PV cells are composed of many material layers, and their production is a complicated procedure requiring meticulous control of multiple factors, including the gas environment. Gas analysis is an important instrument for monitoring and managing the gas environment during the production of PV cells. The article focuses on various methods of gas analysis employed during the manufacturing of photovoltaic panels.
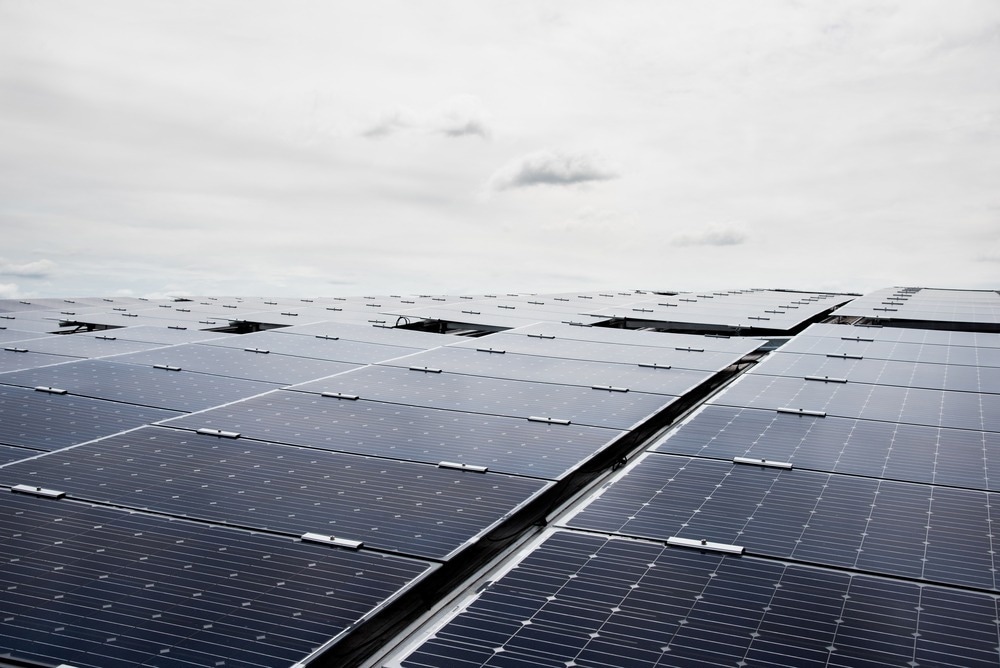
Image Credit: DimonGi/Shutterstock.com
Photovoltaic (PV) cells, sometimes referred to as solar cells, are semiconducting systems that convert sunlight to energy. These are the core constituents of solar panels and are crucial for the generation of sustainable energy.
Gas Analysis In Terms of Photovoltaic Cell Production
The technique of detecting and quantifying the proportion of gases in a specific environment is known as gas analysis. In the context of PV cell fabrication, this entails analyzing and regulating the gases used in different PV cell manufacturing processes to ensure their correct constitution and purity. Hydrogen, nitrogen, oxygen, and argon are the most prevalent gases employed in the synthesis of PV cells.
Gas analysis is utilized to optimize reaction conditions in the solar cell fabrication industry. By analyzing the concentrations of the gases used in multiple processes, designers improve the productivity and purity of PV cells. For instance, the concentration of hydrogen utilized in the diffusion process may be altered to provide the required doping profile in the silicon.
Gas analysis techniques for PV cells are widely categorized into online and offline gas analysis. The online analysis involves the continuous monitoring of the PV cell gas environment throughout its production process. The primary benefit of online gas analysis is that it offers data about manufacturing conditions in real time. Nevertheless, online analysis necessitates costly equipment and has a restricted spectrum of detectable gases.
In contrast, offline analysis involves the periodic collection of gas specimens from the PV cell production assembly. The primary benefit of offline analysis is that it permits the identification of a wider variety of gases. Nevertheless, offline analysis necessitates manual collection, which can be time-consuming and prone to inaccuracy.
Several gas analysis techniques are applied in the PV cell manufacturing process, each with its distinct advantages and limitations.
Applications of Infrared Spectroscopy (IR) for PV Cell Production
Infrared spectroscopy involves analyzing the uptake of infrared radiation by gas particles to recognize the type of gas and measure its concentration. Infrared spectroscopy is susceptible to the majority of gases and may identify minute contaminants in gas mixtures. The primary benefit of infrared spectroscopy is its remarkable sensitivity, which enables the detection of minute quantities of gases. However, the intense calibration of IR instruments is a major drawback.
A research article published in Materials Today focuses on the utilization of flash infrared spectroscopic annealing for environmentally friendly production of perovskite cells. Flash Infrared Annealing (FIRA) is a crystallization process for perovskite thin films that are easily scalable and does not require a highly porous, high-temperature scaffold.
The anti-solvent (AS) approach, in which an anti-solvent, often chlorobenzene, is abruptly introduced to a perovskite predecessor, is the most effective technique for producing PSCs at the laboratory scale. In contrast, FIRA employs a brief IR flash in the range of seconds to facilitate the rapid nucleation and crystallization of the perovskite film from the precursor solution.
The researchers found, based on PV performance and spectroscopic analysis, that the FIRA approach may manufacture cells with comparable efficiency to the frequently adopted anti-solvent methods. Based on a life cycle assessment (LCA) comparison, the FIRA approach had just 8% of the environmental effect and 2% of the production cost of the perovskite active layer compared to the AS method.
Gas Chromatography for PV Cells
Gas chromatography is a technique for analyzing gases that separate gas mixtures into their component gases based on their physical and chemical characteristics. Separating and identifying distinct gases in a mixture is the primary benefit of gas chromatography. Unfortunately, gas chromatography necessitates expensive specialist equipment.
In an article published in the journal Nature, researchers have reported a robust and duplicable doping process that involves bubbling a spiro-OMeTAD:LiTFSI solution with CO2 under ultraviolet light using gas chromatography.
The utilization of altered organic semiconductors as charge extraction interlayers in perovskite solar cells is frequent. Spiro-OMeTAD is the semiconductor employed most commonly in the hole-conducting layer. The doping process typically employs lithium bis(trifluoromethane)sulfonimide (LiTFSI) to increase the electrical conductivity of a material.
CO2 receives electrons from photo-excited spiro-OMeTAD in the unique mechanism proposed by the researchers. The headspace gas combination was analyzed by gas chromatography with a flame ionization detector (FID) using a 250 l syringe injection. As the carrier gas, ultrahigh-purity Argon (99.999%) was utilized. The CO2-treated interlayer displayed about one hundred times greater conductivity than a pristine film, enabling the fabrication of persistent, high-efficiency perovskite solar cells without the use of post-treatment.
How is Mass Spectrometry Utilized in PV Industry?
Mass spectrometry is a technique for gas analysis that determines the mass-to-charge proportion of ions in a gaseous phase. Mass spectrometry is a very sensitive and precise technique that can identify minuscule contaminants in a gas mixture.
A case study published by Perkin Elmer looks at the use of Inductively Coupled Plasma-Mass Spectrometry (ICP-MS) for detecting impurities during the fabrication of Silicon PV cells.
For technique validation, six replicates of a PV silicon wafer specimen were processed with the suggested processing methods and then evaluated using ICP-MS. The results are consistent with the extensive characterization of sample properties. Furthermore, Glow Discharge Mass Spectrometry (GDMS) study confirmed the average ICP-MS results.
Future Trends
The utilization of gas analysis techniques in the production of solar cells is growing in importance. The desire for low-cost, high-performance solar cells necessitates increasingly accurate and precise gas analysis techniques.
Future advancements in gas analysis for the manufacturing of solar cells include the advancement of more precise and selective gas analysis methods. Researchers are investigating the use of nanotechnology and smart materials in the development of gas sensors with increased specificity and selectivity.
Another trend in gas analysis for the manufacture of solar cells is the evolution of superior integrated gas analysis systems. Companies are looking for more computerized and optimized gas analysis systems that can offer real-time data and enable more accurate process management.
In conclusion, gas analysis is crucial to the manufacturing of solar cells. Gas analysis will continue to be an essential tool for optimizing the production process and enhancing the effectiveness and standard of PV cells as the industry expands.
More from AZoM: The Structure-Dependant Design of Circularly Polarized Luminescence (CPL) Polymers
References and Further Reading
PerkinElmer, Inc., Photovoltaic Silicon Impurity Analysis by ELAN DRC ICP. [Online]
Available at: https://resources.perkinelmer.com/corporate/pdfs/downloads/cst_pvsiliconimpurityanalysisbyicp-ms.pdf
Sánchez, S. et al. (2019). Flash infrared annealing as a cost-effective and low environmental impact processing method for planar perovskite solar cells. Materials Today, 31, 39-46. Available at: https://doi.org/10.1016/j.mattod.2019.04.021
Kong, J. et al. (2021). CO2 doping of organic interlayers for perovskite solar cells. Nature 594, 51–56. Available at:https:/doi.org/10.1038/s41586-021-03518-y
Disclaimer: The views expressed here are those of the author expressed in their private capacity and do not necessarily represent the views of AZoM.com Limited T/A AZoNetwork the owner and operator of this website. This disclaimer forms part of the Terms and conditions of use of this website.