Continual consumer demand places increasing pressure on production, which in turn puts a strain on the supply of coated or plated materials. Thus, it becomes necessary to produce components, parts, assemblies, and finished goods in greater volumes with less tolerance for quality defects to optimize yield.
In numerous cases, it is expected that 100% quality inspection is now always conducted, especially in industries like automotive, aerospace, and medical devices, where failures are not tolerated due to inherent safety concerns.
Concurrently, labor costs are on the rise, and employers are finding it hard to find enough qualified workers to keep their operations well-staffed.
To ensure success under these conditions, quality test programs – including the XRF coating thickness and composition analyzer – need to be able to maintain the same pace as production to ensure quality in the end product and catch any deficiencies before they become an issue.
The quicker the right results are achieved, the quicker appropriate action can be taken. This is where the new FT230 coatings analyzer comes in.
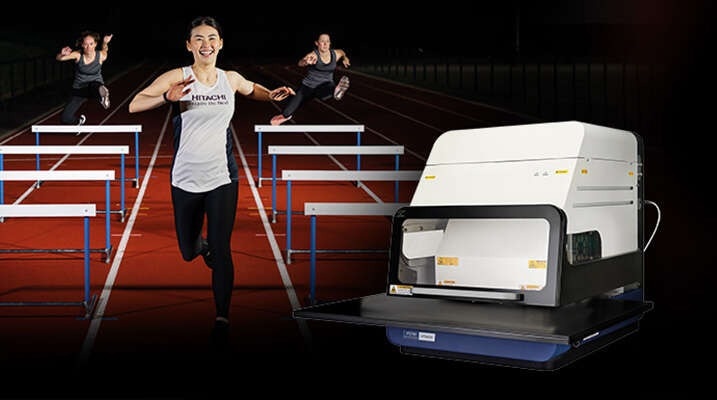
Image Credit: Hitachi High-Tech Analytical Science
Five ways the FT230 can help save money and boost the quality program:
1. Automated Focusing
A key step before initiating an XRF measurement is making sure the part is focused properly. Thereby ensuring the geometry between the X-Ray tube, part, and detector is properly tuned.
Many X-Ray fluorescence analyzers utilize video focus or a laser focus to carry out this task, and those are well-adapted for good focusing. In fact, as the standard configuration, the FT230, comes equipped with a laser focus element. The FT230 can also have two automated focusing techniques that function in different ways: auto approach and auto focus.
The result of the auto approach is similar to the laser focus – the analysis head is transferred to a fixed, pre-set geometry. The difference is that the operator simply initiates the auto approach, and the instrument moves to that geometry automatically rather than the need for manually activating the focus laser. The uto approach is up to 33% faster than manually focusing the laser.
Auto focus works in a different manner. Instead of the analysis head being moved to a pre-set position, the distance from the head to the part is measured by the instrument, which then updates the XRF calculations.
The head does not need to move, even if there are changes in the height, e.g., measuring steps or recessed areas. Auto focus is sometimes referred to as distance independent measurement and works at a range of up to 80 mm (3.1”). As it is not necessary for the head to move, auto focus can be up to 62% faster than aligning parts with a focus laser.
2. Wide-View Camera
When large or complex parts with many features need to be measured, finding the appropriate area to take the measurement from can be a challenge.
The traditional built-in cameras in an XRF coatings analyzer have been developed to magnify a small area of the part to make it easy to pinpoint a measurement location. This means that the operator must manually hunt around the part or with a motorized stage to ensure the area is in view.
It is possible to configure the FT230 using a second camera that is able to see a much larger area of the chamber. The wide-view camera has the capacity to capture an image of the complete measurable area on the stage and enables the user to click on an area of that image to bring the desired feature into view of the conventional positioning camera.
Utilizing the wide-view camera to generate a multi-point program can be up to 20% faster than searching for the intended measurement locations.
3. Find My PartTM
Analyzing routine parts means the same setup tasks are repeated by the operators every time. They need to establish the measurement location(s), select the right calibration(s), select the collimator size that is most appropriate for the area, configure the prescribed measurement time and determine the data handling requirements.
With the exclusive Find My PartTM machine vision feature, each of these steps can be completely automated into one streamlined routine.
The operator simply loads a part into the chamber, initiates Find My PartTM, and the software scans the part and searches for it in the instrument’s library. When an appropriate match is found, the operator only needs to confirm the prompt, and all the measurement and reporting parameters are automatically loaded.
This is the optimal tool for obtaining results fast and getting operators away from measuring coating thickness to optimize the value added to tasks as quickly as possible.
Find My PartTM can also give operators more time and minimize effort by loading measurement routines using a simple text search or by scanning a QR code or barcode. With each of these modes, setup is simplified, removing any questions around the operator’s role, and avoiding mistakes, all of which leads to rapid decision making.
4. User-Centric Software
When working with the XRF machine, nearly all of the operator’s time is spent on the measurement screen. With the all-new FT Connect software on the FT230, the operator’s needs are central to making analysis easier.
The software platforms in use today are typically based on design requirements, limitations, and user preferences from a long time ago. While they incorporate a number of valuable features, training new operators can be difficult since interfaces have advanced significantly since these tools were first developed.
The software on your phone, computer, tablet, TV, car and even your toaster has advanced significantly over the last twenty years. With FT Connect on the FT230, software for any XRF coatings and composition analyzer is up to the task of modern demands.
With FT Connect, the user comes first. FT Connect inverts the user’s interface from previous software platforms. Rather than having a small view of the part surrounded by buttons, controls, and settings, the main focus of the FT Connect measure screen concentrates on the two key tasks an operator must perform: setting up a measurement and acting on the results.
FT Connect incorporates the largest sample view display on the market, covering 60% of the screen, and has extremely flexible lighting controls. The user has the ability to adjust dozens of LEDs as rings, wedge segments or individually to guarantee the best possible view.
The factory pre-set suggestions can assist users who also have the capacity to generate new customized lighting setups to make future measurements easier.
Results are communicated clearly next to the camera view with effective tools for assessing trends and statistics, generating reports, or exporting results and tracking historical results. It is possible to expand each result card to view further details about previous measurements for rapid interpretation.
The data handling capabilities are ready to go for Industry 4.0. Results can be exported in comprehensive JSON format or via spreadsheet for integration with SCADA, QMS, MES or ERP systems. Similarly, it is possible to customize reports for internal or external customers.
5. Instrument Upkeep and Diagnostics
Production facilities are driven to ensure the operation runs continuously; they do not want to face unwanted downtime from production equipment or quality control instruments. One of the best tools to prevent unexpected downtime is the XRF machine’s on-board diagnostics and instrument health check tools.
Routinely running these checks – which typically takes a few seconds to a few minutes – and plotting the results can offer a good indication to the owner and the manufacturer regarding the overall health of the instrument and its components.
It is comforting to know that the instrument is in prime shape, and equally valuable to identify the warning signs early on that something may be going wrong.
The FT230 incorporates a number of features to help with this evaluation. The instrument comes as standard with a reference that is measured to conduct a health check, which tracks the status of vital component parts such as the X-Ray tube and detector.
There is also a daily check routine that can compare the results from calibrations over a prolonged period to see if the instrument is experiencing any drift that needs due attention, either in the form of recalibration or hardware maintenance.
The on-board diagnostics run further tests to collect additional information about the state of the instrument. All diagnostics data can be electronically transmitted to Hitachi engineers, including directly via ExTOPE Connect, Hitachi’s secure, cloud-based data management and storage solution.
This is the quickest way to communicate the data to the engineers, so they are able to review the instrument and precisely pinpoint the problem area before going on-site. This helps ensure that the suitable parts are available to the engineer and gets customers up and running as quickly as possible.
The job does not end once the FT230 has been installed; Hitachi High-Tech will work with customers throughout the instrument’s lifetime to ensure full support is available – whether that be additional training, technical support, or routine maintenance, including preventive maintenance and certification or repairs.
Hitachi’s offices in the US, UK, Germany, India, China and Japan offer first-class technical support and application development capabilities. Hitachi High-Tech also has a complimentary global team of factory-trained partners, who are also committed to providing customer satisfaction.
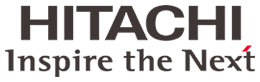
This information has been sourced, reviewed and adapted from materials provided by Hitachi High-Tech Analytical Science.
For more information on this source, please visit Hitachi High-Tech Analytical Science.