For decades, thermal fluids, also known as heat transfer fluids (HTFs) or hot oils, have been widely used in liquid-phase circulating systems to control process temperatures. Due to their low maintenance and provision of consistent, efficient heating without generating high operating pressures, these systems are preferred.
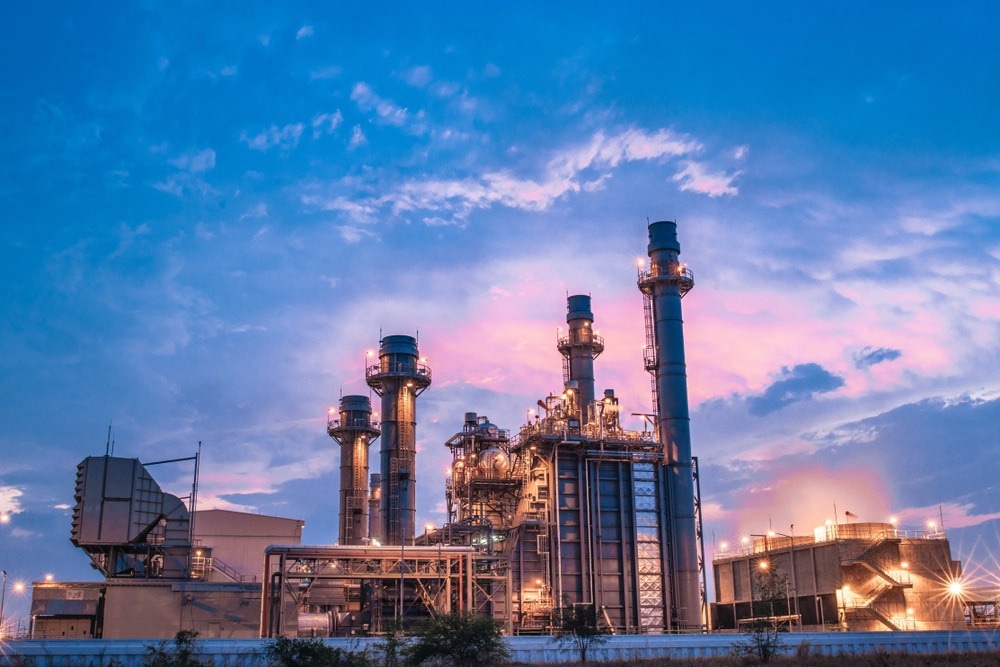
Image Credit: ShutterStock/Oaklism
Thermal fluids will inevitably degrade over time when continually exposed to high temperatures, and the ability of thermal fluids to effectively transfer heat will diminish. Typically, the adverse effects of this type of degradation are slow to appear and can take between many months and years before their impact on system performance becomes apparent.
Due to the low-maintenance ‘set it and forget it’ nature of these operating units, the build-up of degradation products can go completely unnoticed until a major failure occurs. Failures such as these are not inconsequential – from fluid leaks and piping blockages at a minimum ranging to fires, bodily harm, and complete system shutdowns at an extreme.
This presents clear challenges to the essential values of damage control and predictability within plant maintenance operations.
Plant stakeholders need to prioritize obtaining a greater upfront understanding of thermal fluid operations and the impacts of fluid degradation to overcome these challenges. This article will examine what quality makes a thermal fluid uniquely capable of serving its purpose compared to other industrial oils used at a facility.
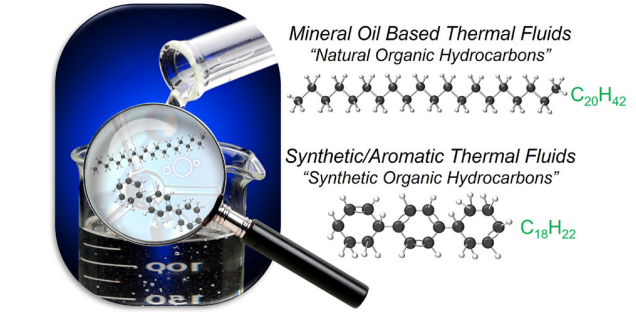
Figure 1. Molecular structures of hydrocarbon-based thermal fluids. Image Credit: Paratherm
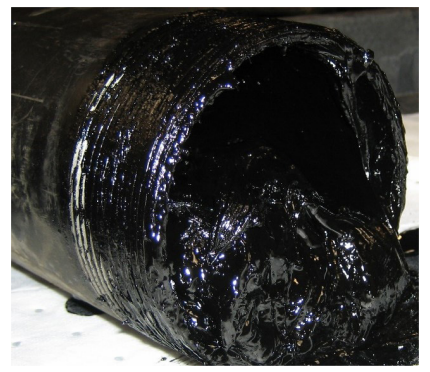
Figure 2. Thermal fluid sludge. Image Credit: Paratherm
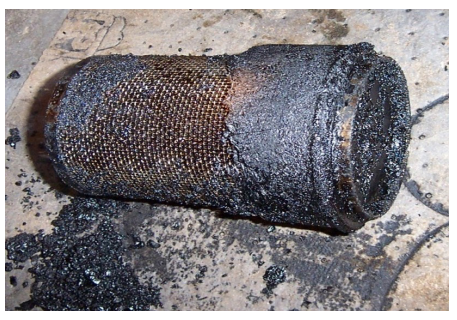
Figure 3. Severe build-up of solid carbon. Image Credit: Paratherm
It will look at how fluid degradation occurs, what is produced by degradation, where these products are most likely to be generated in the system, how the occurrence of thermal breakdown can be identified, and the effect on tracked fluid performance.
A deeper understanding of fluid degradation helps to create confidence that an efficient, predictable heat transfer operation can take place without diminishing the advantages of low maintenance that these systems are designed to provide.
This article will explore the critical aspects of thermal fluid degradation with this goal in mind.
A Closer Look at Degradation Dynamics
The definition of thermal fluid degradation is the irreversible decomposition of a fluid due to thermal stress and prolonged contact with oxygen at raised temperatures.
The inherent molecular structure of the fluid is altered by exposure to heat energy over time. This ultimately results in significant changes to its physical and physiochemical properties. Critical disruptions in fluid performance, working life, and equipment functionality results from the accumulation of degradation products due to these reactions.
Two principal fluid degradation modes are thermal cracking (overheating) and oxidation. Both modes occur as reaction mechanisms and are subject to the long-established principles of thermodynamics, reaction rates, and thermophysical property correlations.
Thermal Fluid Chemistry
Most industrial heat transfer products are created using hydrocarbon-based chemistries. It helps to understand the chemistry of the fluids from that perspective as degradation reactions occur at the molecular scale.
Visual representations of two common molecular structures seen in natural organic hydrocarbon (mineral oil) and synthetic organic hydrocarbon (synthetic/aromatic) based thermal fluids are provided in Figure 1. Specific molecular arrangements of the various hydrocarbon-based fluid types will determine performance, reaction dynamics, and degradation products.
A product of petroleum distillation, mineral oil-based thermal fluids (natural organic hydrocarbons) are made up of a ratio of refined alkanes (paraffins) and cycloalkanes (naphthenes) with a targeted range of chain lengths and arrangements. Figure 1 showcases the alkane C20H42 as just one example of a hydrocarbon chain that may be found within the bulk distribution of a mineral oil fluid.
Products of chemical synthesis, synthetic aromatic hydrocarbons feature ring structures with a degree of double bonding. The chemical composition of each fluid type directly correlates to how each fluid will behave in a thermal operation – in terms of how they will degrade and perform.
Truly legitimate thermal fluids are specifically designed to prioritize heat transfer efficiency, quality, and thermal stability. Superfluous additives and impurities will foul out when exposed to heat and can catalyze degradation reactions.
The selective balance of physical properties determines how efficient a fluid will be at transferring heat energy from the heat source into the fluid and then out into the operating units. At elevated temperatures, products formulated using a foundation of robust chemistries will be more resistant to thermal degradation.
Degradation Products
The following degradation products are those most commonly generated as a result of thermal cracking and oxidation:
- Low boilers: molecules generated when hydrocarbon chains are broken into smaller fractions with boiling points lower than the original distribution of fluid molecules. Generally, an increase in low boilers results in decreased fluid viscosity.
- High boilers: molecules generated when hydrocarbon chains are broken and then reacted with other molecules to generate products with higher boiling points than the original distribution of fluid molecules. Typically, increased high boilers will lead to increased fluid viscosity.
- Thermal fluid sludge (see Figure 2): an acidic, highly viscous tar-like material generated from the combination of oxidized fluid and solid carbon particles.
- Solid carbon (see Figure 3): a product of the ongoing cracking of hydrocarbons into elemental carbon. This can be in the form of a carbon ‘shell’ fouled onto equipment surfaces, as suspended fine carbon soot (darkening the appearance of the bulk fluid), or as larger solid particles.
- Contaminants: Typically, high concentrations of natural impurities from the inferior refinement of raw material and additives will foul out of the bulk fluid far before normal degradation factors come into play. Residual degradation products remaining in a system after fluid changeout are also considered contaminants and can accelerate degradation reactions within the new fluid charge.
In some way, all degradation products will harm the performance of the thermal fluid. Typically, low boilers will contribute to decreased thermal capacity and can cause pump cavitations, pressure fluctuations, and other operating challenges.
Solids can create an insulating layer between the heat source and the thermal fluid through blocked lines and fouled equipment surfaces. High boiling materials and sludge will plug lines, limit fluid flow, and can completely solidify or ‘gel up’ when system temperatures fall.
Though degradation over time is inevitable, understanding the factors that lead to such serious consequences helps minimize the rate at which it happens.
Focus on The Factors: Thermal Cracking (Overheating)
At the most basic level, thermal fluids are designed to perform an arguably complex series of tasks.
Energy in the form of heat is transferred from the heating source (fired heater, electric immersion element, etc.) into the bulk fluid through a conductive surface (i.e. the wall of a pipe coil). The fluid is then required to hold onto that energy as it flows through the piping, until it reaches the operating unit and transfers the energy into the process.
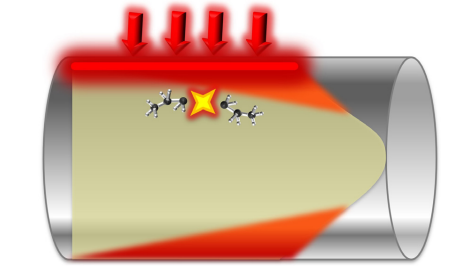
Figure 4. Degradation hot spot: thermal cracking at the fluid film layer. Image Credit: Paratherm
According to the principles of the First Law of Thermodynamics, ultimately, any heat energy that is not transferred out of the heater via bulk fluid movement to be consumed by the process application (or wasted out of a heat exhaust) will eventually be consumed as energy to break fluid molecular bonds.
This is known as overheating or thermal cracking of the fluid. The heat source is the primary area where fluid is most prone to thermal cracking, as it is the area of the highest energy concentration in the system.
Thermal cracking is prevalent at the ‘film layer’ where the thermal fluid comes into contact with the heated surface (depicted in Figure 4, as the inside wall of a heated pipe coil).
The film layer is, therefore, the area of highest heat flux, in addition to being the point at which flow is restricted the most and the fluid friction is highest. To allow the fluid to ‘wash’ the heat energy away from the pipe into the fluid and out of the heater, turbulent fluid flow is critical. A degree of localized thermal cracking will result from any factor that inhibits the fluid from effectively transferring the heat energy away from the heated surfaces.
Limiting factors include poor heat transfer efficiency (inherent to a poorly designed thermal fluid or due to ongoing degradation altering original fluid properties), insufficient fluid flow set points, fouled transfer surfaces, blocked lines and improper system start-up and shutdown procedures.
Figure 5 uses the previous example of C20H42 alkane representing a typical molecule in a basic paraffinic mineral oil thermal fluid to demonstrate that the hydrocarbon chain is broken into smaller fractions as a result of overheating, each with lower boiling points than the original molecule.
Accumulation of the generated low boilers will continue, and drastic changes in the bulk fluid properties will occur due to cracking, diminishing heat transfer efficiency. Eventually, this decrease in efficiency will manifest itself as a loss of temperature output in the operation.
The typical immediate reaction of a plant operator, when this happens, is to increase the heater outlet set point to compensate for the losses. However, this will only accelerate the degradation rate more and compound the problem (the principles of the Arrhenius Equation apply to degradation, which means that every 10 ˚C increase in temperature doubles the reaction rate).
This downward spiral of events will break down the fluid more, ultimately generating solid carbon and compromising the system's functionality.
Focus On The Factors: Oxidation
Oxidation is the name given to a chemical reaction that occurs if heated thermal fluid is continuously exposed to fresh air. The molecules are susceptible to further reaction as heat energy initiates breaking hydrocarbon chains.
The degraded hydrocarbons react with oxygen molecules and other stable hydrocarbons when in contact with fresh air at elevated temperatures and form a variety of new highly-reactive intermediates and byproducts.
The only area in a traditional thermal fluid system that creates the potential for these factors to come together is inside the expansion tank (Figure 6). Chain reactions are perpetuated by continued exposure to heat and air under these conditions, which will form acidic material (carboxylic acid).
Ultimately, these acids decrease the pH, increase the viscosity of the bulk fluid, and generate high boilers. The acidic and high-viscosity material eventually combines with any fine carbon solids fouled out of the fluid to create thermal fluid sludge.
Turning back to Figure 3, there are obvious negative effects of accumulated sludge in the system as can be seen in the physical nature of this material. When unchecked oxidation reaches that extreme, decreased flow dynamics, system cold spots, and plugged lines, along with extensive maintenance procedures and high potential for complete system shutdown, are common.
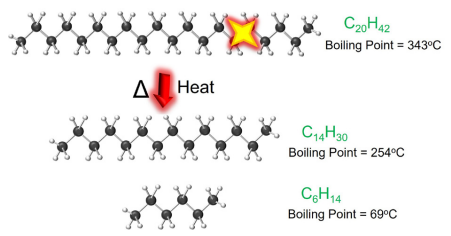
Figure 5. Example of a thermal cracking reaction mechanism. Image Credit: Paratherm
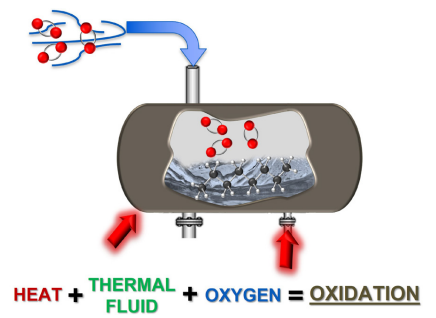
Figure 6. Degradation hot spot: oxidation occurs in the system expansion tank. Image Credit: Paratherm
Evolve: Apply Knowledge and Take Action
This article intended to offer a deeper understanding of how, where, when and why thermal degradation occurs. Applying this knowledge to real-world operations is key even though fluid degradation is inevitable over time, as such knowledge limits the rate at which it happens, and significantly reduces the potential for unidentified issues to amalgamate into a major failure.
However, this knowledge is only effective if it is used to transform conventional approaches to running thermal fluid operations. It is essential to choose a fluid that is purposefully engineered to give the optimal combination of efficiency quality, and thermal stability, with this chemistry in mind.
By maintaining and monitoring design flow rates and temperature set points, thermal cracking at the heat source can be controlled so that the maximum film temperature capability of the fluid is not exceeded.
It is important to slowly accelerate system temperature set points until the fluid viscosity reaches a stage where turbulent flow is possible, as fluid is most prone to overheating during system start-up and shutdown (check with fluid suppliers for specifics on this).
The system’s circulating pump should continue to run after the heater is shut off to remove residual heat from the chamber when shutting down a system. If this does not occur, stagnant fluid will be left to ‘bake’ inside the pipe coils.
This article examined fluid oxidation closely, and taken an in-depth look at precisely where it happens and under which conditions: thermal fluid + heat + air = oxidation. This article has also discussed the appearance of thermal fluid sludge and how detrimental it can be to a system.
Oxidation reactions cannot be accelerated if the expansion tank is kept cool (ideally below 70 ˚C). Purging the headspace in the expansion tank with an inert gas to eliminate the presence of oxygen could be one consideration, removing oxidation from the equation.
Conclusion
It is important for operators to monitor the system: look, listen, and note down any red flags, as well as querying changes in normal system operation, such as pressure fluctuations, heat losses, and altered flow dynamics.
It will likely be detrimental to attempt to compensate for such changes with a simple temperature or flow adjustment (one simple 10 ˚C increase in set point is all it takes to double the rate of degradation). It is, therefore, key to find a testing laboratory partner specializing in thermal fluids (as opposed to a standard lube oil analysis) and to send fluid samples annually.
This is the most effective method to catch the generation of degradation products in sufficient time to make informed decisions and, therefore, to avoid significant failures. It does not take much added effort to make a big difference, and awareness is critical to maintaining a long-lasting, efficient, and predictable thermal fluid operation.
Acknowledgments
Produced from materials originally authored by Ryan Ritz from Paratherm Heat Transfer Fluids.

This information has been sourced, reviewed and adapted from materials provided by Paratherm.
For more information on this source, please visit Paratherm.