Sponsored by ELTRA GmbHReviewed by Emily MageeJul 29 2022
Coal is considered to be one of the most important fossil fuels. The global stone coal output in 2018 was approximately 7 billion metric tons.1 China, USA, Russia and India mine a huge amount of the worldwide traded stone coal.
The required sample volume for the characterization of coal varies from a few mg up to 1 gram, which - compared to the very large amount of mined coal - seems unbelievably small. For any subsequent measurement, correct sampling and sample preparation is a must. For its quality assessment and further use, the correct characterization of coal is important.
Coal is suitable for coking, steel production or electrical power generation, depending on the product quality. This article outlines the chemical background of ultimate and proximate coal analysis and how to use ELTRA’s combustion and thermogravimetric analyzers to establish their correct determination.
The most common types of coal are bituminous, lignite, and anthracite coal which can be distinguished by their distinctive physical and chemical properties. Some of the general physical parameters of coal are moisture, volatile and ash content, as well as gross calorific value. The determination of the elements carbon (C), hydrogen (H), nitrogen (N), sulfur (S) and oxygen (O) is usually what is meant by chemical analysis of coal samples.
This article summarizes all relevant standards and gives recommendations regarding suitable analytical equipment. The characterization of coal combustion products - such as ash - is discussed along with coal analysis. Sulfur content, loss on ignition value and ash fusion temperature are all aspects that can be analyzed.
Gross Calorific Value
It is difficult to name just one parameter that best describes the quality of coal, given the variety of parameters that influence coal quality. The calorific value is suitable to give a first impression of the product quality as coal is mostly used as fuel.
Table Nr. 1 displays the main types of coal, along with their calorific value and the volatile content.
Table 1. Source: ELTRA GmbH
Type |
Calorific value kj/kg |
Volatile content |
Lignite |
6,700 – 25,000 |
45 – 60 % |
Bituminous coal |
25,000 – 35,000 |
14 – 45 % |
Anthracite coal |
≥35,000 |
< 14 % |
Standard bomb calorimeters can be used to determine the gross calorific value and are described in the ISO 1928 and ASTM D5865 standard.
The two categories of calorimeters for coal analysis are adiabatic and isoperibolic. A previously dried coal sample in both types is introduced in a calorimetric bomb before oxygen is added and the coal combusted. The gross calorific value is given when the combustion heat is measured.
Analysis of Proximate Coal
Beside its calorific value, a coal sample’s ash, moisture, and volatile content are also highly relevant. These coal parameters are termed proximate coal analysis, according to ISO 17246 and ASTM D 3172.
Though they refer to different standards like ISO 562, ASTM D 3175 or ASTM D 7582, which describe the determination of one analysis parameter (e. g. volatiles) in more detail, both standards (ASTM and ISO) define proximate coal and coke analysis.
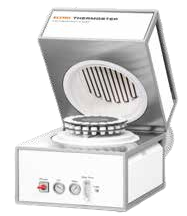
Figure 1. TGA Thermostep. Image Credit: ELTRA GmbH
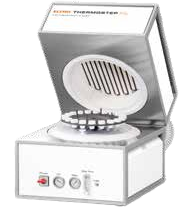
Figure 2. TGA Thermostep ML. Image Credit: ELTRA GmbH
Utilizing balances and furnaces (ISO 562) or, according to ASTM D 7582, using automated thermogravimetric analyzers like ELTRA’s TGA Thermostep (Figure 1) or TGA Thermostep ML (Figure 2), standard-compliant proximate coal analysis can be performed.
Different atmospheres, temperatures, and measuring conditions like weight stability or measurement time must be applied for the reliable and standard-compliant determination of moisture, ash and volatiles. When single furnaces and balances are used, adjusting the different settings is time-consuming as the sample always has to cool down in a desiccator, before the final weight can be measured.
Automated thermogravimetric analyzers, such as the ELTRA TGA Thermostep series, consist of a programmable furnace with integrated balance, a carousel with 19 sample positions and has the ability to measure all requested proximate coal parameters in a single run.
Users simply need to activate the application in the software, fill in a suitable sample weight (typically approx. one gram into the ceramic crucibles) and start the measurement. To measure the current weight, the carousel rotates during analysis and then places every single crucible on a weighing pedestal.
Different temperatures and atmospheres are applied depending on the analysis step during the whole measuring process. An additional empty crucible at position 20 of the carousel is measured to compensate for the thermal buoyancy for the reliable determination of the thermogravimetric parameters.
The analysis time for proximate coal analysis is significantly reduced thanks to this procedure because there is no requirement for the samples to cool down in a desiccator to ensure correct measurement. The ASTM D 7582 standard defines the settings for the automated measurement of volatiles, moisture, and ash (table 2).
Table 2. Proximate coal analysis parameter according ASTM D 7582. Source: ELTRA GmbH
Step No |
Parameter |
Temperature °C |
Atmosphere |
Additional lid
on crucible |
Stop criteria |
1 |
Moisture |
107 |
Nitrogen |
No |
Constant mass |
2 |
Volatile |
950 |
Nitrogen |
Yes |
7 minutes at 950 °C |
3 |
“Cooling down” |
600 |
Nitrogen |
Yes |
Temperature |
4 |
Ash |
750 |
Oxygen |
No |
Constant mass |
The placing of lids on the crucibles for a correct measurement of volatiles is one special setting in a thermogravimetric analyzer.
An additional lid carrousel is utilized by the ELTRA TGA Thermostep analyzer, which automatically applies the lids during measurement. Manual application and removal of lids are required by the TGA Thermostep ML configurations. The length of a complete proximate coal analysis cycle with the ELTRA TGA Thermostep takes roughly 4 hours.
Table 3 and Figure 3 show the typical results of the simultaneous measurement of 19 samples. The placing of lids on the crucibles is one special setting in a thermogravimetric analyzer.
Table 3. Typical results of the TGA Thermostep series analyzer: Dry base means that the given value takes the released amount of water into account. In comparison to a sample which is measured as received, the measured ash and volatile content is respectively higher (ISO 17247). Source: ELTRA GmbH
Sample
(Coal CRM) |
% Moisture |
% Volatile dry
base |
% Ash dry base |
% Fixed carbon
calculated |
92570-3020
(745418) |
0.16+-0.04 |
5.42+-0.14 |
0.08+-0.04 |
94.34+-0.13 |
92550-3020
(776121) |
1.12+-0.02 |
15.79+-0.16 |
20.98+-0.06 |
62.49+-0.20 |
92550-3060
(782118) |
1.82+-0.04 |
30.63+-0.11 |
23.42+-0.08 |
45.08+-0.13 |
92550-3060
(782118): 600 °C |
|
|
23.47+-0.06 |
|
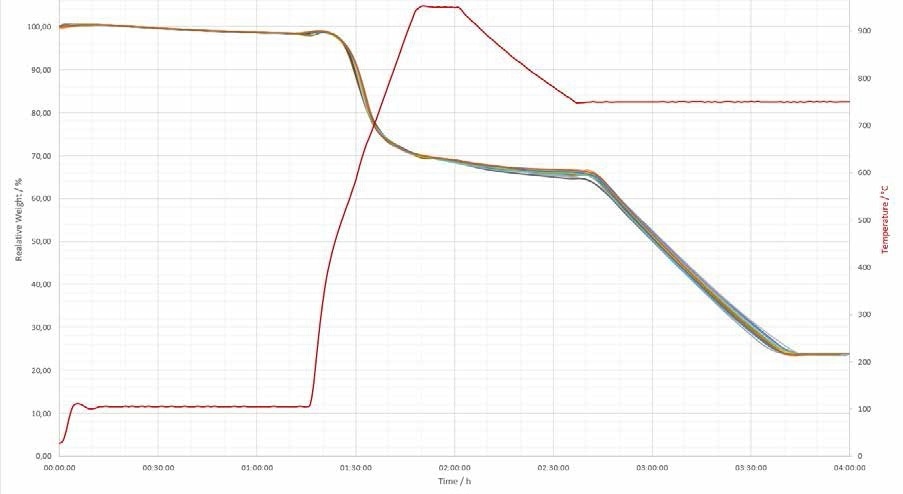
Figure 3. Typical measuring graph of ELTRA TGA Thermostep series analyzer. Image Credit: ELTRA GmbH
- y-axis (left): the sample’s relative weight
- y-axis (right): temperature
- red curve: temperature
- graph 1-19: weight loss of applied coal samples
In Table 3, the first three samples’ analyses have been processed with a 750 °C cool-down temperature. The TGA Thermostep can analyze the proximate coal parameter with this setting in a short analysis time of approximately 4 hours.
The lower standard-compliant cool-down temperature of 600 °C can also be applied in the software. Though the measuring time is prolonged by approximately one hour, the repeatability of the ash measurement is slightly improved with the application of the lower temperature.
These alternative settings do not affect moisture and ash measurement. A calculated value, the fixed carbon content of proximate coal analysis, is utilized to estimate the amount of coke that a coal sample will yield.
Through the process of subtracting the measured amount of the volatile content from the sample mass which was introduced into the ceramic crucible, the fixed carbon content can be calculated. As some volatile hydrocarbons are removed during this analysis process, the calculated fixed carbon is lower than the total carbon content.
Ultimate Coal Analysis (Chemical Analysis)
Ultimate coal analysis requires the determination of further parameters like hydrogen (H), carbon (C), sulfur (S), nitrogen (N), and oxygen (O) content in addition to proximate coal analysis. Typically, the oxygen content is measured by the difference between 100 % and the sum of all other measured values and is not measured directly.
Different types of elemental analyzers are available in the market for standard-compliant determination of the elements: C, H, N, S.
Typically, an elemental (combustion) analyzer combusts the coal sample and then measures the released combustion gas either with infrared cells, a thermal conductivity cell or a combination of the two methods. The analyzers on the market today differ based on the required sample weight, combustion temperature and measured elements.
Though micro elemental analyzers do offer the functionality to measure C, H, N, S in one analysis cycle, they only accept a very small sample weight (of max. 10 mg). Using these analyzers increases the likelihood of errors in preparation, but the standard does not prohibit their use.
In the ISO 29541 and ASTM D 5373 standards, the determination of the elements C, H, and N is regulated.
A standard-compliant common macro elemental analyzer typically employs a steel or quartz combustion tube and processes coal sample weights of around 60 - 80 mg. The applied temperature is limited to approximately 1,000-1050 °C when using these types of combustion tubes. The application of tin foils or capsules can provide the requested combustion temperature of 1150 °C.
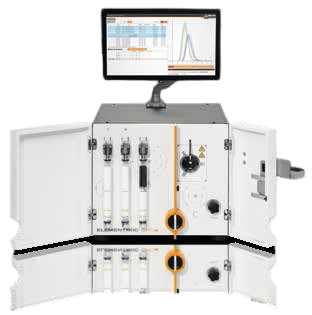
Figure 4. ELEMENTRAC CHS-r with optional monitor holder and touchscreen. Image Credit: ELTRA GmbH
A standard compliant single carbon analysis is defined in addition to the simultaneous measurement of hydrogen, carbon and nitrogen. A single carbon analysis requires combustion analyzers like ELTRA’s ELEMENTRAC CS-r or CHS-r (Figure 4), which provide a minimum combustion temperature of 1350 °C, according to ASTM D 5372 (method B).
The application of a maximum temperature of up to 1550 ° C is facilitated by the resistance-heated ceramic furnace of the CS-r or CHS-r, which assures the complete combustion of a coke or coal sample without the need to add fluxes like tin. Sulfur and hydrogen, alongside carbon, can also be measured concurrently in up to two infrared cells with the ELEMENTRAC CS-r/CHS-r.
Table 4. Typical results for coal and coke (N=10) with ELEMENTRAC CS-r & CHS-r. Source: ELTRA GmbH
Analyzer |
Sample |
Weight |
% Carbon |
% Sulfur |
% Hydrogen |
ELEMENTRAC
CHS-r |
ELTRA 92550-
3040
(Lot 781411) |
200 mg |
67.68+-0.12 |
1.91+-0.02 |
3.97+-0.02 |
ELEMENTRAC
CS-r |
Pet coke
AR 745
(Lot 745416) |
350 mg |
96.03+-0.25 |
0.9+-0.002 |
Not possible |
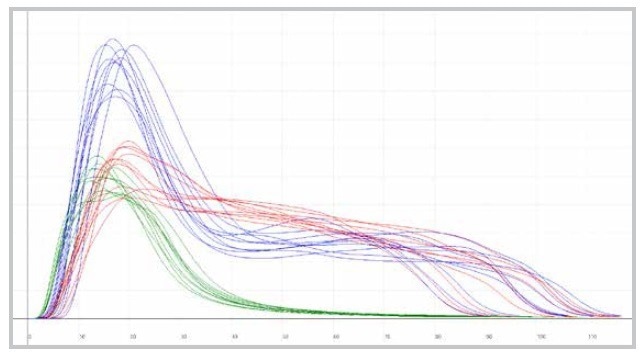
Figure 5. Measuring curve of a CHS-measurement of coal: 92550-3040(Lot 781411). Image Credit: ELTRA GmbH
- y-axis: analysis time (sec)
- y-axis: intensity (V)
- red peak: carbon
- green peak: hydrogen
- blue peak: sulfur
Characterization of Ash
Apart from the analysis of coal, the characterization of its combustion products- coal and coke ash - can be of analytical interest. The analysis of ash, as it can for coal, can be split into chemical or physical analysis.
For instance, for steam power generation, the physical ash behavior at different temperatures (ash fusion test) is very important (ASTM D 1857). Unwanted byproducts like a powder-shaped residue or a glassy slag (clinker) can arise when coal is combusted in an electrical power plant furnace.
Because of the required cost-intensive furnace cleaning, not every electrical power plant can handle clinker-forming coal. The ash is formed in the shape of a cone, pyramid or cube and is introduced into a furnace with a special window when using an ash fusion analyzer, such as the CAF Digital from Carbolite Gero. A camera can record the sample’s behavior during heating through this window.
Typically, the application of temperatures up to 1,600 °C takes place. Parameters such as deformation, hemisphere, softening and flow temperature are observed and recorded during the heating process. The flow temperature is crucial when it comes to deciding on the further use of the coal.
The loss on ignition (LOI) value of solid combustion residues (ASTM D 7348) is another physical parameter. The sample is heated from room temperature up to 950 ° C in an oxidizing atmosphere in a standard-compliant thermogravimetric analyzer like the ELTRA Thermostep.
The LOI parameter indicates whether carbon, moisture, sulfur or any other species are present in the combustion residue. The ASTM D 5016 standard regulates the dedicated sulfur analysis in combustion residues of coal and coke. A tube furnace analyzer like the ELEMENTRAC CS-r or CHS-r is suitable for correct sulfur determination as they offer the required minimum combustion temperature of 1350 °C.
Conclusion & Summary
It is challenging to establish reliable and correct analyses of coal, coke and their combustion residues. This is due to the fact that a variety of standards must be considered, and in a standard coal laboratory, different analytical equipment has to be used.
Cost-effective and reliable solutions can be provided by ELTRA for coal, coke and ash analysis, which is why ELTRA has been considered a reliable partner in the coal industry for over 40 years.
The currently valid standards for coal, coke and ash analysis are summarized in the following table, which also provides some recommendations regarding instrumentation.
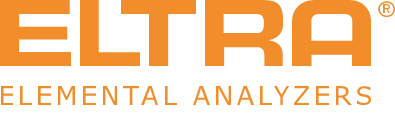
This information has been sourced, reviewed and adapted from materials provided by ELTRA GmbH.
For more information on this source, please visit ELTRA GmbH.