Any pigmented liquid or solid formulation applied to a surface in a thin layer and cured to produce a continuous solid film is considered a paint or an analogous coating. Paints are frequently used in home and commercial settings to create color or texture and preserve a surface.
There are typically five different categories of components in paints and coatings. Pigments regulate gloss, stability, and other qualities and provide color and opacity. For instance, rutile is chosen over anatase as a titanium dioxide (TiO2) pigment in white paints because of its greater refractive index, which contributes to the formulation's whiteness and opacity.
Extenders were once only used as “bulking agents” to make paint formulations less expensive, but more recently, the focus has been on their capacity to enhance qualities like corrosion resistance and gloss retention. Baryte (barium sulfate), talc (magnesium silicate), calcite (calcium carbonate), and mica are frequently used for this purpose. Optical characteristics are also imparted by extenders like dolomite (calcium magnesium carbonate), china clay (aluminum silicate), and iron oxide.
Binders are polymers, like polyurethane, acrylic, and epoxy resins, that bind the pigment particles and aid in the adhesion of the paint to the surface. The pigments and binders are transported via solvents. These can be a typical organic solvent like mineral spirits (also known as white spirit or mineral turpentine) or — more frequently — water.
Additives improve properties like formulation processing and stability, viscosity, adhesion, ease of application, drying speed, and resistance to mold growth, sagging and scuffing. These additives include dispersants, emulsifiers, surfactants, micronized waxes, silanes, and polyelectrolytes.
Even though paints and coatings have a long history, new environmental goals drive further advancements in paint formulation science. Reducing the number of organic solvents and other potentially toxic ingredients in the formulation is crucial to minimize the adverse effects of the manufacturing process and the finished product on the environment and human health.
For example, biopolymers (from plants) and recycled polymers are currently in the limelight to transition away from petrochemical-derived feedstocks.
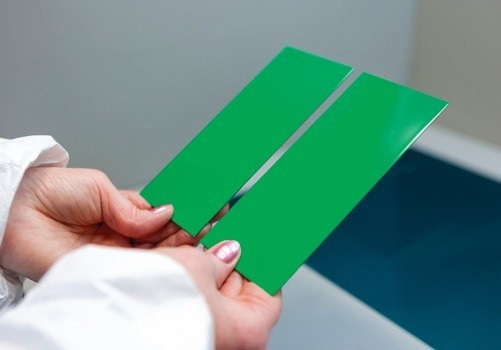
Image Credit: Malvern Panalytical
This ongoing evolution of paint manufacturing necessitates a more thorough, nanoscale understanding of all formulation components to forecast a product's qualities from its constituents and expedite problem-solving.
Such aims are not achievable using prior analytical techniques that only considered macroscopic physical characteristics like texture, film thickness, color, and viscosity. The fierce competition in the paint industry is another factor pressuring producers to switch to more automated analytical techniques instead of labor-intensive ones.
Interestingly, improvements in analytical instrumentation enable the improvement of product properties and production efficiency, as well as the acquisition of more precise and quantitative information on the microstructure and nanostructure.
This provides insights into why a formulation exhibits its properties within the framework of a streamlined workflow.
This white paper outlines some of the significant issues that paint makers must deal with and how these issues can be resolved with knowledge of specific paint component qualities.
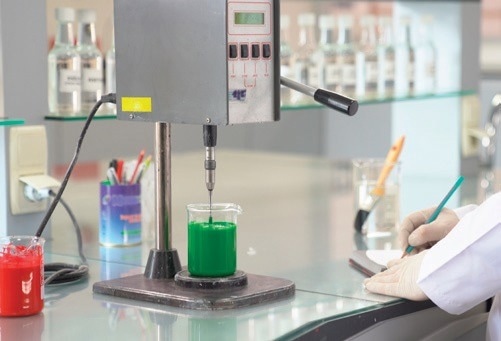
Image Credit: Malvern Panalytical
Challenges Faced by Paint Manufacturers
Confirming Chemical Purity of Raw Materials
While most paint manufacturers depend on the raw material certifications provided by their suppliers, which might not always be satisfactorily reliable and valid, it is essential to know the precise composition of the raw materials used in paint to achieve a formulation that meets the specification.
To ensure that the elemental composition adheres to a preset standard, elemental analysis using XRF is the best method for verifying the purity of paint components without using traditional “wet” chemical analysis.
This method is beneficial when, for example, working out how much titanium dioxide (TiO2) is present, confirming the makeup of pigments and extenders, looking for lead, or seeing if any essential components from component packaging have leached into the raw material during storage.
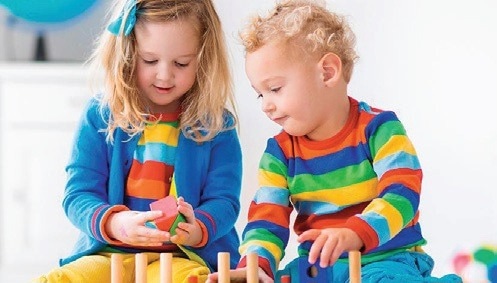
Image Credit: Malvern Panalytical
For accurate determination of pigments and extenders and a thorough understanding of their crystal phases, crystal phase analysis employing XRD is ideal. This is particularly true for TiO2, where understanding the ratio of the rutile and anatase polymorphs can help to reduce rejections (rutile has a greater refractive index and is preferred as a pigment).
Another example is iron oxide, where the various phases offer color gradations that are crucial to monitor during the grinding of pigment.
Adhering to Regulations on Lead Content
Though manufacturers make a significant effort to eliminate lead from pigments and extenders due to lead’s hazardous effects, trace amounts may still be present.
These coatings can offer a specific risk to children through routine hand-to-mouth activity when employed in goods for coating toys, furniture, playground equipment, and other items.
As of 2019, 38% of all nations, including the United States, the EU-28, India, Russia, Brazil, and China, had legally enforceable measures to prohibit the production, import, and sale of lead-containing paints to address the issue.1
These are either a cap on the overall lead concentration, the strictest of which is 90 ppm, or a set of compound-specific regulatory limitations based on managing risks caused by specific lead compounds, as outlined in the EU’s REACH legislation.
Inductively coupled plasma-mass spectrometry (ICPMS) has been used recently to do elemental analyses of lead in paint (or the raw ingredients used to make it). High-purity inert gases are needed, but the testing methods are highly laborious.
Therefore, elemental analysis utilizing XRF is gaining popularity as a substitute method that is considerably simpler and less expensive to conduct, allowing firms to quickly and thoroughly ensure that their raw materials are uncontaminated.
Optimizing Particle Size for Powder Coatings
The thermoplastic or thermosetting polymer used in powder coatings is applied electrostatically using a spray gun to a metal surface, and it is then cured to partially melt the powder. Due to their ease of use and the fact that they do not contain solvent, which has a negative influence on the environment, they are being employed more frequently in industrial applications.
The powder must be free-flowing and have a well-regulated size distribution to provide a consistent coating. Since fine particles adhere to the substrate surface more tightly, less severe curing conditions are required to create a smooth final coating.
These particles, however, have the potential to result in a poor surface finish, the “orange peel effect,” either as a result of melting too quickly during curing or “back-spray” during application due to charge buildup on the surface.
In addition to being challenging to fluidize, fine particles can potentially be explosive and, thus, a respiratory hazard.
Larger particles tend to flow better and are more manageable during application. When sprayed, their mass gives imparts a lot of straight-line inertia, which is particularly helpful for getting into the corners of an object.
Larger particles take longer to melt during curing, however, so there is a risk of partial melting and inclusions, which can compromise the look and mechanical integrity of the product.
Determining Droplet Size in Liquid Spray Paints
Various substrates are coated using liquid spray systems in the coatings business, and calculating the droplet size is a crucial component of evaluating atomization efficiency. For instance, altering the characteristics of the spray plume by adjusting elements like nozzle geometry and atomization pressure is essential for increasing the amount of paint that is transferred onto surfaces.
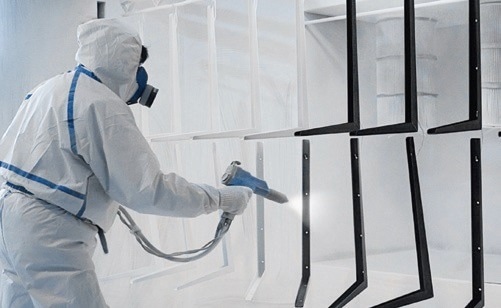
Image Credit: Malvern Panalytical
The size distribution (polydispersity) is crucial for powder coatings. For large particle-size powder coatings, having a wide size distribution is beneficial (Figure 1).
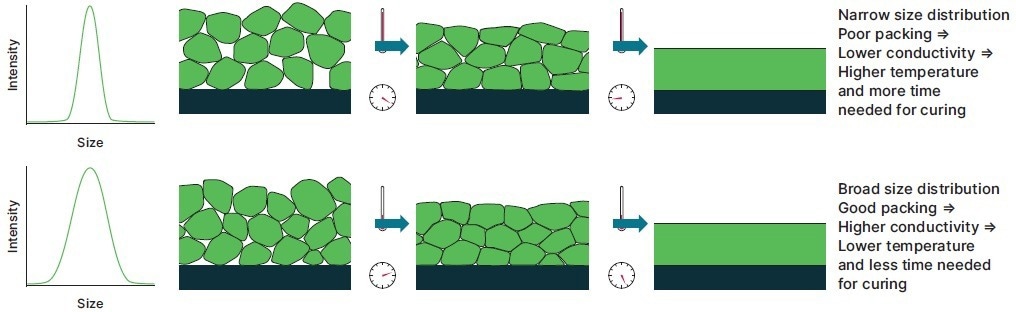
Figure 1. Ensuring that the void fraction in a powder coating is minimized can aid melt formation during curing. Image Credit: Malvern Panalytical
This is due to the fact that the smaller particles are able to fill the voids on the substrate surface, which excludes air, increasing thermal conductivity and the rate of melt formation during curing (narrow size distributions would require more severe curing conditions to avoid the formation of inclusions).
Even with a limited size range, powder coatings with small particle sizes can produce good results.
Though the industry is moving toward the smaller particles required for creating the thinner films that are currently in demand, powder coatings are often manufactured in size ranges of 5 to 100 µm.
LD particle size measuring, however, is an effective and precise method of gathering the required data, regardless of the criteria.
Sprays with a high solid content are becoming increasingly popular since they offer better coverage and have fewer handling issues with solvents. Good transfer efficiencies are required for these coatings to reduce waste and the associated costs.
Regularly analyzing sprays can be difficult for a variety of reasons.
Rapid spray events or particle size fluctuation over brief time frames may indicate subpar nozzle performance.
Particularly while transitioning from the start-up stage of atomization to equilibrium conditions, a large range of particle sizes can be formed.
The most adaptable and quick method among the different analytical techniques utilized is particle size characterization using LD.
Understanding Polymer Properties
In a coating, polymers are used to perform several different tasks. A thin polymeric layer frequently serves as the surface finish, and polymer binders are crucial to application and curing.
Polymer dispersants are additionally employed more frequently to stabilize the pigment particles to avoid flocculation and agglomeration sterically.
The molecular weight and molecular weight distribution and chain branching of the relevant polymers often have a major influence on the properties that are required, and by understanding the polymer chemistry alongside these factors, the properties of a polymer can be tailored for the necessary formulation requirement (Figure 2).
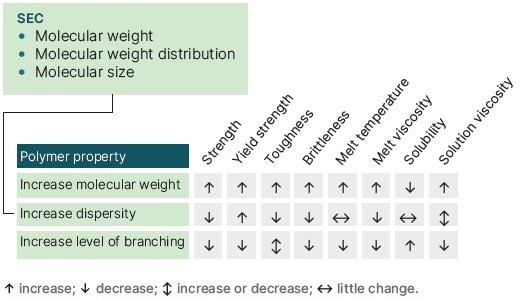
Figure 2. A range of polymer properties are influenced by its molecular weight, dispersity and related factors. Image Credit: Malvern Panalytical
It can be challenging to find the ideal polymer for a certain formulation.
Higher molecular-weight polymers, for instance, are typically linked to a more permanent protective surface when used with solvent-miscible and suspension-based paints and varnishes. Lower molecular weights may result in a higher gloss and better substrate penetration.
High-molecular-weight polymers are a challenge to incorporate into solvent-miscible goods based on alkyd polymers, like gloss paints for domestic use, because doing so causes the product’s viscosity to reach unacceptably high levels.
In this situation, introducing branched polymers can minimize the related solution viscosity for a polymer of equivalent molecular weight.
Through the determination of both absolute molecular weight and molecular weight distribution, as well as opening up the possibilities for measuring intrinsic viscosity, hydrodynamic radius, polymer branching, radius of gyration, and composition of polymers, polymer analysis using GPC/SEC can be used to understand the characteristics of components used in paint formulations.
Understanding Effects of Particle Properties on Color Performance
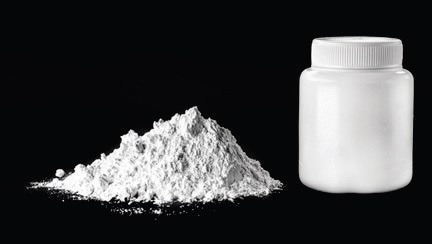
Image Credit: Malvern Panalytical
The form and size of the pigment and extender particles in a paint affect how light interacts with the final covering.
It is standard practice to fine-tune the pigment dispersion’s other parameters after adjusting the particle size to achieve maximum scattering power (Figures 3 and 4).
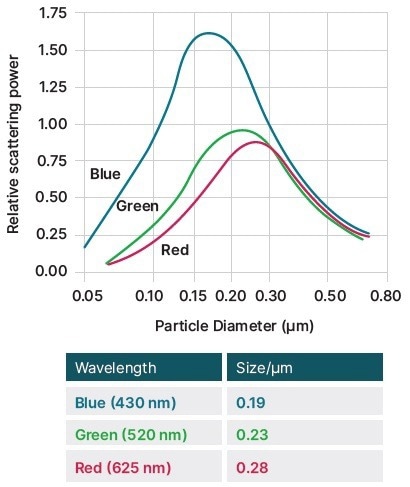
Figure 3. The effect of TiO2 particle size on scattering power, showing how smaller particles are better at scattering blue light. Image Credit: Malvern Panalytical
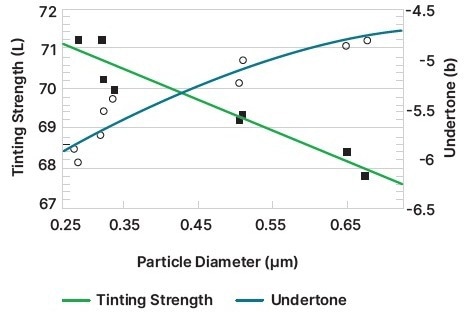
Figure 4. The effect of particle size on tint and undertone, showing how smaller particles increase the tint strength but decrease the undertone. Image Credit: Malvern Panalytical
Significant properties include:
- A pigment dispersion’s opacity, or hiding power, which measures its capacity to conceal the substrate beneath, rises relative to the scattering power when the particle size is decreased.
- The undertone establishes the tint’s color and, for smaller particles, moves to shorter, bluer frequencies.
- The tinting strength, which increases for smaller particle sizes, describes a pigment’s capacity to affect the color of dispersion, including other pigments.
A thorough understanding of crystal structure, as determined by crystal phase analysis using XRD, is necessary to strike a balance between these factors and to optimize the trade-off between high tinting strength and an acceptable hue.
Phase analysis is beneficial for various organic and inorganic pigments and is essential for figuring out the ratio of anatase and rutile in TiO2 due to their distinct refractive indices.
Since particle size affects the light transmission and milling pigments can change or destroy the crystalline phase, size analysis and XRD are a useful combination for optimizing milling. This is another clear advantage of employing LD to detect particle size.
Additionally, surface electrochemistry is crucial in these systems, particularly when water-soluble surface-active components are included.
The interactions with these soluble components and charged particles in the formulation can be examined using ELS's zeta potential measurement.
Understanding the Role of Dispersants for Dispersion Stability
Avoiding sedimentation and agglomeration is important when dispersing pigments in fluid, as large particles will rapidly settle out, but small particles can stay dispersed unless they agglomerate.
The best dispersions preserve their color and have predictable physical qualities at varying dilution levels or “thinning,” ranging from thick pastes for screen printing to quick flows for liquid sprays. Achieving the highest dispersion stability demands considerable knowledge.
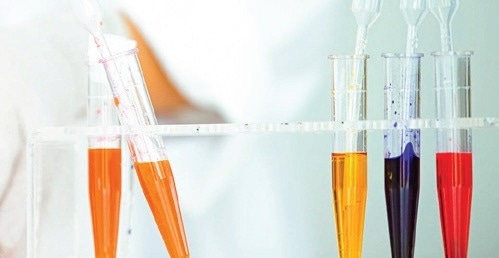
Image Credit: Malvern Panalytical
Utilizing appropriate electrolytes to regulate the liquid’s pH, agglomeration in polar solvents (like water) can be prevented by electrostatic attraction between particles in a medium (Figure 5A).
To study the electrostatic behavior of particles in dispersion and their agglomeration, zeta potential measurements using ELS and nanoparticle size measurements using DLS are used.
As an alternative, a steric polymer coating or dispersant can be used to coat a pigment with a film in non-polar solvents to stop it from attaching to nearby pigments (Figure 5B).
Such dispersants must have clearly defined molecular characteristics, such as chain length and degree of branching. Polymer analysis with GPC/SEC is a suitable tool for this.
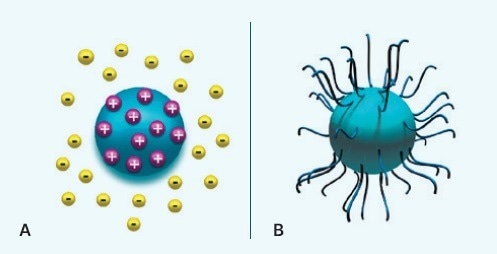
Figure 5. Preventing agglomeration of pigment particles by (A) ionically stabilizing them using a repulsive electrostatic field, or (B) sterically stabilizing them using a polymer. Image Credit: Malvern Panalytical
Understanding Effects of Particle Properties on Gloss, Weathering, and Flatting Performance
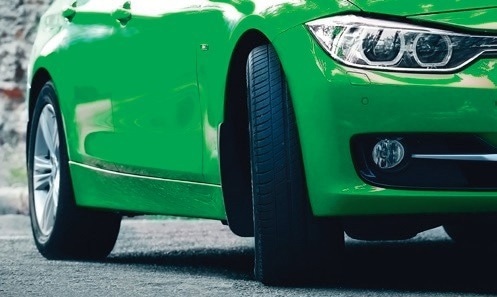
Image Credit: Malvern Panalytical
Pigment and extender particles appear to have a gloss finish and the film resistance of a painted surface.
When combined with the strong scattering power that comes with smaller particles, small particles with a narrow size distribution pack well at the film surface, producing a uniform surface finish that results in a high degree of gloss.
Contrarily, larger particles dispersed throughout a wider size distribution produce reduced scattering power and a lower gloss level.
Such poor distributions may be a feature of the utilized pigment or may be brought on by a lack of dispersion stability, which causes particle agglomeration.
Small particles with a limited size distribution also have the advantage of having a high degree of homogeneity, which makes it harder for water to penetrate and improves waterproofing properties.
Numerous applications would benefit from having such qualities (Figures 6 and 7).2
Large particles or agglomerates can be more readily shaken loose from a coating, which causes the surface to quickly lose its gloss. Small particle size also enhances a coating’s weathering properties.
For obtaining superior gloss, weathering, and flatting performance, particle size assessment using LD (or nanoparticle size measurement using DLS) is essential.
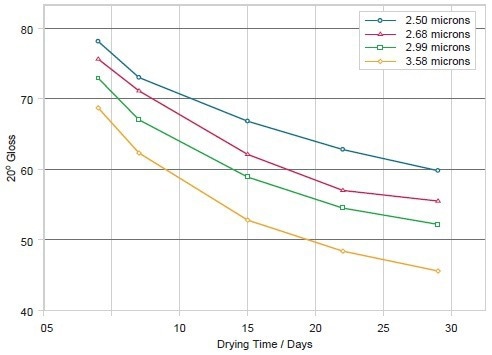
Figure 6. Gloss determined at an angle to the surface of 20° for four particle sizes of barium sulfate extender, showing how the final gloss achieved diminishes with drying time, and how larger particles result in a coating with lower gloss. Image Credit: Malvern Panalytical
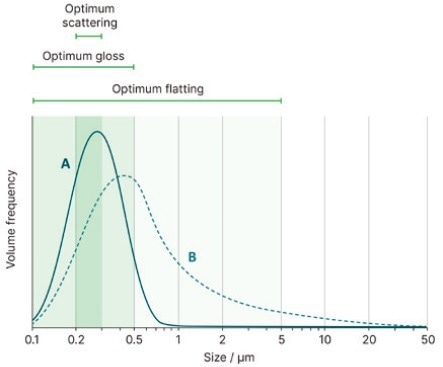
Figure 7. The effect of TiO2 particle size on scattering, gloss, and flatting performance, and how this performance might vary between a sample with a tight size distribution (sample A) and one with a broad size distribution (sample B). Image Credit: Malvern Panalytical
Surface electrochemistry can also influence particle interactions, which impacts how a coating turns out. The interactions between these soluble components and the formulation’s solid particles can be examined using zeta potential measurement utilizing ELS.
References
- Update on the Global Status of Legal Limits on Lead in Paint, September 2019, United Nations Environment Programme, 2019 https://www.unep.org/
- Watching paint dry: Relating paint gloss to the particle size of extender pigments, Malvern Panalytical, 2010, www.malvernpanalytical.com/en/learn/knowledge-center/application-notes/AN101104RelatingPaintGlossToParticleSize.html
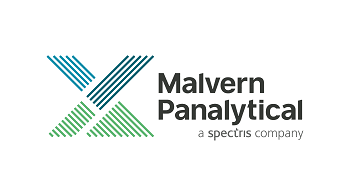
This information has been sourced, reviewed and adapted from materials provided by Malvern Panalytical.
For more information on this source, please visit Malvern Panalytical.