A key physical parameter of powder materials - density - directly influences the performance, quality, and application of the powder material. As a result, it is extremely important to understand the definition and methods of density measurement.
Types of Powder Density
Powder is a collection of single solid particles, which in most cases may be considered a basic unit. Powder is typically comprised of solid particles, interparticle voids, as well as open and closed pores of particles, as displayed in Figure 1-1.
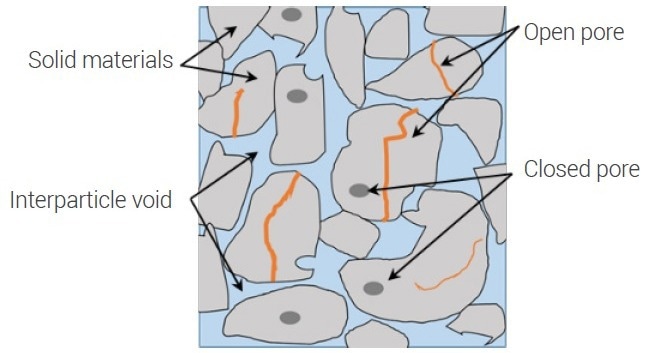
Figure 1-1. Internal structure of the powder material. Image Credit: Bettersize Instruments Ltd.
The physical parameters of the particles, including particle size distribution, particle shape, and surface properties, impact the accumulation performance of the powder, such as tapped density and loose density.
The characterization of powder material density should be based on scientific measurements to enable an understanding of its physical properties, which leads to helping to enhance powder material processing.
Density is defined as the ratio of a sample’s mass and volume. The calculation formula is provided below:
ρ = m / v
where ρ denotes the density, m denotes the mass, and v denotes the volume.
The samples may be weighed using a balance, and the key is to measure the sample’s volume. Densities of the same sample differ as a result of different calculations utilizing distinct types of volume.
According to the British Standards Institute (BSI) and the American Society for Testing and Materials (ASTM), volume types of powder materials may be categorized as true volume, skeletal volume, tapped volume, and bulk volume, related to true density, skeletal density, tapped density, and bulk density.
- True density: This relates to the ratio of the mass and the volume (true volume) of a sample, excluding the volume of the opened pores, the closed pores, and the inter-particle voids.
- Skeletal density: This is the ratio of the mass to the volume (skeletal volume) of the particles, excluding both inter-particle voids and opened pores.
- Tapped density: This is the density measured by mechanically tapping a container of particles to create a regular vibration, and this rearranges the powder particles. The measurement of tapped density is typically conducted using a tapped density tester.
- Bulk density: This is the density measured after the particles have freely filled a standard container under specific conditions, i.e., the mass of the particles per unit volume when they are loosely packed.
The definitions of various types of density are displayed in Table 1-1, which summarizes the volume contained when calculating various types of density.
Table 1-1. Definitions of various types of densities that include different volumes. Source: Bettersize Instruments Ltd.
Type of Density |
Solid Particle Volume |
Open Pore volume |
Closed Pore volume |
Inter-Particle Void volume |
True Density |
✔ |
|
|
|
Skeletal Density |
✔ |
|
✔ |
|
Bulk Density |
✔ |
✔ |
✔ |
✔ |
Tapped Density |
✔ |
✔ |
✔ |
✔ |
Measurement of True Density
Both gas and liquid displacement methods are frequently employed to measure skeletal density or true density. Unlike the liquid displacement method, gas is employed instead of liquid to measure the sample volume.
Liquid Displacement Method
This method is based on Archimedes’ principle: when an object is immersed in a fluid, it is subjected to vertical upward buoyancy which has a value equal to the gravity of the fluid discharged by the object. The principle is expressed with the following formula:
Fbuoyancy = ρliquidgVdischarged
The sample is positioned on the bracket and exposed to air. The mass of the sample is displayed on the electronic balance’s screen:
Subsequently, the sample is immersed in the liquid and hung on the bracket. Buoyancy is part of the mass of the sample:
Fbuoyancy + mfg = mag |
(1.2) |
i.e.:
P1gVdischarged + mfg = mag |
(1.3) |
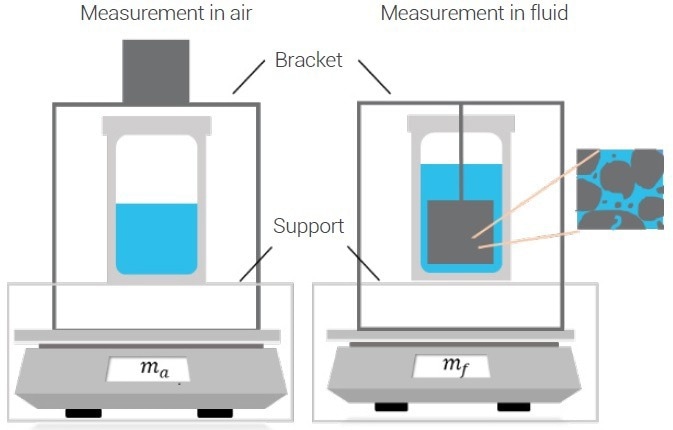
Figure 1-2. Principle of the liquid displacement method. Image Credit: Bettersize Instruments Ltd.
From formulas 1.1 and 1.3, it can be inferred that
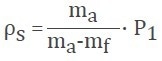 |
(1.4) |
where P1 denotes the liquid density in g/cm3, ρs denotes the true density of the sample in g/cm3, ma denotes the mass of the sample when exposed to air, and mf denotes the balance reading when the sample is immersed in the liquid.
When the liquid displacement method is employed for the measurement of the true density of a sample, it is important to note that:
- The powder sample is insoluble in the liquid.
- No reactions occur between the liquid and the powder particles, as the latter do not absorb moisture and are not straightforward to moisturize.
- The bubbles created at the liquid-solid interface should be removed by a vacuum or heating to guarantee accuracy. Without this, the measurement result will be influenced. It is recommended to use liquids with lower surface tension.
Gas Displacement Method
Boyle’s law determines that under the fixed temperature and quantity, the volume of the ideal gas is inversely proportional to its pressure. With a constant temperature, the relationship between the pressure and the volume of the quantitative gas may be expressed using the following formula:
The production of the pressure (P) and the volume (V) of the gas is constant.
When the gas displacement method is used, the measurement system generally comprises a reference chamber, a sample chamber, valves, a pressure sensor, and a temperature control system. The sample chamber is utilized for the placement of the sample, while the reference chamber is utilized for gas expansion.
Open pores of particles and inter-particle voids are filled with the gas in a gas pycnometer. The gas volume may be obtained via the calculation using the gas pressure before and after gas expansion at a fixed temperature and in sealed chambers with a known volume.
As a result, the sample volume may be acquired based on the gas volume.
Before gas expansion:
where P1 denotes the gas pressure before gas expansion, V1 denotes the volume of the sample chamber, and VS denotes the sample volume.
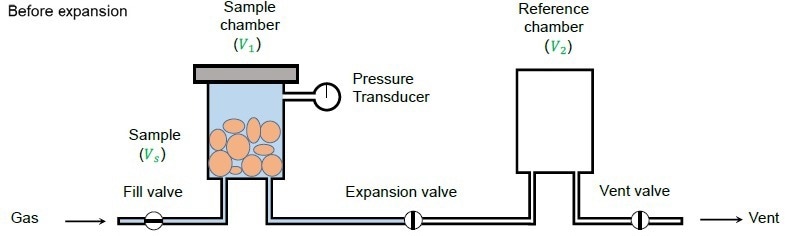
Image Credit: Bettersize Instruments Ltd.
Following gas expansion:
where P2 denotes the gas pressure after gas expansion while V2 denotes the volume of the reference chamber.
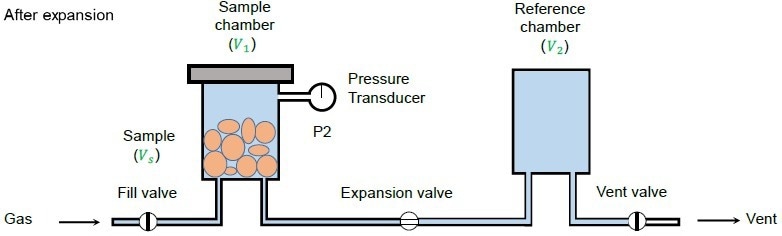
Image Credit: Bettersize Instruments Ltd.
P1(V1-VS) = P2(V1-VS + V2) |
(1.8) |
The true volume of the sample may be obtained using the above formula, allowing the true density to be obtained after the sample is weighed. This calculation is based on ISO 12154:2014 Determination of density by volumetric displacement — Skeleton density by gas pycnometry.
The gas displacement method has the following advantages over the liquid displacement method:
- High accuracy: Extremely high accuracy and reliability with high-resolution transducers, temperature control, and calibrated chamber volumes.
- Multiple functions: Offers four measurements, including density, volume, solid content, and open cell content, while the integrity of the sample is maintained.
- Effortless operation: Enables automatic calibration, measurement, and leak detection, which are all accessible to operators of any experience level.
- Friendly sample requirement: Only requires a sample of size 1-100 cm3, as well as maintaining the integrity of samples.
- Integrated software solution: Directly connected to the balance and with a remote-control connection to the external water bath.
Importance of True Density
True density is among the main physical indicators for the evaluation of the quality of a powder product.
Firstly, true density is a basic parameter of the powder material. The open pores, the closed pores, and the inter-particle voids impact the final performance of the product.
The true density value corresponds to chemical composition and its purity, which determines the performance, quality, and application domain of the product.
Thus the measurement of the true density is essential.
The gas displacement method is widely utilized in product manufacturing.
It is valuable to understand the powder materials’ properties, enhance the manufacturing process and improve the quality of the product when accurately measuring the true density. In scientific research, a gas pycnometer enables the measurement and delivers quick and accurate measurement results.
Powder Metallurgy
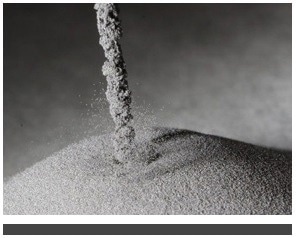
Image Credit: Bettersize Instruments Ltd.
(ASTM B923-22)
The skeletal density of metal determines its properties and processing results, with the performance of metal structures able to be predicted from powder skeletal density.
Powder Coatings
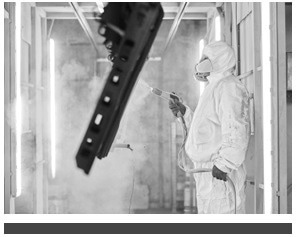
Image Credit: Bettersize Instruments Ltd.
(ASTM D5965-20)
Total solids content helps determine coating coverage potential. Dry pigment blends are observed by evaluating measured densities against theoretical densities based on composition.
Cement
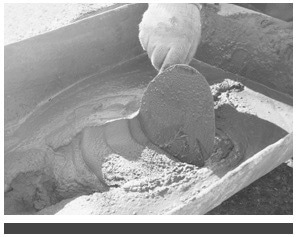
Image Credit: Bettersize Instruments Ltd.
True density is fundamental to guaranteeing the performance and quality of cement powder, affecting its strength, flowability, and environmental impact.
Cellular Plastics
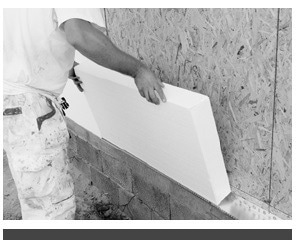
Image Credit: Bettersize Instruments Ltd.
(ASTM D6226-21 and ISO 4590-2016)
Plastic foam properties differ based on the ratio of open cells to closed cells. Insulation foams lower thermal conductivity with trapped gas in closed pores. Flotation devices float because of closed air-filled pores.
Pharmaceuticals
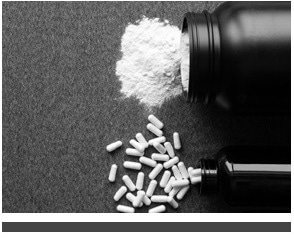
Image Credit: Bettersize Instruments Ltd.
(USP 699 and EP10 04/2019:20923)
Product density defines and controls active or excipient composition. Product forms, purity, etc., can be established by comparing measured density with historical and theoretical values.
Soil
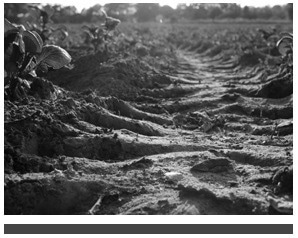
Image Credit: Bettersize Instruments Ltd.
(ASTM D5550-14)
Soil specific gravity (SG) must be corrected due to precipitate formation after drying. A precipitate with lower SG leads to lower results, while one with higher SG leads to higher results.
Food
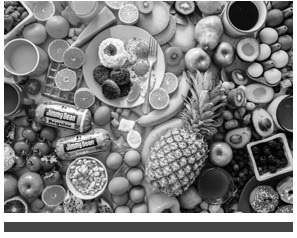
Image Credit: Bettersize Instruments Ltd.
True density is critical for confirming the consistency and quality of dry food, impacting its processing, nutritional value, and shelf life.
Calcined Coke
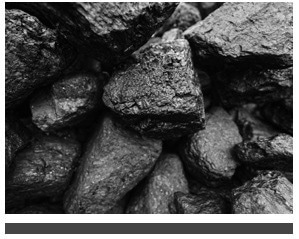
Image Credit: Bettersize Instruments Ltd.
(ASTM D2638-21)
The density of calcined petroleum coke is a critical quality specification for coke calcination as it impacts the properties of the resultant artifacts.
Refractory
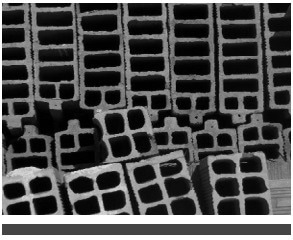
Image Credit: Bettersize Instruments Ltd.
(ASTM C604-02)
True density is beneficial for classification, revealing mineral phases or alterations, identifying chemical differences, determination of total porosity, and calculating results for other tests.
Download the full powder density guide
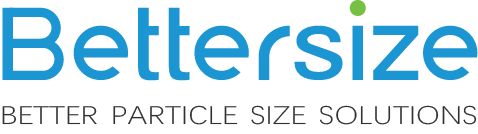
This information has been sourced, reviewed and adapted from materials provided by Bettersize Instruments Ltd.
For more information on this source, please visit Bettersize Instruments Ltd.
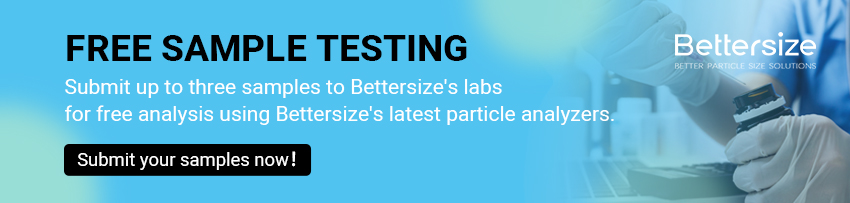