A future driven by electric vehicles (EVs) is now a reality made possible by technology, innovation, and careful testing. This article discusses the seismic shift away from the combustion engine with Nigel Taylor.
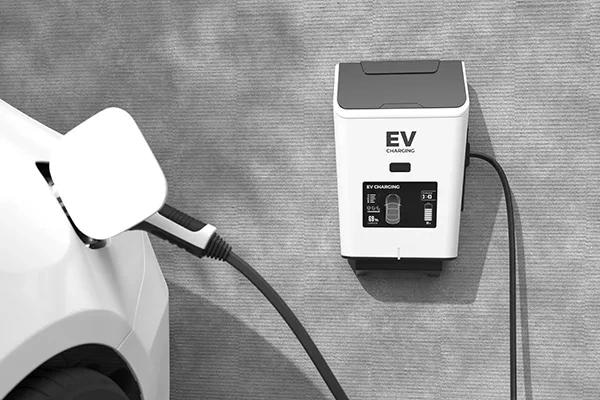
Image Credit: H.E.L Group
Nigel has applied his talent to low-carbon electric vehicles for 30 years, initially in the automotive industry for companies such as Jaguar Land Rover and the Rover Group. He is a freelance technical specialist and the founding director of BatteryDesign.net.
Fit for Purpose Design
Battery design is challenging, and the complexity increases as more advanced cells are needed. The battery design and optimization process requires the close collaboration of specialists in various fields, from chemistry to electrical and mechanical engineering.
This multidisciplinary group worked on all the different steps of the process, including the cells, module, and battery. Like chains, a battery is only as strong as its weakest cell.
The design of effective and reliable batteries must consider the following five critical elements:
- Thermal: Consistent temperature across the battery is required for it to work appropriately.
- Electrical: Batteries may experience resistance problems, leading to other issues like electrical arching or shorting.
- Mechanical: Vehicles can be involved in accidents. Batteries must be designed so that physical impacts will not cause them to catch fire due to thermal runaways.
- Control: A good understanding of the battery’s chemistry aids in predicting the behavior during the life cycle, particularly when being pushed to its limits.
- Safety in design: The risks associated with using batteries (overheating, short circuits) must be addressed during design so that if things go wrong, users will not be put in danger, for example, by providing warnings for users.
There are considerable scientific challenges encountered in electric vehicle design. This article provides a summary, while a full explanation of these challenges is available on the Modern Chemistry podcast.
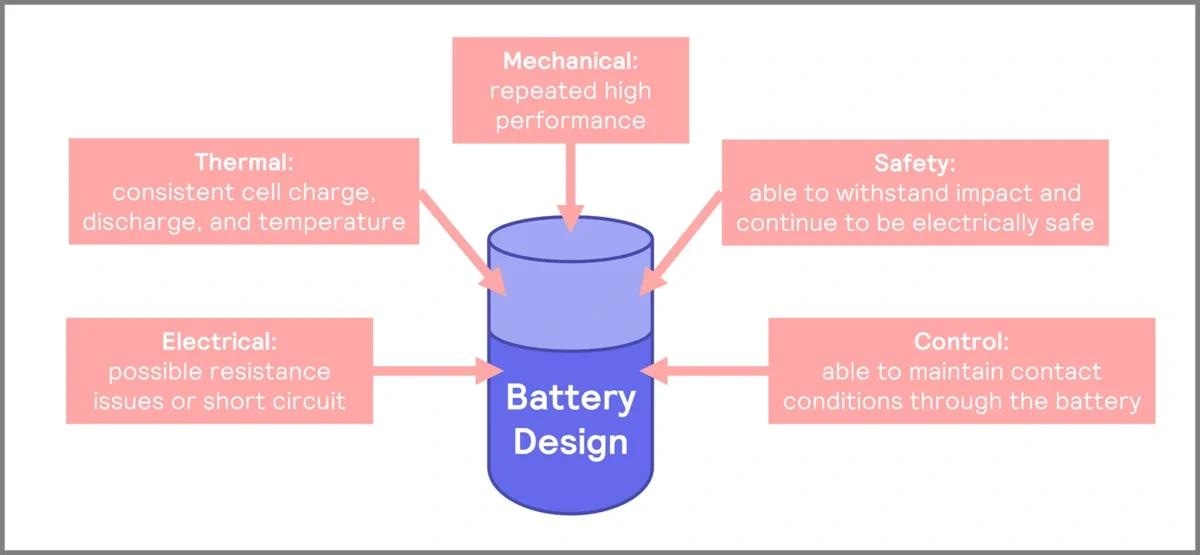
Figure 1. Battery design diagram. Image Credit: H.E.L Group
Not All Batteries Are the Same
Electric vehicle batteries vastly differ from AA or cell phone power pack cousins. A cell phone begins to drop recharge performance in around two years, but a car needs to last far longer.
An electric car will typically be recharged around five to eight times more than any phone. While a phone runs from just one cell, a Tesla car is powered by 6,000 electrically connected cells.
We carry phones and usually go indoors when it is cold, meaning that phones are exposed to a wide but not extreme range of temperatures.
However, an electric car left outside requires a rechargeable battery that can effectively discharge anywhere between -20 °C and 60 °C. Concerns such as this are responsible for the initial slow uptake of electric vehicles, and in response, manufacturers now provide extended warranty periods.
This has also helped the second-hand car market, as an owner can now expect the lifespan of a car to be around 10 to 15 years and 150,000+ miles.
The speed at which a car battery discharges power differs significantly from a cell phone. In constant use, a cell phone will discharge in around 10 hours, with a C rate greater than 10, while steady motorway driving discharges a car battery in around two hours.
Considering cars on a racetrack, the battery will discharge in 20 minutes. This is a C rate of two, and designing a battery to achieve this requires very careful management.
The Problems With Power
A high-end car can deliver between 150 and 225 kW. To match this value, it is assumed that an EV would require over 200 kilowatts (kW).
A single electric lithium cell can produce 3.6 V or 4.2 V at its peak. With 100 cells in the battery, where each negative pole of the cells is connected to the positive pole of the next one, it would increase the voltage from 360 V to 420 V. The following formula provides the calculation of power from current and voltage:
Power(kWh) = Current(Amp) x Voltage(V) / 1000
In terms of energy, regular batteries have 5 A, which would mean: 360 V x 5 A = 1.8 kWh. This is enough to travel only 10 km. A solution would be connecting the cells in parallel instead, resulting in each positive pole being connected to a positive pole and, likewise, to negative poles.
Having 60 series of 100 cells sequences would increase the power 60 times theoretically. A block of 300 A cells with 360 V means the battery's capacity is 108 kWh. The maintenance of this power is the next challenge to overcome.
All 6,000 cells in this EV must function as one, with unified resistance and temperature levels. Any substantial temperature differences pull in high currents and impact how the cells discharge.
The desire of the industry to double what is currently typical to run the packs at 800 V only compounds the difficulty and risk. Just one of the cells malfunctioning and producing a conductive gas is enough to cause arcing across the 6,000 cells.
Capping the Heat
Maintaining a cool temperature is hard to achieve. Even relatively small batteries are designed with a cooling infrastructure or release included. However, EVs must manage their heat loss in a minimum 400 V setting.
In an ideal scenario, an EV would have an electrically insulated but thermally connected cooling system. Having an electrically conducting cooling system could lead to short circuit events, and processes of electrolysis if it is a case where there is a fluid.
The coolant is housed in structures like those at the back of refrigerators to overcome this challenge. The cooling packs would consist of an electrically insulating external coating and a thermally conducting layer between the battery and the cooling plate.
The present solution is a very thin structure consisting of a silicate-based coating with a graphite interlayer. These keep the cell connected, maintaining the series, but allow it to be electrically isolated and, therefore, able to lose heat.
This is a highly innovative solution for when any cell must stay within two degrees Celsius of the other cells.
A significant risk when maintaining a healthy thermal condition in an EV’s battery is ensuring the cooling mechanism remains in place. Despite how smooth the EV’s drive is, it will vibrate, leading to cooling packs dislodging.
A key issue is that uneven temperatures across the cells cause them to age inconsistently. As the whole cell pack is only as good as its worst part, if one cell of the 6,000 is weakened, then the energy of all other cells cannot be exploited.
Since most EV battery packs are irreplaceable and intended to last the car’s lifetime, premature aging is a great cause for concern.
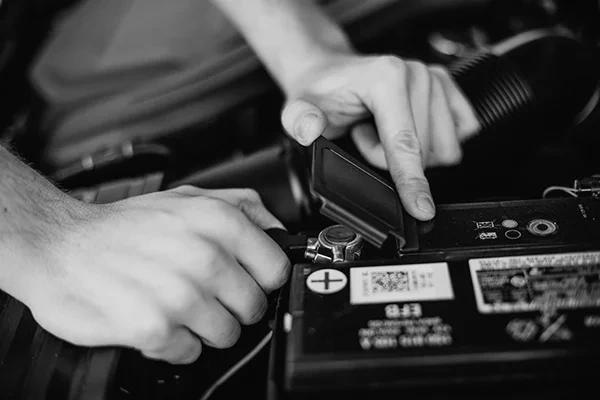
Image Credit: H.E.L Group
EV Wins to Date
However, Nigel explains that it is time to have more confidence in the safety of EV cars.
We don’t worry about the battery in our remote control, so need not worry about the safety of the battery in a car.
Trace elements, like niobium, are being put into some cells to make them more robust, and the latest battery packs in Formula E are making a step change in energy density too.
[The cars will] feel like early 1970s Formula One in terms of performance. That [should] boost consumer confidence in the lifespan of electric cars to the point that they [become] the norm.
Nigel Taylor
Nigel feels that the general journey of EVs into the mainstream has gone well, and with recent advances in technology, it is now possible to use a phone app to monitor battery health.
Access to high-quality data has also put some pack control system management into the cloud, where battery performance is tailored to individual usage or optimum experience, regardless of the driving conditions.
Considering the Future
There is much discussion concerning the possible reuse of EV batteries. This helps in terms of sustainability, but it will only prove possible in cars if it is demonstrated to be commercially viable. The costs to disassemble a pack and ensure its safe reconfiguration are too high.
There are also concerns regarding the validity of conducting this process on packs that have already undergone a hard-working life.
Vehicle-to-grid innovations may be a possibility if pack reuse within cars is not viable, in addition to using repurposed batteries in the home which are charged by solar panels during the day to power the home at night.
A further idea is putting repurposed batteries together to create multi-car, fast-charging points that could protect the grid from brownouts and boost local communities.
EV cars are past their infancy, but they still have plenty of progress to make, which may include an awkward adolescence with essential benefits to motorists and the planet. There is undoubtedly plenty of change to come.
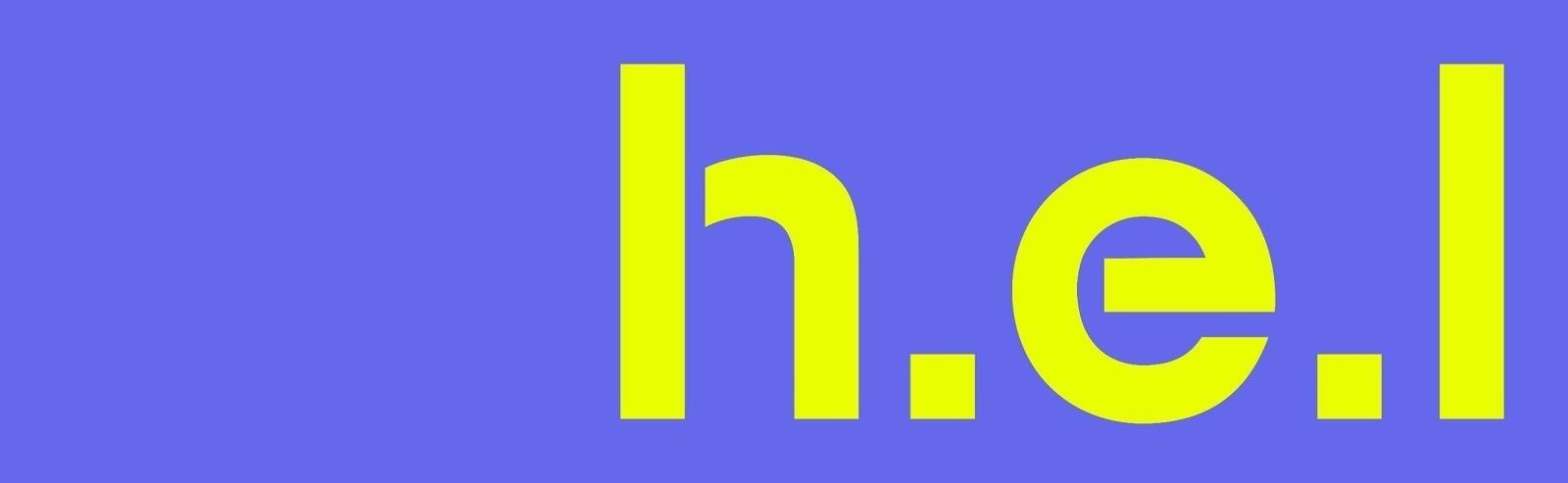
This information has been sourced, reviewed and adapted from materials provided by H.E.L Group.
For more information on this source, please visit H.E.L Group.