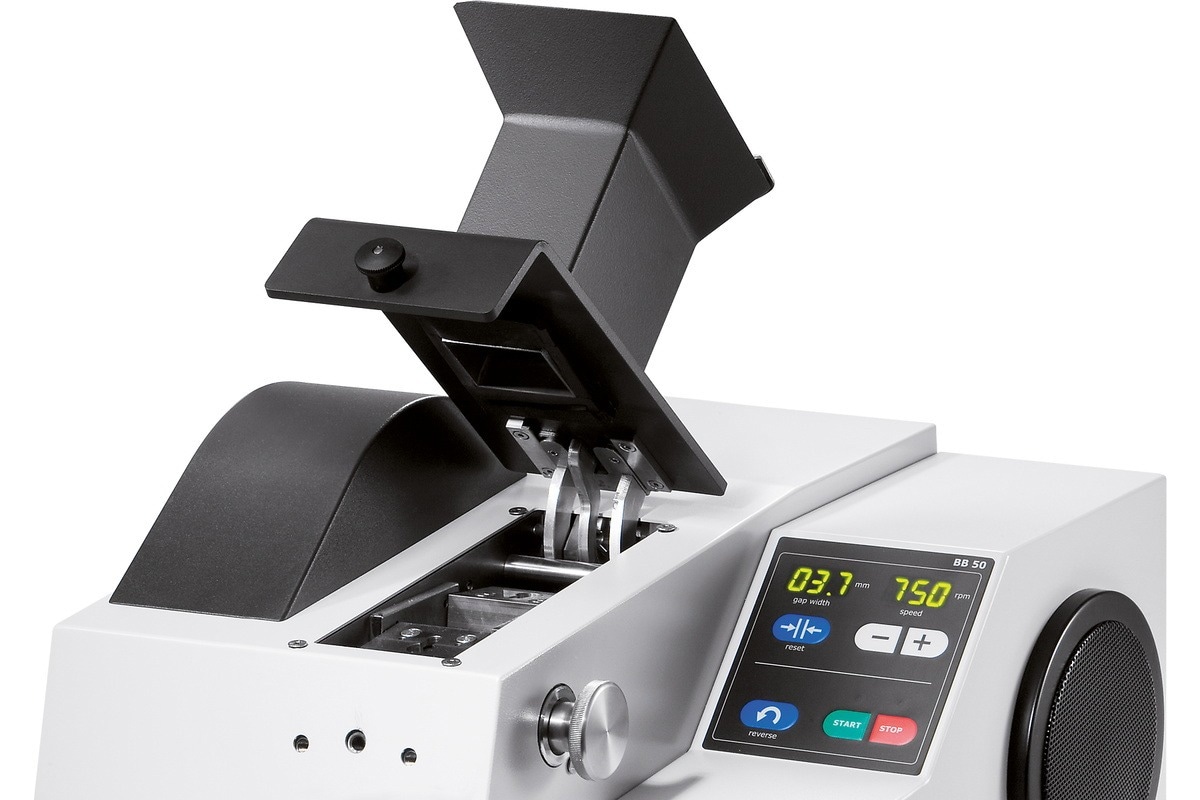
Image Credit: RETSCH
After the material has been crushed, what instruments are best suited for further milling?
The RETSCH Ultra Centrifugal Mill ZM 200 is particularly suited for milling cathode materials, facilitating the batch-wise preparation of amounts up to around 10 kg. These parameters vary depending on the sample and how dense the milling material is, but this model can give a high final fineness of 40 microns.
One feature that is critical in the battery sector is the usage of iron-free wear-resistant coated sieves and rotors. These are perfect when preparing abrasive sample materials with high metal content, where it is essential to preserve sample purity.
To support process optimization, this model lets operators vary the speed to between 6000 and 18000 rpm. RETSCH also offers an optional cyclone attachment for superior sample discharge, giving operators the ability to mill up to 4.5 liters of sample material in a single batch.
The DR 100 vibratory feeding system enhances easy feeding, and the push-fit rotors and accessories allow for easy assembly, disassembly and cleaning.
The larger SR 300 Rotor Beater Mill model can mill roughly 40 kg of sample materials in a single batch, though it still provides a high achievable final fineness of 50 microns.
It also possesses variable speed options for process optimization and allows for an optional cyclone and the adding of the DR 100 vibratory feeding system.
The SR 300 model can tolerate feed sizes up to 25 millimeters and is able to accommodate batch sizes up to 26 liters.
Fine grinding processes in battery manufacturing usually require the deployment of ball mills. RETSCH offers a wide selection of planetary ball and traditional ball mills that are a good fit when milling anode and cathode materials requiring the greatest degree of sample homogeneity and final fineness.
These mills are utilized in research and development.
With their high degree of adaptability in terms of different jar materials, ball size, amount of balls used, variable speeds and different jar sizes, the operator has a broad selection of possibilities to discover the optimal process for their individual requirements.
The PM 400 can be utilized in small-scale production, has four grinding stations, and can be utilized to grind a maximum of 500 milliliters of sample material. The mills can additionally be applied to more specialist processes, such as working in a specific atmosphere to prevent contact with oxygen.
The Emax high-energy ball mill came to the market in 2015 and has been well accepted in the battery research sector since then. It allows quicker and finer grinding than any other ball mill presently on offer, giving a speed of 2000 rpm for ultra-fast sample pulverization.

Image Credit: RETSCH
The core of the Emax, and crucial to its milling speed, is its water-cooling option. This option lets the mill work without the frequent cooldown breaks that are typically necessary for planetary ball mills.
The Emax allows operators to run a temperature-controlled grinding program, which is especially valuable when working with temperature-sensitive materials.
This program allows operators to specify a lower and upper temperature, meaning the grinding process continues until the upper limit is achieved and will pause until the sample has cooled down to the lower temperature.
The Emax possesses narrow particle size distribution due to its special oval-shaped jar design, which enhances sample mixing and guarantees narrower particle sizes.
The jars also include an integrated safety closure to make certain they remain safely screwed shut during transport. Once removed from the machine, the jars can be allowed to cool in either a water bath or in air.
The jar is pressurized up to a minimum of five bars and can be utilized with a wide array of materials, for example, tungsten carbide or zirconium oxide, to facilitate contamination-free grinding.
What instrumentation is available for dividing samples?
The PT Range of sample dividers are perfect for taking sub-samples, as sub-samples are an important stage in producing reliable results. These confirm the representativeness of a sample and, subsequently, the reproducibility of the analysis.
Sample dividers also allow for easier cleaning of the instrument while assisting avoidance of sample contamination. A range of different models are offered, and the largest can be utilized on material batches up to 60 liters.
The utilization of a random sampling approach can cause segregation between finer particles and larger particles, for example, only selecting the finer or larger particles that could possess identical composition.
RETSCH also offers a range of laboratory sieve shakers that are ideal for sieving cathode materials. Sieve shakers can be employed in accurate and reproducible particle size determination or a sieve cut, where only one sieve is used.
These stages facilitate further quality assurance for finished products and valuable raw materials.
The jet model and control models can be wholly calibrated and recalibrated, guaranteeing the highest degree of quality. The 3D throwing motion of the jet technology allows for the highest degree of separation.
What type of applications are these instruments suitable for? Are there any representative examples?
One example of an application is the milling of graphite or carbon materials, for example, carbon nanofibers, carbon black, active carbon or spherical graphite powder. These materials can be tricky, especially spherical graphite, which weakens and smears away from the ball milling process.
A trial milling of 60 grams of active carbon was ground using standard accessories in the ZM 200 from an initial particle size of 5 millimeters to 250 microns in 1 minute.
A similar trial involving the larger SR 300 resulted in a 450 gram sample being ground to a fineness of 300 microns. The ZM 200 struggles to accommodate particle sizes up to ten millimeters.
The SR 300 would be more appropriate, but to reach a final fineness of, for example, 4 microns, it would be vital to use the planetary ball mill system, or possibly the PM 100 with zirconium oxide balls and jars.
In this trial, it would be feasible to attain the target grinding size of 4 microns in about 20 minutes.
Some applications require a two-step grinding process. Firstly, larger - 10 millimeter - grinding balls should be used at the pre-grinding stage at a moderate speed (1200 rpm) for five minutes.
Secondly, the balls and the pre-ground sample should be separated. Smaller grinding balls – for example, 0.5 millimeter balls – should be inserted for a wet grinding process.
Grinding with 0.5 millimeter balls for 60 minutes after the pre-grinding step should result in a fine powder material with a particle size smaller than 400 nanometers.
When working on graphite or carbon, it may be feasible to utilize jaw crushers like the PB 250 for larger sample material. Working on more specialist material - like graphite foil - may necessitate a cutting mill rather than a jaw crusher.
The SM 300 cutting mill can essentially reduce the foil down to 4 millimeters in size, and it has the potential to merge the pre-cutting and ball milling processes to provide 10-micron samples of used graphite electrodes.
The ZM 200 may be suitable for this application also, or possibly the CryoMill, where the process involves working with a temperature-sensitive material. The CryoMill lets the operator actively cool the sample down with liquid nitrogen and can produce 500-micron particles.
A broad selection of application examples are offered for lithium drill cores or different salts. It may be suitable to utilize planetary ball mills, jaw crushers or the ZM 200 with various accessories.
What advice would you offer potential users working with specific materials?
Lithium silicate has a tendency to cake on grinding balls and jars, so it is advisable to add a few drops of methanol to the jar. This is not wet grinding – only a few droplets are needed to avoid the caking effect and get a smooth powdered sample.
Silicon or polysilicon grinding tends to result in larger lumps. Jaw crushers can be utilized with tungsten carbide jars and wearing plates to avoid iron contamination.
Different gap sizes can be set to achieve different degrees of fineness. Planetary ball mills can be utilized to achieve the fine pulverization of these materials.
The Emax and PM 100 can be utilized with silicon, while it is feasible to utilize a higher energy input with the Emax.
In this instance, the same configuration, jars sizes, sample, and balls can be utilized with each instrument; however, the Emax would produce 3x finer particles over an identical milling time due to the higher energy input.
Setting the temperature control mode at a point between 70 °C and 85 °C will make certain the temperature stays at levels that are favorable for this sample. Breaking jaws of NiHard4 offer a good alternative for grinding silicon.
How does the MM 500 Control further optimize the milling process?
The MM 500 Control device is a unique and very novel machine. It can be utilized for wet, dry and cryogenic grinding, with a frequency of up to 30 Hertz.
It operates in a similar way to the Emax, with the screw lock grinding jars capable of accommodating up to 125 milliliters of sample.
The crucial difference between the MM 500 and the Emax is that the MM 500 includes thermal plates. Grinding jars are installed above the thermal plates, which support the transfer of heating liquids or cooling liquids to the jars. This makes it possible to operate within a temperature range of -100 °C to 100 °C.
It is also feasible to utilize a cryotank to reach incredibly cold temperatures. A thermostat, chiller and even tap water can be utilized to modify the temperature by heating or cooling this further.
If operators choose to work cryogenically via the application of a liquid nitrogen tank, they can utilize the optional cryoPad. This makes it simple to sustain a specific cold temperature at the thermal plates; -100 °C to 0 °C - in steps of 10 °C.
This system incorporates a touch display for straightforward operation and storage of cycle programs and Standard Operating Procedures (SOPs).
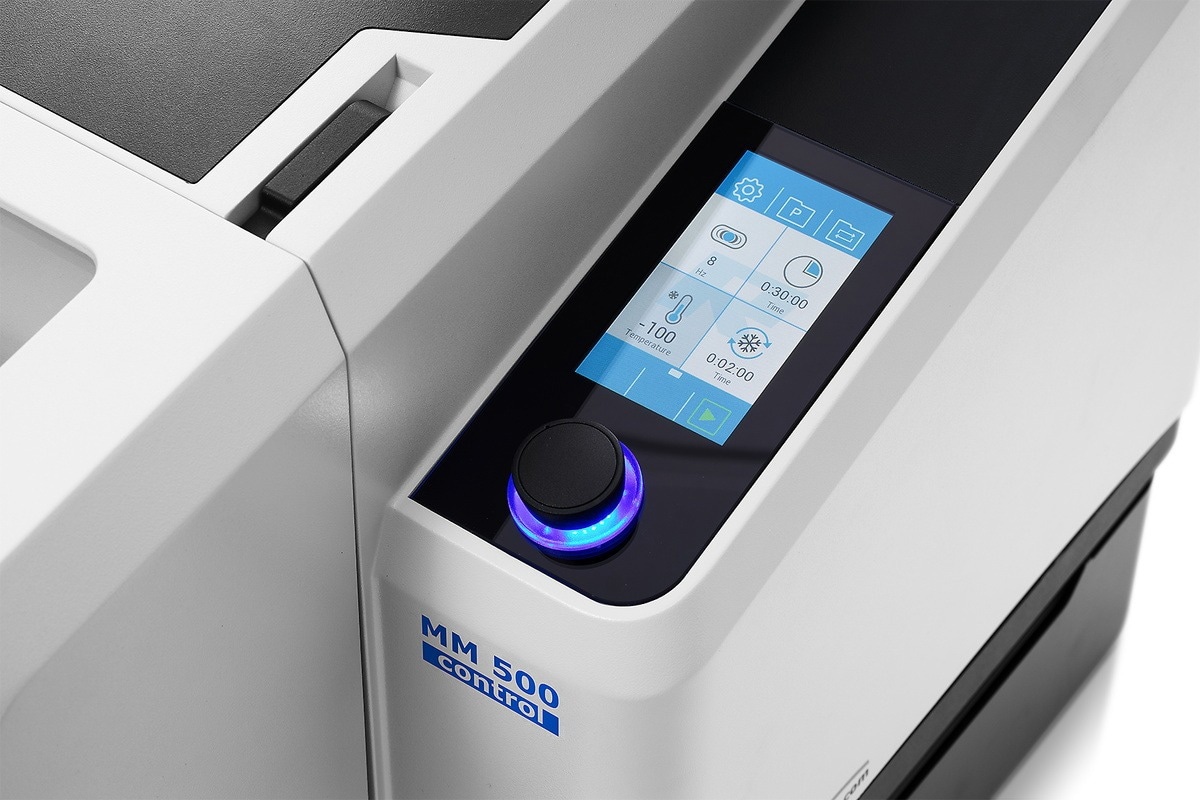
Image Credit: RETSCH
The machine needs time to cool the thermal plates down, for example, 50 minutes from 20 °C down to -100 degrees.
Operators can opt for a specific or fixed sample cooling time until the sample inside has cooled to the desired temperature. This temperature will reach a steady state where no grinding or process takes place.
Once grinding has begun, the energy input will have a warming effect, which contradicts the cooling process. The continuing temperature will be dependent on how the operator sets the cooling options and their parameters for the milling process.
This degree of flexibility gives operators the freedom to work with the machine at a range of temperatures, even during the comparatively brief times that mixing mills tend to be utilized for.
The MM 500 also has the capacity for wet grinding processes. A chiller can be utilized to keep samples at 4 °C, facilitating accurate nanometer-scale grinding, where the temperature is continuously kept under 20 °C due to the use of the chiller.
This is an outstanding feature for any operator working on temperature-sensitive samples.
About Dr. Tanja Butt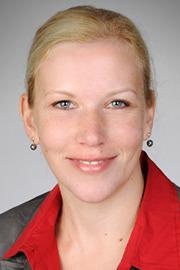
Dr. Tanja Butt studied Biology at the University of Duesseldorf, Germany, and graduated with a Diploma in Biology. After that she earned her PhD in biotechnology at the Forschungszentrum Juelich, Germany. Later, she worked in R&D and project management for different institutions. She joined Retsch in 2013 as Product Manager for the whole milling and sieving product range.

This information has been sourced, reviewed and adapted from materials provided by CARBOLITE GERO Ltd.
For more information on this source, please visit CARBOLITE GERO Ltd.
Disclaimer: The views expressed here are those of the interviewee and do not necessarily represent the views of AZoM.com Limited (T/A) AZoNetwork, the owner and operator of this website. This disclaimer forms part of the Terms and Conditions of use of this website.