Detecting and measuring gravitational waves requires the use of extremely sensitive instruments.
Laser interferometry was pioneered in the 1970s by American physicist Rainer Weiss. This technique uses lasers to detect gravitational waves. Extensive research in recent decades has produced extremely advanced interferometric techniques, giving scientists the tools to observe previously elusive phenomena.
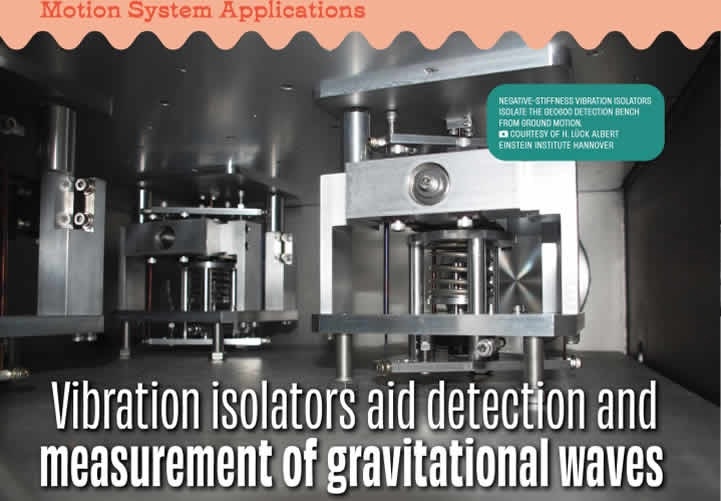
Image Credit: Einstein Institute Hannover
With laser interferometry we can retrieve information from spaces in the universe that are otherwise not accessible, and we can look back in time much further.
Dr. Harald Lück, Max Planck Institute in Gravitational Physics, Hannover, Germany.
Dr. Lück’s division operates the GEO600 gravitational wave detector in conjunction with colleagues from the UK and Leibniz Universität Hannover. Funded by the Max Planck Society and the Science and Technology Facilities Council, the project is a ground-based interferometric gravitational wave detector.
Located near Hanover, the project uses a laser interferometer to directly detect gravitational waves.
Scientists at GEO600 have provided innovative, cutting-edge research in the field of interferometry and interferometry-related technologies, encompassing areas such as laser stabilization, control engineering, absorption-free optics, vibration damping, and data acquisition and processing.
A central innovation in the GEO600 project is the use of squeezed laser light to enhance the detector’s sensitivity. Indeed, it is the first gravitational wave detector to utilize this technology.
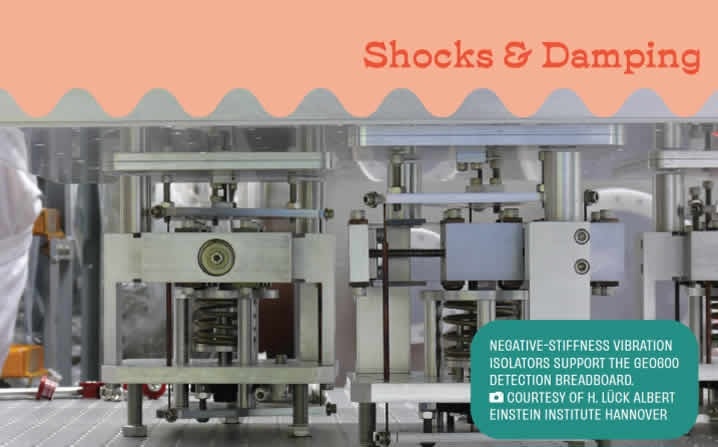
Image Credit: Einstein Institute Hannover
“GEO600 is also the first gravitational wave detector that uses squeezed laser light to improve sensitivity,” said Dr. Lück.
“Squeezed states are of high interest since they show a squeezed uncertainty which can be used to improve the sensitivity of measurement devices beyond the usual quantum noise limits.”
“The quantum nature of light has an influence at all frequencies, but at about 1,000 to 4,000 Hz – where signals from supernovae and the birth of neutron stars are expected – quantum noise dominates at these higher frequencies. Hence, it is at high frequencies where we currently benefit from squeezing the most.”
“Individual photons will hit the detector at an uneven rate,” explained Lück. “Because of quantum fluctuations, these photons will show up as a fluctuating background signal that could completely obscure the expected short gravitational wave signal from the event itself.”
“GEO scientists have managed to tame unwanted signal noise by manipulating the fluctuations, so as to produce this squeezed light. Both LIGO and Virgo now use squeezed light. Virgo uses a squeezed light source built and operated by GEO, while LIGO uses a squeezed light of its own design,” said Dr. Lück
The increased sensitivity of the LIGO detectors is based on multiple technologies developed and tested at GEO600.
Shielding Optics from Terrestrial Vibrations
Multiple types of seismic vibrations or environmental disturbances, such as temperature and air pressure fluctuations, can hinder signal detection, potentially concealing the signal completely. Designing equipment that prevents this issue is a significant challenge in gravitational wave interferometry.
“The central elements in all gravitational wave detectors are mirrors,” said Dr. Lück. “The GEO600 mirrors, which are used to direct the laser beams, weigh about 6 kg. These mirrors are suspended as triple pendulums, so that they’re isolated from various disturbances.”
“Thin threads made of quartz glass – fused silica fibers – are bonded directly onto the mirrors and a second pendulum mass, which means there is no friction at the point of contact. This increases the overall sensitivity of GEO600 through reduced mechanical loss.”
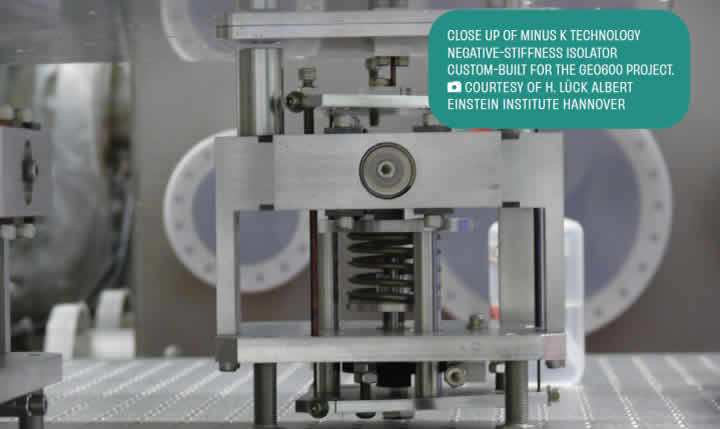
Image Credit: Einstein Institute Hannover
The entire assembly is enclosed within a vacuum chamber. The equipment includes a detection bench, carrying mode matching optics, output mode cleaner, Faraday isolator, and a photodiode situated on a breadboard. This sits upon three negative-stiffness vibration isolators, which isolate the entire system from ground motion.
The selection of appropriate vibration isolator technology was given key attention during the design of the GEO600 gravitational wave detectors. Low-frequency range measurements below 100 Hz are particularly vulnerable to seismic disturbances.
“We selected Negative-Stiffness vibration isolators because they are very simple to use, compact, and operate without the need for compressed air or electronic cabling,” explained Dr. Lück. “In a vacuum we try to minimize connecting cable components.”
"These isolators are not only more vacuum compatible, they are more reliable than air tables or active systems. They isolate very well from the outside world.”
Negative-Stiffness Vibration Isolation
Negative-Stiffness vibration isolation technology was developed by Minus K Technology. These types of vibration isolators are compact and do not require electricity or compressed air, which enables sensitive instruments to be located in any laboratory or production facility in the world.
No motors, pumps, or chambers are used in these isolators, and they operate in a purely passive mechanical mode. This means that there is no need for maintenance, as there are no parts that can wear out.
Negative-Stiffness isolators have one big advantage: they can achieve a high level of isolation in multiple directions. These isolators are adjustable, resonant frequencies can be custom tailored to 0.5 Hz both horizontally and vertically. Some versions can achieve horizontal resonant frequency tailoring to 1.5 Hz.
For an isolation system with a 0.5 Hz natural frequency, isolation begins at 0.7 Hz and improves with increased vibration frequency. The natural frequency is more commonly used to describe the system's performance.
How a Negative-Stiffness Vibration Isolator Works
Vertical-motion isolation is provided by a stiff spring that supports a weight load, combined with a Negative-Stiffness mechanism.
The net vertical stiffness is made low without affecting the static load-supporting capability of the spring. Beam-columns connected in series with the vertical-motion isolator provide horizontal-motion isolation. A beam column behaves as a spring combined with a negative-stiffness mechanism.
The result is a compact passive isolator capable of low vertical and horizontal natural frequencies and high internal structural frequencies.
Dr. David Platus, Inventor of Negative-Stiffness Isolators, and President and Founder, Minus K Technology.
Negative-Stiffness isolators deliver high performance, which can be measured by a transmissibility curve. Vibration transmissibility is a measure of the vibrations that are transmitted through the isolator relative to the input vibrations.
Negative-Stiffness isolators, when adjusted to 0.5 Hz, achieve approximately 93% isolation efficiency at 2 Hz, 99% at 5 Hz, and 99.7% at 10 Hz.
“One issue with our systems that we use is the suppression of the resonance,” added Dr. Lück. “And here, the Negative-Stiffness isolators turn what is usually considered a disadvantage into an advantage.”
“If you build a low-frequency suspension system then you typically find that the mechanical Q values go down and the dissipation goes up. I think that is what the Minus K isolators use for keeping the resonance peak low enough, and that is a neat use of turning this seeming disadvantage into an advantage.”
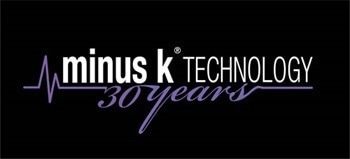
This information has been sourced, reviewed, and adapted from materials provided by Minus K Technology.
For more information on this source, please visit Minus K Technology.