It is critical that battery manufacturing processes be monitored throughout the entire production process, from incoming raw materials to finished cells.
This interview with Chris Burnett, Senior Field Marketing Manager for Gauging at Thermo Fisher Scientific, and Zal Louw, the company’s Marketing Development Manager, looks at a range of tools, techniques and process improvements designed to ensure optimum quality and productivity at every step of the battery manufacturing process.
The practical applications of each tool and method are summarized and explored in an array of raw material inspection, electrode manufacturing and cell material validation and inspection process steps.
Could you start by providing a brief summary of the battery manufacturing process and where monitoring occurs during this?
Material scientists continually strive to design the ultimate battery in terms of its lifetime, charge capacity and suitability for its final application.
When they have selected the ideal chemistry for their battery application, the bulk materials containing the required elements must be extracted from mines, where quality inspection and bulk chemical analysis can take place. Once the raw material has been refined, it must be inspected to make sure it possesses the required level of purity.
Electrical testing takes place once the final cell is complete, but there are a number of other non-destructive testing that can be employed at various steps throughout the production process to analyze the quality of the battery before it reaches its final application.
Materials must also be recycled once the battery has reached the end of its life. Many expensive materials are used in making batteries, so we want to ensure that the recycling steps are equally robust and that we use the right tools to check the composition so we are not throwing away materials that have value.
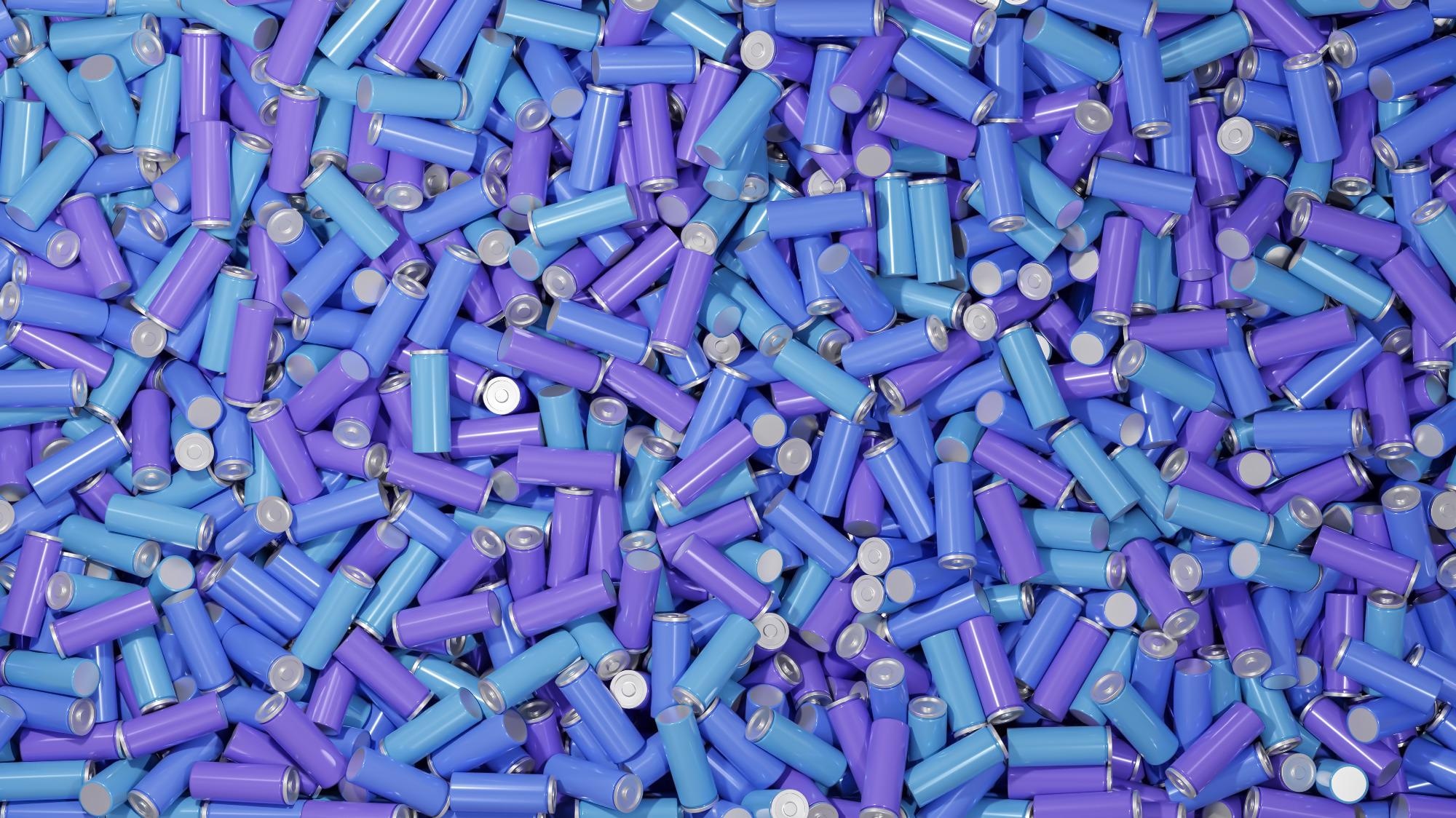
Image Credit:Shutterstock/Black_Kira
What are some of the most commonly employed tools for monitoring quality throughout the battery process?
A number of tools are available to do this, including laboratory essentials such as clean rooms, safety equipment, respirators and Tyvek suits. Working in the most sterile environment possible gives the battery materials the best chance of achieving their longevity and charge capacity goals.
Sampling every ingredient for chemical purity and mechanical properties results in a quality outcome. Essentially, when you have mechanically and chemically pure raw materials, you can manufacture the best battery.
It is possible to do this by conducting a vibrational study using Raman, FTIR or near-infrared, or by looking at the material’s structure using X-Ray diffraction.
Material and elemental identification can be done using X-Ray fluorescence or optical emission spectroscopy. When working with individual smaller samples, it is also possible to achieve a high-resolution image using ultraviolet and visible light.
Looking at the compound typically involves looking at its mechanical properties, whether this is the viscosity, the rheometry of the slurry used in making the battery or a simulation of the extrusion process.
All of these steps and processes can be monitored using different instruments. It is essential to look at every process step to validate the quality of components going in or the quality of the battery coming out.
Could you elaborate on some of the chromatography techniques used for verifying the quality of the raw materials used in batteries?
Mass spectrometry and ion chromatography are excellent means of identifying the non-volatile electrolyte and analyzing this in terms of degradation in the electrolyte itself.
ICP mass spectrometry can be used to investigate some of the battery’s metal-based compounds. At the same time, gas chromatography helps look at the volatiles involved in the degradation of the electrolyte, potentially by looking at any off-gassing occurring.
Instruments are available which are very specific and sensitive enough to measure these compounds at parts per billion levels. Incoming material can be analyzed using optical emission spectroscopy, XRF or ICP.
The cathode is the most expensive part of the battery, so it is important to detect these impurities early in the process before starting to mix the slurry and adding this to the electrode. Again, optical emission spectroscopy and mass spectrometry can help achieve those vital raw material goals.
Tools such as glow discharge mass spectrometry, X-Ray fluorescence and X-Ray diffraction are all extremely useful for looking at the composition of the material, ensuring the cathode alloy contains the correct percentage of each individual element and that the construction itself features the correct crystal structure.
These techniques can be leveraged via several benchtop and laboratory-based units able to offer fast and accurate results. The goal is to ensure that production remains in a steady state and that this is not interrupted by poor-quality materials.
Manufacturers need to be able to correct any problems with incoming material purity in order to prevent poor battery construction further down the line.
What tools and techniques can be used to monitor quality during the electrode coating process?
Electrode coating represents a sizable investment, whether it is the anode or the cathode coating process. A coating line typically includes rewinders, ovens and extrusion dies. It is important to monitor these processes at every point in the line to check the quality of the incoming raw material.
For example, it is possible to check the application of slurry onto the substrate, ensure an appropriate amount of drying is taking place in the oven and look at the thickness of the coating on both the top and bottom sides of the substrate.
Each of these steps must be differentiated with high-resolution measurement edge to edge to ensure uniform loading across the battery.
Another important constituent of the battery cell is the separator film. In large-scale manufacturing processes, this material can be up to seven meters wide, requiring a wide scanner able to measure thickness uniformity. When slitting the separator film, we need to ensure that the thickness at one edge is the same as the middle and the other edge.
Once anode and cathode electrode materials are complete, a calendaring operation takes place where dimensional thickness is critical. This can be monitored using online confocal laser thickness gauges to ensure that materials are pressed to the exact thickness required.
The confocal laser provides the sub-micron resolution needed to be able to validate the thickness, which can quickly add up to become out of spec as multiple layers are stacked or as this is coiled for a cylindrical battery.
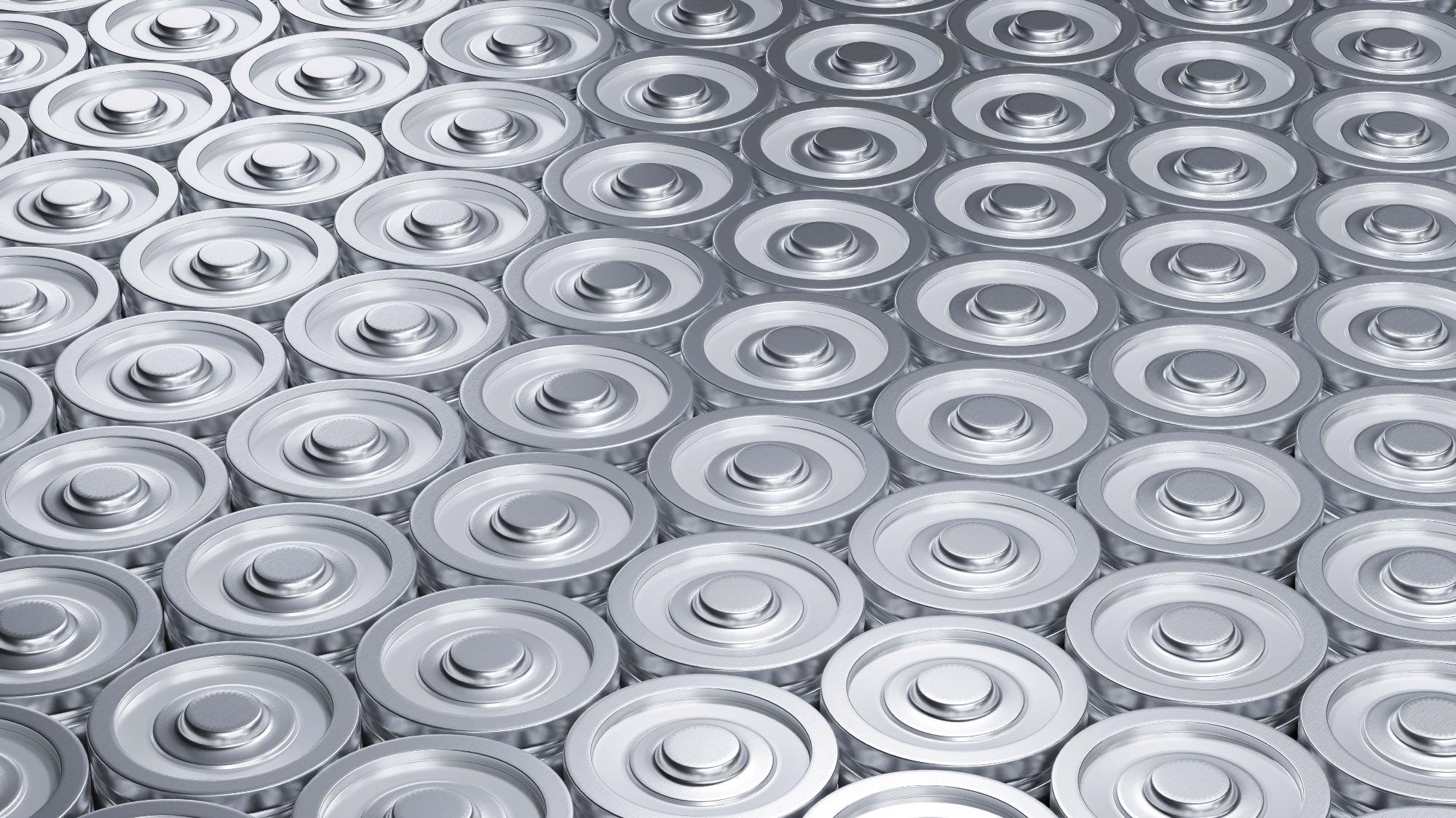
Image Credit:Shutterstock/Black_Kira
Where do microscopy and image characterization techniques fit into quality control processes in battery manufacturing?
Microscopy and image characterization techniques can be used as part of cell validation and for vital material checks during the manufacturing process.
A typical battery has a complex electrode chemistry system that must be monitored and validated from the raw materials to create the electrode and cell. We need to understand this process at a market scale level.
At the market scale, we can use a range of different imaging techniques to understand the correlation between a battery’s structure and its performance, such as micro-CT, electron microscopy, and even TEM. Each of these techniques offers the range of resolutions required to understand the different battery parts.
Micro-CT is a vital tool in an industry environment for the non-destructive 2D and 3D inspection of battery cells. This allows manufacturers to understand the cell structure after this has been manufactured, providing valuable manufacturing insights and ensuring.
Using non-destructive X-Ray techniques to penetrate a completed cell and see the internal details allows manufacturers to enhance the safety of the battery and help protect end-users.
Micro-CT works by passing an X-Ray through a cylindrical sample shape while a stage rotates in a helical shape. This allows the collection of useful 3D data and the internal information, for example, the cell shape, what the center pin looks like, how the electrode is wrapped up, and how this changes from the top to the bottom.
This data can be used to investigate defects affecting performance, for example, caused by electrode delamination in the fabric cell.
Scanning electron microscopy can be used to study the battery materials’ quality – particularly the materials’ morphology, which is critical for the batteries’ performance.
How does EDS and ACM analysis complement the techniques already discussed?
EDS capability on the electron microscope is ideal for materials analysis because it can deliver accurate elemental data in a short amount of time. This element information is important for understanding the chemical components of battery materials. While EDS is useful for elemental analysis, ACM is ideal for material structure analysis.
Technology is available to automatically use ACM and EDS to study battery components and analyze sample purity. This is important because magnetic materials such as zinc, iron, or nickel can be harmful to custom materials fabrication processes because they can cause a short circuit and degrade battery cells.
An automated ACM and EDS workflow involves inserting sample which is automatically divided into different regions. In each region, users can automatically differentiate the particles of interest; for example, some customers are only looking for contaminants larger than 10 microns in size.
Once a potential contaminant has been highlighted, we can do EDS analysis on that particle to determine what type of matter it is and if it could be the root cause of any contamination.
This process helps monitor the purity of a manufacturing environment, enabling the detection and characterization of any impurities in electrodes and raw materials.
What are the benefits of using dual beam technology in quality and failure analysis?
A scanning electron microscope can be used to understand a battery sample’s morphology at the nanoscale and microscale.
Adding a focused ion beam column as an additional column enables better battery targeting and more in-depth analysis. For example, using the focused ion beam to open an electrode sample allows the user to check the electrode quality and interface.
Where there is no uniform distribution across the electrode, this may be an indication that the process needs to be improved
This technique can help with quality analysis and failure analysis. It can also provide excellent image quality at marginal scales because we can look at particles and small features like binders collecting multimodal information.
About Chris Burnett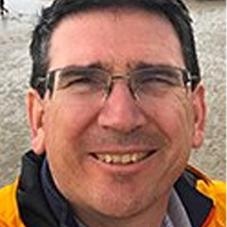
Chris Burnett studied Physics at Worcester Polytechnic Institute, MA/USA and has held various positions at Thermo Fisher Scientific such as Director of Sensor Development or Manager of Systems Integration and Systems Production in the company's Flat Sheet Gauging business unit. With more than 25 years of experience, Chris currently helps drive solutions for the battery industry in his current role as Senior Field Marketing Manager.
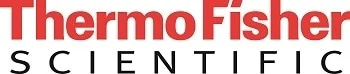
This information has been sourced, reviewed and adapted from materials provided by Thermo Fisher Scientific – Solutions for Industrial and Safety Applications.
For more information on this source, please visit Thermo Fisher Scientific – Solutions for Industrial and Safety Applications.
Disclaimer: The views expressed here are those of the interviewee and do not necessarily represent the views of AZoM.com Limited (T/A) AZoNetwork, the owner and operator of this website. This disclaimer forms part of the Terms and Conditions of use of this website.