Complementary metal oxide (CMOS) detectors have revolutionized spark optical emission spectrometer (OES) analysis.
This technology offers an alternative to the photomultiplier tube (PMT), a fully semiconductor-based apparatus employed in some metal analyzers for high-end analysis. In several OES applications, CMOS technology is the preferred option for various reasons.
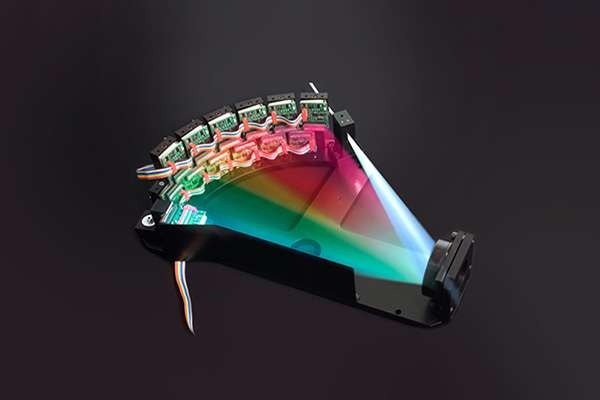
Image Credit: Hitachi High-Tech Analytical Science
This article will outline four compelling reasons why users should consider switching to CMOS-based spark spectrometers.
1. You Do Not Have the Capital for a Top of the Range OES Instrument
Investing in optical emission spectrometers is a significant decision. Historically, advanced instruments have utilized several photomultiplier tubes to detect various elements across a broad range of optical wavelengths.
The high cost of these PMTs results in expensive instruments. However, CMOS-detector alternative instruments have made it possible to achieve a broader range of elements and wavelengths at a significantly lower cost.
2. You Need to Analyze a Wide Range of Elements
Although PMT detectors are excellent at measuring ultra-low levels of specific elements, they have limitations. Each detector is optimized for a few wavelengths of incident light, resulting in limited results for a few elements.
If a broader range of tramp and trace elements in various materials needs to be measured, investing in an instrument with multiple detectors can quickly become costly (as noted in point 1).
A CMOS-based detector, on the other hand, can measure a much wider range of the optical spectrum, enabling the detection of more elements within the samples.
3. You Anticipate Branching into New Areas of Metals Production
New alloy development is an active field today, with continuous efforts to develop high-strength, lightweight materials to increase fuel economy and medical devices that the body can accept after implantation. As new material specifications and customer demands regularly emerge, selecting the appropriate OES instrument is crucial.
If an OES instrument with PMT detectors optimized for the current application is chosen, it may become obsolete when new applications arise. In contrast, opting for CMOS-based instruments allows the user to keep their options open in the future.
4. You Need to Keep Costs Low to Protect Margins
Foundries and metal production and fabrication facilities incur high running costs, with the added challenge of price fluctuations in raw and recycled feedstock materials due to market variations. To keep all other costs as low and predictable as possible, foundries are under constant pressure.
Compared to their PMT counterparts, CMOS-based OES instruments require less power to operate, resulting in lower operating costs.
The OE Series of OES spark spectrometers, specifically, further reduce power consumption on the vacuum pump and the quantity of argon required during analysis, providing even greater cost savings.
The Importance of Detection Limits
In certain scenarios, PMT-based detectors are still necessary for analysis requiring detection limits below the capabilities of CMOS detectors.
For OE Series that utilizes a CMOS-based detection system, Hitachi publishes articles containing tables of detection limits for various base alloys, such as iron and steel. These notes showcase the exceedingly low detection limits achievable.
However, selecting the most appropriate detector technology for a specific application is critical, and PMT detectors may still be required if detection limits dictate.
Hitachi’s OE Series
Hitachi’s OE Series of optical emission spectrometers merges the broad range and sensitivity of CMOS-based detectors with a novel optical design, resulting in performance levels typically only attainable with significantly more expensive instruments.
With its compact size and low operating costs, the OE Series is capable of detecting the entire spectrum of elements within metals, including gases, with the OE750 model.

This information has been sourced, reviewed and adapted from materials provided by Hitachi High-Tech Analytical Science.
For more information on this source, please visit Hitachi High-Tech Analytical Science.