Matt Kreiner is the product manager for Hitachi High-Tech’s coatings analysis product line. In his role, he is committed to finding new solutions for Hitachi’s coatings global customer network across different industries and tackling the challenges faced in an everyday work environment. With 19 years of experience working closely with XRF technology, Kreiner has held a variety of roles across the organization.
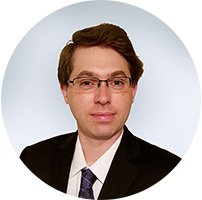
Image Credit: Hitachi High-Tech Analytical Science
His latest accomplishment has been the successful launch of the FT230, the company’s newest XRF coatings analyzer. In this interview, Kreiner discusses how he became product manager for Hitachi High Tech’s coatings instruments, how the FT230 was developed, and what potential customers really need to know about the latest innovation in the modern coatings market.
When did you begin working with coatings products?
After graduating from Northwestern University with a degree in chemical engineering, I first began working with a company that developed and manufactured XRF and electromagnetic thickness gauges; later, that division became Hitachi High-Tech Analytical Science.
One of my earliest responsibilities was testing a new temperature compensation feature for one of our XRFs for coatings analysis. It was compelling work, and I continued to learn a lot. But it was not very glamorous. There was a lack of suitable facilities for that work, so a lot of my time was spent working on equipment that was assembled in a makeshift environmental chamber – a bathroom fitted with heating and cooling equipment. Although effective at the time, I am glad to say that we have significantly improved our facilities since then.
What other roles and job positions have you held in your professional life?
I worked my way through as an applications engineer working with benchtop and handheld EDXRF, WDXRF, electromagnetic thickness gauges, optical emission (OES) and spectral reflectance. I supervised the applications lab as well as our inside sales department; as such, I was responsible for key account management and business development. I also managed our Latin American business before returning to coatings products on a full-time basis almost a decade ago.
What is it that you enjoy most about working in the coating industry?
Surprisingly, the average person is not aware of how much of the surrounding world is made up of coated materials.
I have always taken enjoyment from dismantling things and figuring out how they work and understand the interaction between individual pieces. It is incredibly satisfying and fun to be able to work with manufacturers who produce tiny and huge components that are then incorporated into products that are recognizable right away.
I get to see the intricacies in the machines, and I learn from the people running the production lines as well as the engineers who work on the development. It is an incredibly demanding industry since coated parts are necessary for mission-critical and essential devices that need to be reliable. It is great to be able to help them solve their problems.
What was the reason behind creating the FT230?
The conventional ways of using XRF for coatings are now behind us, and the FT230 offers a way to draw a line in the sand. Our customers – as well as people who utilize equipment from other providers – are seeking ways to simplify operations and enhance testing volumes.
Everyone feels the pressure of having to do more with less, and that includes manufacturing increased yields and ensuring better quality products with less staff that may not have as much expertise in XRF. There were a number of ways that we wanted to do this.
One approach included incorporating better analytical components, and we have applied that with the most sophisticated detector and signal processing technology available today. That helps, but we also discovered that the aspect of XRF testing that consumed the most time was not the actual analysis; it was the assembly of the measurement routine for the part.
Operators approach the XRF with a part that needs to be measured. They then interact with the software, which means making a lot of decisions, e.g., where to position the part, where best to take measurements from, what calibration should be applied, what working distance is safe, and what length measurement is adequate etc.
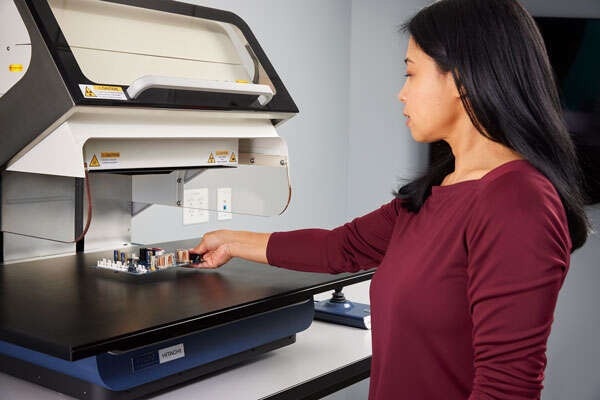
Image Credit: Hitachi High-Tech Analytical Science
We believed that if we could automate the measurement routine and limit the need to make such decisions, we could get operators on and off the XRF quicker, saving time and preventing user mistakes at each of those decision points.
How has the development of the FT230 advanced since its inception?
Prior to designing any key features, we carried out the largest voice of customer (VoC) exercise that we have ever done for a coatings project. We visited plating shops worldwide with the R&D and design team, asked questions, and listened to what users wanted and needed.
Using all of that input, in combination with the feedback that we had amassed over decades of experience in the industry, we created our vision of a product that would help resolve those wants and needs. Based in our XRF technology center in Espoo, Finland, the project team is well supported by our global team.
The team oversaw the design of the internal electronics and mechanics, how the instrument would look, and the software. Each and every aspect of the product has been tested, improved, validated with valuable user feedback, and modified to create the best user experience on the market.
What do you think the most exciting features of the FT230 are?
Personally, there have been a number of significant “Wow!” moments for me during the project development. The look and feel of the software is a radical shift from what is currently on the market today, including our own products.
The main focus has been on making operators’ lives easier and reducing the analysis path from unknown to fully quantified so production lines can be efficiently tracked and adjusted. Instead of a screen laden with cluttered controls and settings crowding the camera view and results display, the camera view is now the largest focal point of the software, followed by the results pane.
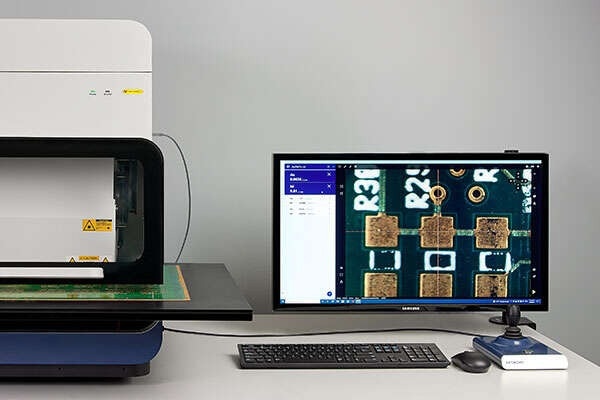
Image Credit: Hitachi High-Tech Analytical Science
The camera’s clarity is remarkable. It is aided by the adjustable, enhanced LED lighting, controlled by rings, wedge segments, or individual LEDs, and the results pane is big, sharp and easy to read. Each result card is expandable so it is able to display even more details of the measurements.
The Find My PartTM routine is an impressive feature. Using machine vision, the FT230 makes light work of setting up a measurement – the lengthiest and most challenging aspect of XRF measurement. The feedback that we have received from customers thus far has been extremely positive.
The data handling capabilities are ready to go for Industry 4.0. Results are instantly obtainable using FT Connect and can be exported in a spreadsheet or comprehensive JSON format for integration with SCADA, QMS, MES or ERP systems. Bespoke reports can also be generated for internal or external customers. Diagnostics data can be directly shared with Hitachi’s technical support team over ExTOPE Connect - Hitachi’s cloud-based solution.
Where does the FT230 fit in relative to other Hitachi coatings solutions?
Hitachi has an extensive range of XRFs for coatings analysis, such as the X-Strata920 and FT160 models, which are purpose-built for the coatings market, and our handheld X-MET8000, which is able to measure coatings and materials, including metal alloys.
In terms of feature set and pricing, the FT230 is somewhere between our basic X-Strata920 and our high-end FT160, which includes capillary optics for measuring nanometer-scale coatings on features less than 50 µm.
The FT230 is our first product that runs on new FT Connect software, so it includes a series of unique features that are not currently available on our other products. Beyond XRF, Hitachi has a line of electromagnetic gauges with the capacity to measure the thickness of paint, anodizing and PCB copper for both surface and thru-hole technologies.
What are the main reasons for choosing Hitachi for coatings analysis products?
Hitachi’s coatings products have amazing capabilities as they are reliable and easy to use. With solutions ranging from measuring simple coatings on flat parts to complex coatings on parts with varying geometry, Hitachi has products for measuring the thinnest coatings on tiny features: however, products only make up one part of the equation.
We have a global team of technical support and applications experts keen to work with our customers to help resolve any challenges as new ones come up. Our customers also value the fact that coatings analysis is one of many issues that Hitachi can address.
They will have access to all of Hitachi’s expertise and equipment – scanning electron microscopy for fundamental evaluations and failure analysis, thermal analysis equipment for physical properties testing, equipment for analyzing contaminants in plating baths and many more instruments and services.
How do you see the market developing in the near future?
Platers face the same challenges, regardless of the markets they work within. Automation or Industry 4.0 is here, and it is expanding, as is the need for 100% inspection to limit operating costs, increase production volumes, and reduce any failure rates.
The coating industry has embraced automation for a long time, but quality control testing is frequently forgotten. That will all change as the higher production speeds will not facilitate extra time for offline testing. Demand in the electronics market is exceeding supply, and that situation is expected to develop as more devices are electrified, automobiles become more autonomous, and 5G technology is fully implemented.
5G may need some essential changes to final finishes used by PCB manufacturers to enable devices to function at the higher frequency bands available to 5G. The metal finishing industry also faces pressure from environmental concerns to replace certain coatings that have long been the cornerstones of the plating industry.
What is Hitachi’s approach to supporting those changes?
The FT230 is innovative and leads the way in demonstrating the advances that we are making with our products to support the industry. We are discovering new ways to reduce total measurement times to help with 100% inspection, connect to ERP, MES, QMS and SCADA systems to be ready for integration of hardware and data, and design software that can rapidly adjust for new coating applications.
It is an exciting time to be a part of the industry, and we are excited to continue working with our partners and customers to face these challenges together.
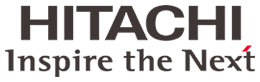
This information has been sourced, reviewed and adapted from materials provided by Hitachi High-Tech Analytical Science.
For more information on this source, please visit Hitachi High-Tech Analytical Science.