Ahead of the Battery Electric Vehicle Architectures USA conference this June, AZoM spoke with H. Yiğit Cem Altıntaş from Ford Otosan about the company's history, and how it will evolve to meet the new challenge of transitioning to vehicle electrification.
Please can you introduce yourself and your professional background?
My name is H. Yiğit Cem Altıntaş. I am a sustainable product development engineer at Ford Otosan, mostly focused on EV Battery Circularity. I have been working at Otosan as a full-time employee, and before this I did a one-year internship in the same department. I have a bachelor's degree in the Mechatronics Engineering field from Yildiz Technical University.
Could you tell us more about Ford Otosan’s history and the scope of its operations?
The company’s history dates back to 1928 and started with an official Ford dealership agreement. Between 1928 and 1956, Vehbi Koç showed enormous success and in 1956 was ranked the most successful dealer amongst 34 Ford near-east dealerships. Following this and with Turkish government support, Vehbi Koç opened an assembly dealership, which was the first of its kind.
In 1956, Ford Otosan was founded as a joint venture between Ford Motors Co. and Koç Holding with equal shares, and the first Otosan plant construction began. The plant was completed quickly enough that Otosan was able to start manufacturing in 1960. Since then, Otosan has manufactured Light Commercial, Medium Commercial, Heavy Commercial, and passenger cars, which were added to the product portfolio in 2022 following the purchase of the Craiova plant of Ford Motor Co. in accordance with the “Future . Now” motto.
Ford Otosan is the leading manufacturer of commercial electric vehicles in Europe, and in 2022 announced the building of a new, more sustainable plant to support its production. Why is vehicle electrification investment so integral to Ford Otosan’s mission?
As our motto says, “Future. Now.” Developing and integrating future technologies is in our DNA. Therefore, this investment is very crucial for us to achieve future net zero transportation and to be a sector leader in Europe and Turkey. As a company that has always followed the mission of offering products and services that benefit the environment and society since its establishment, Ford Otosan strives to create more benefits in environmental, social, and governance aspects as part of its sustainability strategy.
The “Future. Now” motto describes our dynamic structure to develop and address future technologies right now.
Ford Otosan has been a pioneer in R&D activities in Turkey since 1961. Could you share some notable developments over the course of this history?
With the structuring of the Product Development Department in 1961, we launched R&D activities, becoming a pioneer in the Turkish automotive industry. These activities led to the design and development of “Anadol, the first Turkish passenger car” produced in 1966, and ERK, Turkey’s first local diesel engine, in 1986.
After establishing an equal partnership with Ford, we developed the Transit Connect, our first large-scale project, followed by the new Cargo truck and Ecotorq, a brand new heavy-duty vehicle engine, in 2003. Our R&D organization possesses all the capabilities and infrastructure required to design, develop, and test a whole vehicle, including its engine, from scratch to the complete commercial product. The company employs cutting-edge technology to offer competitive products developed by a highly-skilled R&D workforce not only for Turkey but also for all potential export markets, including Europe and North America.
As the biggest R&D organization in the Turkish automotive industry and with over 1,300 R&D engineers, we export engineering to international markets. Our total engineering exports since 2010 reached $ 697 million.
How have your R&D activities evolved, and what do they look like now within the company?
Ford Otosan has the biggest R&D organization in the Turkish automotive industry, with more than 2,000 R&D engineers. The R&D activities have continued since 1961, with the re-structuring of the Product Development Department, which has evolved into three R&D centers now, all of which have been certified by the Ministry of Science, Industry, and Technology.
Located in Sancaktepe, Gölcük, and Eskişehir in Turkey, Ford Otosan’s R&D organizations possess all the capabilities and infrastructure required to design, develop, and test vehicles from start to finish.
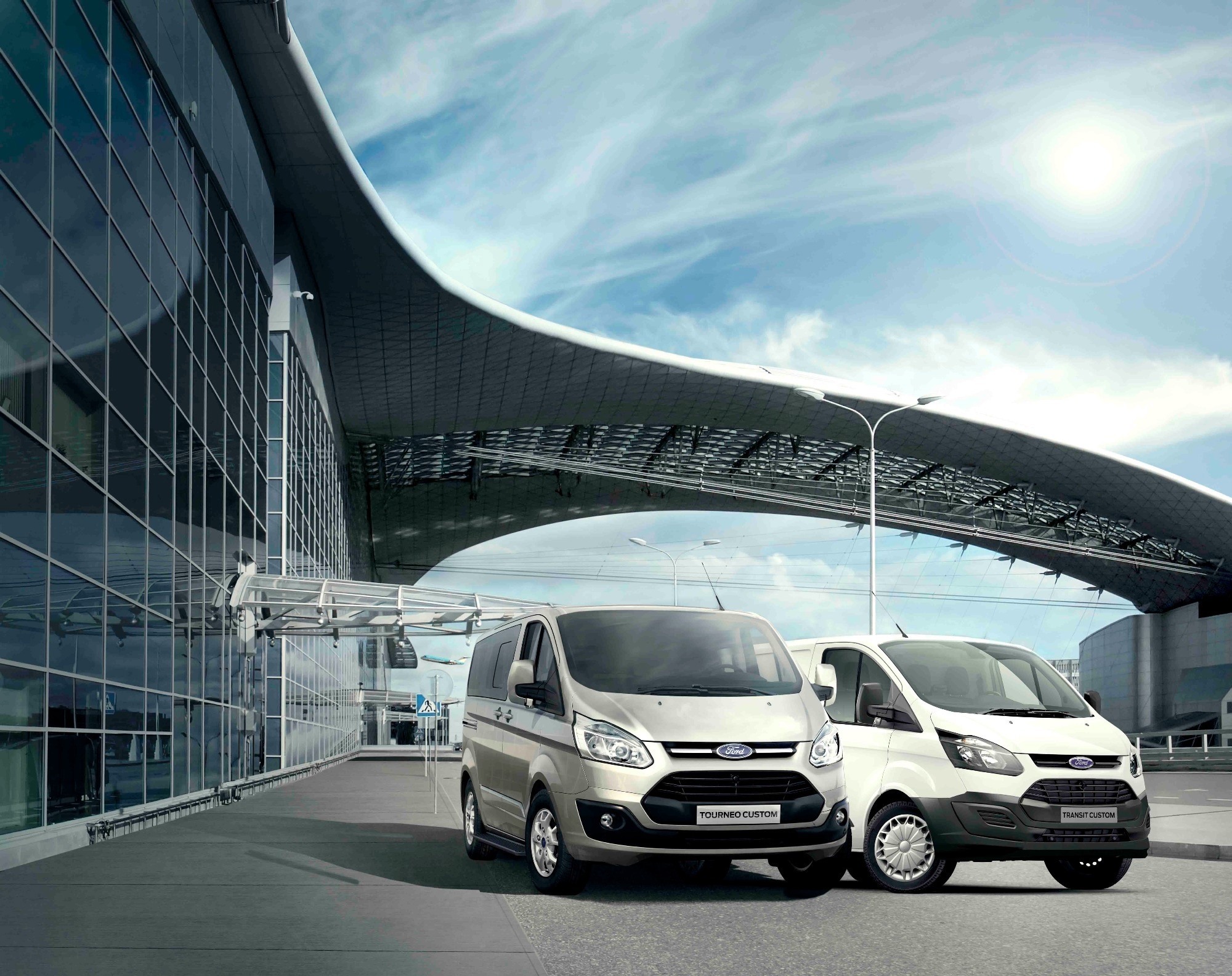
Image Credit: Ford Otosan
As part of the ongoing research and product development activities for Ford Motor Company and Ford Otosan, several projects in different scales are carried out on engine and powertrain systems, interior and exterior bodies, chassis systems, and electrical and electronic systems of vehicles. Following the technological transformation in the automotive industry, and in addition to conventional automotive products and services, advanced R&D studies are carried out on a wide array of topics, including the reduction of CO2 emissions, connected vehicles, autonomous vehicles, electric vehicles, and electrification as well as light vehicle technologies. Investments in the R&D infrastructure also continue.
Ford Otosan will be attending the Battery Electric Vehicle Architectures USA conference in June, with two speakers from the company contributing to the program. Why is it important for Ford Otosan to engage in conferences such as this?
It is a great opportunity for Otosan to mention studies on an international stage. Besides that, Otosan can learn much about how the EV Industry is evolving, which is one of the most important things for us because, like every other OEM, we are in an EV transition period too. There is no preconception of what to do, so we value other companies’ ways of navigating an EV transition.
What can attendees expect to hear from the talks conducted by yourself and your colleague Cemre Sila Atiglan?
The audience can expect to hear information on the following topics:
- A circular economy model for EV batteries
- What is a second life (reusing) business model and its advantages?
- Limitations of EoL Processes
- Recycling Industry outlook and its impact in terms of sustainability
- Life Cycle Assessment (LCA) from OEM perspective etc.
- Battery LCA methodology & benchmarking
In your opinion, what more must be done to produce a sustainable and cost-efficient global automotive industry?
There is much progress to be made to achieve a sustainable and cost-efficient automotive industry. For example, we need to make zero-emission vehicles that are accessible to all customer profiles independent of their financial status, geographic location, etc. Also, relevant infrastructures should be prepared for public use to encourage people to buy zero-emission vehicles. Lastly, holistic and pragmatic supply chains should be created for sustainability to ensure a net-zero automotive industry.
Are there any particularly exciting developments in the near future for Ford Otosan?
With significant investment and Ford Motor Co.'s ambitious future plans, Ford Otosan will be fully electrified by 2030 with a significant capacity increase. That makes us one of the biggest EV manufacturers in Europe and the biggest in Turkey.
Also, besides the EV transition, we will still be developing future transportation technologies, such as hydrogen fuel cells, hydrogen ICE, and other alternative fuel technologies.
About H. Yiğit Cem Altıntaş
H. Yiğit Cem Altıntaş is a Sustainability Engineer who is passionate about EV and EV battery technologies. He is a strong engineering professional with a Bachelor of Science (BS) focused on Mechatronics Engineering from Yıldız Technical University.
LinkedIn
Disclaimer: The views expressed here are those of the interviewee and do not necessarily represent the views of AZoM.com Limited (T/A) AZoNetwork, the owner and operator of this website. This disclaimer forms part of the Terms and Conditions of use of this website.