Separator film is a critical component within a lithium-ion battery and ensuring a consistent thickness and homogenous distribution of the pores is key to optimizing battery performance and safety.
This interview with Chuck Blanchette, Field Marketing Manager for Thermo Fisher Scientific, discusses the reasons why uniform separator film is essential in lithium-ion batteries.
The interview outlines the characteristics and role of separator film, looking at both the dry and wet manufacturing processes that are used in the production of separator film.
It also looks at how automatic control can be used to increase and maintain film uniformity, as well as exploring the different sensor technology options available for measuring separator film thickness.
What is the significance of separator film, and where do these sit in terms of overall battery construction?
Separator film is a membrane placed between the anode and cathode in a battery to facilitate the flow of charged ions from one electrode to the other while preventing short circuits.
It is also used as a safety net. If there is a short circuit within the battery and the battery heats up, the separator film will melt, closing the tiny pores, stopping the transfer of ions, and avoiding thermal runaway.
Separator film used in a lithium-ion battery is a thin, porous membrane typically made out of polymers like polyethylene (PE) or polypropylene (PP). It is produced in both monolayer and multilayer versions, with PP components used more as a structural component, while PE components are typically used as the safety component.
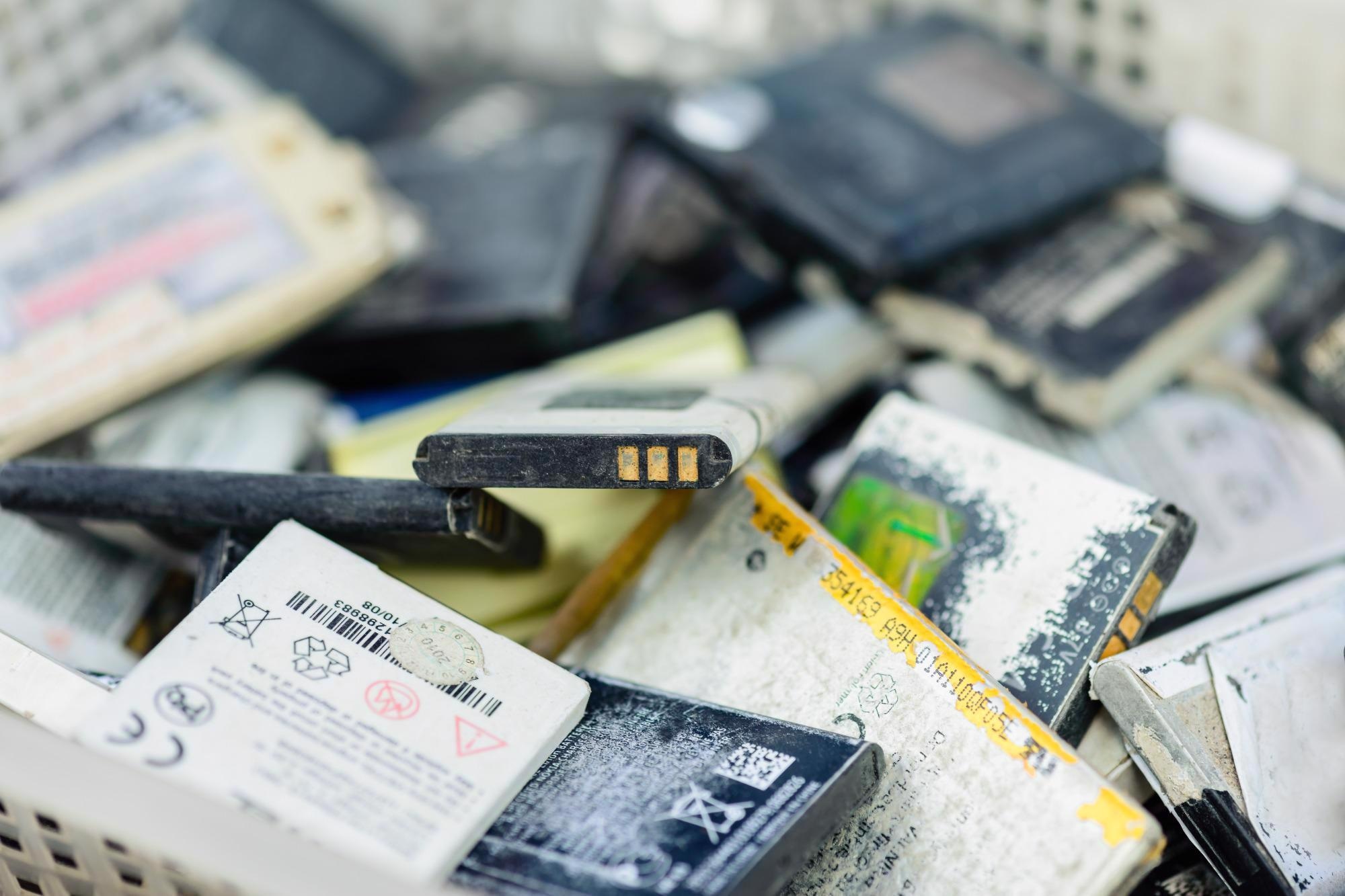
Image Credit:Shutterstock/vietnamstockphotos
Why is it important to ensure the separator films maintain uniform thickness?
Maintaining a uniform thickness is important since this ensures uniform porosity in the separator film, which in turn promotes homogenous ion distribution.
Non-uniformity or defects in the separator film can also cause both performance and safety problems with the battery. Performance problems such as voltage instability, self-discharging, or rapid capacity decay could occur, while safety issues in the battery such as internal short circuiting, hot spots, or thermal runaway are also possible.
Non-uniform separator films can cause excess lithium-ions to accumulate in different areas on the anode surface, leading to uneven absorption into the anode with excess ions not absorbed and accumulating on the surface during the charging cycle.
This causes lithium dendrites, which are sharp metallic lithium-ion deposits on the anode surface. These dendrites can penetrate the separator and cause internal short circuits. Uniform separator films can help to suppress the growth of dendrites and prevent dendrite related defects.
What is the typical manufacturing process for separator films?
Separator films can be manufactured using a dry or wet process.
The dry process for manufacturing lithium-ion separator film supports the creation of high-powered batteries, as it creates an open and more uniform pore structure in the separator film. However, this only works with high crystallinity polymers.
In the dry process, the polymer is extruded out of a flat-die extruder where it is annealed, which is a heating and cooling process. This improves the crystallinity of the polymer itself. It is then stretched in both the machine direction and the cross-machine direction, and this process creates the micro-pores needed to transfer ions.
Once the film has been extruded onto a casting roll, it is typically measured by a thickness gauge - either a beta gauge, an x-ray gauge, or possibly, an infrared gauge. It is then also measured at the final film location before being wound up.
In contrast, the wet process creates stronger mechanical properties for a longer life cycle but a lower pore density. The wet process sees the polymer mixed with a paraffin oil in the extruder before being extruded and stretched.
It is then submerged into a bath of solvent to extract the paraffin oil, creating the micro-pores. The process is very similar, but there is also a measurement made after the film is stretched for the first time (transverse direction orientation) and before the oil extraction at the wet film location. This measurement is done so that the oil content can be quantified as well.
What role does automatic control play in this process?
Automatic control is used to control the die adjustment bolts during the extrusion process. These die bolts control the opening of the gap at each die bolt location across the die itself. This is a closed loop control, which makes the thickness measurement, adjusts the die to increase uniformity and then repeats the cycle.
The measurement data is segmented into zones that represent each die bolt and is used as feedback. Flatness errors for each die bolt zone are determined, and these dictate the change in the power level for each die bolt actuator. In order to create a final flat film, a target frown shape is made at the cast section and the material is stretched in both directions.
Automatic control is achieved in three stages. The first stage maps the position of each die bolt, from the die to where it is measured at the cast film measurement location.
Next, the die bolt regions are mapped from the cast film to where it actually ends up, at the finished film measurement. This is necessary due to the nonlinearity experienced in the transverse direction oven (TDO). The third step is to determine the thickness errors and feed them back to the automatic control at the extrusion die.
The step for mapping accurately from the die to the cast scanner is relatively easy because the mapping is linear, and it is not stretched from these two points. There may be some shrinkage, but the shrinkage is linear in most of the profile. There is some non-linear shrinkage on the edges, but these can be handled by entering a model into a compensation table.
Once you have the information that determines where the die bolts are at the first measurement point, you can determine how much weight - and how much material - is attributed to each die bolt.
Using this information, you can develop a mass map of the die bolt regions. This map can be applied to the measurement at the film, and by doing so, you can determine where the boundary points are for the die bolts as they pass through the oven and end up at the final film.
A table of thickness errors is derived from the film die bolt map, which is then used to create an ideal cast shape target for the control loop. The automatic control system will run to create this cast shape profile.
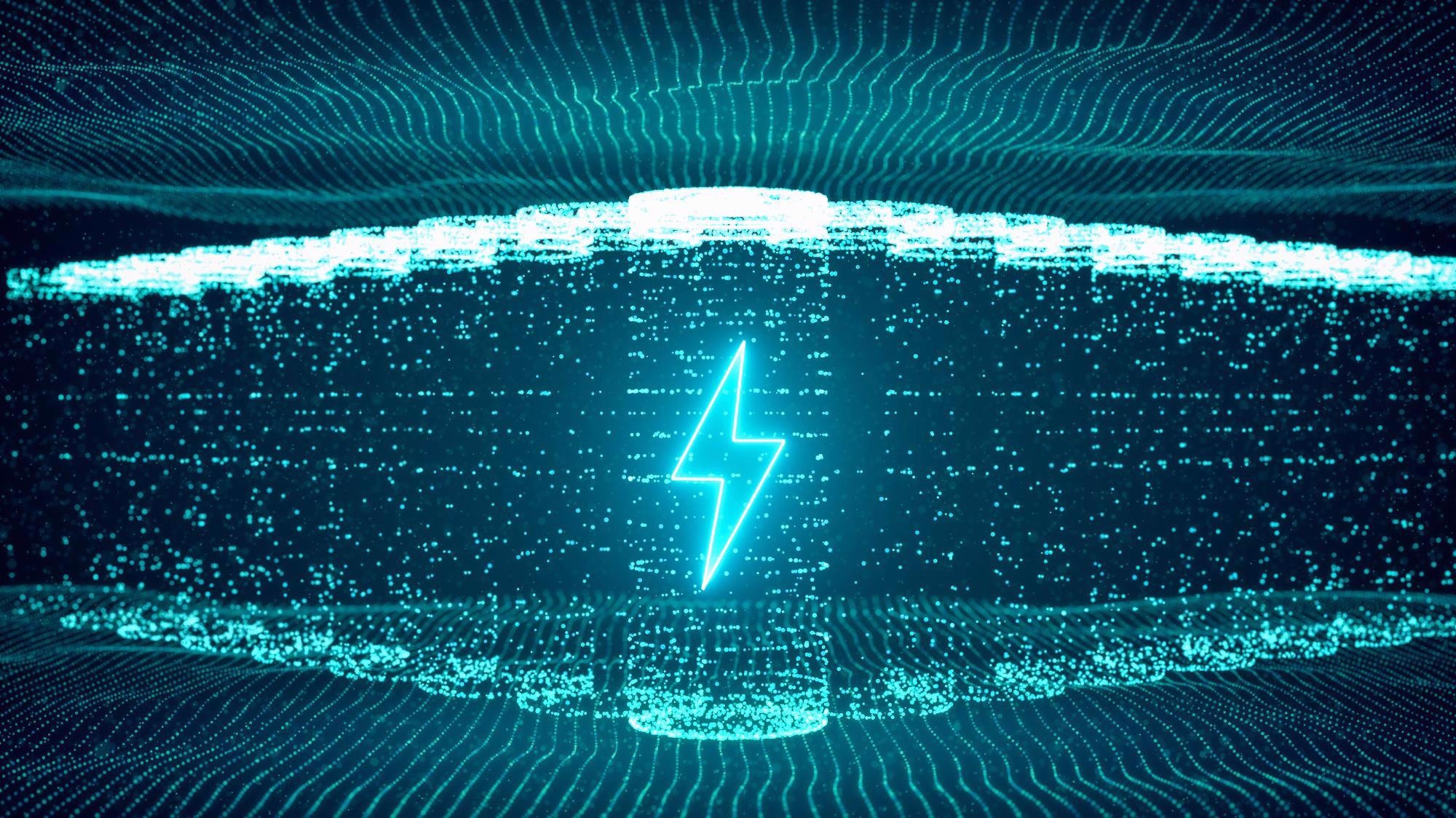
Image Credit:Shutterstock/Black_Kira
What sort of sensor technologies can be used for measuring the thickness of separator films?
There are three different types of sensors used to measure the thickness of separator film. The first is a beta isotope sensor, the second is an x-ray sensor, and the third is a full-spectrum, infrared sensor.
Beta and X-ray sensors measure basis weight ( mass ), while a full-spectrum infrared sensor can be trained to measure either weight or thickness.
The advantage of using a beta sensor is that the source lasts more than ten years and that it measures mass directly, and it is not as sensitive to different composition, for example, different coatings as an x-ray sensor.
The advantage of using an x-ray sensor is that it has the smallest measurement footprint of the three technologies, while a full-spectrum infrared sensor can provide a multi-layer measurement, depending on the coating used, and it does not need any type of special licensing.
Is it possible to measure the thicknesses of individual layers in multi-layer coatings?
For some multi-layer products, including some types of coatings, full spectrum infrared sensors can measure the individual weight and thickness of the layers, provided they operate in the near infrared region of light.
Depending on the material being measured, IR absorption can look different at different wavelengths, so it is possible to see where the two materials differ because different points in the spectra will change at different thicknesses.
These absprbance differences along the entire NIR wavelength range can be used to quantify changes in the material thickness or other properties, because the full-spectrum infrared sensor can measure the entire spectrum at one time. It looks for subtle amplitude changes at all wavelengths to determine the thickness changes.
During calibration, a matrix of samples will be measured, varying one component while keeping the other component stable. This will teach the sensor to determine which wavelengths react proportionally to the sample thickness changes.
The sensor looks at each individual wavelength . In certain wavelengths, signal changes proportionally, and in other wavelengths, it changes randomly.
The full spectrum infrared thickness gauge uses this correlation information to determine how much weighting to apply to each wavelength while calulating the thick ess during the in-line measurement .
If a wavelength scores low in correlation, it is largely ignored, while high scoring wavelengths are weighed heavily in the calculation. This allows a full-spectrum infrared sensor to determine which material is changing when it sees a material spectral change in a multilayer product.
About Chuck Blanchette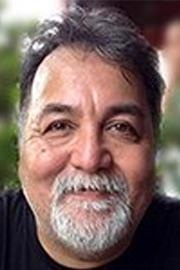
Chuck Blanchette is the Field Marketing Manager for the Flat Sheet Gauging Business, Web Applications and is responsible for the external support of the product portfolio and training worldwide. He has worked for Thermo Fisher Scientific for over 30 years in various development engineering, product management and marketing positions and has a wealth of experience in gauging, web applications, manufacturing processes and instrument and sensor design.
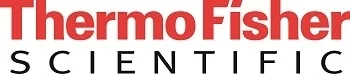
This information has been sourced, reviewed and adapted from materials provided by Thermo Fisher Scientific – Solutions for Industrial and Safety Applications.
For more information on this source, please visit Thermo Fisher Scientific – Solutions for Industrial and Safety Applications.
Disclaimer: The views expressed here are those of the interviewee and do not necessarily represent the views of AZoM.com Limited (T/A) AZoNetwork, the owner and operator of this website. This disclaimer forms part of the Terms and Conditions of use of this website.