Sponsored by PerkinElmerReviewed by Maria OsipovaAug 30 2022
The article will outline the characterization of polybutadiene. Glass transition temperature is crucial when considering the material for various applications. The modulus and the damping properties of rubber tend to change dramatically when transitioning from the glassy to the rubbery state.
Dynamic Mechanical Analysis (DMA) can be used to show the extent of the change of both the modulus and tan δ as the material undergoes a glass transition. It will also try to pricely characterize the glass transition temperature.
One of the best techniques for examining relaxation events is DMA. The experimenter faces difficulty with clamping when the sample being tested is rubbery at room temperature, and the instrument faces difficulties when the material’s stiffness ranges from glassy to rubbery.
Samples of rubber are typically tested in either a shear or bending geometry. This article discusses single cantilever bending and how the PerkinElmer DMA 8000’s distinctive layout helps researchers get around tricky experimental problems.
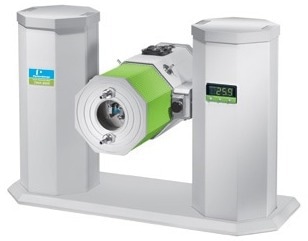
Image Credit: PerkinElmer
DMA operates by providing an oscillating force to the material and measuring the sample’s subsequent displacement. This allows for the determination of stiffness and the calculation of tan δ. Tan δ is the proportion of storage to loss in a system.
The damping qualities of the material can be ascertained by measuring the phase lag between the displacement and the applied force. Tan δ versus temperature is typically detected as a peak when the glass transition occurs, as the material will absorb energy as it goes through the glass transition.
Car tires, wiper blades, gaskets, and other products that require the capacity to deform and regain their original shape are all made with polybutadiene rubbers. The glass transition temperature is crucial for characterizing the material and evaluating how well the finished product performs.
Experimental
Multifrequency Temperature Scan of Polybutadiene
A single cantilever bending clamp was used to hold the sample while it was cooling to about –150 °C (to confirm the sample was glassy). For the oven to cool down further to –170 °C, the clamps were tightened.
Source: PerkinElmer
Equipment |
Experimental Conditions |
DMA 8000 1L Dewar |
Sample: |
Polybutadiene |
Geometry: |
Single Cantilever Bending |
Dimensions: |
7.5 (l) x 10 (w) x 2 (t) mm |
Temperature: |
-170 °C to 50 °C at 3 °C/minute-1 |
Frequency: |
0.1, 1.0 and 10.0 Hz |
Results and Conclusion
The glass transition of this material is depicted in Figure 1 as a peak in the tan δ and a decrease in storage modulus. The sample was not clamped until it reached a glassy condition, as was mentioned in the experimental portion. It keeps the clamps from spreading, thereby improving measurement accuracy.
The DMA 8000 is built such that the oven can be swiftly removed from the device to enable reclamping. This feature prevents water from condensing on the surface of the sample and keeps it from turning rubbery before the clamps is tightened.
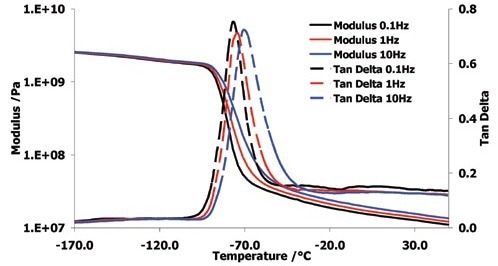
Figure 1. Glass transition of polybutadiene rubber. Image Credit: PerkinElmer
As this experiment was conducted at −170 °C (the instrument can readily cool down below –190 °C), it should be emphasized that this is an appropriate instrument for studying very low-temperature relaxation events, such as low Tgs or δ relaxations.
The data also reveals a two-order of magnitude decrease in storage modulus. This is well within the limits of the instrument and enables the DMA 8000 to evaluate studies where the stiffness of material changes significantly in a single experiment over the whole temperature range of interest.
As expected, the glass transition is demonstrated to be extremely abrupt and frequency dependent. Additionally, even after the glass transition temperature has passed, the tan response is still much above zero. This shows that this material, in its rubbery state, has strong damping qualities.
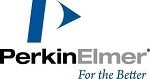
This information has been sourced, reviewed and adapted from materials provided by PerkinElmer.
For more information on this source, please visit PerkinElmer.