QPAC® Polyalkylene carbonates, especially QPAC® 40 Polypropylene carbonate, are used extensively as a binder to form parts from nitride-based ceramics such as Aluminum Nitride (AlN), Boron Nitride (BN), and Silicon Nitride (SiN). The parts are formed by either tape casting or pressing.
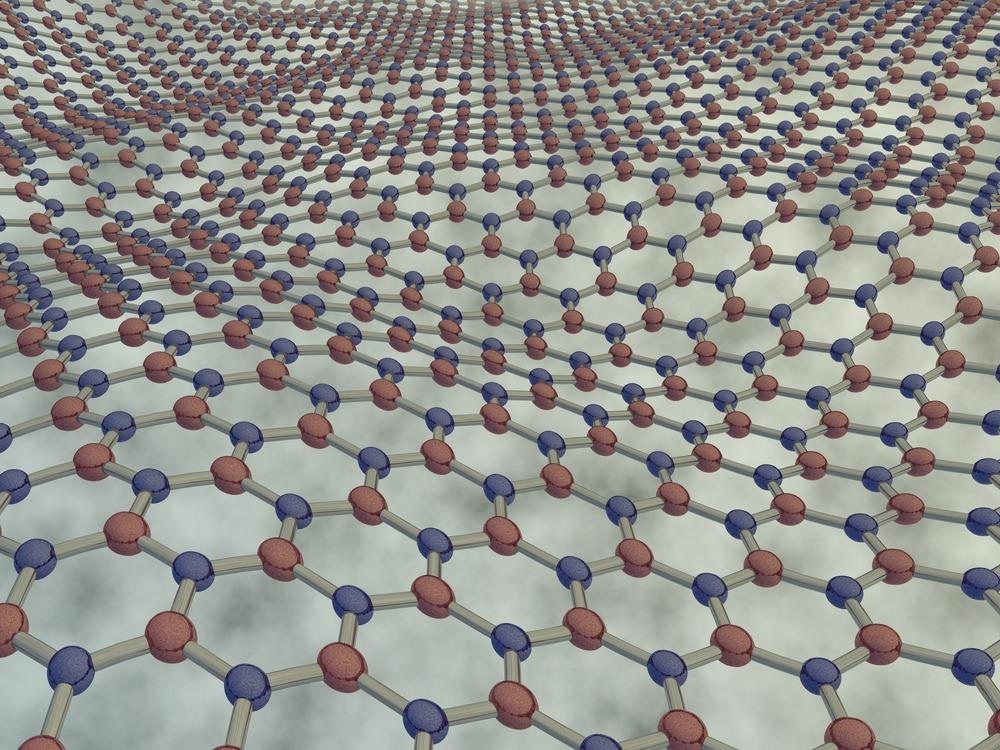
Flexible sheet of hexagonal Boron Nitride
Image Credit: ShutterStock/ogwen
AlN has both excellent electrical insulation and high thermal conductivity properties. It is finding growing usage in heat sink applications to dissipate heat generated by high power electronics. Another property advantage of AlN in high power electronic applications is that it's electrical insulation and thermal expansion properties are similar to silicon. BN has similar properties but is not used as extensively.
SiN offers good hardness at low densities due to its porosity. Its properties offer good hardness at very high temperatures, high wear resistance, good creep resistance, oxidation resistance, and high mechanical strength.
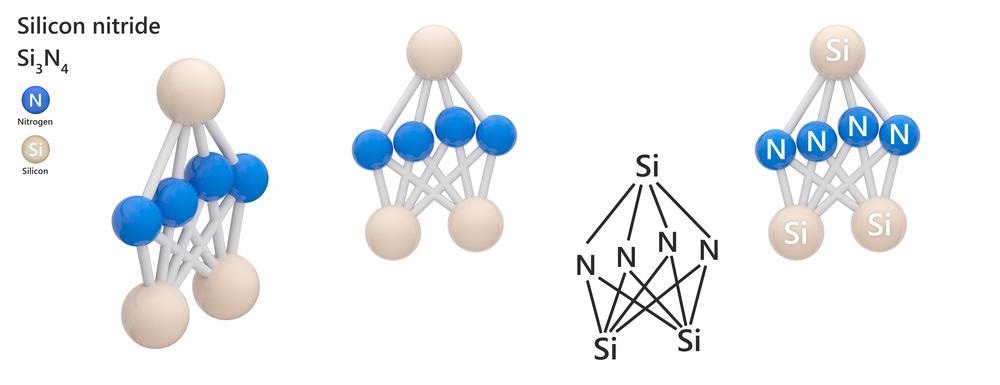
Image Credit: ShutterStock/Orange Deer Studio
As mentioned, QPAC® is an excellent binder choice for fabricating these ceramics into parts. The QPAC® Polyalkylene carbonate binder system permits a clean burnout at low temperatures in N2 atmospheres. This atmosphere is required to provide the materials from undergoing oxidation. QPAC is the only binder that will fully decompose at a low temperature under these non-oxidizing environments (including vacuum and Argon). The mechanism of decomposition is also gentle resulting in a stronger stress-free final part. This is especially important for thicker parts. Compared with other binders such as polyvinyl butyral binders, the residual carbon, and other contaminants are significantly lower after the decomposition process. Extensive analysis of parts prepared using QPAC as the binder consistently shows no detectable residual carbon. The absence of carbon results in stronger mechanical properties and enhanced electrical and thermal properties.
Tape prepared using QPAC as the binder maintains their surface dimensions and is flexible so that they can be easily handled and fabricated. This is owed to its lower glass transition temperature (below room temperature). Another unique characteristic of the QPAC® is its ability to be plasticized by its own monomer, propylene carbonate. As a result, QPAC® 40 Polyproylene carbonate has excellent film-forming capabilities for the tape casting process.
The ability to decompose completely with no residuals at low temperatures in inert environments makes QPAC® an excellent choice for use with AlN, BN, and SiN ceramics. These applications continue to grow as the materials experience further acceptance into the power electronics market and other advanced ceramic markets.
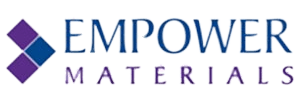
This information has been sourced, reviewed and adapted from materials provided by Empower Materials.
For more information on this source, please visit Empower Materials