Gas analysis has essential applications in research, development, and industry. Gas analysis instruments are typically used to determine the concentration of known gases in an environment or atmosphere that may contain one or many gases of interest.
Effective gas analysis improves and assists laboratory and industrial applications, helping to advance key areas such as efficiency analysis, quality studies, process safety improvement, and emissions monitoring. AZoM spoke with Jay Roberts of Thermo Fisher Scientific to discuss the key applications of gas analysis, current trends, and the future of the technology.
Please, can you introduce yourself and tell us about your role at Thermo Fisher Scientific?
I am a product manager at Thermo Fisher Scientific, responsible for gas analysis applications and based in Madison, Wisconsin. I have been with the company for approximately 30 years, with most of that time spent in gas phase analysis. My educational background is in chemistry, focusing on analytical chemistry and sensors.
I work with FTIR (Fourier transform infrared) spectroscopy, a general-purpose technology that can be used to analyze various organic and inorganic compounds. Over the years, I have been exposed to many different applications for FTIR, including gas analysis.
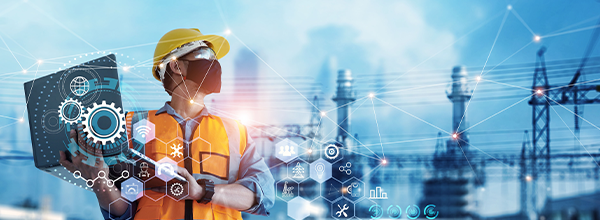
What are the key applications in laboratory and industrial gas analysis?
There are several key applications of laboratory and industrial analysis, and they can typically be organized into two primary groups: dirty and clean gases.
Dirty gases are environmental toxins or pollutants. Diesel engine exhaust, industrial smokestack emissions, or biomethane from wastewater treatment sites would fall into this category.
Over the years, we have done significant work on combustion analysis for engine exhaust from engine tailpipes. Our systems can analyze approximately 30 different components in the exhaust stream five times a second.
These same systems are also used to investigate industrial smokestacks and environmental contaminants. For example, a chemical, polymer, or petrochemical plant might be interested in studying what gases are generated in their process and then expelled from their smokestack.
Recently, there has also been increased interest in renewable energy gases. For example, biogases like methane or hydrogen sulfide are generated from the anaerobic digestion of landfills and wastewater treatment sites. Other gases of interest for renewables research include hydrogen, ammonia, or alcohol which could be useful for fuel cells or combustion.
On the clean side, the application of gas analysis would focus on the ultra-pure gases from gas supply companies; they include companies such as Air Liquide, Linde, and Air Products. These specialty gases may be used as calibration references for analyzers or used as feedstock in industrial processes.
A good example of specialty gas use would be semiconductor wafer manufacturing: ultra-precise gases are used throughout the process for doping, etching, and as clean blankets to keep particulates out. Application of gas analysis is necessary prior to use to ensure the gases are clean and not contaminated.
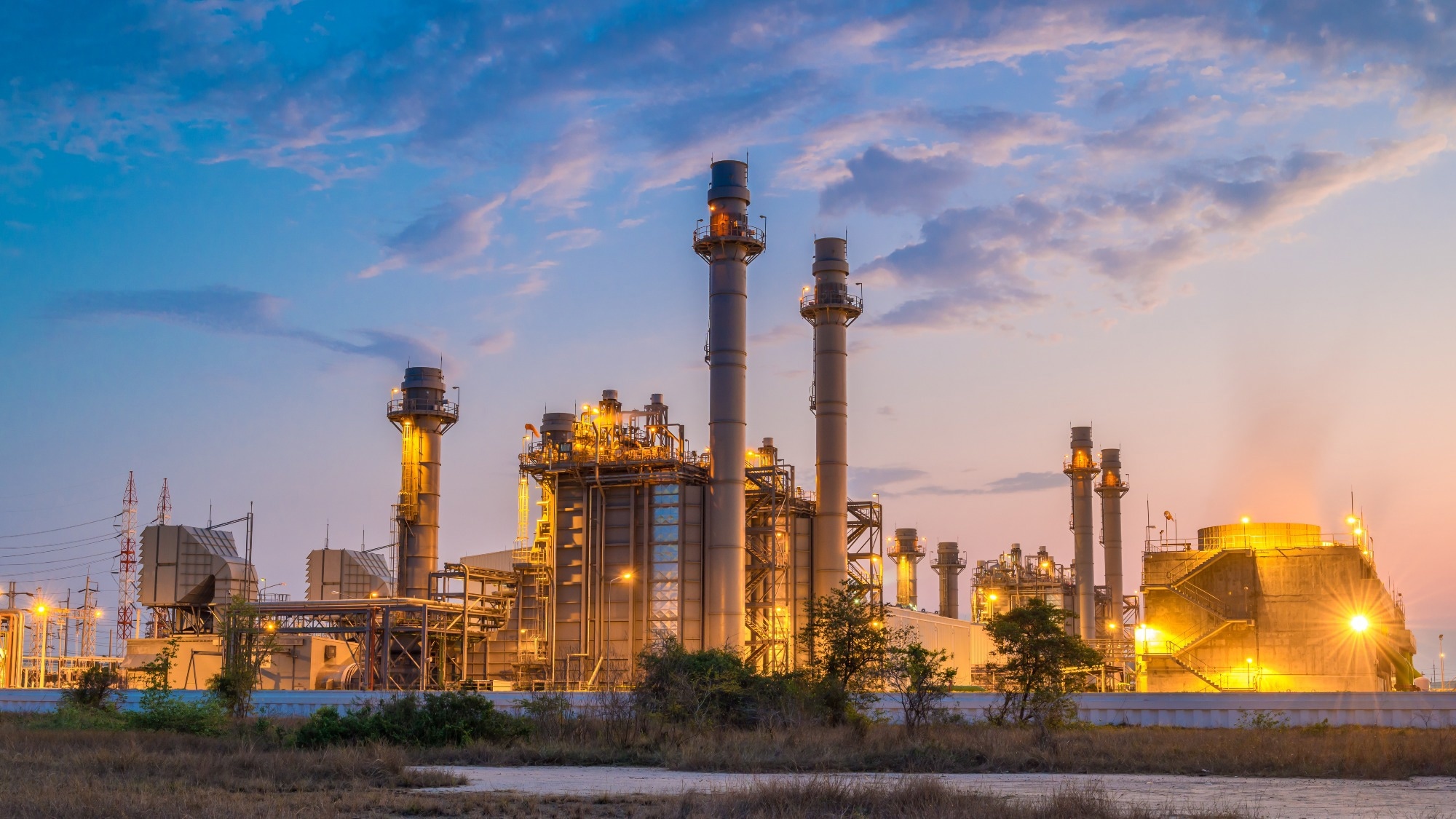
Image Credit:Shutterstock/Ha-un-an
How are most clean and dirty gases measured?
Single-component analyzers have been used over the years to measure one gas at a time. For example, non-dispersive IR technology measures CO or CO2, and chemiluminescence measures NOx or electrochemical sensors. There are a wide variety of simple diode laser sensors or electrochemical devices. These analog instruments are still valuable and widely used. Over the last five or ten years, different laser techniques have been developed, and quantum cascade laser (QCL) or cavity ring-down (CRD) lasers are becoming more prevalent in the field.
However, the application space has grown, and customers now often need to measure multiple gases simultaneously. Five (or say, eight) single-component analyzers, all requiring calibration and maintenance, are typically required to measure five (or eight) gases. That occupies a lot of resources – space, time, money, etc.
Gas chromatography (GC) and GC mass spectrometry (GC-MS) systems are widely used when multiple components are required, and they offer flexibility for different compounds at very low detection limits. Use of any GC-based system, however, generally requires sample handling and maintenance, plus carrier gases and sometimes thermal desorption tubes for samples, and then you also lose immediate response. In contrast, an FTIR system can provide results quickly, online, with minimal maintenance. The ability to analyze more than one gas within a single sample is where FTIR comes into its own: as a multi-component analyzer.
Your work today deals primarily with FTIR. Based on your experience, in which applications is FTIR gas analysis considered the most useful?
In R&D, gas analysis is generally used to develop new knowledge or understand different chemical processes.
In the laboratory, a trained chemist usually uses FTIR spectroscopy and other techniques to characterize unknown compounds. This might happen when they attempt new and different chemistry without knowing exactly what products to expect in the resulting gas. FTIR collects a broad spectrum across many frequencies, so it can identify unexpected components beyond those in the calibration set. This is a crucial advantage of FTIR.
Gas analysis of industrial emissions is another application where FTIR is very useful. Analyses of this type often take place in a chemical plant or a coal plant, where there are smokestack emissions. Industrial gas analysis with FTIR involves automated instruments that do not require a chemist. This is of particular benefit because industrial operators are often engineers rather than chemists. Also, these analyses are primarily concerned with the quantitative values generated by the FTIR analyzer. Analysis of these industrial samples usually requires knowledge of the emitted gases’ identities, because environmental regulations demand that certain gases are measured, and their emission levels must remain below certain thresholds.
In industry, processes are more automated and integrated than in a laboratory, which is more manual based on what and how the scientist decides to investigate. But FTIR can be very useful in either setting.
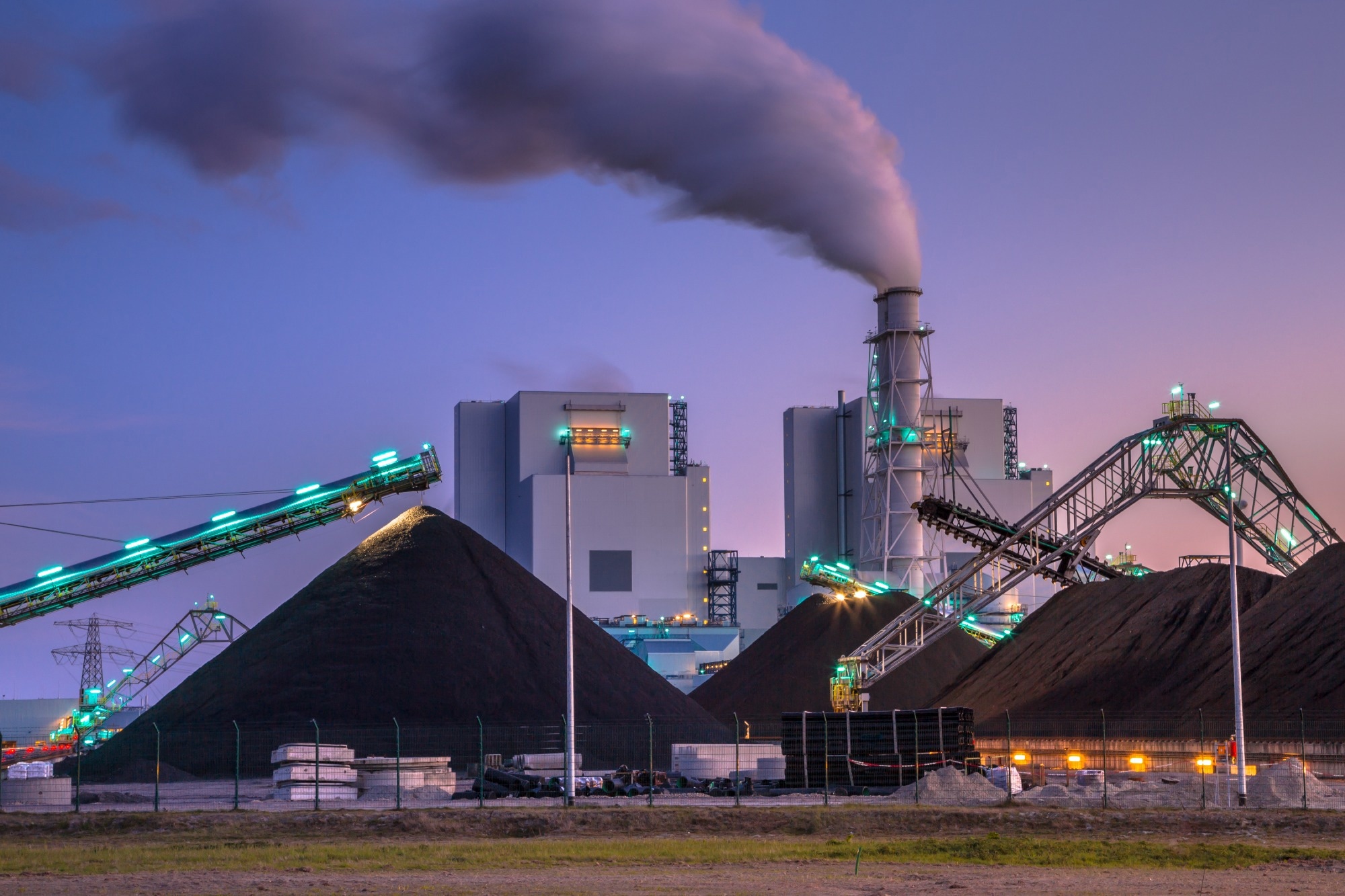
Image Credit:Shutterstock/RudmerZweaver
How does FTIR compare to other techniques?
Compared to some of the other advanced techniques, such as GC or laser techniques, FTIR is relatively easy and inexpensive. The user essentially has heated lines coming from the sample through the gas cell, and the gas flows continuously through. No other sample preparation or derivation is required.
With FTIR, the user simply hooks up a pipe and flows the gas through the gas cell, with concentration data produced at regular intervals. Some of the main strengths of FTIR for multiple components include its ease of sampling, its low maintenance, and its ability to enable automation and integration for external control.
How has FTIR gas analysis changed since Thermo Fisher entered the field?
Thermo Fisher’s FTIR division was initially a separate business called Nicolet before being purchased by Thermo Fisher, and I was part of that business. FTIR technology has since matured. When I first started, technology was handmade, and there was significant variation between systems.
Now, everything is more compact, more rugged, and more ‘push button.’ Automation and integration are becoming increasingly important, allowing the FTIR software to communicate with an external digital control system, which is either a PC-based program or a programmable logic controller (PLC).
In addition, we have a new technology that expands the sensitivity of FTIR for industrial gas analysis. It makes the technique available to a new group of users who haven’t been able to tap into the benefits of FTIR before now. With optical enhancement, the new technology can analyze specialty and bulk gases down to parts-per-billion (ppb) and in some instances even parts-per-trillion (ppt). We call it optically enhanced (OE) FTIR or ultra-sensitive FTIR, and it has the potential to really change the way many applications in industrial gas analysis have traditionally been done.
What are some of the latest advancements in gas analysis?
Analyzers like FTIR that used to be restricted to laboratories are now becoming more rugged, automated, and often less expensive. So, they are being used more frequently, and advanced metrics in industrial plants or the industrial space are the most significant recent advancement.
Another significant trend is that the chemical business, especially for gases, is going global. In the past, Europe had its own sets of regulations which were more advanced than Latin America, India, or other places. This is changing, and the world is seeing common global analysis due primarily to environmental concerns.
Gas analysis has seen increased interest in the measurement process. With more components, lower sensitivity levels, and earlier involvement with the production process, the analytical technology used — process analytical technology, or PAT — is now finding use in more varied industries across the globe.
PAT in industry gives scientists access to more information —- specifically digital information — earlier in the process, allowing them to make changes or adapt their process earlier. By comparison, in the past, they would run through an entire chemical process before sampling things at the end. A mistake or imbalance in the chemical process would not be identified until after the batch was made and would thus have to be thrown out. As a result, earlier detection is very significant, and the ability to do this is an important advancement in gas analysis.
Looking at gas analysis from a user’s perspective, what are some challenges they frequently face?
Increasingly, scientists want to measure contaminants at lower concentrations, which for some applications can be sub-part per million (ppm) and sub-ppb. That can challenge the equipment, especially in a complex mixture with various gases. Cost and complexity are still challenges in the broader use of gas analysis. Then there is the ‘hassle factor.’ Industrial GC analysis can solve several problems, but carrier gas, replacement columns, and calibrations are still required. There is also a lot of care and analyzer feeding that can be costly and time-consuming in industrial situations.
Training is still required to fully understand certain variables. Although FTIR and other systems are more intuitive, results are still not always push-button or automatic. For example, if a researcher is only measuring SO2, there may be disruptions to the process that the SO2 analyzer fails to measure. Finding trained chemists and engineers with experience to tackle such an issue is a global challenge.
How can FTIR analysis help users and clients to overcome challenges?
FTIR has several advantages for both R&D and industry. Many components can be measured with a broad spectral range to detect various compounds, contaminants, or even components not initially calibrated. The information is in the spectrum, allowing the user to return and reanalyze data as needed.
Another challenge for users is that many analyzers will provide a concentration value, and the user is stuck with it even if that value does not make sense. For instance, if the SO2 sensor provides the number ten when the user expects one, there is little recourse to discover what went wrong.
Comparatively, with FTIR’s raw spectrum and diagnostics, the user can go through the data, reanalyze, and find the interference that provided a false positive for the SO2 or maybe an unexpected gas compound. Alternatively, if the number ten was legitimate and there was an unexpected disruption in the process, FTIR can offer a significant amount of information for multiple components.
How does technology developed by Thermo Fisher Scientific help clients and users reduce time delays and potential errors?
Our ‘push button’ system can be integrated and can operate automatically in industrial plants early in the manufacturing process. Our technology enhances the PAT and identifies errors earlier on in the manufacturing process. The earlier an error, leak or contaminant can be caught, the more time and money can be saved.
The migration of instrumentation from the lab to industrial space is a continuous trend across the markets, and Thermo Fisher is involved in that. We’re actively pursuing systems with lab-level capabilities that are hardy enough to use in industrial processes.
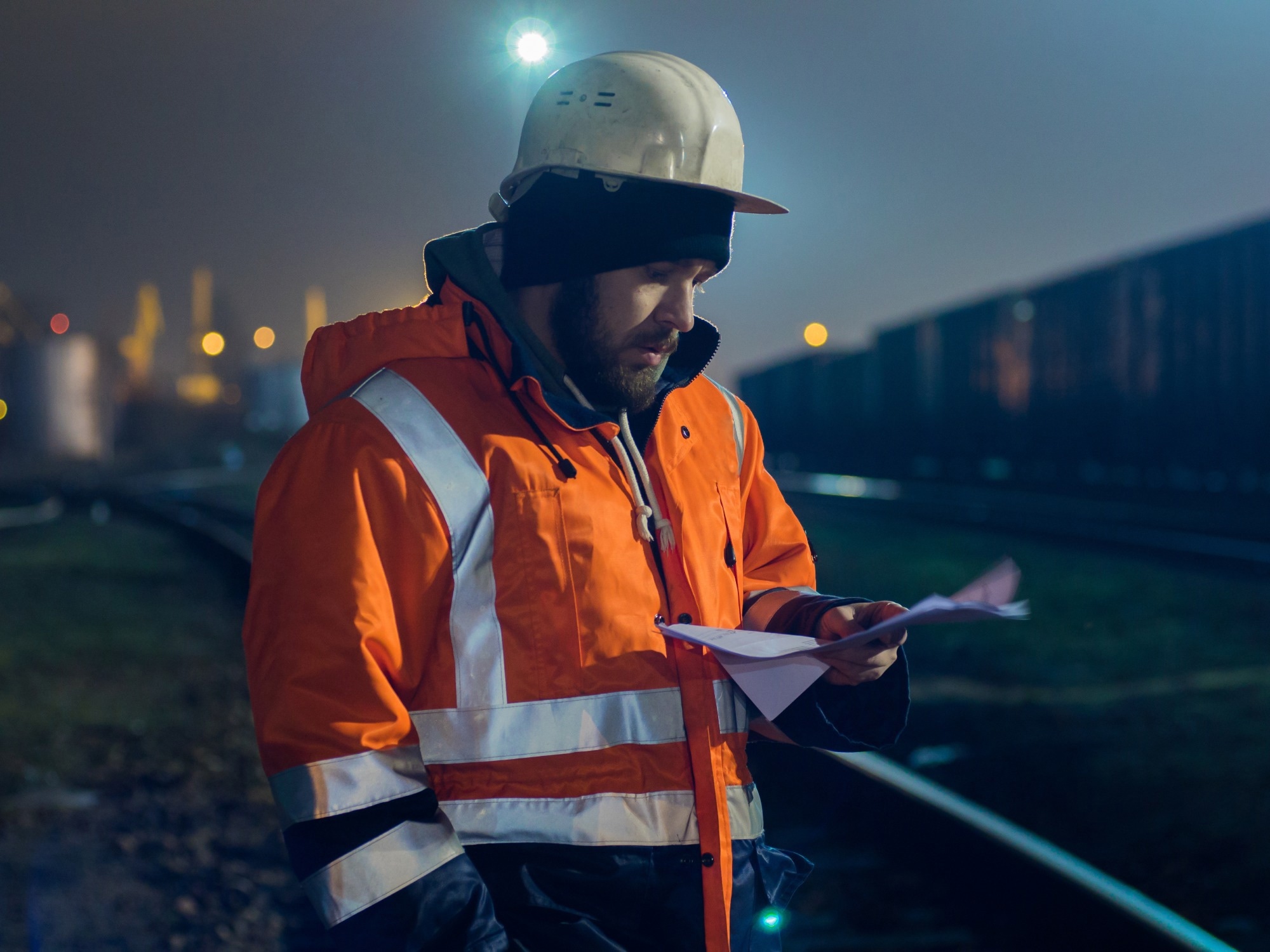
ImageCredit:Shutterstock/DmitriBunnen
You mentioned OE-FTIR or ultra-sensitive FTIR before. Why do gas analysis users need ultra-sensitive FTIR technology?
FTIR is perceived to be a comparatively less sensitive technique for some applications than others, such as GC-MS or cavity ring-down (CRD) lasers. FTIR has not been considered a match for those techniques in applications where very low detection levels are required. However, new optical and digital enhancements that our gas analysis group at Thermo Fisher has created enable FTIR to overcome certain challenges.
Sensitivity, particularly for the clean side of applications is particularly important as contaminants can hamper key processes—for example, they could clog the membranes used to create electricity from fuel cells. It’s critical to prevent such clogging, which is why extremely sensitive equipment is needed to measure the impurities in the hydrogen used in those fuel cells.
Additionally, improved sensitivity is required to keep up with needs of the ever-expanding semiconductor market and of semiconductor-dependent technologies like solar panels, smart phones, car devices, various electronics, and traditional computers. As those devices’ components get smaller — down to low-nanometer technologies — they are increasingly sensitive to contaminants or errors in processing.
That’s why the semiconductor industry is trying to obtain more precise and pure gases. As a result, getting down to sub-ppb levels for several semiconductor processing applications is essential. OE-FTIR can help ensure that gases have the necessary purity.
What sets Thermo Fisher Scientific’s gas analysis solutions apart from other instrument providers?
We are the market leader across many different disciplines. Thermo Fisher Scientific has the unique ability to understand a customer’s process and needs and help him or her address them with the best solution. While I work with FTIR technology, FTIR cannot solve all problems. That’s why our instrument portfolio also offers GCs, MS systems, liquid chromatographs (LCs), and atomic absorption (AA) spectrometers, among other systems. Across Thermo Fisher Scientific, we provide instruments, accessories, consumables, software, support, and expertise to solve our customers’ problems with coordinated solutions.
Support can make a big difference, and this is another area where Thermo Fisher Scientific shines. Most instruments cannot simply be bought, installed, and forgotten for 15+ years. Many require maintenance, training, upgrades, or other types of ongoing support. We are dedicated to providing the level of support our customers want and need.
In addition, our customers can find us easily anywhere in the world. Thermo Fisher Scientific has a global presence with direct or indirect sales, applications, and service support. That means when a user buys one of our systems, whether he or she is in New York City, Buenos Aires, or Vietnam, Thermo Fisher Scientific can provide him or her with the specific service and training needed.
What will Thermo Fisher’s role be in the future as gas analysis applications develop further?
Remember the trends we discussed already: gas analysis will become more rugged, more automated, and less expensive, with more components, enhanced sensitivity, and more information in the field.
There is also a significant interest in environmental monitoring, with an FTIR analyzer or a station set up on top of a mountain to measure greenhouse gases or environmental pollutants. This interest in monitoring carries over to industrial plants and chemical processes as they also require measuring multiple components at lower sensitivities. Thermo Fisher Scientific is dedicated to leading the development of solutions for these trends.
I referenced an example of this earlier: a quantum step forward has been made by developing an ultra-sensitive OE-FTIR analyzer. This exciting new technology improves the sensitivity of FTIR for industrial gas analysis by a factor of 25 or more, getting well below the one ppb sensitivity level for some gases; it can also measure down to ppt for some bulk gases.
Our new analyzer, called the Thermo Scientific™ MAX-iR™ FTIR Gas Analyzer, was built for automated sample handling. For example, one of the configurations can automatically sample from up to 20 different locations inside a plant to provide environmental health and safety monitoring of internal leaks or emissions.
To automatically analyze gases from multiple points, detecting from dozens to hundreds of potential chemical leaks, set off alarms, and control it all automatically is a significant step forward for FTIR analysis in industrial applications. Thermo Fisher Scientific will continue to support, develop, and improve on these applications, in the present and in the future.
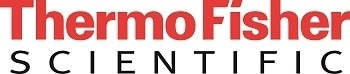
This information has been sourced, reviewed and adapted from materials provided by Thermo Fisher Scientific – Materials & Structural Analysis.
For more information on this source, please visit Thermo Fisher Scientific - FTIR Gas Analysis
Disclaimer: The views expressed here are those of the interviewee and do not necessarily represent the views of AZoM.com Limited (T/A) AZoNetwork, the owner and operator of this website. This disclaimer forms part of the Terms and Conditions of use of this website.