This article analyzes the thermal welding process of semicrystalline polymers and discusses the superiority of polyether ether ketone (PEEK) over other commonly used semicrystalline thermoplastic polymers.
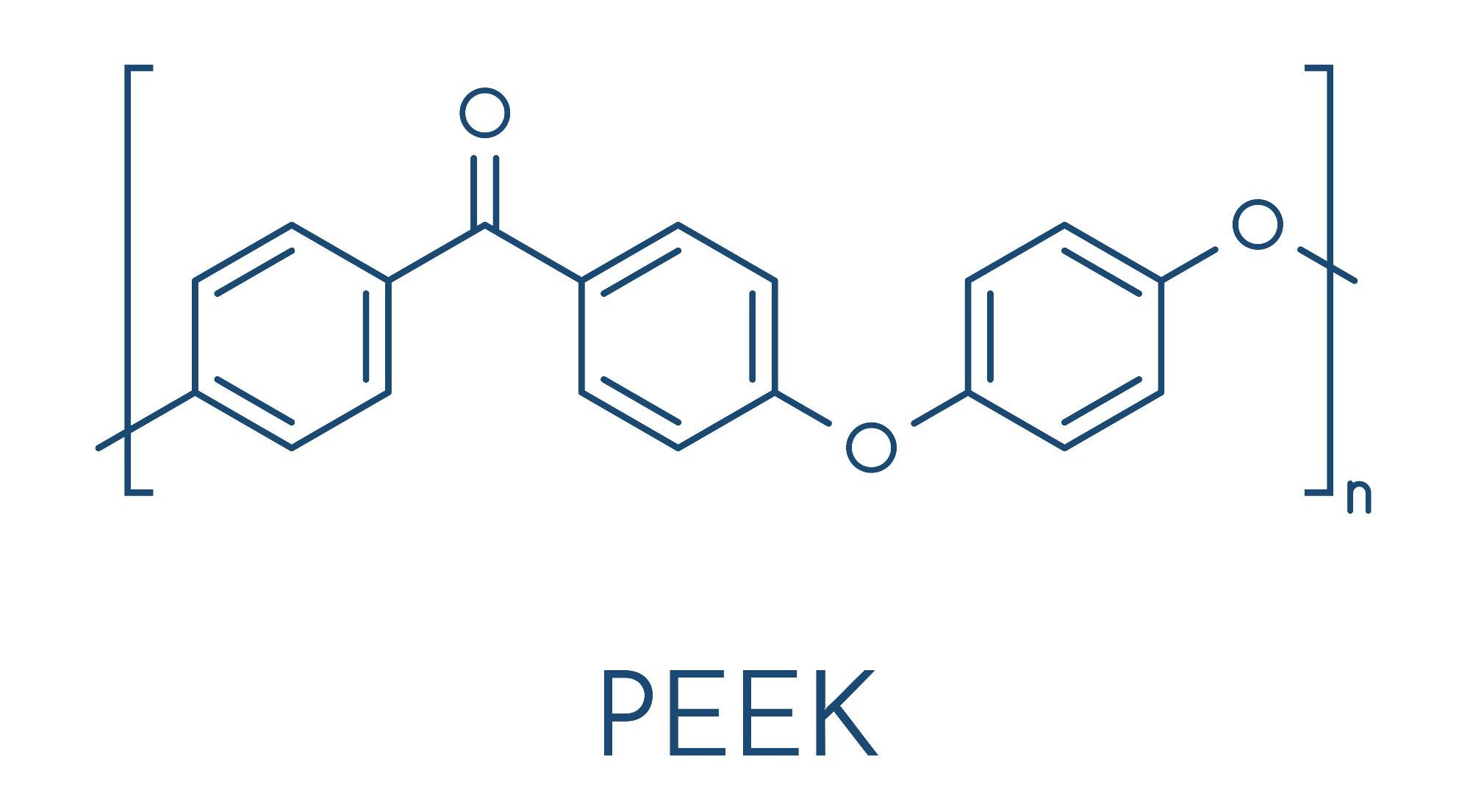
Image Credit: StudioMolekuul/Shutterstock.com
Background
Plastics are long chains of specific polymers. The use of plastics has grown significantly owing to their high strength, high stiffness, high formability, and lightweight. Additionally, the most commonly used plastics are thermal and electrical insulators. However, polymers are replacing metals and ceramics in modern electronic devices owing to their flexibility, compactness, and high volume-to-weight ratio. Some of the polymers also have demonstrated electro-responsive properties, which makes them suitable for sensors and actuators.
As the uses of polymers are growing, the demand for improving their repairability is also growing. This is more crucial when most of the plastic wastes are non-biodegradable and harm the environment when directly released into it, or release hazardous gases when incinerated.
Thermal Welding of Polymers
Currently, thermal welding of polymers is the most popular and cost-effective method to repair polymer-based components or design complex parts. Some of the known thermal welding techniques for polymers are hot plate welding, hot bar welding, hot gas welding, impulse welding, extrusion welding, flash-free welding, vibration welding, spin welding, orbital welding, ultrasonic welding, friction stir welding, resistive implant welding, induction welding, high-frequency welding, infrared welding, microwave welding, and laser welding.
The most notable thing is that only thermoplastic polymers can be thermally welded, whereas thermosetting polymers can only be joined by adhesives. For strong welding, the welded interface should have higher strength compared to that of the bulk polymer. Polymers are usually either in amorphous or semicrystalline form. Most of the studies on thermal welding have been done on amorphous polymers; however, the understanding of welding of semicrystalline polymers is obscure.
In the case of amorphous polymers, the interfacial strength of the weld directly depends upon the chain entanglement. Moreover, it increases by one by the fourth power of total welding time (i.e. tw1/4) until the density at the interface becomes equal to that of the melt. Similarly, fracture toughness and shear stress at the interfaces are directly proportional to tw1/4.
More from AZoM: Producing Polymer Composites with High Thermal Conductivity
Meanwhile, the effect of process parameters on the crystallization of semicrystalline polymers at the interface requires proper modeling. Three processes that drive thermal welding are heat diffusion, mass diffusion, and crystallization.
Modeling with PEEK
PEEK is a semicrystalline thermoplastic polymer with a melting point of 345 ℃ and high glass transition temperature of 143 ℃, which are much higher than most commonly used semicrystalline thermoplastic polymers viz. polyethylene (PE), polypropylene (PP), polybutylene terephthalate (PBT), and polyethylene terephthalate (PET) with melting points of ~110 ℃, ~160 ℃, ~223 ℃, ~255 ℃, respectively.
Its high melting temperature facilitates better control over melt and weld interface thicknesses. Moreover, it has excellent chemical and mechanical stability at high temperatures, which makes it a suitable candidate for the thermal welding model.
Latest Research
In a study conducted by Adhikari et al. (2022), infrared radiation with a source temperature of 850 ℃ was used to melt and weld two surfaces of PEEK polymer. They found that the thermal diffusivity was 1.13 × 10−7 m2/s. Moreover, the molecular weight of polymer and temperature had a significant effect on polymer chain diffusion at the interface. The isothermal crystallization rate of 5 s-1 gave a characteristic crystallization time of 1.77 s.
During the cooling process, no crystallinity was developed for the first 2.5s even after crossing the melting temperature. This indicated that the mass diffusion continued even after the melting point, and the time window between melting point and crystallization is crucial for the strength of the weld interface. However, with the increase in crystallization, mass diffusion began to slow. Due to crystallization, both surfaces interlocked with each other with high strength compared to amorphous polymers.
Furthermore, down from the interface, the interpenetration width was directly dependent upon the far-field temperature and the depth of the interpenetration was independent of the width of the melted region above a threshold value. Thus, careful consideration of the dimensions of the polymer samples is very important. In this regard, polymers like PEEK facilitate better control of interpenetration depth and width over PE, PP, PBT, and PET.
Conclusions
In summary, analysis of thermal welding of semicrystalline polymers is essential for a better understanding of process parameters that affect the polymer chain diffusion and crystallinity-based interlocking, which are the major contributing factors to the strength of weld interface. Any semicrystalline thermoplastic polymer having a longer time window between the melting point and initiation of crystallization exhibits higher mass diffusion and higher strength.
References and Further Reading
Adhikari, S., Durning, C., Fish, J., Simon, J., Kumar, S., Modeling Thermal Welding of Semicrystalline Polymers, Macromolecules, 2022 https://doi.org/10.1021/acs.macromol.1c02612
Welding technologies for polymers and composites. (n.d.). TWI. https://www.twi-global.com/technical-knowledge/published-papers/welding-technologies-for-polymers-and-composites
Disclaimer: The views expressed here are those of the author expressed in their private capacity and do not necessarily represent the views of AZoM.com Limited T/A AZoNetwork the owner and operator of this website. This disclaimer forms part of the Terms and conditions of use of this website.