Vast amounts of energy are used every year (3-5% of the world’s total electrical energy use) in the mining and minerals processing industries to grind mined rocks and ores in preparation for subsequent processing and metal extraction. However, this could be greatly reduced by using microwave energy. EPSRC-funded research at the University of Nottingham has investigated the use of microwaves to weaken ores prior to the grinding mill stage. Potential Savings Using Microwave Energy While research in this area has been going on for a number of years, engineers at Nottingham have made a breakthrough by developing a technique that uses microwave energy at significantly reduced levels. ‘In the past you may have been able to save 20 kilowatt hours per tonne of grinding energy but it would take 200 kilowatt hours of microwave energy to achieve this,’ says Dr Sam Kingman, who is leading the research. ‘We only need to use less than half a kilowatt hour per tonne [of microwave energy] to enable a potential energy saving of 10-12 kilowatt hours per tonne in grinding energy.’ How Microwave Energy is Used to Assist in Mineral Processing Using numerical modelling and computer simulations, Kingman has discovered that you do not need the microwaves to heat the samples to very high temperatures, just the ability to heat them differentially. Working with Rio Tinto and Professor Steve Bradshaw from Stellenbosch University in South Africa, Kingman hopes that within five years there will be a plant somewhere in the world taking advantage of the technology. How the Microwave Process Works Currently, the mining industry uses crushers and grinding mills to break and then liberate individual minerals. Once liberated, the minerals can be recovered and concentrated. ‘To grind the material into a size that is recoverable is very energy intensive,’ says Kingman. ‘Typically, only 1% of the energy input is used to create new surfaces, the rest is turned into noise and heat.’ Now, prior to mechanically grinding the material, microwaves can be used to selectively heat parts of the rock, causing them to fracture along grain boundaries. ‘Just like when you put a treacle tart in the microwave to heat it up, the treacle gets hot but the pastry doesn’t because the sugary centre has much greater microwave absorbing properties. The same happens in this process - certain phases heat and certain phases don’t because they are transparent. Heating within a transparent matrix creates thermal stresses, which pre-weakens the material by creating cracking along the grain boundaries,’ says Kingman. Determining the Optimum Microwave Parameters Undeterred by the problems that have hindered many researchers before, Kingman went back to basics - investigating how microwaves interact with minerals and how you can control this interaction to develop the best way to microwave different rock types. This has involved using computer simulations to calculate the timing and power of microwaves required, and testing these in a microwave cavity once the optimum treatment conditions for a given material have been established, figures 1 and 2. 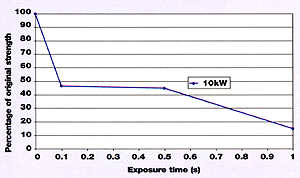 | Figure 1. Results from tests performed to determine optimum treatment conditions for a lead-zinc ore. | 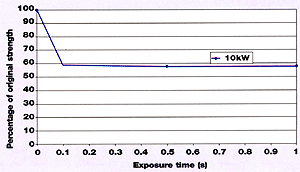 | Figure 2. Results from tests performed to determine optimum treatment conditions for a copper ore. | Modelling Microwave Induced Stress Distributions Using 2D finite difference modelling, Kingman can simulate microwave heating and how it affects the distribution of stresses within the sample. ‘If we have an idea of what the heating rate is inside each mineral we can then model the thermally-generated stresses,’ he says. ‘Once we know what the thermal stresses are, we can then predict how the stress of the ore will change and what the likely affect of microwave treating at that power level will be.’ ‘As we are using irregular particles, we test at least 20 and take the mean to produce the graphs [shown in figures 1 and 2],’says Dr Keith Jackson, Research Fellow at the University of Nottingham. ‘In general, we find that there is a maximum level of damage we can create for a given ore under a given power level and when we achieve that we see a marked flattening of the curve, as shown by the copper ore (figure 2).' Determining Optimum Heating Rates Kingman has also been working with Professor Bradshaw on electromagnetic modelling, which involves 3D modelling of microwave fields, and using this data for setting specific heating rates. ‘They design the microwave cavity, which gives us certain values of electric field. We can then use those values and put them into our stress simulations to see if the rock breaks or not.’ Optimum Microwave Processing Parameters Based on the modelling work, the researchers have developed a range of microwave ‘recipes’ for breaking down different rock types, which vary depending on the material being heated and how it needs to be broken down. The team has found that some rocks only need to be microwaved for less than a tenth of a second to produce the desired effect. ‘The most important thing is the heating rate,’ says Kingman. ‘We have found that if you deposit energy into the sample very quickly you create thermal stresses along the grain boundaries without the need to heat the material to very high temperatures. The rock doesn’t actually get hot. instead it heats up along the grain boundaries, which causes it to fail.’ Microwave Cavity Design for Minerals Processing The design of the cavity is very different from that seen in a conventional kitchen microwave, but the electromagnetic principles are exactly the same. Home cooking units tend to incorporate a multimode cavity, which means the energy is not focused on one specific point. However, when microwaving rocks you do need energy focused on one point to get sufficient energy into the rocks to efficiently break them down. Kingman has received additional funding from the EPSRC to collaborate with Professor Steve Bradshaw on designing special microwave cavities for industrial equipment. ‘It is a classic case of multi-disciplinary work taking things forward,’ says Kingman. ‘Professor Bradshaw and his team understand how to model microwave fields, and we know what microwave fields we want and the affect they will have on the material. The marriage of the two fields of expertise is important for the future development of the technology.’ The Effect of Ore Composition Kingman and his team have made more progress towards economic breakage of rocks in the past year than people have made in the past two hundred years. To date work has been carried out on a variety of ores, including gold, copper, lead, zinc and iron. ‘You need a material that has at least one phase that responds well to microwaves,’ he says. ‘The best absorbing minerals are sulphides and oxides, such as pyrite, haematite and magnetite.’ Advantages of the Microwave Processing Technique The design of the microwave cavity has produced a step change in the development of the technology by taking electromagnetic design principles and integrating them with process engineering. The energy-saving technique has already attracted interest from some of the key players in the mining industry, including Rio Tinto, who has supported the research since 1995 and plans to use the technology, if further tests prove successful. Not only do you save energy but you also recover more of the valuable mineral. ‘This is quite an important time for us as we move from the laboratory towards designing and building pilot equipment based on the technology,’ says Kingman. ‘Hopefully by the end of this year we will be able to process samples at around a tonne an hour, and by early next year, up to two or three tonnes an hour.’ Only when the technology is used at scale will the real benefits become clear, but the technique has the potential to reduce current grinding costs by 50-60% and have a significant impact on reducing global warming. ‘Each kilowatt-hour of electricity used currently produces 1.5kg of CO2,’ says Kingman. ‘The fact that you need less grinding mills is one thing, but reducing emissions is the most important thing.’ If the technology is used in the design stage, it could allow plants to be smaller, saving capital costs by replacing two or three pieces of equipment that might cost up to US$10 million each. Summary The demand for new metals is increasing and this technology could offer the ability to process ores that cannot be treated at the moment, at a time when conserving energy and reducing global warming has never been more important. |