Historically speaking, optimizing the refinery has been mostly focused on final products (e.g., gasoline and diesel), slowly shifting focus to conversion and upgrading process units across the refinery, such as naphtha conversion, catalytic conversion, upgrading units, and alkylation.
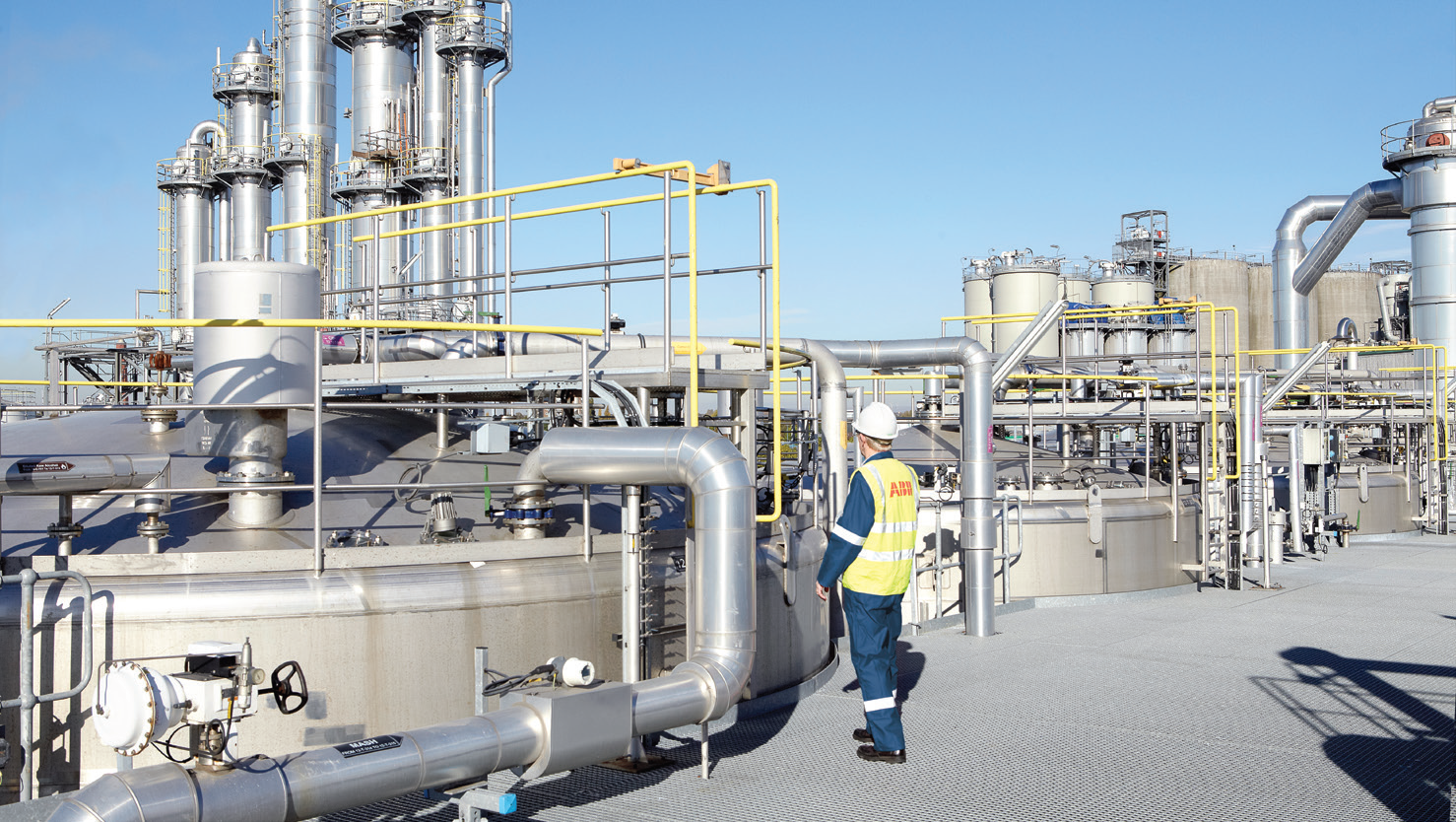
Crude distillation unit (CDU) sometimes called an atmospheric distillation unit (ADU) due to fractionation or distillation of incoming crude feed at atmospheric pressure. Image Credit: ABB Measurement & Analytics
Yet there is one key element of the refinery that has not been optimized to its full potential: rapid and online characterization of crude oil composition. The requirement to identify reliable crude oil quality attributes or qualities is crucial to optimizing yields and maximizing profit in an industry where profit margins are extremely tight and competitive.
Known as the ‘crude assay,’ this existing laboratory method has the potential to determine the state of crucial crude oil parameters. However, crude assays require specialized equipment, time, and operator expertise, which are both time-consuming and expensive.
As a result, full crude assay testing is virtually non-existent or conducted on an infrequent basis predicated on historical supplier information. Refiners often become dependent on outdated or inaccurate data to project production schedules.
This article outlines and demonstrates how ABB near-infrared spectroscopy (FT-NIR) offers a rapid and efficient online crude oil characterization solution, allowing planners to optimize their processes based on accurate real-time knowledge of particular crude oil input.
Crude Oil Chemistry and Characterization Challenges
Crude oil must undergo a process of refinement to produce final products that can range from base fuels (e.g., gasoline, diesel, jet fuels, etc.) to complex petrochemicals (e.g., BTX, ethylene, propylene, lube oils, etc.). The range of products is contingent on the complexity and processing capacities of any given refinery.
Crude oil is a complex mixture of hydrocarbons that range from sweet to sour in content (i.e., low to high sulfur) and other elements, contingent on source extraction, that influence the proportion of light to heavy hydrocarbons in the crude.
These factors have a significant influence on the crude’s price and also on its yield and quality of final products. One considerable challenge encountered with crude oil is that its properties and chemistry are not always consistent, even when they originate from the same source (or same well).
Additionally, most refineries acquire their crude from different sources from around the world. Crude oil is typically purchased on the spot market, with the balance of crude pricing contingent on the qualities and chemical makeup desired. In this context, the differences in yield for crudes acquired at different times can be considerable.
The most important and obvious characteristics of crude oil are its distillation parameters, which are determined by the TBP (true boiling point) curve and consequential cut-point gains, the sulfur content, and the total acid or naphthenic acid content (TAN or NAN).
These vital properties have significant influence ranging from changes in cut-point yields, atmospheric residue %, an impact on downstream clean-up requirements by hydro-treating and the ability to control CDU process train corrosion issues.
For crude processing, the challenge faced by the refiner is processing a time-varying supply quality going into the CDU and a time-varying demand for the distillation products coming out as side draws.
This problem is usually addressed by the refinery LP (linear program) model, which attempts to manage these variations and maintain a balance in supply quality, CDU constraints, and final product demands to optimize the refining margins. As refinery operations may have only historical or partial information on the crude properties, this task becomes even more complex and, in some cases, impossible to plan properly.
In the majority of cases, crude oil, as acquired at the refinery, comes with paper crude assays that are outdated or generic and, sometimes, only based on the extraction site. The actual crude properties for the purchased crude may vary significantly over time, which will have a direct impact on a refinery in its capacity to plan refinery operations to respect customer product quality and maintain profit margins.
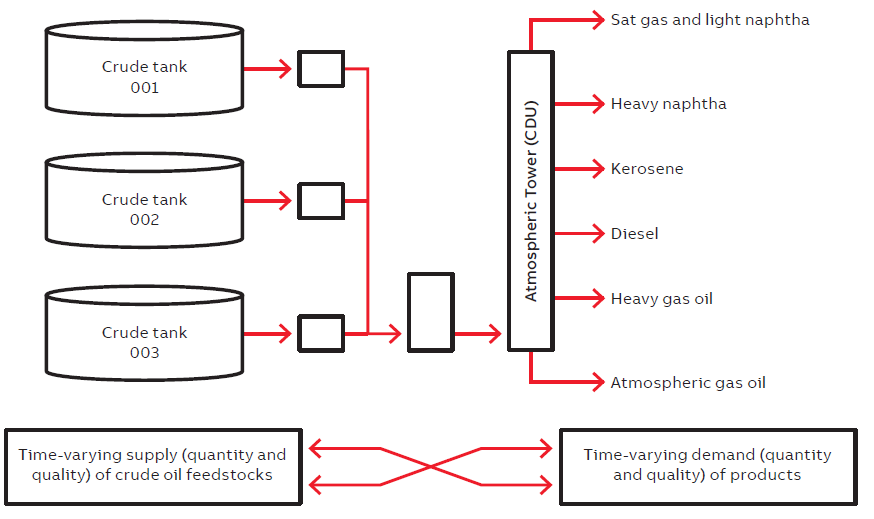
Balance required in the refinery to deal with time-varying supply with time-varying demand of products. Image Credit: ABB Measurement & Analytics
The Importance of Crude Oil Characterization Before Processing
Insufficient crude quality or restricted knowledge about the composition of the crude influences downstream feed quality to other processing units. This can lead to a failure to meet intermediate or final product specifications, impact cost optimization (quality, energy, etc.), and have a significant effect on production planning.
When variables are present in the process input as much as in crude oil, effective analysis tools can assist in maintaining a controlled and balanced production flow. Successfully identifying a given crude slate boosts yields and reduces dependence on supplier-based data.
Unfortunately, conventional crude assay testing methods are expensive ($10K to $20K per single crude assay), extremely complex and time-consuming (up to 2-3 weeks); therefore, they are not usually conducted for every delivery of crude received at the refinery.
The information on quality is absolutely vital, however, to accurately determine the boiling points, sulfur and acid levels, viscosity, water levels, as well as other key qualities, to give a detailed quality breakdown and facilitate adjustment of CDU parameters accordingly. Therefore, it is important that refineries characterize the quality of the crude purchased.
There are two primary reasons for this: First, there is a great degree of commercial competition in this field, and sometimes crude comes from questionable sources or operators. Second is the necessity to validate, in near-real-time, the quality of crude processed in the refinery and applied to processing units, including the crude distillation unit (CDU), and its effect on downstream operational units in a prompt manner to facilitate rapid control and optimization.
Failure to characterize crude oil prior to introduction into the CDU can lead to millions of dollars per year of optimization loss for refiners as a result of process adjustments to compensate for different properties found in crude oil as well as to handle crude transitions.
Depending on the nature of the raw crude to be refined, the operational process units in the refinery must be carefully calibrated. Any changes in crude composition have a significant impact on distillation/fractionation (i.e., yields), as well as downstream to the different conversion and treatment units within a refinery.
The actual impact in dollars will be contingent on the refinery’s capacity and throughput of crude, while the main issues are common from refinery to refinery.
In an industry faced with ever-decreasing profit margins, refineries attempt to optimize every compound extraction and refining process available. Production necessitates constant monitoring and sophisticated analytical equipment.
Vertically integrated or not, refineries are reliant on contemporary data about the crude oil they feed into their process. Given the volumes at stake and the added value of output, the returns can represent millions of dollars,
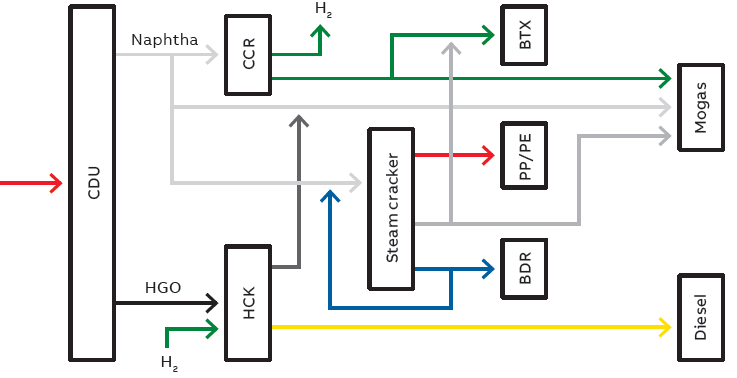
Simplified representation of downstream intermediates and petrochemical products originating from the CDU. Image Credit: ABB Measurement & Analytics
NIR Technology: A Proven Fast and Reliable Analysis Solution
FT-NIR spectroscopy offers a multi-component analysis of key physical and chemical properties through a single measurement: the NIR absorbance spectrum. It facilitates multi-property determination on a complex sample or mixture.
NIR technology is extensively used in the modern refinery as well as in other industries, such as chemical, food, pharmaceutical and semiconductor. ABB has applied FT-NIR technology successfully and extensively in final product blending and to a variety of conversion/upgrading process units within the refinery to supply rapid, precise multi-property analysis.
ABB FT-NIR analyzers can also be applied in crude oil analysis, providing real-time data on crude oil composition prior to it entering the CDU, thus enabling process efficiency with rapid online measurement for control and optimization, replacing the costly and time-consuming laboratory methods for crude oil assays.
An online pre-distillation analysis procedure, therefore, represents the next step in refiners’ efforts to optimize crude oil refining efficiency and profits. The ABB FT-NIR-based solution facilitates proactive process adaptability rather than reactive planning process modifications as a result of inaccurate or flawed data.
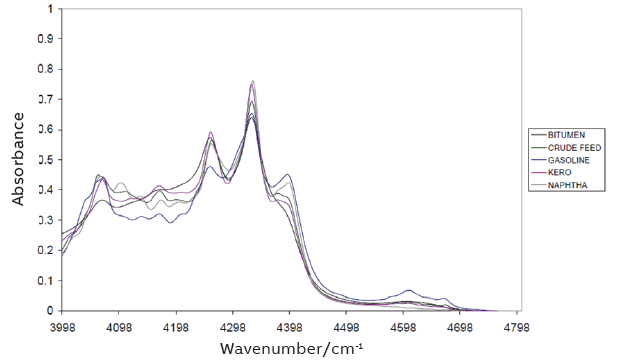
Example of various sample FT-NIR spectra acquired for various sample streams (light to heavy) in the combination band region (4000-4800 cm-1). Similar absorptivity for different hydrocarbon streams despite very different composition and color. Image Credit: ABB Measurement & Analytics
Near-infrared (NIR) technology measurement, as a correlative method, necessitates initial calibration of the analyzer (spectrometer) against a reference method for each property of interest.
The absorption property of near-infrared (NIR) light in the combination band region is analogous to all liquid hydrocarbon streams, regardless of color or chemical makeup. The combination band region can be defined from 4000 cm-1 to 4800 cm-1.
It is the limit between the conventional mid-IR and near-IR spectrum regions, determined by a combination of fundamental vibrations. Absorbance spectrum in combination band region (4000-4800 cm-1) where absorptivity is similar for light to heavy hydrocarbon streams.
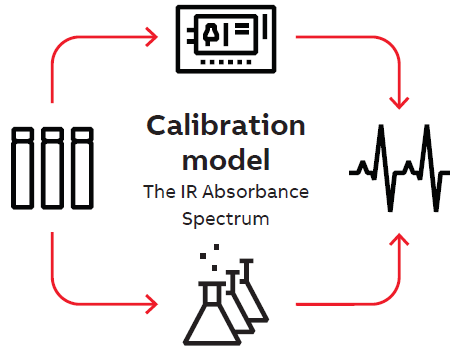
Conversion of absorbance spectrum to chemical and physical properties. Calibration models applied to absorbance spectrum to produce values. Calibration models are essentially learning sets with ASTM laboratory reference values. Image Credit: ABB Measurement & Analytics
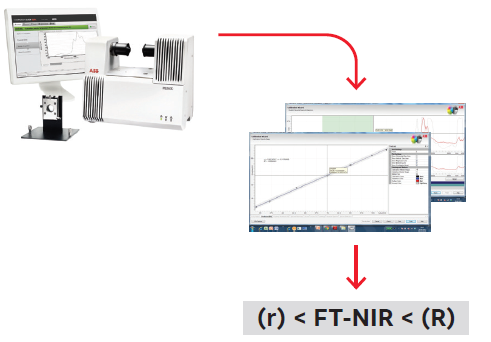
Conversion of absorbance spectrum to chemical and physical properties. Calibration model performance is dependent to local laboratory quality (r) while typical better than the ASTM repeatability (R). Image Credit: ABB Measurement & Analytics
Once the NIR analyzer has been calibrated, it can be applied for routine analysis rather than the more time-consuming conventional measurement methods. The analyzer will demonstrate similar accuracy (i.e., reproducibility) as the reference measurement method against which it was calibrated and will generally offer superior precision (i.e., repeatability) as the technique is not restricted by any potential operator-related error.
NIR analysis, performed within minutes, enables frequent testing of key quality parameters without the need for highly trained, experienced personnel and a number of pieces of specialized equipment on site. It also negates the requirement for consulting external service laboratories.
Existing NIR Crude Oil Characterization Solution Using ABB Crude Assay and Heavy Oil Analyzers
ABB can supply lab-based analyzers, with the MB3600- HP12 model and online process analyzers, such as the FTPA2000-HP260X or TALYS-ASP400-EX models, for crude characterization. Sample conditioning is to ensure reliable measurement and limited maintenance.
Over the years, ABB has built up extensive expertise when it comes to handling crudes and other viscous or heavy products.
All aspects of the process have been taken into account (heating, filtering, flushing, redundancy, stream switching, etc.) within a particular sample conditioning system (SCS) adapted for crude handling to offer dependable solutions for hydrocarbon analysis.
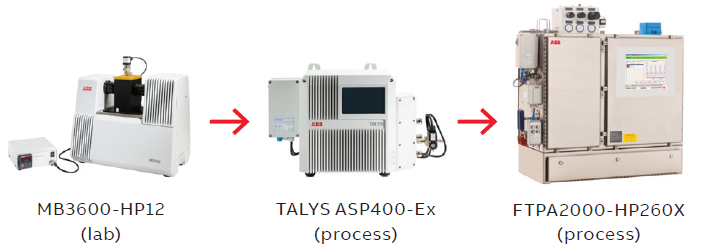
Example of laboratory to process FT-NIR analyzers. Image Credit: ABB Measurement & Analytics
FT-NIR technologies also have the advantage of rapid response, low noise and highly repeatable real-time measurements that can be applied to replace routine labor-intensive and time-consuming standard tests on crude oils and heavy feeds.
This efficiency is backed up by an influential multi-property physical and chemical analysis feature that allows a single analyzer to determine a wide array of crude properties (TBP curve [points], TAN, API Gravity, Conradson Carbon, KV50, KV100, PAH), all on multiple physical streams per analysis.
Single/multiple stream measurements can successfully be achieved with the fiber-optic-based TALYS-ASP400-EX (single channel) and the FTPA2000-HP260X (8-channel) analyzers with the application of a customizable sample conditioning system adapted for crude.
Mastering the crude CDU output measurement has enabled ABB to increase yields considerably for crude oil refiners by limiting measurement times, introducing efficient sampling and enabling planners to work with real-time data to optimize process flow.
The next logical step was to design a solution to address crude oil variability, whether at the extraction site or when crude shipments arrive at the refinery.
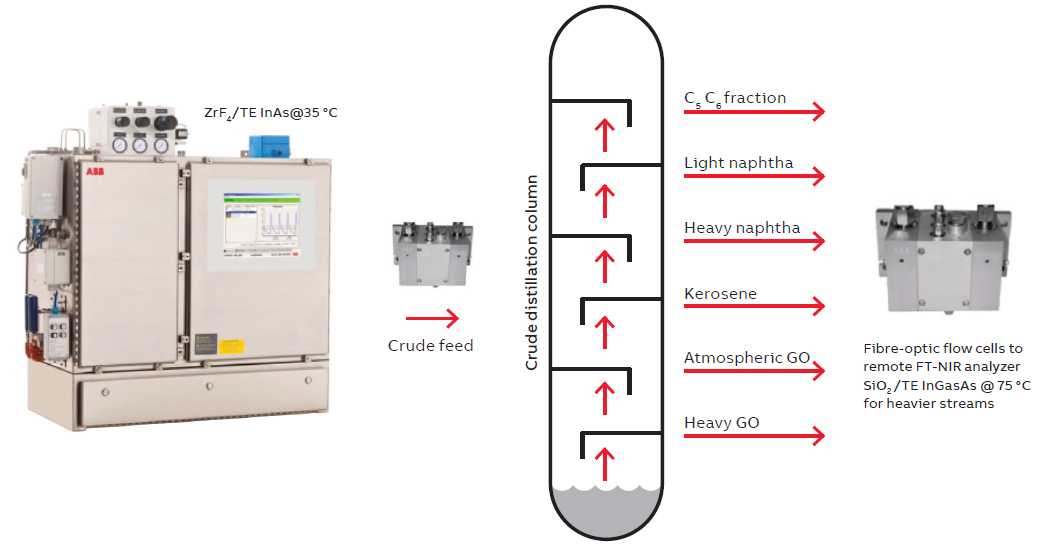
ABB FTPA2000-HP260X multi-channel FT-NIR online analyzer for multi-stream CDU optimization. Image Credit: ABB Measurement & Analytics
ABB’s Crude Oil Input Analysis Solution
The measurement solution that ABB has developed aims to replace expensive formal crude assays and allow optimization of the CDU process before downstream process units. Customization of the entire full online apparatus is possible to match the slate of crudes as used by a refinery.
The online ABB crude oil analysis solution, and its operating system, mean that each system can be adapted to the refiner’s needs or product specialization as it is fully customizable. The online crude oil FT-NIR analysis must be conducted on a sample representative of the product flowing through the pipeline.
Once the sample is fed into the analysis station in a time-constructive manner, it must be properly conditioned for filtration to prevent the build-up of any particles and droplets that could interfere with the measurement.
ABB’s innovative sample conditioning system (SCS) has been developed for this difficult task, taking into account the nature of the product. The SCS principle is to maintain consistent operation with limited maintenance, achieved with dual-stage particle filtration at high temperature and with redundancy.
The system also has the potential to operate on one fast loop while the other is subjected to an automatic cleaning cycle. The SCS can also control the temperature of the sample for optimal water emulsion separation and measurement performance.
Like every ABB SCS, stream switching capabilities are incorporated into the system to allow for automatic analyzer reference measurement. Pressure and temperature feedback are communicated for adequate system control and monitoring.
Once defining the SCS is complete, the end-users only need to calibrate the analyzer using the relevant assay results that exist to correlate data with the NIR spectrum. Crude assay databases, as managed by Intertek, for instance, or spectral standards, verified by crude assay, will therefore be the foundation by which crude oil shipments will be determined and optimized in real-time.
The calibration step determines a numerical relationship between the NIR spectrum of a sample and its assay value as measured by a reference method. This typically involves some mathematical modeling and the application of chemometric algorithms that optimize the covariance between spectral features and the property of interest.
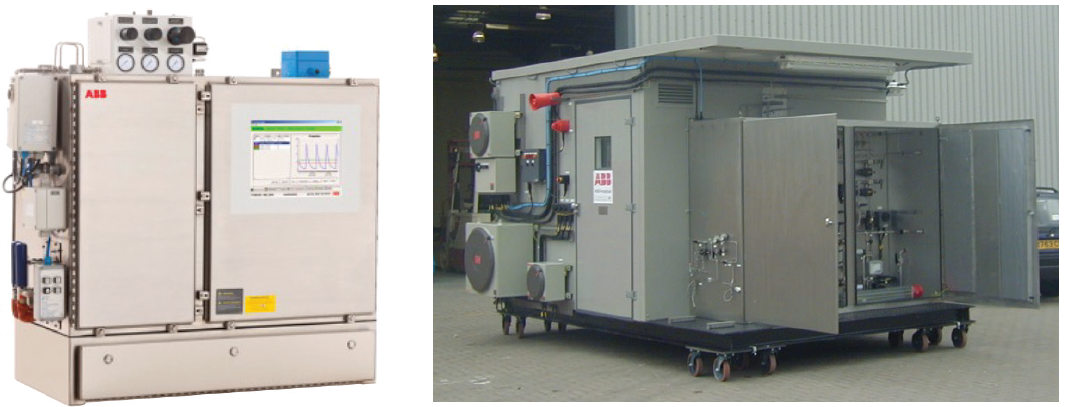
Online crude analyzer with full shelter and sample conditioning system. Image Credit: ABB Measurement & Analytics
When the online apparatus is deployed and calibrated, it becomes a powerful crude oil analyzer configured for analysis, integrated data acquisition, sample control, and reporting.
The solution, with settings that are easily configurable for broad customization, allows for the routine analysis of physical and chemical properties and eradicates operator-generated errors. The ABB crude oil input analysis solution is a complete measurement and reporting solution for refiners as it offers a detailed status display for concentration analysis history.
The technology also has a real-time analyzer health monitoring function incorporated which ensures reliability of data and comes with a range of tools that facilitate easy data export and archiving, thus ensuring accurate crude oil measurements.
ABB’s robust and reliable sampling conditioning and analysis equipment allow production planners to access crude allocation and segregation data in real-time, as well as the use of crude blending optimization parameters and more dependable crude switching (or transition) optimization.
Furthermore, with the constant availability of distillation properties (TBP), contemporary crude assay data, and a crude stability index, planners are able to implement feed preparation to improve process stability.
Most significantly, the data that is readily available facilitates the optimization of various CDU modes, resulting in CDU throughput efficiency and making sure downstream needs to process units are properly met.
Key Advantages of FT-NIR Crude Oil Input Analysis Solution
Crude Trading & Crude Management
- Allows optimal management and scheduling of crude storage.
- Helps purchasing and enables quality assurance to be conducted on the incoming crude against specifications.
- Improves refinery yield prediction with real-time actual crude analysis of all crude imports.
Crude Blending
- Maximizes refinery performance by efficiently controlling the crude blend formulations of CDU feed as close as possible to the optimal crude composition while taking into account tank farm constraints.
Improved CDU Control and Optimization
- Allows the user to feed the actual crude and rundown property measurement to a rigorous dynamic model linked to both the APC and refinery LP.
- Helps accomplish tighter control of CDU by limiting the variations of crude properties at source.
- Links to APS and MES systems to accomplish Refinery Operational Benefits.
Conclusion
The use of NIR technology to conduct a precise determination of various crude oil attributes completely changes conventional monitoring solutions for refiners, allowing for rapid pre-process crude oil measurement to facilitate efficient feedback and control.
The main elements of crude oil composition that have a bearing on CDU optimization can be easily determined with a greater level of precision, replacing missing or expensive crude assays with a fast online measurement.
This produces the opportunity for refinery production planners to conduct crude oil analysis prior to distillation, allowing CDU optimization and effective product control downstream to other refinery process units.
Moreover, the ABB NIR online crude oil measurement solution facilitates the determination of multiple properties for all new samples simultaneously, with accuracy relative to the conventional laboratory assay methods.
These analyses can be carried out by operators without analytical backgrounds. As a result, the number of routine analyses can be increased significantly, while the cost per analysis is significantly reduced compared to conventional assay methods.
The main benefit of NIR technology, with reference to crude oil analysis, lies in its novel combination of precision, versatility and simplicity. The latest generations of NIR analyzers are also exceptionally durable and virtually maintenance-free as they do not necessitate any consumables or preventive maintenance.
At the heart of the solution is the sample conditioning system (SCS), which allows for online sample integrity and therefore makes sure that NIR readings are reliable and uniform.
Additionally, any previously stored sample spectra can be assessed using the latest added calibrations to improve data space for deeper sample analysis. It is also possible to conduct analyses on various sample types (crude mix, altered crude, regional crude extract comparison) to optimize CDU throughput efficiency with considerable savings by lowering operational costs.
The ABB NIR based crude oil input analysis technology is a complete and powerful solution for all refiners.
References
- https://en.wikipedia.org/wiki/Nelson_complexity_index#:~:text=The%20 Nelson%20complexity%20index%20(NCI, of%20various%20refineries%20 and%20units
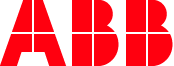
This information has been sourced, reviewed and adapted from materials provided by ABB Measurement & Analytics.
For more information on this source, please visit ABB Measurement & Analytics.