Granutools is a Belgian company that specializes in powder flow characterization; the University of Bolton is a British academic institute with several years of research experience in the material characterization field; CfAM is the Centre for Advanced Manufacturing, based in Bolton, UK. In this interview, Robert Higham, Head of CfAM, provides insight into AM research.
Can you provide a brief introduction to some of the projects conducted at the University of Bolton in the Additive Manufacturing field?
The University of Bolton uses AM across undergraduate and postgraduate teaching. We believe that the technology and the full value that AM can bring are only attainable with a fundamentally different approach to design, characterization, manufacturing/production, and quality assurance. It is, therefore, critical that students are exposed while they are still flexible and open-minded.
Taking AM into research is then often associated with validation and answering the what-if questions the industry often has. Specifically, we are looking at areas in powder characterization for alternative powder size fractions and rapid process development alongside static and dynamic characterization and, finally, using advanced imaging techniques to close the knowledge gap when it comes to using powder.
What is CfAM (Centre for Advanced Manufacturing) and its role in the research and industrialization of additive manufacturing?
The CfAM is a newly created entity that takes the AM capability and brings a more direct link to industry. The CfAM aspires to have the agility and scientific backbone of a rapid research and development center with a variety of capabilities to support the industrialization of advanced manufacturing.
Within AM, we are aiming to build a comprehensive technical offering from powder production and characterization, various metallic AM manufacturing capabilities with aerospace-grade testing capabilities. Under one roof and with constant monitoring and collation of data, we will then be in a strong position to support industry with science, access, and finally, with people.
The CfAM will also be an educational center in the coming years that makes use of a pedagogically unique method of development and mentoring focussed education in the field of advanced manufacturing. The industrialization of AM will therefore be supported by our equipment, knowledge, and people.
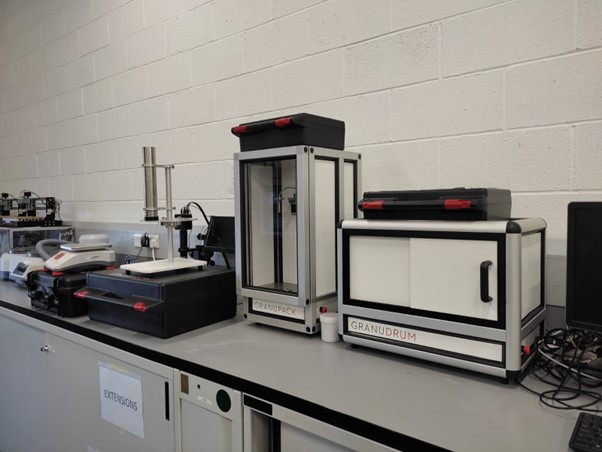
Granutools workflow for Additive Manufacturing powders, including GranuFlow, Granupack, and GranuDrum, installed in the laboratory of the Center for Advanced Manufacturing (CfAM) at Bolton University.
Image Credit: Granutools
What is the importance of powder characterization in your research?
Powder characterization, monitoring and correlation to processing are critical factors in the success of AM. Without cauterization and monitoring, we will simply be unable to support the uptake of AM.
In powder-based metallic AM, the evolution (or devolution) of powder is a well-covered topic; however, we aim to further link the processing, monitoring, and characterization of powders with a focus on developing materials for AM but also maximizing the potential value of AM.
A strong understanding and confidence in our powder before the process can save organizations significant sums of money, waste, and time.
What is, for you, the challenge with powder characterization?
Within our core offering at the Centre for Advanced Manufacturing, we believe in adapting and optimizing our processes to maximize value.
For us, value is an interesting aspect, and in many cases, industrial value is classed as confidence. Yet, confidence can often be confused with following a well-trodden path. This sense of confusion between confidence and value leads us to look closer at materials and processes that work in harmony, which we term Materials for AM (MatfAM).
As AM processing technology changes and more options become available, the dynamics of powder per technology are different, and even within technology, the powder dynamics from machine-to-machine change. The challenge, therefore, is adapting our characterization and measurement methods to suit the dynamics of our process. If we can change the method to suit, we can bring optimization processes down from weeks to days or even hours.
Our goal is to support rapid optimization to ensure the maximum value of AM is achieved, and as a result, leads to the need for rapid and lower-cost methods of analyzing powders.
Why did you choose Granutools instruments?
Representative analysis of the dynamics of powders and correlating them to our AM processes is possible with Granutools instruments. When choosing the appropriate instrument, it was also important for us to consider the time and cost involved.
Our Granutools lab setup allows a full flowability and cohesivity analysis to be undertaken in minutes, and our lab costs a fraction of a “traditional” powder characterization lab.
Granutools is a key enabler in meeting our aims as an organization. It adds value to our work while we continue to build full AM process data. There are not many purchases you can make in AM, which add significantly more value with each use, but in this case, we believe Granutools instruments do just that.
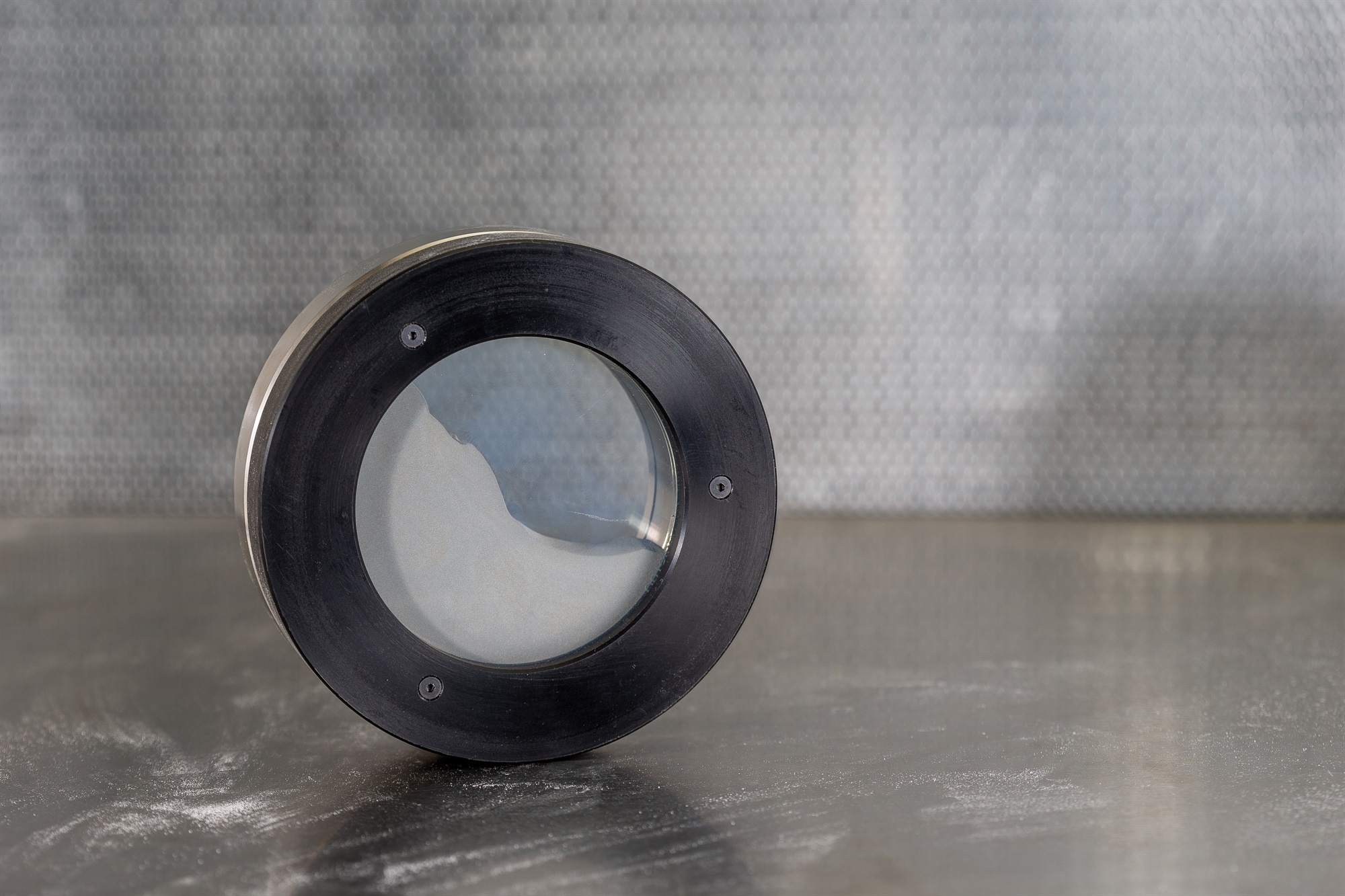
Cell of the GranuDrum instrument.
Image Credit: Granutools
What are the next steps, plans, and challenges in your research, e.g., regarding the industrialization of additive manufacturing?
By now, it may seem obvious that the value in Granutools seems strongest when linked to a process. But the question that is quite often asked is, what about users who do not have the time or finances to do this R&D? CfAM exists in the hoe to help answer this question.
If AM is to win and support the value that many users see and many potential users can imagine, we need to support each other as AM users. The CfAM strategy is a springboard for supporting growth by answering questions for and with you.
AM is complex and calls on a strong and broad skillset. Our commercial aim is not part sales or machine sales, but if we meet our mission to support AM growth, we will win by supporting companies with their research, recruitment, and growth.
In turn, more students and companies will want to support us, and our growth will become indicative of the sector's uptake in AM - all while our core ethos of support remains the same.
We will support AM value by investing in and analyzing emerging technology across the AM value chain, which in turn, will bring more opportunities for our students to grow and instigate change when they go into industry following their studies.
In the immediate future, we will be using Granutools, new materials, new size fractions, and rapid characterization of parts from powder bed fusion to look for additional methods and ways of adding value, in this case, bringing down the cost for entry-level AM users. Low cost does not mean low quality, and Granutools will enable that project.
About Robert Higham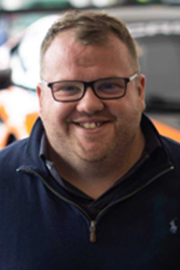
Robert Higham has worked across motorsport, space, and aerospace. Robert was responsible for the qualification of materials, processes, and parts produced by additive manufacturing, most recently for Airbus, before joining the University of Bolton 5 years ago. Robert has created an AM capability at Bolton and integrated it into various parts of students’ educational journeys. The newly launched Centre for Advanced Manufacturing was strategically supported by the university following Robert’s analysis of the market and where a gap in the provision of people and technological access could be supported.

This information has been sourced, reviewed and adapted from materials provided by Granutools.
For more information on this source, please visit Granutools.
Disclaimer: The views expressed here are those of the interviewee and do not necessarily represent the views of AZoM.com Limited (T/A) AZoNetwork, the owner and operator of this website. This disclaimer forms part of the Terms and Conditions of use of this website.