Etching is a method employed during the fabrication of semiconductors to chemically remove layers from the surface of the wafer substrate. Etching is a crucial process, and each wafer is subject to several etching steps before it is complete.
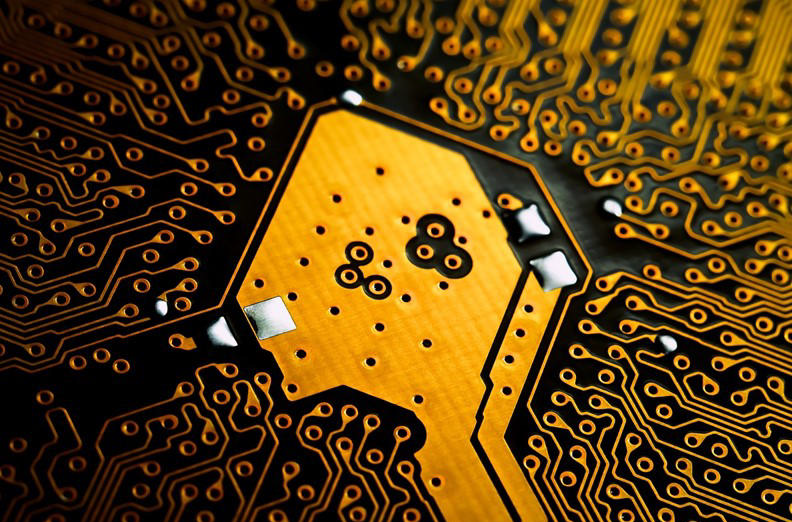
Image Credit: Metrohm USA Inc.
To guarantee that the etching performed is optimal, strict quality control measures are required to determine the acid etchant concentration in the varied mixed acid solutions.
Either SPM (sulfuric acid-peroxide mix, referred to as piranha solution), DSP (dilute sulfuric acid-peroxide mix), or DSP+ (dilute sulfuric acid-peroxide-hydrofluoric acid mix) are usually utilized as etching solutions, with the selection being dependent on the wafer substrate and etching step.
Preserving the proper balance of acid concentrations in these mixtures is vital for optimizing the etch rate, uniformity, and selectivity of the etching process.
This article presents a technique for simultaneously measuring hydrogen peroxide and sulfuric acid online in SPM and DSP solutions via Raman spectroscopy using the PTRam Analyzer from Metrohm Process Analytics.
Two types of etching processes are utilized in the semiconductor industry, namely dry and wet etching. Dry etching utilizes reactive gases such as plasma to remove the undesired parts of the semiconductor material. Wet etching involves the selective removal of material from a substrate via chemical solutions.
These processes are widely employed in many industries, such as semiconductors, electronics, and metalworking. Wet and dry etching processes are used depending on the unique needs of the device that is being manufactured.
However, wet etching has been more commonly employed than dry etching in producing semiconductors, especially for removing substantial amounts of wafer material and for ease of handling.1
Depending on the layer or material undergoing etching and the intended outcome, different types of chemical baths may be used for the wet etching of semiconductors. Sulfuric acid-peroxide mix, piranha solution (SPM), and dilute sulfuric acid-peroxide mix (DSP) often produce silicon wafers.2
For wet etching to be successful, precise control of the reagent concentration in the bath solution is required. Determining the acid concentration in mixed acid etching baths is a crucial step in quality control that can impact the outcome of the etching process.
Both DSP and SPM are potentially toxic solutions that require extreme caution when handling. Personal protective equipment (PPE) should be worn when working with these chemicals, and all waste materials must be disposed of according to local regulations.
As a result of this, online analysis is required to reduce employee exposure as far as possible and to prevent accidents. In addition to the hazards previously mentioned, the manual sampling of mixed acid baths is undesirable due to potential inaccuracies, time constraints, and interruptions in the production process.
Manual sampling may lead to inconsistent sampling locations and depths, potentially providing inaccurate data regarding the actual condition of the bath. A better solution is required to enable real-time control of the process, minimization of operational disruptions, improved safety, and more accurate and representative data.
A safer, quicker, and more efficient method of simultaneously monitoring multiple parameters in mixed acid baths is through reagent-free online analysis using Raman spectroscopy.
The PTRam Analyzer from Metrohm Process Analytics, as shown in Figure 1, is well-suited for this challenging situation. This Raman analyzer allows the real-time spectral data from the process to be compared to a reference method, such as titration.
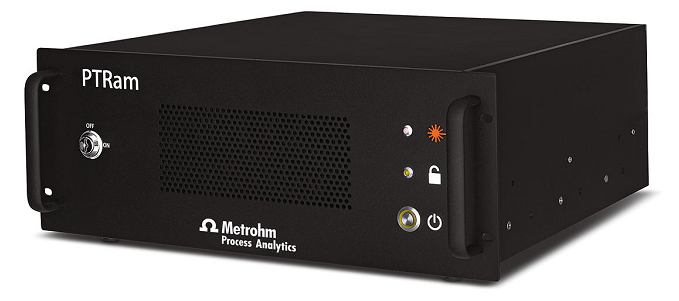
Figure 1. The PTRam Analyzer from Metrohm Process Analytics. Image Credit: Metrohm USA Inc.
There is minimal space available to install an analysis system within the wet bench area, as shown in Figure 2a. As a result, the small dimensions of the PTRam Analyzer make it the perfect solution for confined spaces.
The embedded IMPACT software and the range of industrial communication protocols enable results to be transmitted in the same format to a Programmable Logic Controller (PLC), a Distributed Control System (DCS), or a Supervisory Control And Data Acquisition (SCADA) system for further actions such as adjusting chemical dosing.
Application
Perfluoroalkoxy (PFA) tubing is widely employed for applications with aggressive media because of its excellent chemical resistance, which is highly valuable. Raman spectroscopy enables the measurement to be taken through transparent and semi-transparent materials.
This application uses this property by measuring the sample through PFA tubing, as shown in Figure 2b.
a)
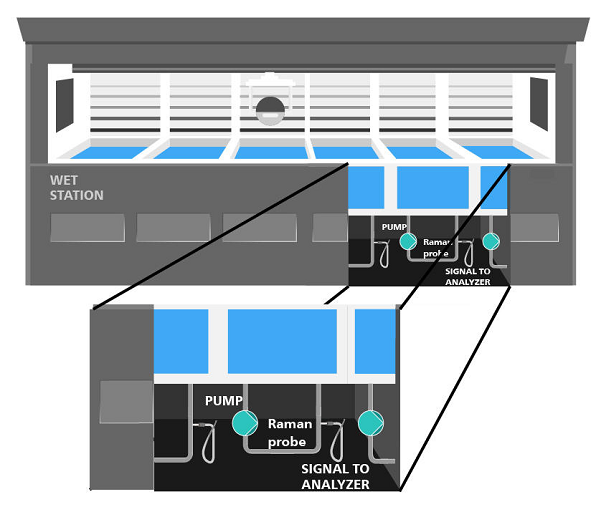
b)
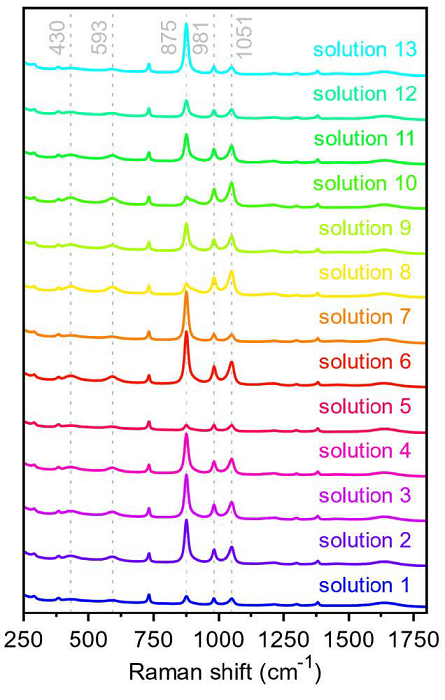
Figure 2. a) Stylization of suggested placement for an online Raman probe on a wet bench in the wafer etching process and b) Raman spectra collected during measurements. Image Credit: Metrohm USA Inc.
Conclusion
The utilization of Raman spectroscopy, specifically the PTRam Analyzer from Metrohm Process Analytics, offers an efficient and reliable technique for online monitoring of the hydrogen peroxide and sulfuric acid content in etching solutions such as DSP and SPM.
This online analysis method allows real-time measurements of multiple parameters simultaneously, delivering precise control over the reagent concentrations in the mixed acid baths.
By comparing spectral data and reference methods, Raman spectroscopy can contribute to a safer production environment by eliminating exposing operators to hazardous chemical reagents.
The use of Raman spectroscopy to monitor the etching bath composition also improves the efficiency of wafer cleaning. It increases product throughput, production rates, reproducibility, and overall profitability by reducing wastage and providing optimal etching processes.
References and Further Reading
- Dry Etching vs. Wet Etching - Differences and Applications. https://www.xometry.com/resources/blog/dry-etching-vs-wet-etching/ (accessed 2023-05-03).
- Clews, P. J.; Nelson, G. C.; Matlock, C. A.; et al. Sulfuric Acid/Hydrogen Peroxide Rinsing Study, Sandia National laboratories.
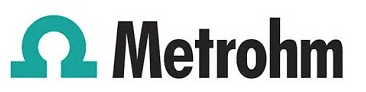
This information has been sourced, reviewed and adapted from materials provided by Metrohm USA Inc.
For more information on this source, please visit Metrohm USA Inc.