In this interview, AZoM talks to Rohit Ramnath about the certifications for epoxy adhesives and electrical arcing.
What are some of the tests that UL performs with respect to epoxy encapsulants and potting compounds?
Underwriters Laboratories Inc. (UL) is a global safety consulting and certification company. Specific Master Bond epoxy systems are tested by UL in a comprehensive manner for compliance. For example, certain products are used in a very special and specific manner as potting or encapsulating compounds and must be “self-extinguishing” per UL.
Ratings such as UL 94V-0, 94V-1, and 94V-2 are standards for flame retardancy. Other UL ratings test to ensure the safety of hazardous locations. For example, the UL 1203 standard contains technical requirements needed for electrical equipment to be labeled as “explosion-proof” and “dust-ignition proof.” Yet another UL certification tests for resistance to electrical arcing. UL 746A is a High Amp Arc Ignition test for electrical arcing.
Why does electrical arcing occur?
Electrical arcing is a luminous discharge of current that is formed when a strong current jumps a gap in a circuit or between two electrodes. In other words, electrical arcing occurs when electricity jumps from one connection to another.
Arcing can arise through a number of occurrences. For example, a break in the electrical insulation or faulty insulation, corrosion, rupturing, or exposed surfaces on the conductor are all situations that may lead to electrical arcing. If the electrical current loses its way and becomes uncontrolled, the air surrounding the current can ionize and arc. This could lead to combustion and fire.
Ideally, the situation should be avoided entirely, but if arcing does occur, one would want to mitigate the potential damage.
What is the UL 746A High Amp Arc Ignition test and what flame retardancy requirements are applicable for electrical device applications?
An electric arc can potentially cause the degradation of plastics. Compounds can be specifically formulated in a way that makes them not susceptible to such degradation. Underwriters Laboratories developed comprehensive standards to evaluate these materials, and the High Amp Arc Ignition (HAI) specification per UL 746A tests materials for resistance to over 150 arcs without igniting.
In addition to the HAI test, the UL 94HB (horizontal burn) flame retardancy rating for 1.5 mm and 3 mm thickness can be used to determine the suitability of a sealing, potting or encapsulating compound within an electrical system, especially if it is near an ignition source. This combination helps end-users gauge that the product is not only arc-resistant but also flame retardant.
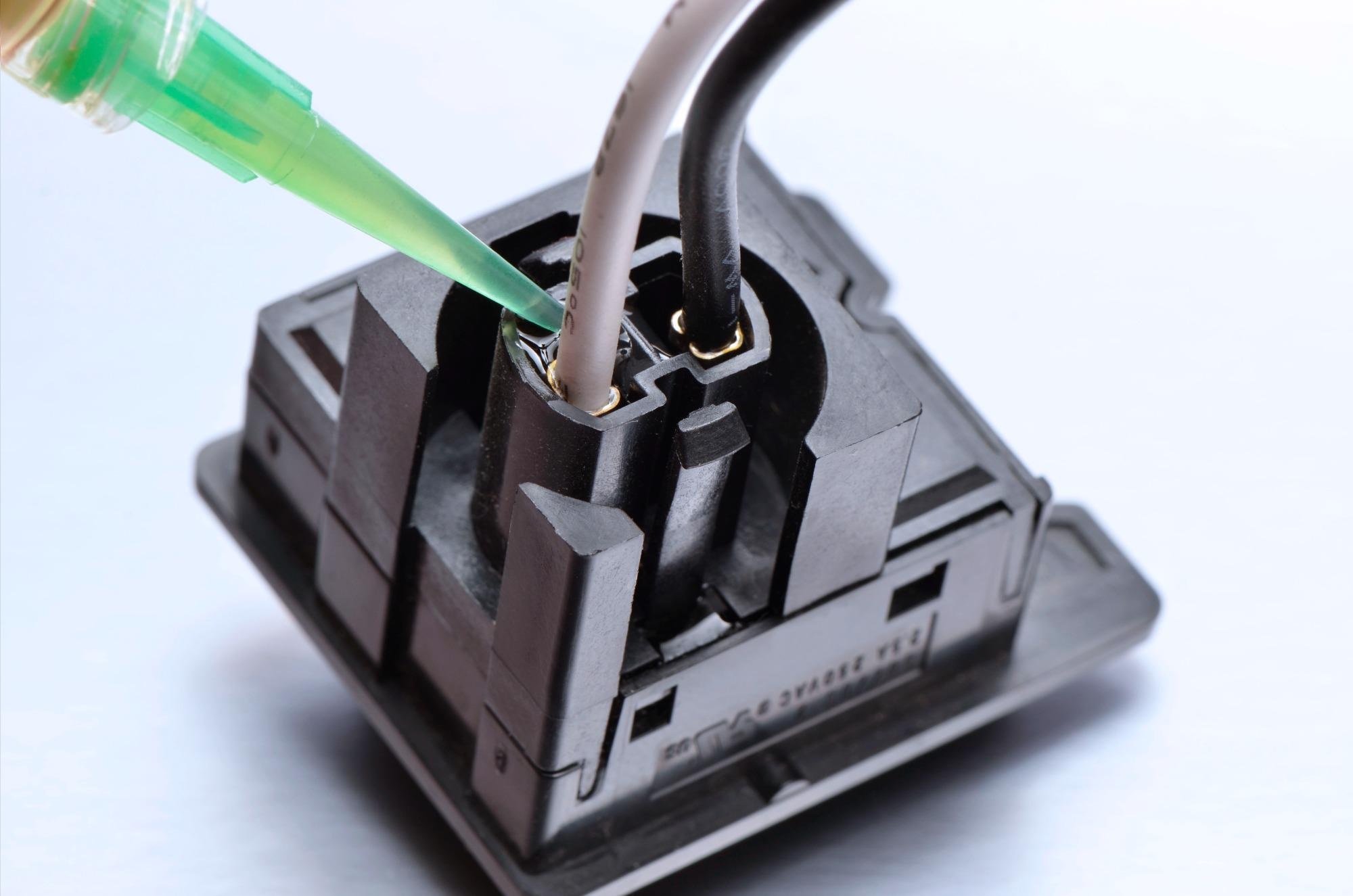
Image Credit: Master Bond Inc.
What Master Bond epoxy can be recommended for applications where arc resistance and flame retardancy are required?
EP21AC is a two-part epoxy with a non-halogenated filler that is formulated for applications where arc resistance and flame retardancy are required. This product was formulated to optimize arc resistance and can be utilized for encapsulating or coating when electrical arcing might be a concern.
When EP21AC was cured at a thickness of 3.0 mm, it withstood 150 arcs without ignition, thereby achieving a Performance Level Category (PLC) of 0. The numbers range from 0 to 4, with 0 being the best achievable rating. EP21AC also passed the UL94HB flammability test.
Where can an epoxy that passes both the UL 746A HAI and the UL94HB tests be used?
Some examples of where electrical arcing might occur are in electronic, electrical, aerospace, automotive electric vehicle, and specialty OEM applications. Such compounds can be used as an encapsulant, sealant or potting compound in various electrical connectors and seals, motors, battery systems etc.
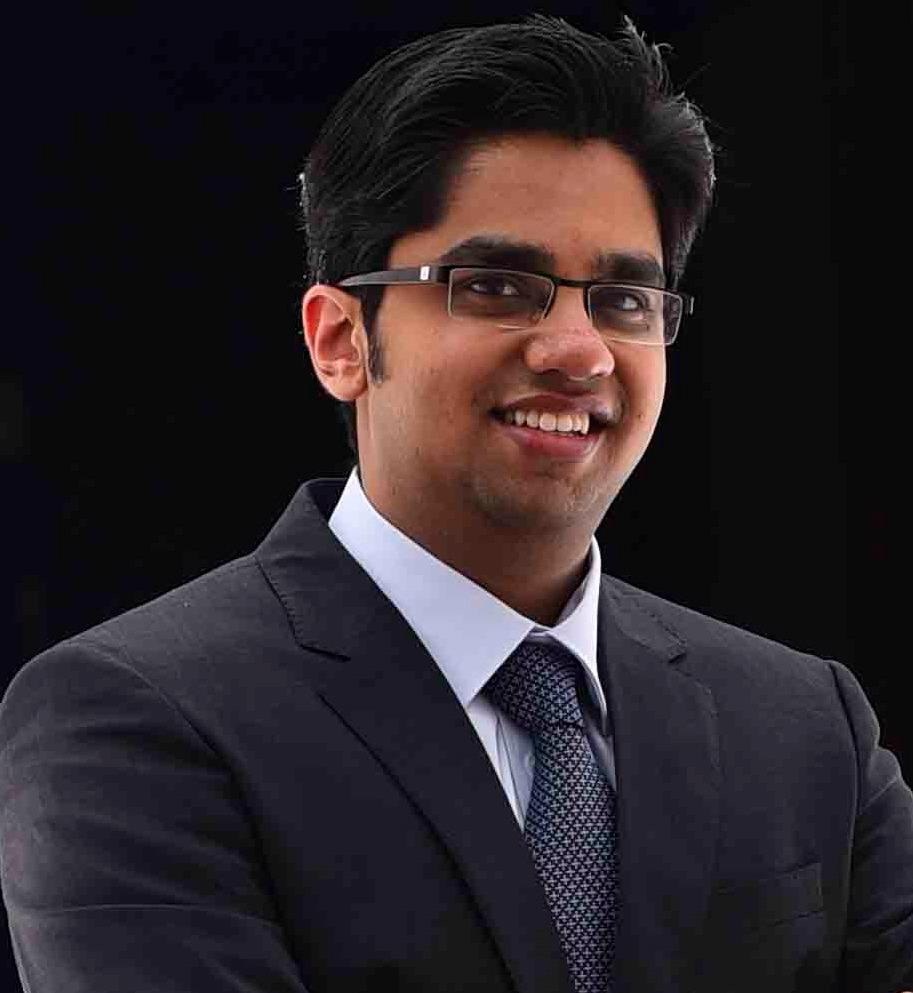
About Rohit Ramnath
Rohit Ramnath is a Senior Product Engineer for Master Bond Inc., a custom-formulated adhesives manufacturer. He analyzes application-oriented issues and provides product solutions for companies in the aerospace, electronics, medical, optical and oil/chemical industries.
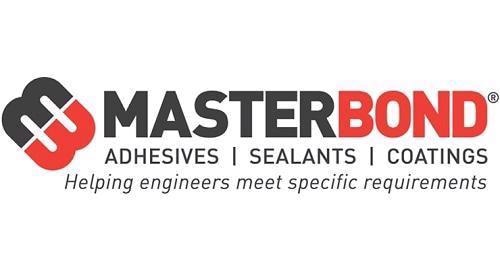
This information has been sourced, reviewed and adapted from materials provided by Master Bond Inc.
For more information on this source, please visit Master Bond Inc.
Disclaimer: The views expressed here are those of the interviewee and do not necessarily represent the views of AZoM.com Limited (T/A) AZoNetwork, the owner and operator of this website. This disclaimer forms part of the Terms and Conditions of use of this website.