The rapid development of electronic vehicle engines is driving innovation in automotive greases, since there is a need for lubricants that can withstand new, demanding working conditions.
Lubricants for high-performance electric motor vehicles must withstand various loads, speeds, and temperatures to reduce friction and wear effectively.
Manufacturers and laboratories require tribological testing to evaluate and rank lubricant performance to improve formulations for new applications.
Testing in a real system is an expensive and time-consuming approach. Therefore, various national and international testing standards are available to assess the performance and load-carrying capacity of different lubricants outside a real system.
The four-ball test is one of the most widely used methods for selecting lubricant additives and controlling batch production quality.
This article presents a practical testing solution for rapidly and critically evaluating electric motor greases in a controlled environment and with automated varying test conditions using the Bruker UMT TriboLab® system.
The wear rate, frictional torque, coefficient of friction, critical seizure, and weld points are experimentally determined to analyze the wear-resistant properties of commercially available electric motor greases.
Performing Four-Ball Tests
The Bruker UMT TriboLab (Figure 1) employs a typical four-ball test setup. The upper holder has a stationary steel ball in contact with three lower steel balls firmly secured in a rotating cup holder. To enable the testing of lubricants or greases, the ball-to-ball contact areas are coated with the material under test.
A thermocouple and PID feedback loop heater control the lubricant up to 400 °C.
The Bruker Gold Series linear-force sensor allows for the application of constant or progressive loads up to 2 kN. Both upper and lower holders rotate centrally along their axis of symmetry, ensuring an even load distribution. The Bruker torque sensor, connected to the tribotester, measures the frictional torque up to 10 Nm.
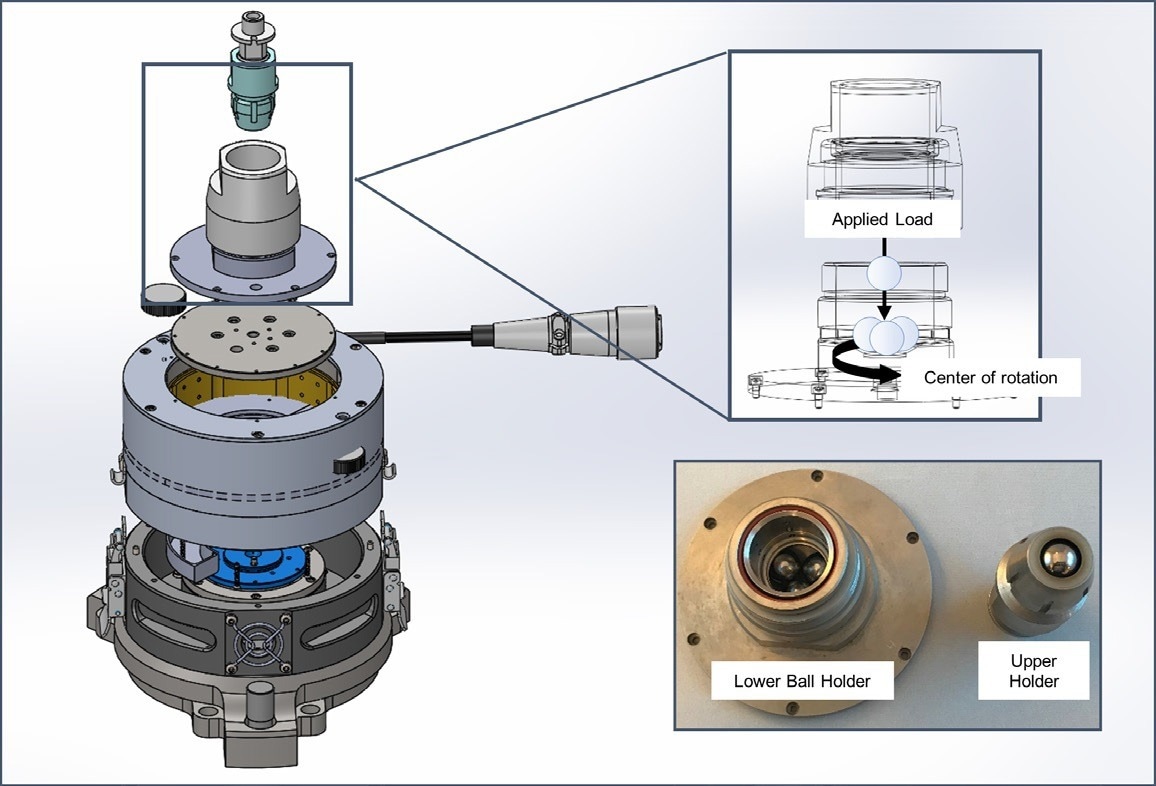
Figure 1. Schematic diagram of a four-ball rotary tester on the Bruker UMT TriboLab. Image Credit: Bruker Nano Surfaces
Table 1 summarizes several standardized four-ball test protocols, as described by ASTM, which evaluate the performance of various lubricants and greases. Due to its modularity, the UMT TriboLab can perform all protocols listed in Table 1.
Table 1. Summary of standardized four-ball tests to evaluate the performances of various lubricants. Source: Bruker Nano Surfaces
TEST METHOD |
DESCRIPTION |
LOAD (N) |
SPEED (RPM) |
TEMPERATURE (°C) |
TEST DURATION |
ASTM-D2266 |
Wear prevention - Greases |
392 ± 2 |
1200 ± 60 |
75 ± 2 |
60 ± 1 min |
ASTM-D2596 |
Extreme pressure properties - Greases |
Step load, starting from 784 |
1770 ± 60 |
27 ± 8 |
10 ± 2 s per load step. (New balls each step) |
ASTM-D2783 |
Extreme pressure properties - Fluids |
Step load, starting from 784 |
1760 ± 40 |
18 to 35 |
10 ± 2 s per load step. (New balls each step) |
ASTM-D4172 |
Wear prevention - Fluids |
147 ± 2 or 392 ± 2 |
1200 ± 60 |
75 ± 2 |
60 ± 1 min |
ASTM-D5183 |
Coefficient of Friction - Lubricants |
Wear-in: 392
Test: Step load, starting from 98.1 |
600 |
75 ± 2 |
Wear-in: 1 h
Test: 10 min per load step |
ISO-20623 |
Extreme pressure and anti-wear properties - Fluids |
Step load, starting from 100 |
1450 to 1500 |
Room temperature |
10 ± 0.2 s or 60 ± 0.5 s |
Assessing Anti-Wear Performance of Electric Motor Greases
This study critically evaluated the wear-preventive characteristics of electric motor greases using TriboLab.
To determine the lubricated wear behavior and wear rate of two commercially available synthetic bearing greases, namely polyolester (POE) and polyurea (PU), the four-ball standard test procedure (ASTM D2266-01) was adopted.
The tests were performed by applying a 392 N load against three lower balls (AISI 52100 steel, Ø12.7 mm) covered with a layer of the test grease at a speed of 1200 rpm for 60 minutes in a temperature-controlled environment of 75 °C.
The optical microscope with a magnification of 4.5x was utilized to measure the average wear scar on the three lower balls to compare anti-wear properties. The wear volume and wear coefficient were then determined using equations derived from existing literature.1,2

where V is the wear volume, d is the diameter of the wear incision in millimeters, and L is the applied load in kilograms.
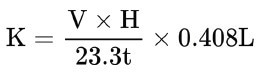
where H is 720 g/mm2, t is the test duration in minutes, and 23.3 is in revolutions per minute. Literature also reports direct wear calculation from white light interferometry areal topography measurements, which combine a large field of view with an exclusive nanometer vertical resolution (Figure 2 and Table 2).
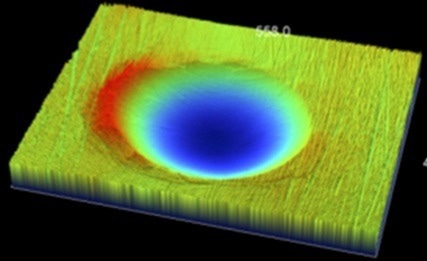
Figure 2. Topography was mapped using a Bruker white light interferometry 3D profiler. Image Credit: Bruker Nano Surfaces and Metrology
Table 2. Example of direct wear volume calculation using topography information from Figure 2. Source: Bruker Nano Surfaces and Metrology
Volume Calculations |
[μm3] |
Natural Volume |
294813.28 |
Normal Volume |
0.82 |
Negative Volume |
97191.68 |
Positive Volume |
17990.81 |
Net Missing Volume |
79100.87 |
Total Displaced Volume |
115182.49 |
The homogeneity of the force applied and distributed among the three lower balls in a tetrahedral-geometry four-ball test is influenced by rotational symmetry.
TriboLab has a unique four-ball cup design that secures the lower balls to positions parallel to the axis of rotation, contributing to accurate measurements and meaningful conclusions.
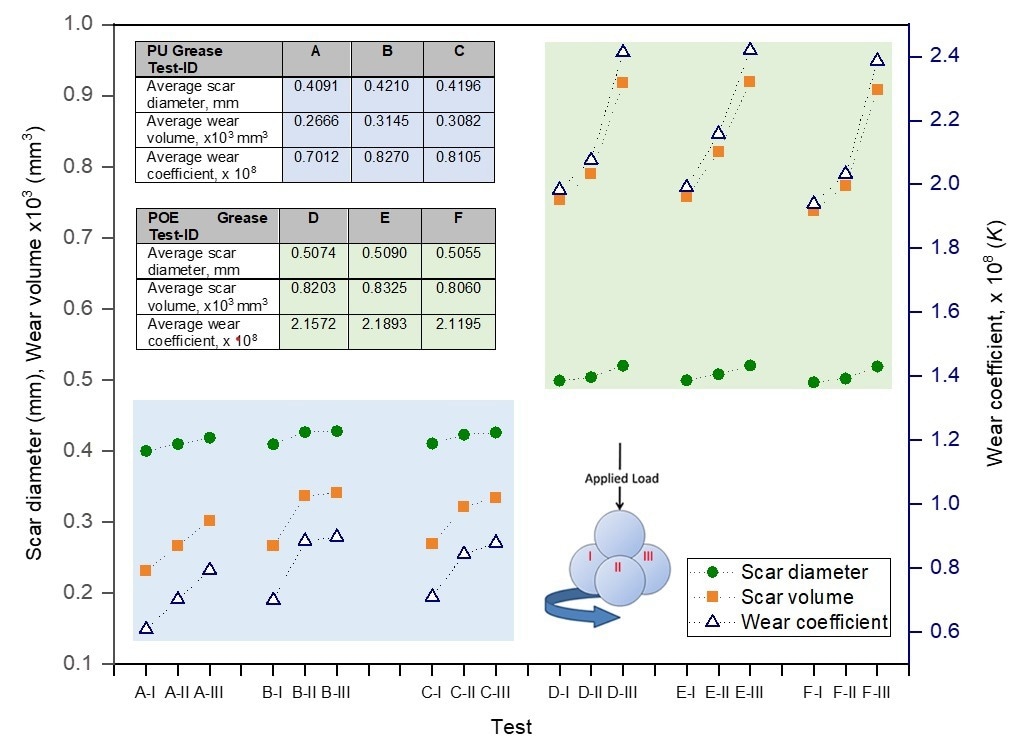
Figure 3. The scar diameters, wear volumes, and wear coefficients of PU grease (A, B, C) and POE grease (D, E, F). The triplicate tests demonstrated highly repeatable and reproducible results. The roman numbers I, II and III denote the three steel balls in the test cup. Image Credit: Bruker Nano Surfaces
This design allows for a consistent wear scar, as shown in Figure 3, during one-hour metal sliding tests with PU and POE greases. The circular shape of the scars, as depicted in Figure 4, confirms that the balls remained affixed during the tests.
The average scar diameter of 0.4166 mm from PU grease matches the result reported in the manufacturer’s technical datasheet, which supports the accuracy of TriboLab’s four-ball test implementation and its suitability for grease quality control.
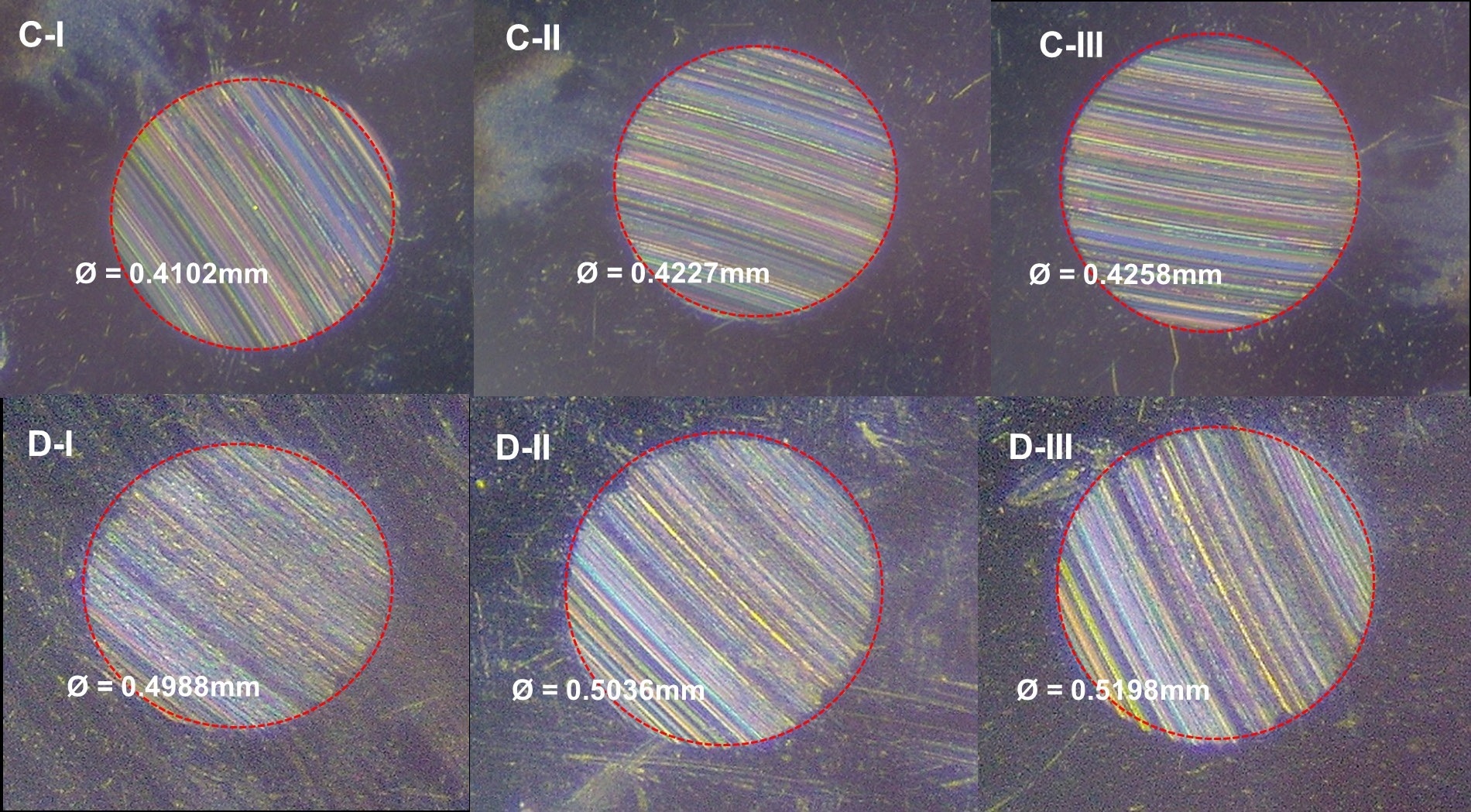
Figure 4. Optical micrographs of wear scars on each of the lower steel balls. The test with PU grease (C-I, C-II, and C-III) produced smaller scars compared to the test using POE grease (D-I, D-II, and D-III). Image Credit: Bruker Nano Surfaces and Metrology
The results plotted in Figure 3 were highly repeatable and reproducible, demonstrating the high repeatability of wear scar measurements (PU: 0.4166 ± 0.0065 mm and POE: 0.5073 ± 0.0018 mm) with a 95% confidence limit.
However, the minimal variation seen in wear scar measurements resulted in significant variations in wear coefficients (wear rates) due to running-in effects that depend on speed, load, temperature, and grease additives, according to the literature.1,3
It is accepted that suitable greases have lower wear rates (smaller wear coefficients and wear volumes). Based on the experimental data obtained in this study, it can be concluded that PU grease, with its lower wear scar and wear rate, provides better wear protection than POE grease.
Determining Friction Coefficient through Step-Load Tests
Reducing frictional forces between contacting surfaces is crucial when evaluating grease performance. One standard method of assessing lubricants is measuring their coefficient of friction (COF), obtained from step-load tests per the ASTM D5183-21 standard.
The UMT TriboLab offers the convenience of performing both step-load and four-ball testing on the same platform due to its inherent flexibility and programmable load.
To illustrate, step-load tests were conducted on PU and POE greases, and the measured friction torque was used to determine their respective COF values, as summarized in Table 3.
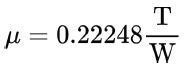
where T is the frictional torque (kg.mm) and W is the applied load in kilograms. The ASTM D5183 test protocol is suitable for field performance evaluations and tool-matching correlation studies.
Table 3. Test protocols to determine coefficient of friction of lubricants, as described in ASTM D5183-21. Source: Bruker Nano Surfaces
|
Wear-in |
Test |
Temperature |
75 ± 2 °C |
75 ± 2 °C |
Speed |
600 rpm |
600 rpm |
Duration |
60 min |
10 min |
Load |
392 N per 60 min |
98.1 N per 10 min increment to a load that indicates incipient seizure |
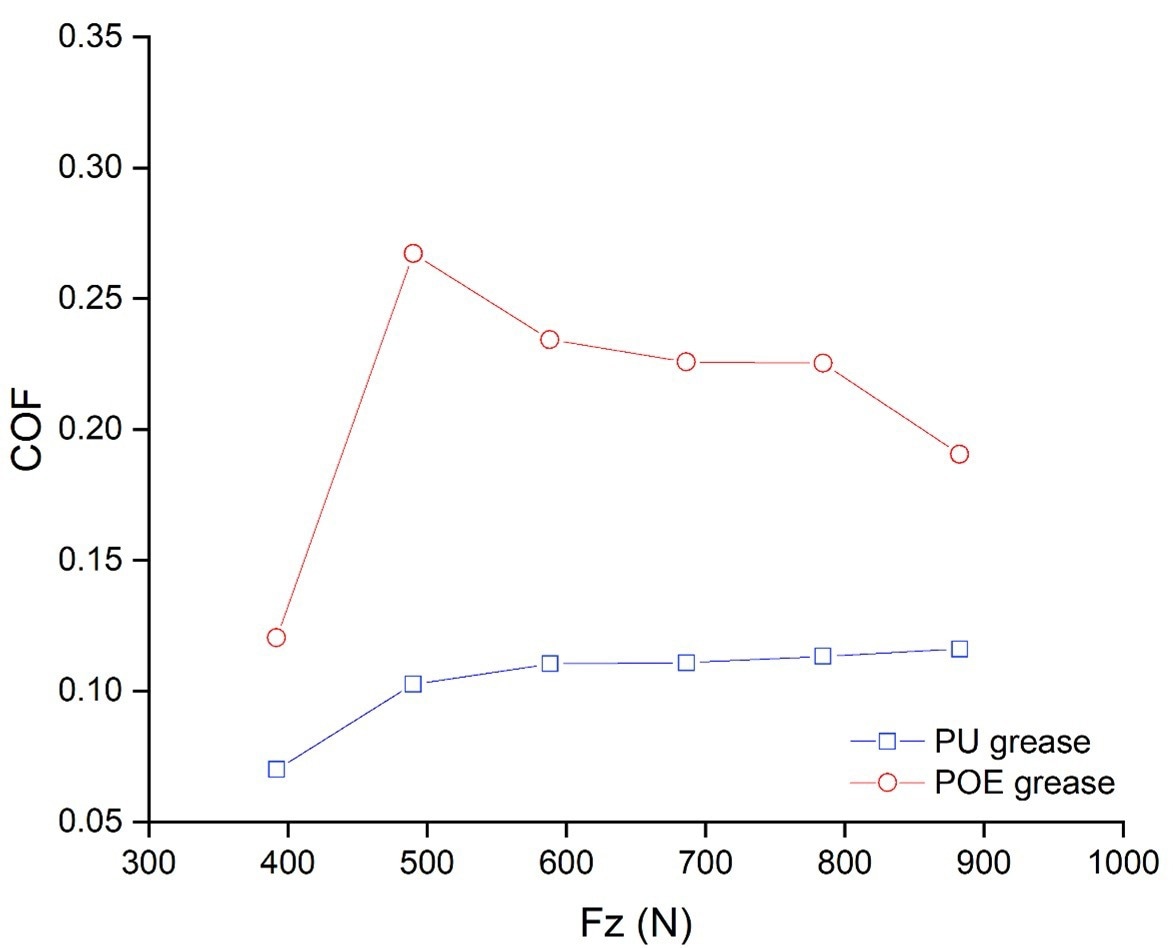
Figure 5. Coefficient of friction as a function of applied load for POE and PU greases. Image Credit: Bruker Nano Surfaces and Metrology
Figure 5 illustrates the calculated coefficient of friction (COF) for two electric motor greases. Neither grease exhibited welding, but the load-carrying capacity of the polyurea (PU) and polyolester (POE) greases differed significantly under extreme pressure (EP) conditions.
It was observed that the PU grease displayed a lower friction coefficient and wear scar than the POE grease under the same operating conditions, making it a more suitable choice for high-load and high-pressure applications.
The COF of the PU grease remained relatively constant when subjected to incremental loads ranging from 490.1 N to 882.5 N, indicating that it facilitated hydrodynamic effects in the step-load tests and prevented seizure from occurring.
In contrast, the POE grease demonstrated poor resistance to seizure, with its COF increasing by more than double when the applied load increased from 392 N (µ = 0.1204) to 490.1 N (µ = 0.2673).
The incipient seizure in the POE grease is likely due to EP film or lubrication failure, where the POE grease underwent chemical reaction changes resulting in possible decomposition.4
Above 500 N, the decrease in friction coefficient was attributed to a mixed-lubricant regime caused by direct asperity contacts between steel balls. This regime induced oxide formation, leading to a thin tribofilm layer that further reduced friction.
Identifying Seizure and Weld
While most bearings are designed to last longer than the equipment they are installed on, premature failure can occur due to wear and improper lubrication.
Lubricants lose their load-carrying capacity as the lubricating film becomes too thin, leading to metal-to-metal contact between rolling elements and raceways, which can cause seizure and welding.
Although field testing the load-carrying capacity of lubricants can be expensive and impractical for manufacturers, TriboLab offers a viable solution in a four-ball test kit that can quickly detect lubricant failure.
In a simulated test designed to induce seizure and welding, steel balls coated with a thin layer of PU grease were subjected to a 1000 N load at varying rotational speeds of 1000, 1500, 2000, and 2500 rpm. The results of the test are presented in Figure 6.
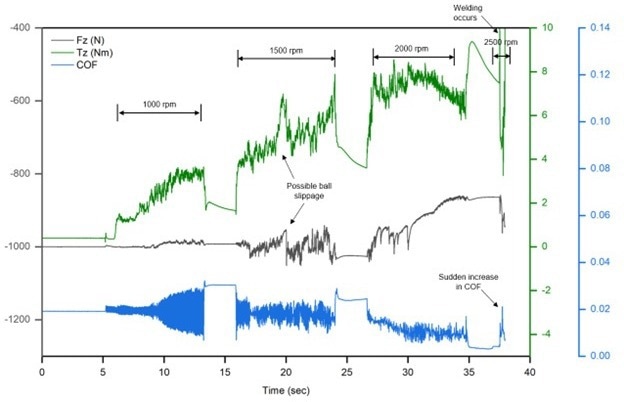
Figure 6. Changes in frictional torque (Tz) at rotation speeds of 1000, 1500, 2000, and 2500 rpm. The drastic Tz surge at 2500 rpm corresponding to an increase in COF indicates complete seizure, where welding of the steel balls took place. Image Credit: Bruker Nano Surfaces and Metrology
The coefficient of friction (COF) of the PU grease decreased as the rotational speed increased, shifting from the boundary regime to the mixed boundary regime (0.019 at 1000 rpm, 0.018 at 1500 rpm, 0.011 at 2000 rpm).
Sudden changes in rotational torque (Tz) and COF in Figure 6 provide a reliable indicator of seizure and weld. At 2000 rpm, Tz increased from 4.2 Nm to 6.8 Nm at t = 20 s, before dropping back to approximately 5 Nm.
Even though the COF remained within the range of 0.018, fluctuations in Fz suggest the possibility of ball slippage due to incipient seizure. The complete seizure occurred at approximately t = 38 s when Tz sharply rose above 10 Nm and COF suddenly increased.
The high torque value activates a safety feature that forces the tribometer to stop as it exceeds the maximum drive torque of the motor. This safety feature protects the components of Bruker UMT TriboLab sensors from damage and enables automatic seizure detection, allowing for unattended tests and swift screening.
Figure 7 depicts the surface of the welded steel balls, where the upper ball is substantially worn out, and its metal surface has transferred onto the lower balls. The growth and extension of localized damage on the lower balls constitute a seizure.
This visual and non-standardized evaluation is helpful for rapidly assessing the performance of various lubricating fluids and greases.
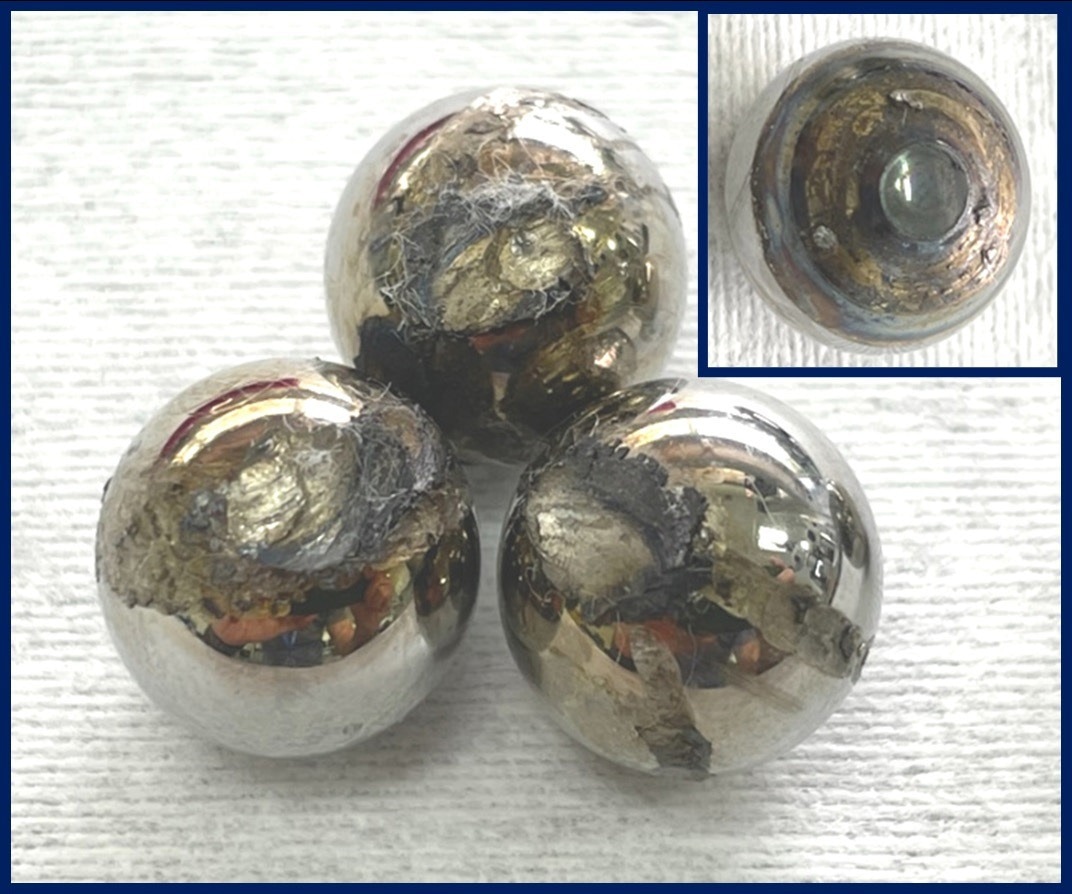
Figure 7. Severely damaged steel balls with signs of oxidation, slipping, and welding. Image Credit: Bruker Nano Surfaces and Metrology
Conclusions
The Bruker UMT TriboLab is a valuable tool in the rapidly evolving electric vehicle technology space. It provides an agile platform that accurately simulates real tribo-conditions. It also enables fast screening for lubricants and greases that can sustain high rotational speed and high torque at zero speed.
This article highlights the use of high-precision four-ball tribotesting to evaluate lubricants' anti-wear and extreme properties at varying loads and rotating speeds according to internationally adopted and recognized standards.
The four-ball test kit is designed with rotational symmetry to properly assess lubricant properties, including friction, load-wear index, last non-seizure load, initial seizure load, and weld point, among others.
The unique modular concept of the TriboLab offers complete and uncompromised testing of a wide range of friction-wear mechanisms and operating conditions, providing a benchmark for innovative lubricants and greases.
References and Further Reading
- Torbacke, M., Rudolphi, A., and Kassfeldt, E. “Lubricants: Introduction to Properties and Performance,” John Wiley & Sons. (2014). http://dx.doi.org/10.1002/9781118799734
- Rowe, C., Peterson, M., Wiler, W. “Wear Control Handbook”, American Society of Mechanical Engineers. (1980).
- Peterson, M. ”Design Considerations for Effective Wear Control”, American Society of Mechanical Engineers. (1980).
- Sethuramiah, A., Okabe, H., Sakurai, T., “Critical Temperatures in EP Lubrication,” Wear. (1973). https://doi.org/10.1016/0043-1648(73)90134-8
Relevant Standards
ASTM D2266-01, “Standard Test Method for Wear Preventive Characteristics of Lubricating Grease (Four-Ball Method),” ASTM International. (2015).
ASTM D2596-20, “Standard Test Method for Measurement of Extreme-Pressure Properties of Lubricating Grease (Four-Ball Method),” ASTM International. (2020).
ASTM D2783-19, “Standard Test Method for Measurement of Extreme-Pressure Properties of Lubricating Fluids (Four-Ball Method),” ASTM International. (2019).
ASTM D4172-20, “Standard Test Method for Wear Preventive Characteristics of Lubricating Fluid (Four-Ball Method),” ASTM International. (2020).
ASTM D5183-21, “Standard Test Method for Determination of the Coefficient of Friction of Lubricants Using the Four-Ball Wear Test Machine,” ASTM International. (2021).
ISO 20623:2017, “Petroleum and related products - Determination of the extreme-pressure and anti-wear properties of lubricants - Four-ball method (European conditions),” ISO. (2017).
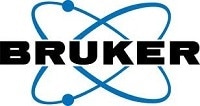
This information has been sourced, reviewed and adapted from materials provided by Bruker Nano Surfaces and Metrology.
For more information on this source, please visit Bruker Nano Surfaces.