This article discusses the impact of heat treatment on the development of the microstructure and corrosion resistance of weldments made of 2205 duplex stainless steel (DSS). It also provides an overview of the properties and applications of DSS.
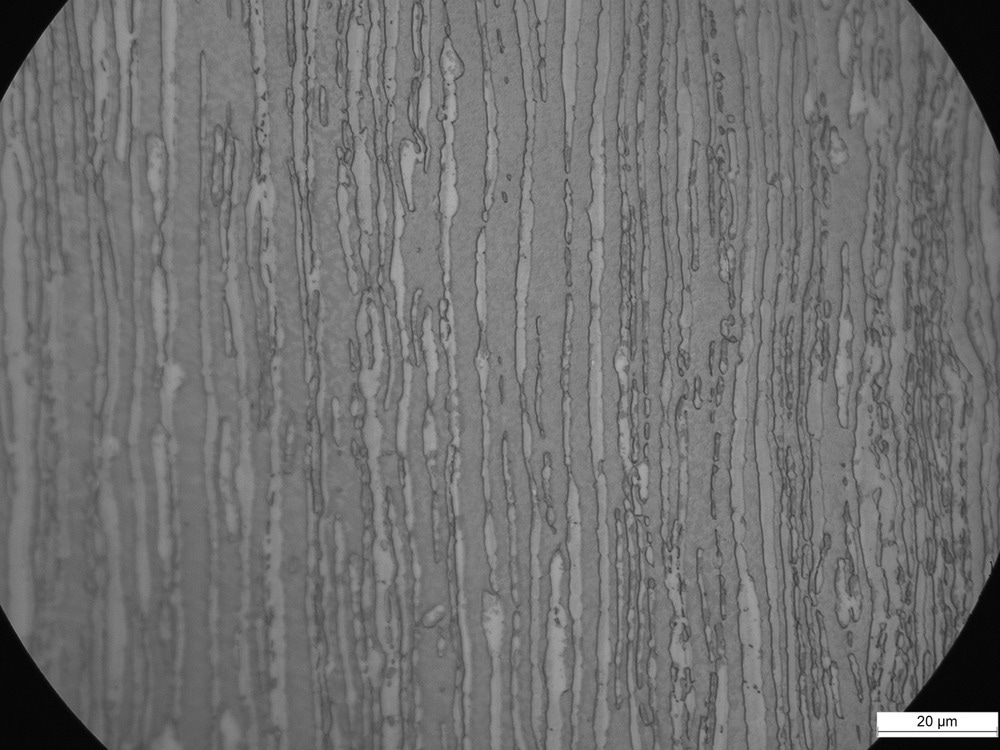
Image Credit: lbrumf2/Shutterstock.com
Duplex Stainless Steel (DSS)
Due to its exceptional corrosion resistance and high strength, DSS is the best metal to use in harsh settings such as reactors, petroleum tankers, deep-sea pipelines to transport petroleum material, saltwater desalination, oil refinery chemical, and petrochemical industries. It has a chemical composition that includes Cr, Mo, Ni, and N.
Annealing temperature, cooling rate, solidification following the welding process, and heat input are the main factors that affect ferrite volume fraction and intermetallic phases precipitation in the harmful phases, such as the sigma phase, chi phase, secondary austenite, nitride (CrN and Cr2N), and carbides (M23C6).
DSS Welding in Industries
Welding is a fundamental and essential activity. Three zones are created as a result of the heat treatment process: a base material (BM), a heat-affected zone (HAZ), and a weld zone (WZ). Following welding, DSS reveals three distinct zones in the chemical makeup of the ferrite and austenite phases, each resulting in a different level of corrosion resistance.
The heat from welding also impacts the volume fraction of ferrite in addition to its chemical makeup. Multiple-pass welding permits the formation of an excessive amount of secondary austenite. As a result, the weld zone has limited corrosion resistance. Also, choosing the right welding electrode is crucial for managing the microstructure of the welding area and, consequently, the properties after welding.
The influence of filler metal on the microstructure, mechanical characteristics, and solidification of the dissimilar weld between high strength low alloy API X70 pipeline steel and super duplex stainless 2507 has been investigated. It was concluded that the 2594 filler weld contains multiple reformed austenite embedded in the ferrite matrix, whereas the 309L filler weld's microstructure comprised skeletal ferrites in the austenite matrix. Another study used gas tungsten arc welding (GTAW) with ER2553 and ERNiCrMo-4 filler metals to explore the weldability, metallurgical, and mechanical characteristics of the UNS 32750 super-duplex stainless steel joints. Due to the improved mechanical qualities of welded joints using ER 2553 compared to welded joints using ER NiCrMo-4, the authors advised using it for welding super-duplex stainless steel. These investigations indicate that managing the microstructure of the weld zone is crucial.
Post-Weld Heat Treatment
The most well-known and significant method for improving microstructure after welding is post-weld heat treatment (PWHT), which includes several elements such as heating temperature, holding time, cooling rate, and process atmosphere. Intermetallic precipitation, which depends on the presence of Cr, Mo, and C, is promoted by PWHT, incorrect annealing temperature, protective gas, and slow cooling rate. The PWHT of welds, in general, and DSS weldments, in particular, has been the subject of numerous investigations.
According to several studies, annealing should take place between 1000 and 1200 °C, followed by water quenching. Some studies stated that between 1050 and 1100 °C is the ideal annealing temperature for DSS without intermetallic precipitation. The annealing duration and cooling rate should be taken into account during PWHT. Many researchers have examined the impacts of solution annealing time and have found that lengthening the annealing period causes corrosion resistance to diminish.
The production of hazardous phases is caused by the slower cooling rate that occurs after solution treatment of welded joints, even though the cooling rate during PWHT is a significant cause for concern. The presence of intermetallic phases and the sigma phase, which is richer with Cr and Mo, make DSS steel more susceptible to embrittlement, which results in decreased mechanical qualities and low corrosion resistance.
To prevent the creation of hazardous phases, the PWHT technique must be followed appropriately. On the other hand, the right PWHT can increase the austenite volume fraction, which increases the corrosion resistance of the DSS weldments. This viewpoint emphasizes the significance of selecting the best PWHT settings. Only a few studies have been reported on the impact of heat treatment atmosphere on the microstructure of DSS welded joints.
Recent Studies
In a recent report published by the journal Scientific Reports, the authors discussed the post-weld heat treatment of 2205 DSS at 1050 °C, followed by water quenching to prevent the production of detrimental phases such as sigma, secondary austenite, chi, nitride, and carbides, that degrade microstructure, mechanical characteristics, and corrosion resistance.
Energy-dispersive X-ray spectroscopy (EDS) revealed that a particular studied EDS point had a significant level of nitrogen content and, in turn, a lower amount of chromium nitride. Argon and nitrogen were used separately as controlled atmospheres compared to unprotected samples. Investigations were done into how the environment used for the PWHT affected the microstructure and corrosion resistance of the welded joints made of duplex stainless steel.
Microstructural analyses of heat-treated samples showed that second-phase precipitation did not occur when argon was used as the controlled atmosphere. Still, it occurred in the microstructure of the samples when nitrogen was used in the atmosphere. Moreover, the unprotected sample produced intermetallic precipitates with a microstructure that was fairly similar to that of the protected sample with nitrogen.
The samples heated under nitrogen- and nitrogen-controlled atmospheres showed nitride precipitates in the ferrite zones, but samples heated under argon-controlled atmospheres showed no precipitation. In-depth microstructure analysis using optical and scanning electron microscope revealed that nitride precipitates were frequently seen in the welded zones for nitrogen-protected samples. The corrosion resistance of heat-treated welded joints was increased as a result of a decrease in ferrite volume percentage in post-weld heat-treated samples compared to welded samples without heat treatment.
The weld zone hardness of post-weld heat-treated samples was higher than that of the base alloy. The initial hardness of duplex stainless steel was 286 Hv, while the average weld zone hardness for PWHT employing air, argon, and nitrogen atmospheres was 340, 411, 343, and 391 Hv, respectively.
Hardness in the weld zone increased to 33, 44, 20, and 37%, respectively. A substantial reduction was observed in the elongation and ultimate tensile strength after PWHT. The initial maximum tensile strength of the base material, the 2025 DSS, was 734.9 MPa, while the ultimate tensile strengths of the welded joints were 769.3, 628.4, 737.8, and 681.4 MPa under the welded PWHT using air, argon, and nitrogen atmospheres, respectively.
In conclusion, this investigation into the impact of the heat treatment environment on the microstructure of duplex stainless steel welded joints revealed that PWHT improved grain refining and increased the austenite fraction in the HAZ and weld zone. The production of nitride precipitates was caused by employing nitrogen as a protection gas during heat treatment. The same effect was also seen when the specimens were heated without a protection gas. However, nitride precipitation did not occur when argon was used as a protective gas.
The specimen heated with nitrogen during PWHT had the largest ferrite volume fraction compared to specimens heated with argon and air during heat treatment. After PWHT, it was found that the ultimate tensile strength (UTS) and ductility significantly decreased, especially when nitrogen and air were used as heat treatment atmospheres. For HAir and HNitrogen welded joints, higher Vickers hardness values were observed. This was attributed to the precipitation of nitride. Due to nitride precipitation and secondary austenite, corrosion resistance was reduced for HNitrogen samples that underwent PWHT using nitrogen and for as-welded W samples.
More from AZoM: Showcasing Composite Material Innovation at JEC World 2023
References and Further Reading
Mohamed, A. Y., et al. (2023). Effect of heat treatment atmospheres on microstructure evolution and corrosion resistance of 2205 duplex stainless steel weldments. Scientific Reports, 13, 4592. https://doi.org/10.1038/s41598-023-31803-5
Pitkälä, J., et al. (2022). A Study of the Effect of Alloying Elements and Temperature on Nitrogen Solubility in Industrial Stainless Steelmaking. Metallurgical and Materials Transactions B, 53, 2364–2376. https://doi.org/10.1007/s11663-022-02534-1
Wang, H., et al. (2022). Effect of Secondary-Phase Precipitation on Mechanical Properties and Corrosion Resistance of 00Cr27Ni7Mo5N Hyper-Duplex Stainless Steel during Solution Treatment. Materials, 15(21), 7533. https://doi.org/10.3390/ma1521753
Disclaimer: The views expressed here are those of the author expressed in their private capacity and do not necessarily represent the views of AZoM.com Limited T/A AZoNetwork the owner and operator of this website. This disclaimer forms part of the Terms and conditions of use of this website.