The advent of widely available cloud computing and Industry 4.0 has opened up new possibilities in remote monitoring and measurement systems that are ideally suited to lithium-ion battery production.
This interview with Chris Burnett, Senior Field Marketing Manager for Gauging at Thermo Fisher Scientific, and his colleague Jim Frye looks at this exciting and emerging area.
They begin by looking at the role of inline metrology solutions in the production process and their benefits in ensuring battery quality and the safety of the final battery cell.
Having looked at these processes, they then outline the benefits and capabilities of remote monitoring systems, providing insight into their current architecture and capabilities and how these are set to develop in the future.
Could you start by providing a brief overview of the overall battery manufacturing chain?
Manufacturing quality batteries essentially begins with extracting raw materials out of the ground, then field testing the materials for purity and concentration levels. This allows for chemists to carry out research to determine the exact battery composition that is most ideal for your application.
This involves looking at raw material processing, inspecting the bulk material and the ores themselves. Quality control issues on that raw material must be addressed before beginning production of the electrode materials and the manufacturing of the battery cell itself. This also involves quality assurance personnel and an in-depth testing program.
Contributing to the growing popularity of batteries is their role in protecting the environment from carbon emissions via electric vehicles over traditional fossil fuel based vehicles. Additionally, recycling spent batteries is also very important in order to ensure that batteries genuinely contribute to the green energy revolution.
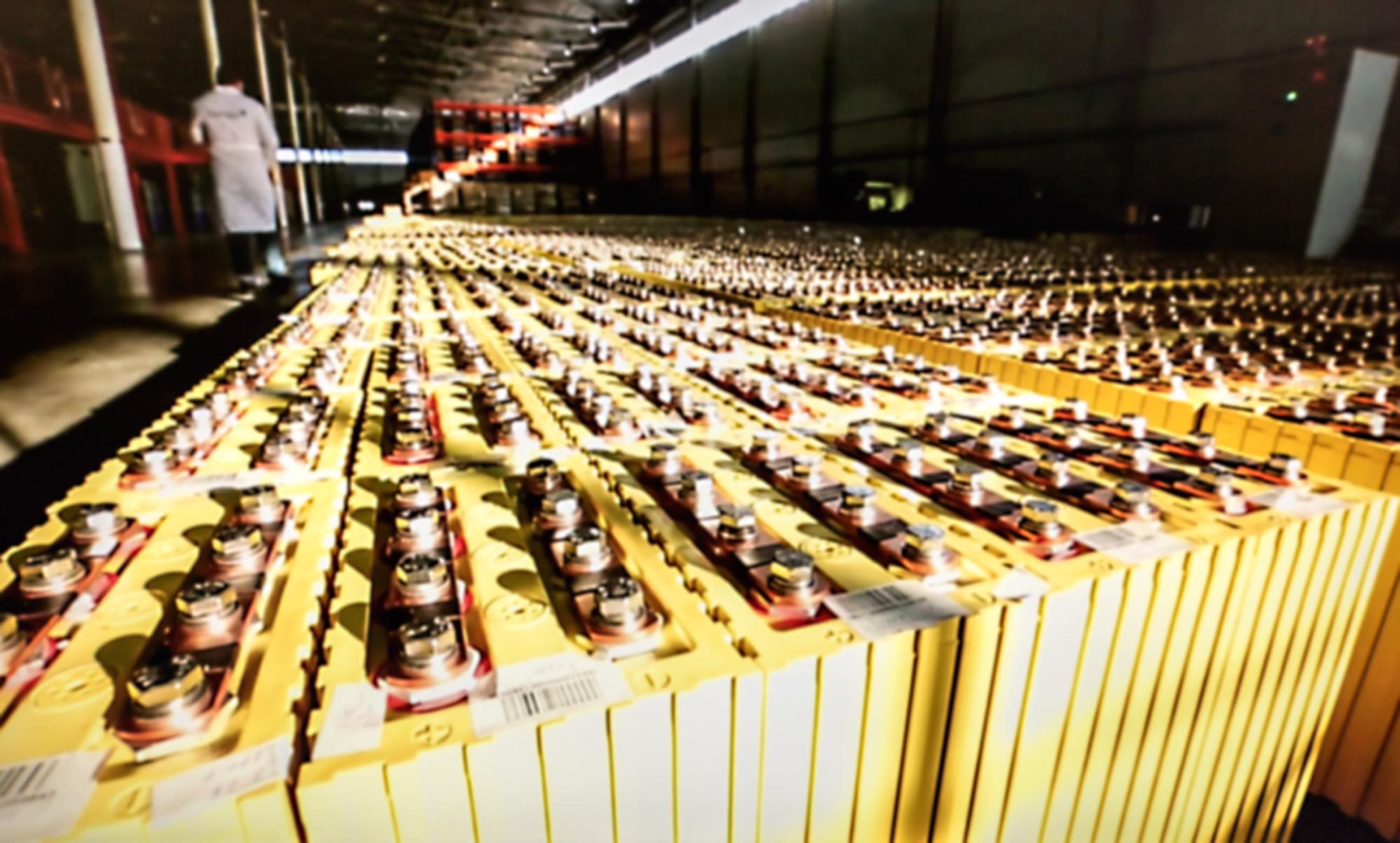
Image Credit:Shutterstock/Fishman64
Where do process control and inline inspection fit into this wider manufacturing chain?
Process control and inline inspection can provide significant benefits to coating lines themselves. Once the battery design is complete, and the materials are in place, it is critical that this production process has inline metrology capabilities to ensure that you are producing material that meets the design specification of the final battery.
The production process may feature multiple frames throughout that measure the base material, the wet coating and the dry coating. Once this is done, they will often flip the material over and measure the wet and dry coating on the bottom side.
This intelligent multi-frame system is going to be collecting a tremendous amount of data that is used for controlling the process. Due to this, you want to make sure that the instruments themselves offer optimum performance and that these are working to the right performance schedule for preventative maintenance, etc.
Online metrology must be flexible enough to accommodate different battery designs while reliably being able to make accurate measurements as long the battery line is working.
The separator film is the safety net of a lithium-ion battery. It is the material between the anode and the cathode. The separator film allows ions to pass through, but in the case of overheating, it can melt and stop that flow to protect the battery from thermal runaway.
In this particular process, we see three frames at three measurement locations in the process. These are first at the cast sheet, second at the point where the oil impregnated film has the oil extracted to create the desired porosity, and then finally, as the sheet is stretched and goes through the TDO steps.
This ensures uniform film thickness across the entire battery. We certainly do not want a thinner area that might puncture and cause a short or a failure in the battery itself, so metrology is also an important part of this process.
The calendaring line is much simpler from a schematic standpoint. This is where the physical dimensions of the battery are compressed down to meet the cell design itself. If you have a hundred layers of material in your battery, and it is one micron thicker than is ideal, that starts to add up, and the battery may not fit in its final application.
The measurement technique here is typically a confocal laser type technology, which has an accuracy of less than half a micron in terms of determining the thickness of the battery and its patch or stripe.
This technique measures a focused spot along the strip as it goes back and forth along the material. It is important to ensure that the control software ignores the gaps in between the patches and can pass along that measurement information to the calendaring equipment in order to maintain good control.
What are the advantages of using remote monitoring for these types of control processes?
Throughout these processes, you are collecting a lot of data. What you need from an operator standpoint is a quick visual representation of what is going on so that you can quickly make a decision.
For example, if the process is out of tolerance and you want to make it lighter or heavier, you can look at a map and make some real-time decisions. These HMIs also provide information regarding the instrument’s health.
Remote monitoring of this type of information provides tremendous benefits.
The first notable benefit of remote instrument performance management and data collection was that we could more easily monitor the health of the equipment and the health of the process. The health of the instrument that measures your product is what allows you to maintain the levels of quality that your customers demand.
We found that when this instrument is online, providing real-time data, we are able to allow our service engineers and our customers’ plant maintenance personnel to identify problems before they happen or as they happen.
In the past, they would have to wait for high volumes of bad product to be created, addressing issues from a reactive posture as opposed to a proactive or predictive posture.
This is important in decreasing the mean time to repair. We do not have to receive a phone call and send a service engineer to the site to be able to observe data from the system – with remote diagnostics, we can observe that data in real-time.
This also increases the mean time to breakdown failure because we can start to prevent that by collecting data to train AI models that will hopefully help us predict major instrument or part failure before it happens, allowing us to proactively replace those components.
So those two features of remote diagnostics will serve to increase productivity because we are making sure that your measurement equipment is up and running with minimum downtime.
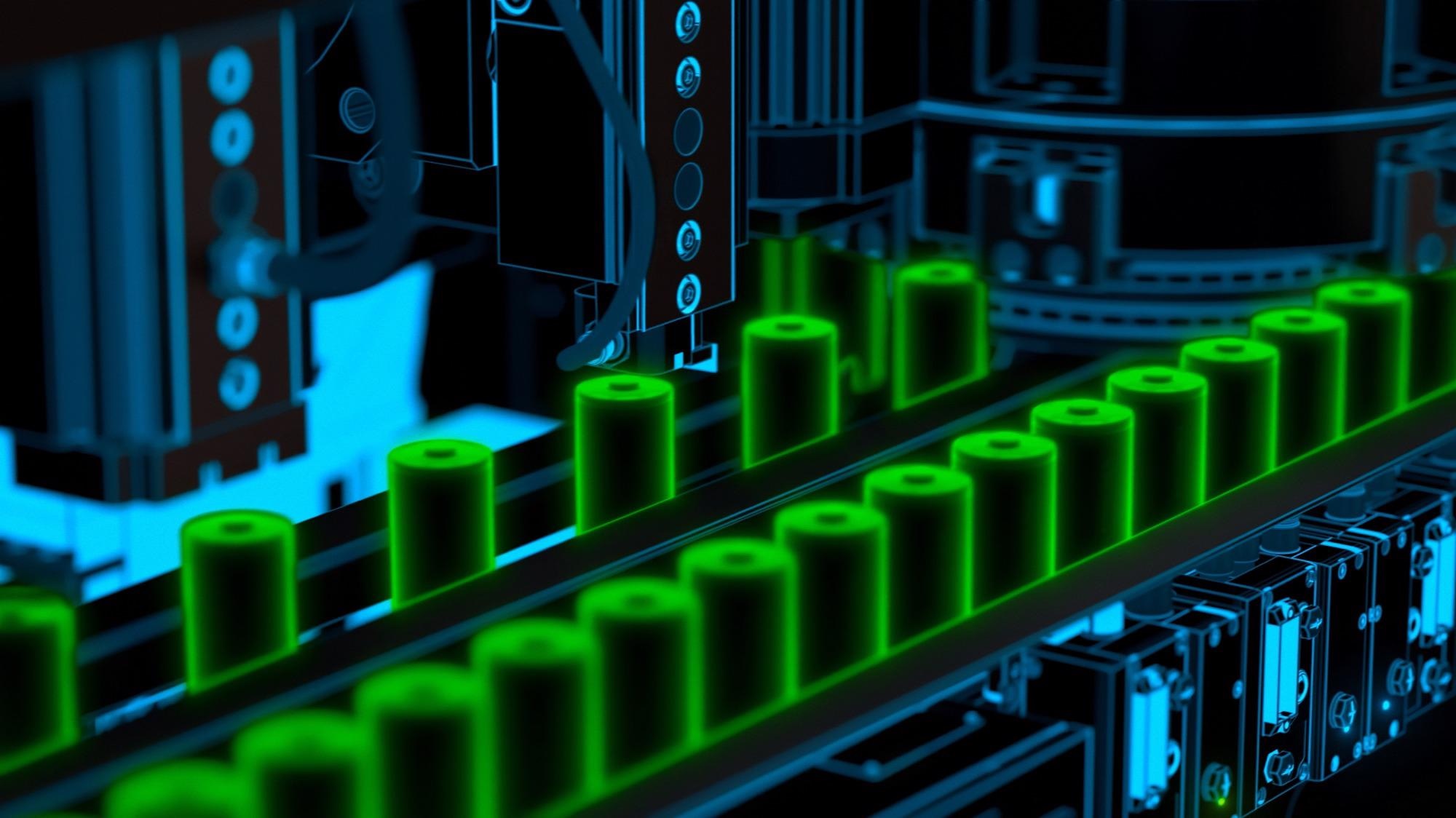
Image Credit:Shutterstock/u3d
What roles do cloud computing and 24/7 connectivity play in these processes?
The push towards Industry 4.0 is resulting in a lot of data being collected. We know that maintaining that data onsite is becoming more and more impractical, so the cloud is being leveraged to make it easier for that huge amount of data to be stored and analyzed and to allow things that are happening on the line to inform decisions from a technical standpoint.
Using the cloud, we are going to be able to look at those measurements, store them and use the Industrial Internet of Things to integrate those measurements into models that will tell us what is going to happen in the future. That is going to be increasingly important as we move forward in creating this 4.0 paradigm.
We have been focused on gathering data for tech services, field service and customer maintenance personas. We use these ‘personas’ to establish a set of annotated data that we can use to train models in the future.
To do this, frames are connected to an industrial edge device that uploads data to the cloud to be stored for future training.
The data is currently focused on those concerns because we think that is the quickest, most optimal way for our customers to derive benefits from the system. It saves service trips and ensures the right parts are sent before the service engineer arrives on site.
There are lots of efficiency benefits that we can gain from focusing on the service needs first. After the service needs, the focus will be on production data, guaranteeing quality, and having certificates of inspection so that we know that the product is good and what our machine was measuring was good. This will assure manufacturers that their batteries are safe and they are not going to cause issues for their customers.
We can achieve this with an industrial edge server by bridging the gap between the internet and the production network.
How is data security and integrity maintained when connecting production networks to the cloud?
Typically, there is a DMZ that defines a safety layer or buffer between production systems and the cloud.
That bridging of the insecure and secure layer is one way that we maintain security, and another way is by allowing only outbound data from the system. As the system is collecting data, it is only pushing this to the cloud. There are no inbound requirements for data coming to the system.
As we strive for safety and security, we make sure that that data is encrypted in transit, so it is not possible to intercept this in a readable fashion, and there is no possibility for outside parties to interfere with the internal production network.
In addition to security, many of our customers are concerned with bad actors tampering with the data. We aim to make sure that we have a reliable stream of data so that when things fail, we have the ability to buffer the data on that edge device.
The edge device features software called Kepware that reaches from the OPC server and converts data to an MQTT message which is buffered. That buffering to static or non-NVRAMs or a hard drive maintains a safe place to keep data in instances where we lose connection to the cloud.
We have written custom services to leave that data on the drive when there is no access to the cloud, and when the service is reconnected, we have the ability to re-consume that data in a throttled fashion so that it does not interfere with the real-time production data being streamed to the cloud.
What will future advances in remote monitoring look like, and how will these expand on these systems’ existing functionality?
Production data is going to be the next key differentiating factor for long-term storage.
We can already show measurements along the material, averages of profiles, and things that have been taken in time in the direction of travel the material in distinct graphs.
We can also overlay these on the same graph in order to troubleshoot synchronization issues or to see if a change in line speed has caused an issue.
This is one of the types of data we are going to store long-term in order to introduce additional personas to our software.
In this context, a persona represents a focus on a particular user type. Our focus is currently on those service and maintenance personnel looking to guarantee uptime.
Future personas that we are going add include those of the quality engineer and the production manager, tracking things like product yield, the efficiency of the coating, the uptime of the line and the physical dimensions of the battery.
The other types of measurements that we are going to store are high resolution measurements across the strip. As the profile is taken, the carriage is sweeping across the material. There are around 2,000 measurements taken, and those measurements are going to be stored in a down-sampled format so that users can observe, replay and analyze those in the future.
We will have the ability to display those and to tab or play through them to see what has happened historically, allowing users to observe those changes versus a target or versus the average of what was being produced at the time.
We are already developing the second version of the platform, and we think that the ability of people with larger facilities to see at a glance the entire scope of the health of their systems will be key moving forward.
Our field service engineers will also be able to see the health of those systems, allowing them to proactively contact customers if they see an issue.
Online notifications will be enabled, so when something breaks, both the manufacturer’s personnel and our service personnel will be able to react much quicker than having to wait for an issue to be discovered, wait for a phone call or a service visit, and then finally seeing the data needed to analyze the situation.
These are all capabilities we are building into future systems.
About Chris Burnett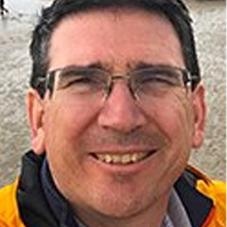
Chris Burnett studied Physics at Worcester Polytechnic Institute, MA/USA and has held various positions at Thermo Fisher Scientific including Director of Sensor Development and Manager of Systems Integration and Systems Production in the company's Flat Sheet Gauging business unit. With more than 25 years of experience, Chris currently helps drive solutions for the battery industry in his current role as Senior Field Marketing Manager.
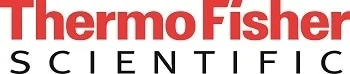
This information has been sourced, reviewed and adapted from materials provided by Thermo Fisher Scientific – Solutions for Industrial and Safety Applications.
For more information on this source, please visit Thermo Fisher Scientific – Solutions for Industrial and Safety Applications.
Disclaimer: The views expressed here are those of the interviewee and do not necessarily represent the views of AZoM.com Limited (T/A) AZoNetwork, the owner and operator of this website. This disclaimer forms part of the Terms and Conditions of use of this website.