Can you explain what Automated Quality Control (AQC) is?
In simple terms, automated quality control is the process of mounting metrology equipment on an industrial robot to automate the measuring process. A more sophisticated definition could be that AQC is a path to solve productivity issues of the quality control process of manufacturing companies.
What fields are we seeing AQC being used in the most?
AQC can be used in different industries, traditionally for the quality control of the production process. This particular application implies measuring multiple parts in repetition to analyze trends to evaluate how a manufacturing process evolves over time. Trend charts can also be used to optimize that specific process.
Another area where we see increased adoption of AQC is to monitor quality control prior to the start of production. Customers used to have to measure one part with the CMM to adjust fixtures or tooling.
Now, however, a more recent trend is to see manufacturing companies measuring 10-15 parts prior to making a decision on tooling modification to average the impact of multiple factors involved in making a part. This places increased pressure on CMM which are already quite slow. To compensate for that loss of productivity, people are beginning to turn to AQC, also known as 3Dscanning CMM.
What are some of the difficulties of Automated Quality Control?
Usually, there are two main difficulties that need to be considered before adopting automated quality control: experience and Return On Investment.
Experience refers to the fact that some customers do not have employees with skills in robotics. Many executives or managers of manufacturing companies wonder if their employees will be able to deploy and use AQC, taking advantage of all of the benefits of such an automated quality control solution.
ROI, like any other capital expenditure, is important to build a business case. When it comes to AQC, customers need to first decide which task they want to automate and then explore all the factors that will be impacted by the automation of that task.
It is common to say that Automation is productivity, meaning that it can help to increase the top-line gain by getting more parts out of the door. That is only one portion of the ROI calculation, however. Cutting waste – rework – scrap can also have a massive impact on the profitability of a company. It is important to consider multiple factors in the ROI calculation.
Can you explain what VXscan-R is and what it does?
VXscan-R solves the issue associated with experience, as previously mentioned. VXscan-R is a Creaform proprietary digital twin environment. VXscan-R enables customers without experience in robotic or 3D scanning to use the MetraSCAN-R in a custom robotic cell or the CUBE-R (Creaform turnkey solution for AQC).
Users only need to specify what they want to scan by selecting surfaces on a CAD model and the software will generate a robot path free of collision and singularities, and is optimized for scan quality and cycle time.
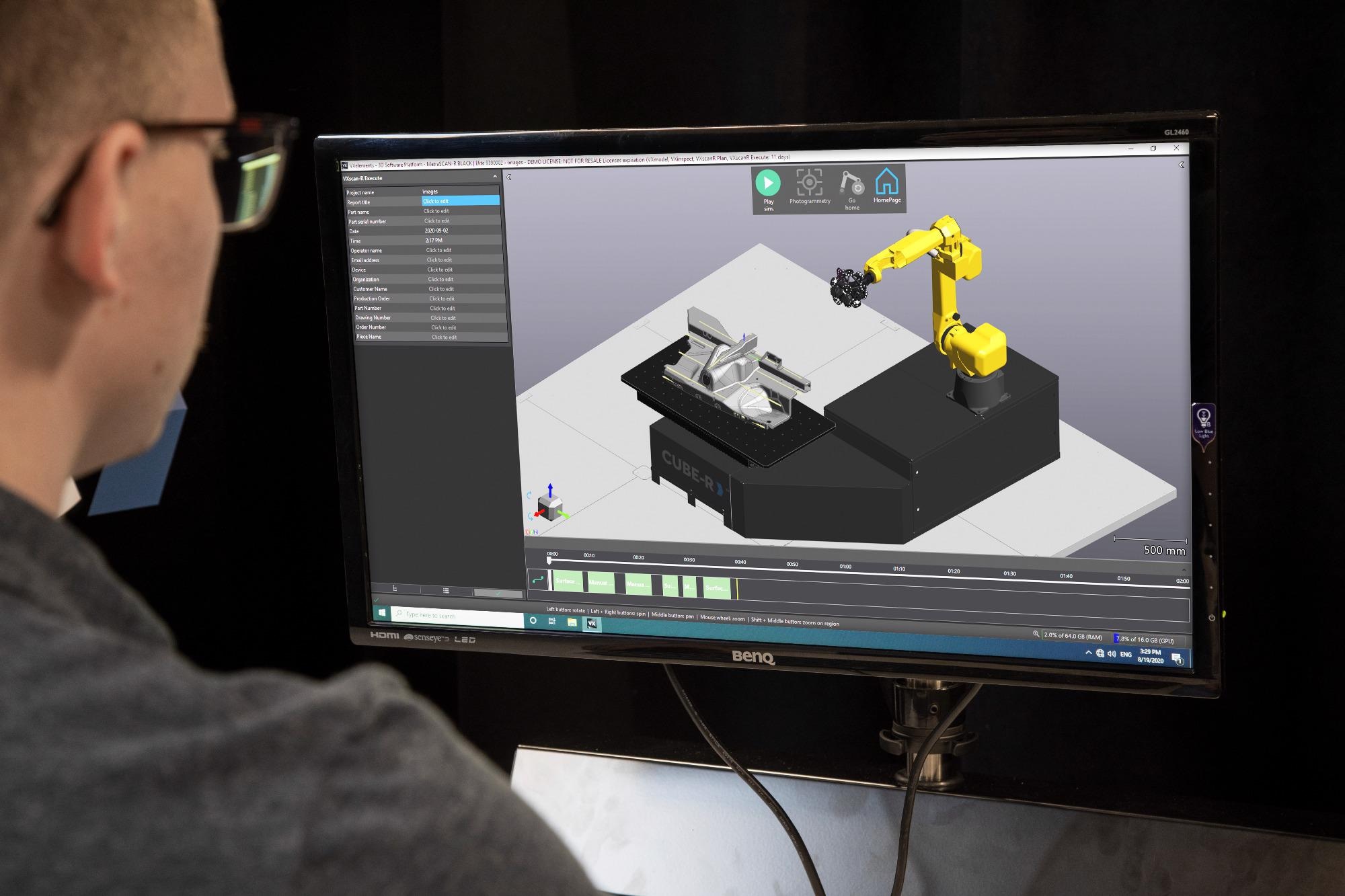
Image Credit: Creaform
What makes the VXscan-R ideal for beginners working in the fields of 3D scanning or robotics?
The simplicity of VXscan-R makes it ideal for beginners in the robotics industry. Users just need to specify which surfaces need to be covered and the software takes care of the rest while taking into account the scanning parameters (speed, line of sight, overlap, etc) to maximize scan quality with the shortest cycle time possible.
How does VXscan-R achieve optimal dimensional measurements in the shortest cycle time?
VXscan-R is the only software optimized for Creaform technologies when generating the scan path. All the best scanning techniques are embedded in the software path planning tool to find the best solution for scan quality in the shortest cycle time.
An example would be the scanning speed, which is linked to the scanning resolution. When scanning a surface, if a user desires more detailed measurements (resolution), the program will automatically adjust the scanning speed to make sure there is enough density to properly reconstruct the surface at the resolution requested by the user.
This principle is the same for the line of sight between the scanner and the tracking device (C-Track), overlap between scanning sweeps, collision detection, etc. Everything is optimized based on what the user requests. Some parameters are configurable and others are hard constraints that the software needs to work with.
How does this element of the system compete with alternative platforms on the market?
Compared to traditional off-line programming solutions, VXscan-R with its scanning intelligence (best practices embedded) is simpler to use and much faster. The solution generated is optimal for the scanner as it requires much less fine-tuning compared to the scan path generated by generic OLP.
Can you explain the benefits that this element of the performance of VXscan-R offers the consumer?
The VXscan-R offers the use four main benefits:
- Simplicity: Easy to use programming tools and a realistic simulation environment.
- Speed vs Resolution: Automatic adjustment of scanning speed based on the scanning resolution.
- Scanner Orientation: Optimization for stand-off distance, scanning angle, overlap and MetraSCAN-R visibility.
- Calculation time: Faster overall process compared to working with other solutions.
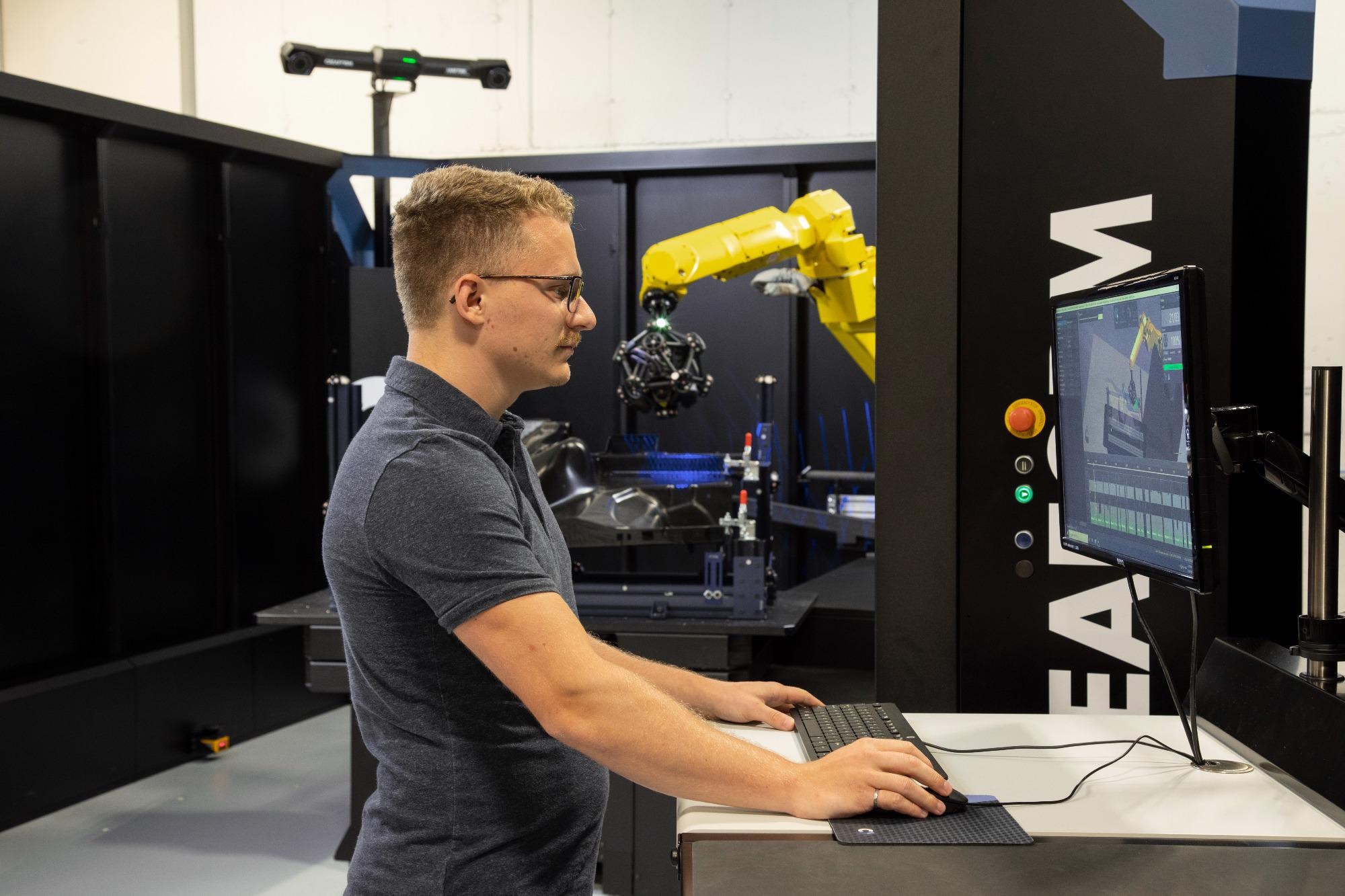
Image Credit: Creaform
Can you explain some of the security and programming issues that VXscan-R helps the user avoid or overcome?
When it comes to overcoming security and programming issues, VXscan-R is ideal. It first helps users overcome collision avoidance. VXscan-R includes algorithms and tools to detect and calculate alternative paths to avoid collision between the MetraSCAN-R and the fixture or the part. To do so, VXscan-R uses a collision envelope that is bigger than the MetraSCAN-R to make sure it remains safe to scan the part.
VXscan-R also limits the scanning speed of the robot to make sure the scan quality remains good but also to ensure that the scanning equipment is not damaged by too strong acceleration or deceleration.
The visibility between the MetraSCAN-R and the C-Track is always maximized. This has a direct impact on the scan quality.
VXscan-R can also optimize cycle time by reorganizing the scan path in an order that is the most efficient instead of keeping it by order of creation. Users do not need to pay attention to how they create areas to scan, the software will optimize everything for them. They can also add or remove more areas to scan and the software will reoptimize it.
Can you explain how well VXscan-R links up with metrology software?
VXscan-R can be directly linked to Metrologic X4, PolyWorks and VXinspect. Based on users' preferences, the software will connect to the Metrology software and send the data to this platform to complete the inspection program.
What are some of the benefits of using a combination of both VXscan-R and metrology?
When choosing a metrology software that users already know, they can benefit from VXscan-R because they do not need to learn how to use a new type of metrology software (this should be included in ROI calculation). By using a known metrology software with an existing program and report template, users can experience a seamless (or even simpler) transition toward automation.
Some solutions on the market are not linked to metrology software, which means the inspection process needs to be triggered manually or automatically from an external application. Other solutions are linked to only one software program, which forces the user to learn and use that particular software. This means, more often than not, that the user has to rebuild the inspection program and report layouts.
About Jérôme-Alexandre Lavoie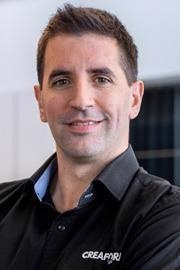
Jérôme-Alexandre Lavoie holds a physics engineering degree from Laval University in Quebec and he joined Creaform in 2007 as an application engineer. Over the years he became expert in all Creaform technologies. After four years of working closely with customers, he became product manager with the mandate to develop Non-Destructive Testing solution using Creaform technologies.
Jérôme-Alexandre accumulated 10 years of experience in 3D data management. He is now in charge of multiple products in various market such as Quality Control, NDT and Automated Quality Control
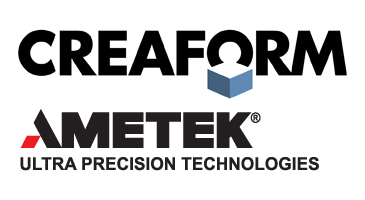
This information has been sourced, reviewed and adapted from materials provided by Creaform Inc.
For more information on this source, please visit Creaform Inc.
Disclaimer: The views expressed here are those of the interviewee and do not necessarily represent the views of AZoM.com Limited (T/A) AZoNetwork, the owner and operator of this website. This disclaimer forms part of the Terms and Conditions of use of this website.