From defense and solar system research to boats and aircraft, radome structures play a vital role when it comes to protecting radar equipment. These weatherproof shells are transparent to radio frequency systems, such as radar, microwave, and other antennae, and are utilized for signal transmission and capture without interfering with the signal traveling through them.
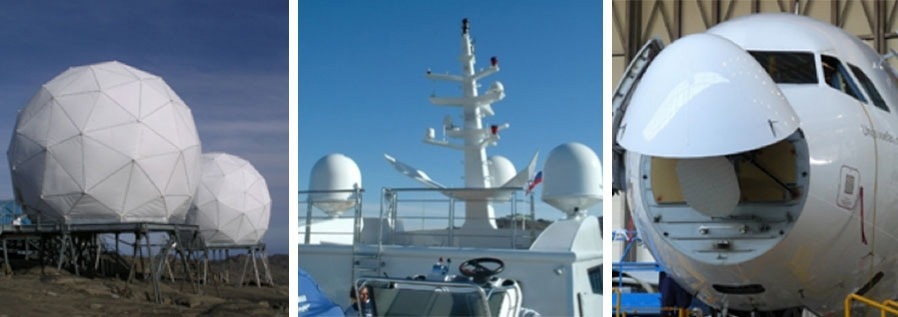
Image Credit: General Plastics Manufacturing
Although the term “radome” is a combination of “radar” and “dome,” these protective structures are not typically dome-shaped and exist in a variety of shapes, including flat panels that are designed to protect sensitive antenna components on big dishes and compact radar systems that are used in naval applications.
Polyurethane foams from General Plastics are commonly utilized as composite materials and have dielectric properties for the construction of radomes and related housings.
They act as an optimum insulator between sensitive electronics used in communication, telemetry, and radar systems and environmental threats posed by rain, wind, hail, snow, sand, insects, bird strikes, UV damage, and fast temperature variations.
Wide-Ranging Radome Applications
- Security/Military/Defense: Radomes shield and obstruct electronic surveillance tools, such as those used to intercept satellite communications and for various radar air defense uses. They provide support to military aircraft platforms for reconnaissance, electronic warfare, defense, and preemptive strikes, as well as data links and electronic countermeasures.
- Stationary Antennae: Radomes prevent debris, ice, and freezing rain from forming directly on the metal surface.
- Commercial Aircraft: Commercial flights rely on signals for navigation or communication. Radomes utilized in aircraft nose constructions ensure optimal antenna functioning for weather detection.
- Maritime Satellite Communications: Radomes are used on ships to safeguard dish antennae that are used to continuously track fixed satellites and for navigation.
- Broadband Communications: On oil tankers and large cruise ships, radomes with diameters greater than 3 m may cover antennae that connect to voice, data television, and Internet transmissions.
- Private Yachts: For voice and low-speed data, small private yachts may use radomes as small as 26 cm in diameter.
- Solar System Research: NASA employs enormous radar dishes in remote, uninhabited places with low signal pollution.
Why Polyurethane Foams are Optimal for Constructing Effective Barriers
Radomes constructed with appropriate materials and appropriately configured for the application and radio frequency range are virtually undetectable electronically, preventing any detrimental impact on the performance of the signals produced or captured.
Polyurethane foams are versatile, strong, and cost-effective, with good performance and low dielectric interference, as well as excellent dimensional stability. As these foam materials are closed-cell and hydrophobic (they do not absorb water), they do not alter over time. Water is highly polar, which can cause them to lose their properties or change over time.
Furthermore, in extremely cold and windy environments, foam structures surrounding radar dishes prevent snow and wind from moving them around. Additionally, as a natural insulator, the foam material inhibits cold and heat from transmitting, reducing potentially hazardous temperature swings.
An unprotected antenna in bright sunlight, for example, might quickly heat up during the transition from night to day, endangering performance and longevity.
Radomes are often built utilizing layup or prepreg processes, in which resin-reinforced laminate materials are easily bonded to low- or medium-density rigid polyurethane foams. Polyurethane foams are already well-known for their ability to sustain composite constructions due to their excellent strength-to-weight ratio.
Selection Considerations
All of General Plastics’ foam materials have unique properties and benefits that help determine their application. The low dielectric constant and low loss tangent of certain General Plastics foam make it suited for radome applications.
Material selection may also depend on the shape or contours of the sensitive electronics being covered and how imperative it is to protect them. The LAST-A-FOAM® FR-3700 Performance Core series and FR-7100 Multi-Use Core series polyurethane foams are ideally suited for these applications.
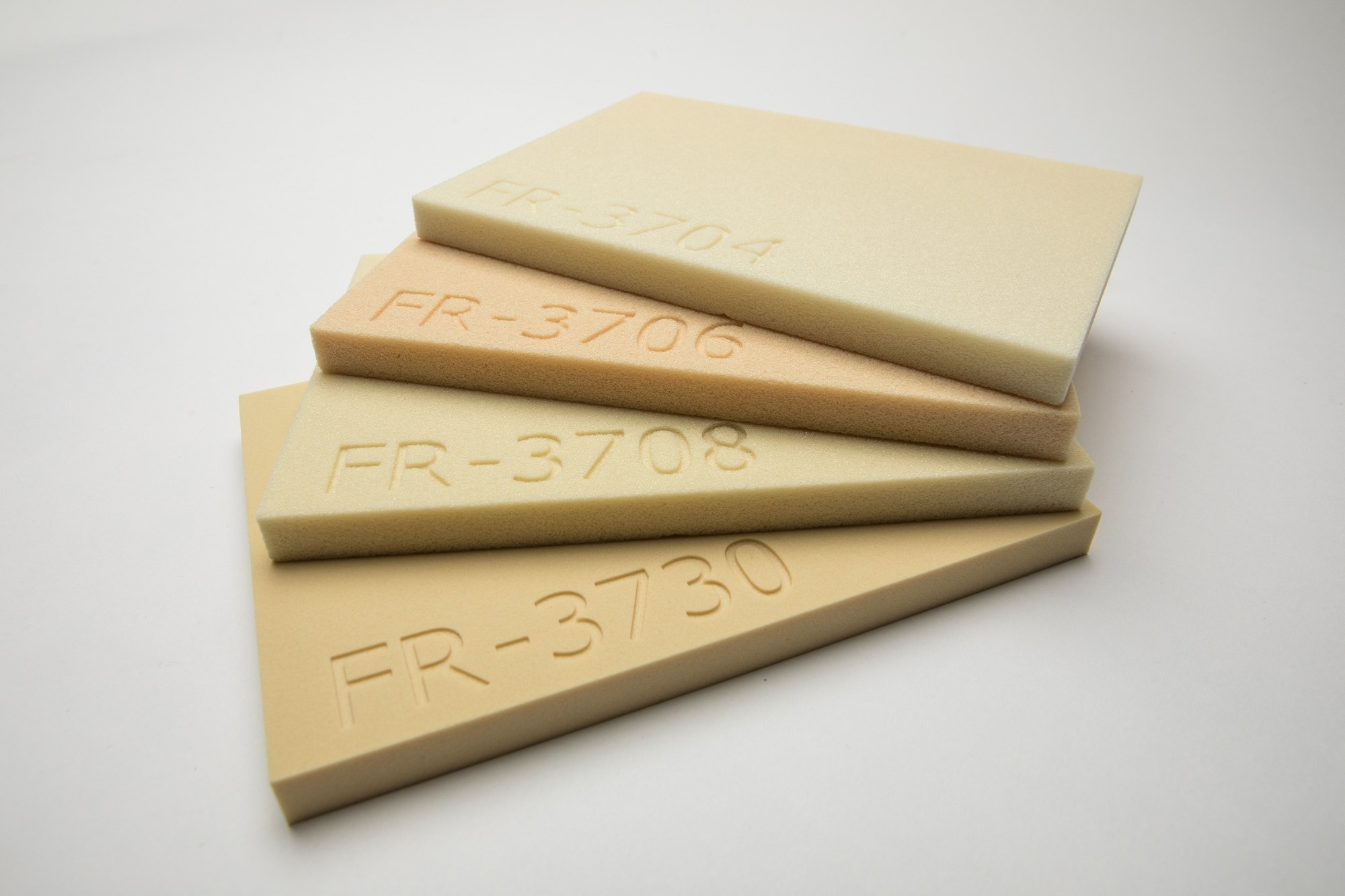
Image Credit: General Plastics Manufacturing
LAST-A-FOAM® FR-3700 has been specifically built to be tougher and more durable than the FR-7100. The FR-3700 can withstand harsh environments with a high density, such as those required for military and defense applications requiring the greatest levels of protection.
This flame-retardant performance core series is an excellent alternative to wood, is resistant to most chemicals and solvents, and has a high strength-to-weight ratio.
Although not as robust as the FR-3700, the LAST-A-FOAM® FR-7100 is adequate and less expensive for lower-risk applications.
Other advantages of this multi-purpose core series include its fine cell structure, which allows for smooth finishes, dimensional stability, and closed-cell structure, which does not absorb water or moisture. The FR-7100 is best suited for applications with greater variety or lower performance needs.
Larger radomes usually have less stringent exposure needs. A very large radome in Alaska, for example, simply needs to withstand wind and possibly hail, whereas a naval ship or a weaponized system will require a stronger, more significant composite to safeguard that radar system from loss. This is also influenced by foam formulation and density, which drive material properties.
Proven Capabilities
Testing that has been carried out on General Plastics’ distinctive LAST-A-FOAM® materials reveals how the foams functioned well across a wide variety of microwave frequencies without considerable heat loss.
The products have been proven to be resistant to moisture and virtually transparent to radio signals, making them the preferred choice for safeguarding aerospace, marine, and land-based microwave antennae.
The polyurethane foams are available in three forms: (1) as sheet stock that can be further customized to fit the demands of the customer, (2) machined to shape based on a supplied drawing with dimensions stated, and (3) as a molded part. Furthermore, for particular applications, General Plastics delivers material that has been cast to a specific shape.
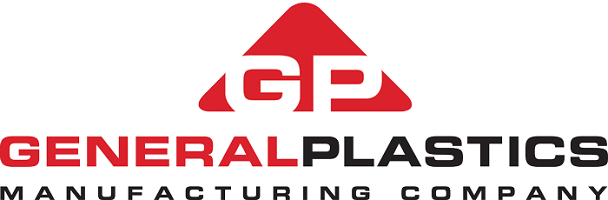
This information has been sourced, reviewed and adapted from materials provided by General Plastics Manufacturing.
For more information on this source, please visit General Plastics Manufacturing.